For smooth work center management, it is better to manufacture different variants of products in different work centers. So we can consider some examples. Let's imagine that a customer needs a table with its different variants, and the onhand quantity of the table will be zero. So to satisfy the customer, the company wants to manufacture the product.
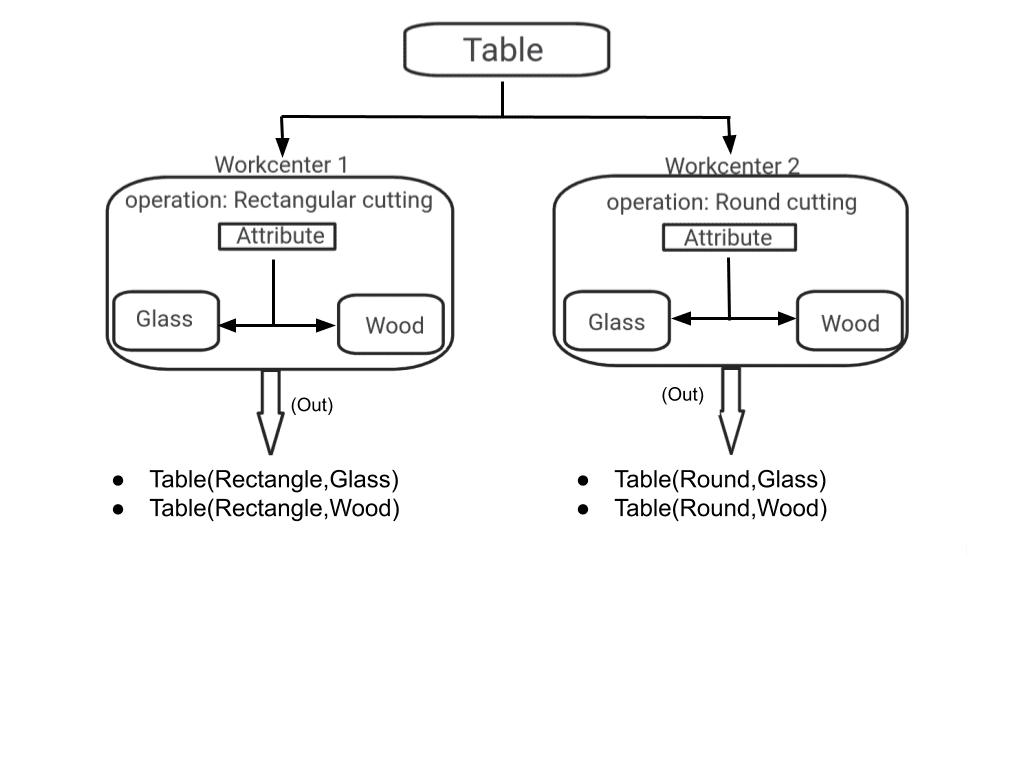
From the above figure, we can identify that the table has four variants, rectangular wooden table, rectangular glass table, round wooden table, and round glass table. When a customer places an order, the company instantly starts the manufacture of the product but uses different work centers for different shapes. That is, the round table is manufactured from one work center, and the rectangular table is manufactured from another work center.
So to check out the whole manufacturing process, go to the Odoo 17 manufacturing application. Create a product ‘Table’ from the Manufacturing application itself. Go to the Products menu and click the Products sub-menu from there by clicking on the New button to configure a new storable product table with the on-hand quantity as zero.
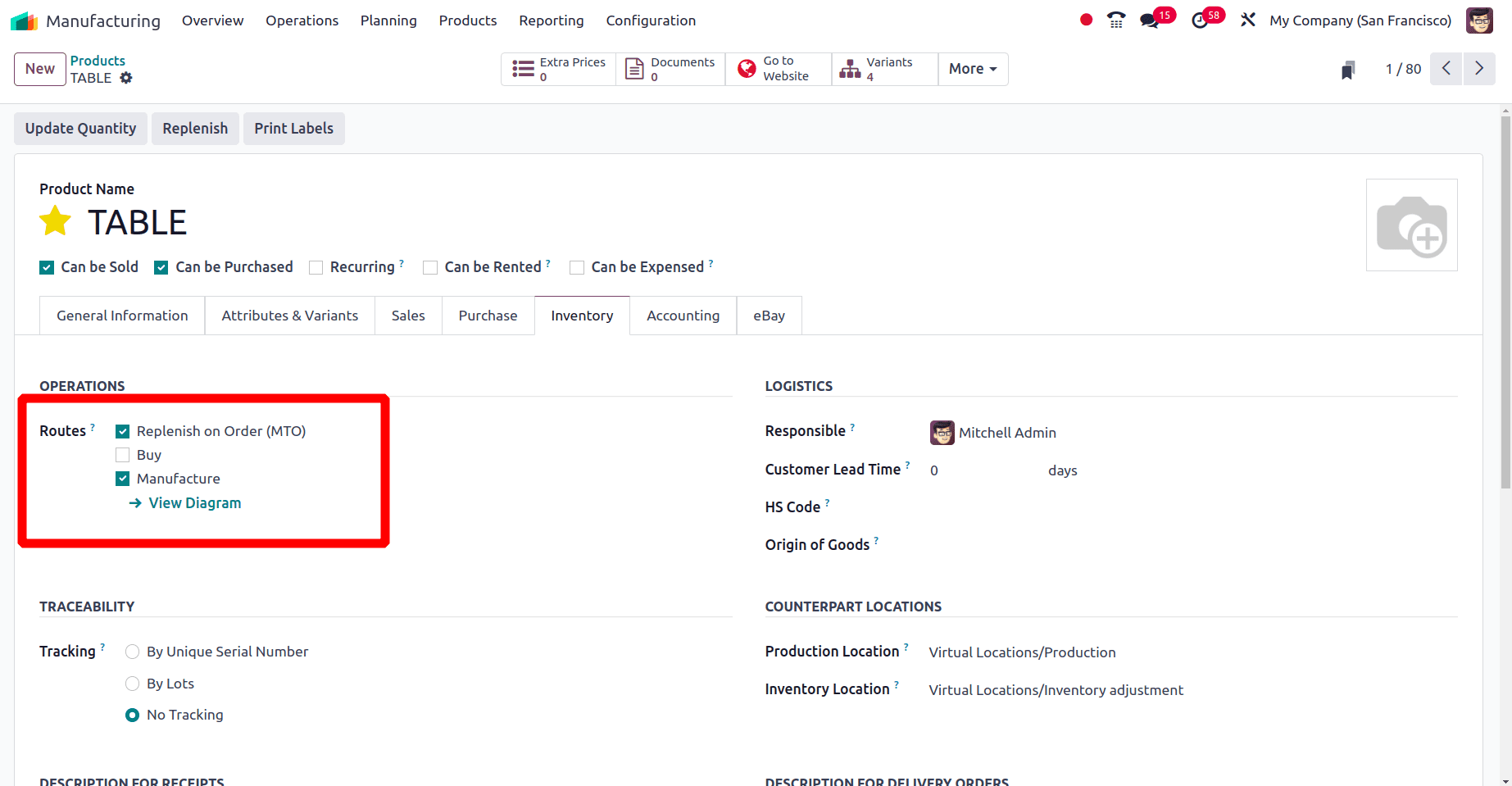
Then go to the inventory tab of the product form and set the routes as Replenish on order (MTO) and Manufacture.
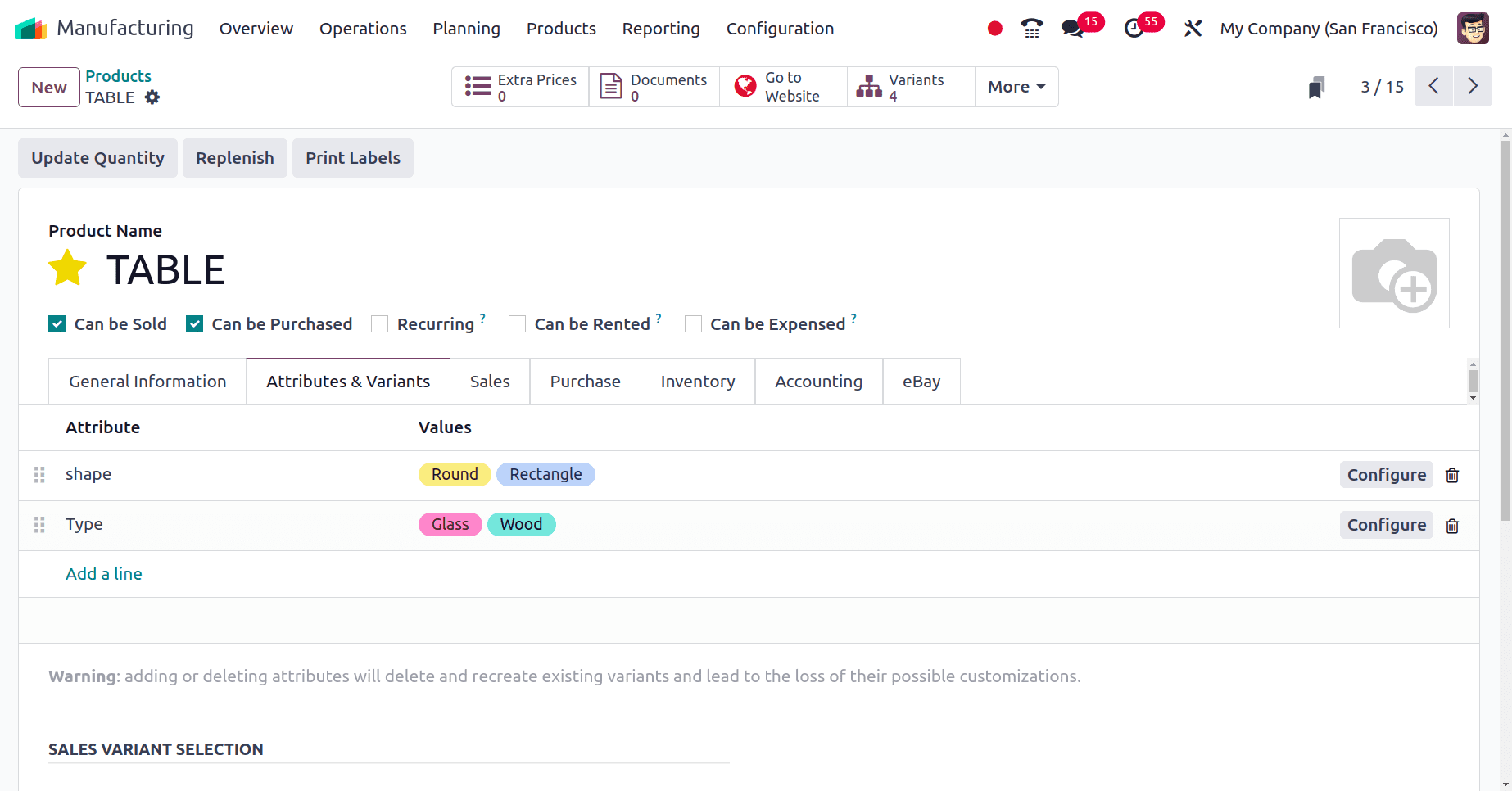
From the above screenshot, we can see that we have configured four different variants for the product Table. We are manufacturing the round table from work center 1 and the rectangular table from work center 2. So the next step is to configure two work centers. To configure a work center, first go to the configuration settings of the manufacturing application.
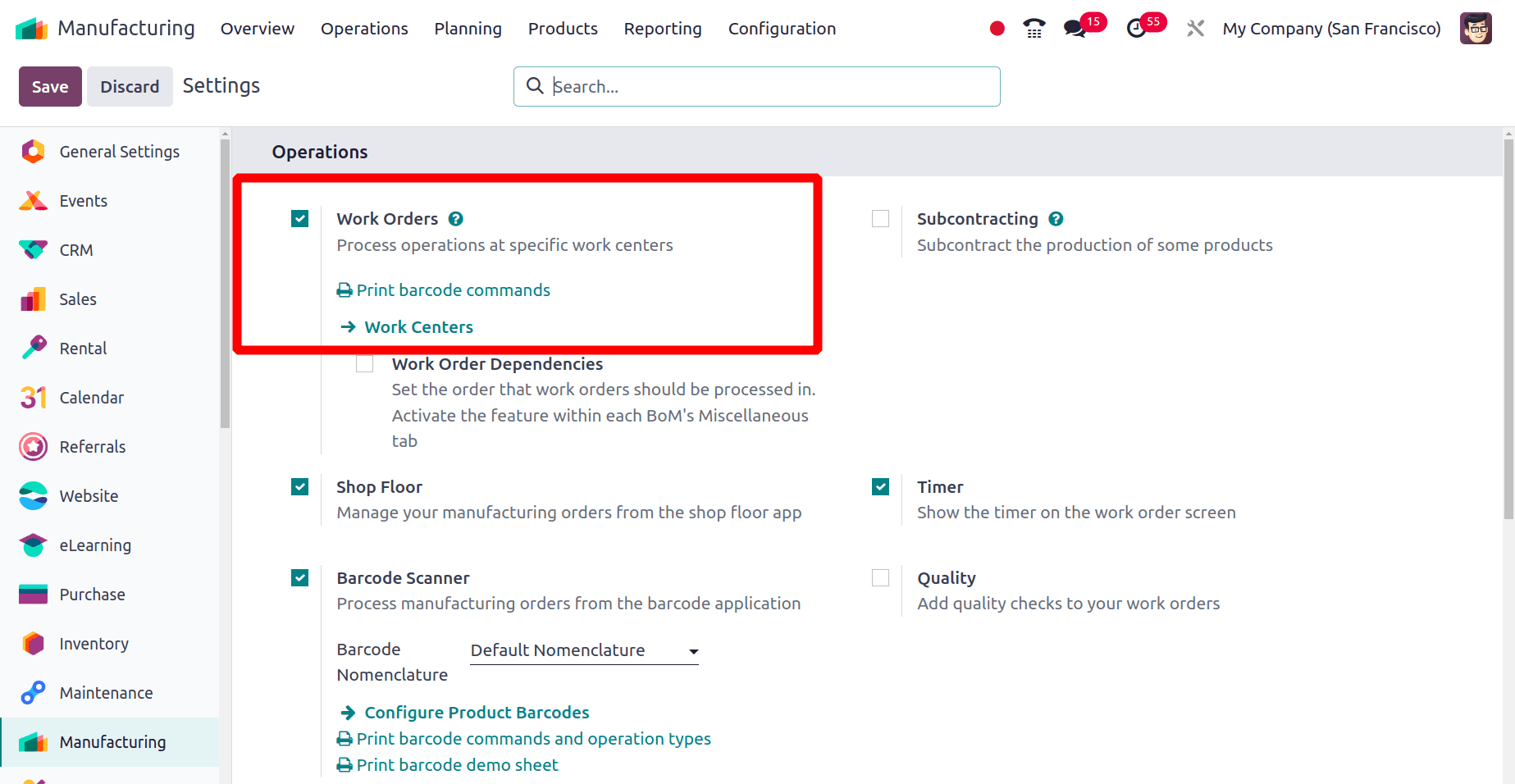
Under the operation section, enable the work orders option and save changes. Move to the Configuration menu and click the Work Center sub-menu. Then we have the option to create a new work center. Click the New button to configure the new work center. Here we have created two work centers, ‘work center 1’ and ‘work center 2’.
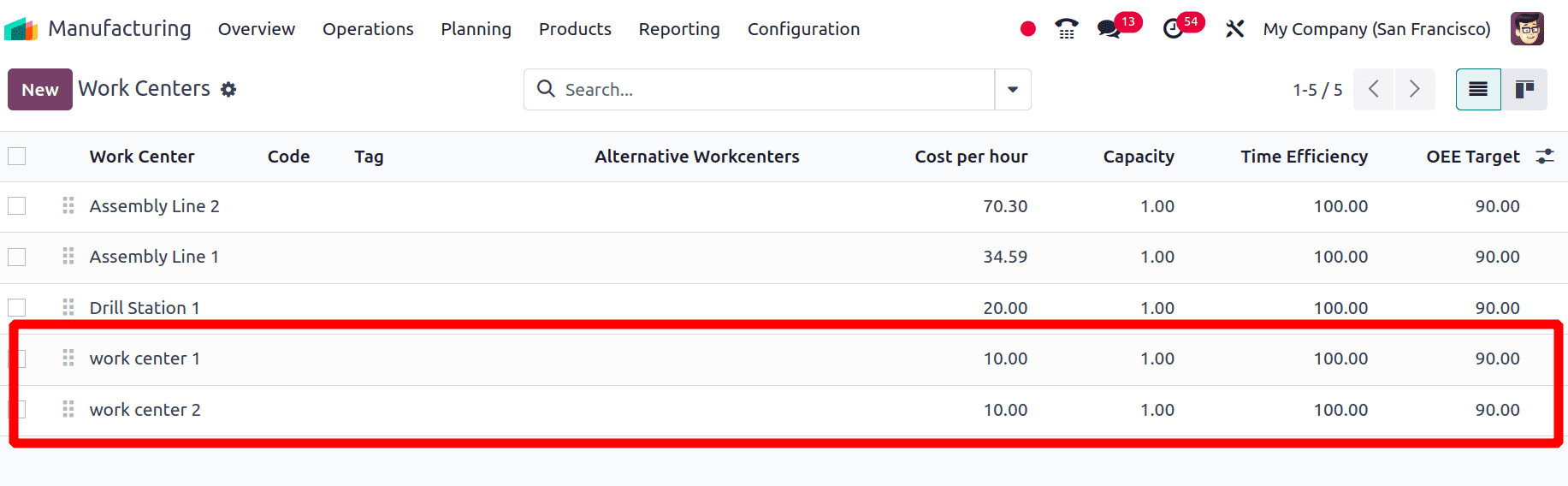
Then the next step is to create Bills of Materials for the different variants of the product. A Bill of Material is a list of components and their quantities needed to manufacture or assemble a product.
By clicking the Bill of Materials smart tab in the product form, we can create a Bill of material. Otherwise, click on the Products menu and then click on the Bill of Material sub-menu. Click the New button and create the new bill of materials for the product Table with its four variants.
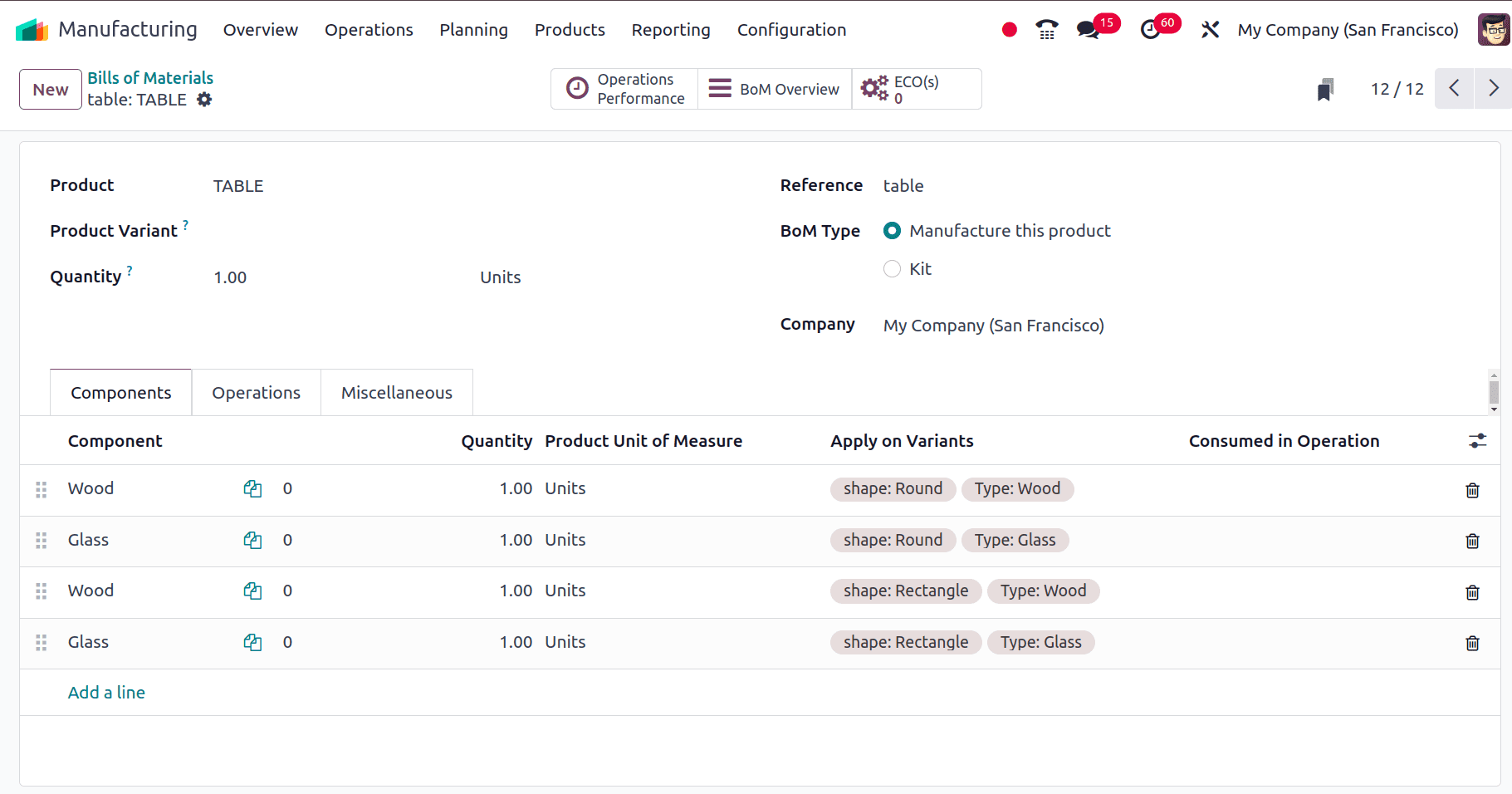
Then, move to the Operation tab of the Bill of Materials form, there is an option to provide the work center. When clicking on the add a line option from the Operations tab a new popup window appears and provides the operation that is taking place and the work center in that popup window.
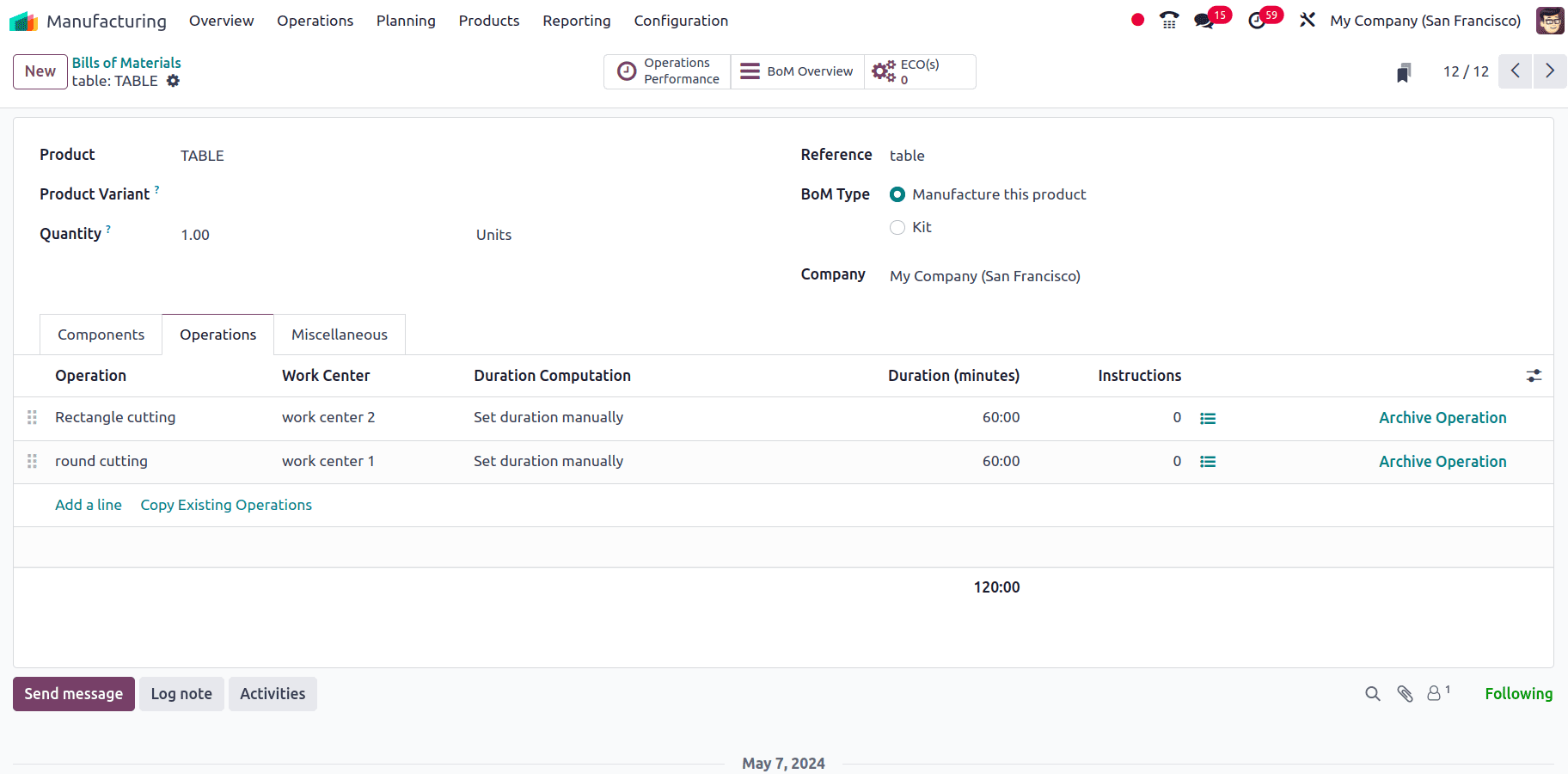
In that popup window, there is an ‘Apply on variants’ field. Provide the name of the variant for which that operation is taking place.
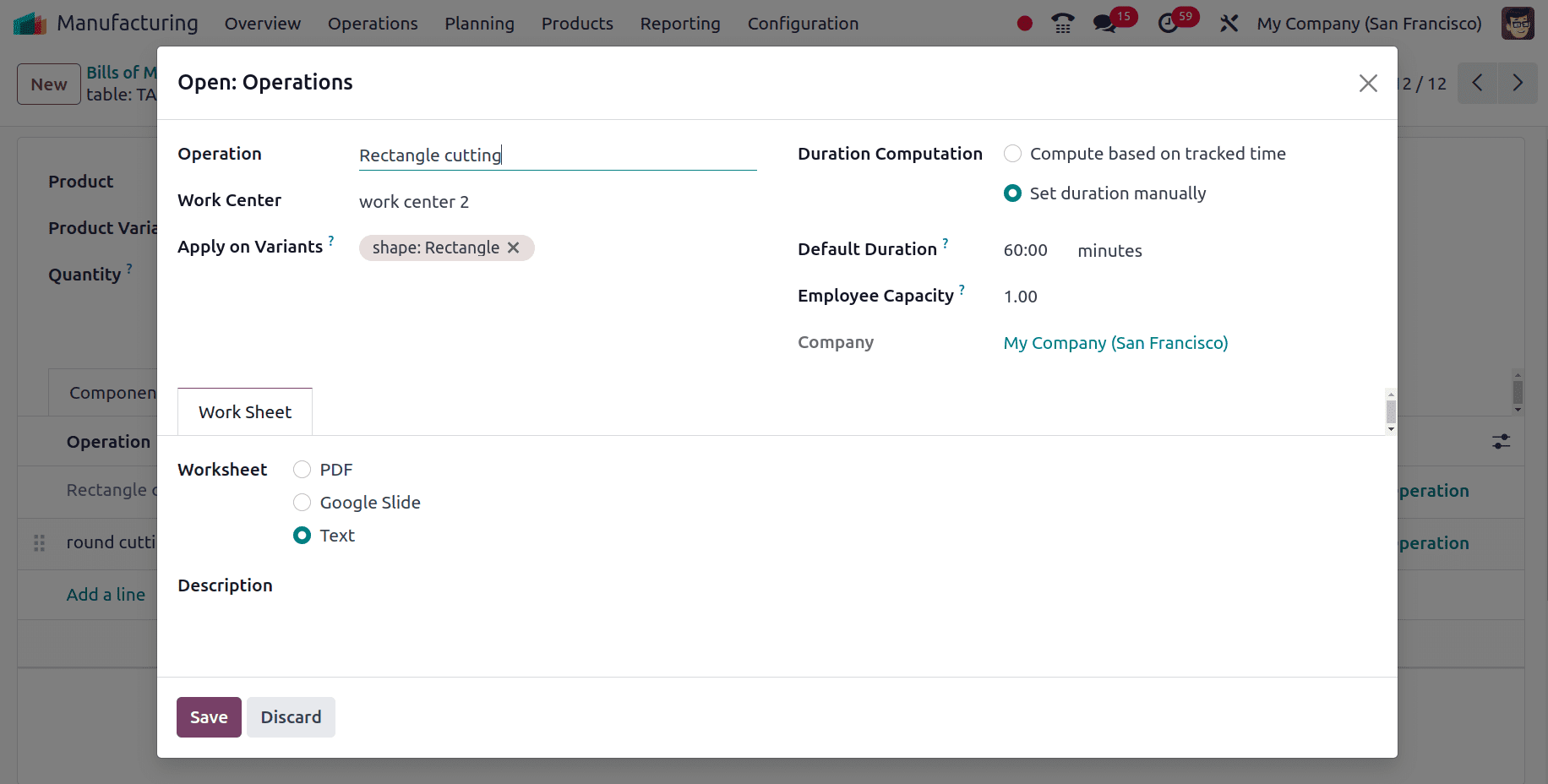
From the above screenshot, we can see that the operation of the ‘Round cutting’ is taking place in the ‘work center 1’ and the ‘rectangular cutting’ operation is taking place in the ‘work center 2’. In the ‘Apply on variant field’, we have provided the rectangle variant of the product for which this operation is assigned.
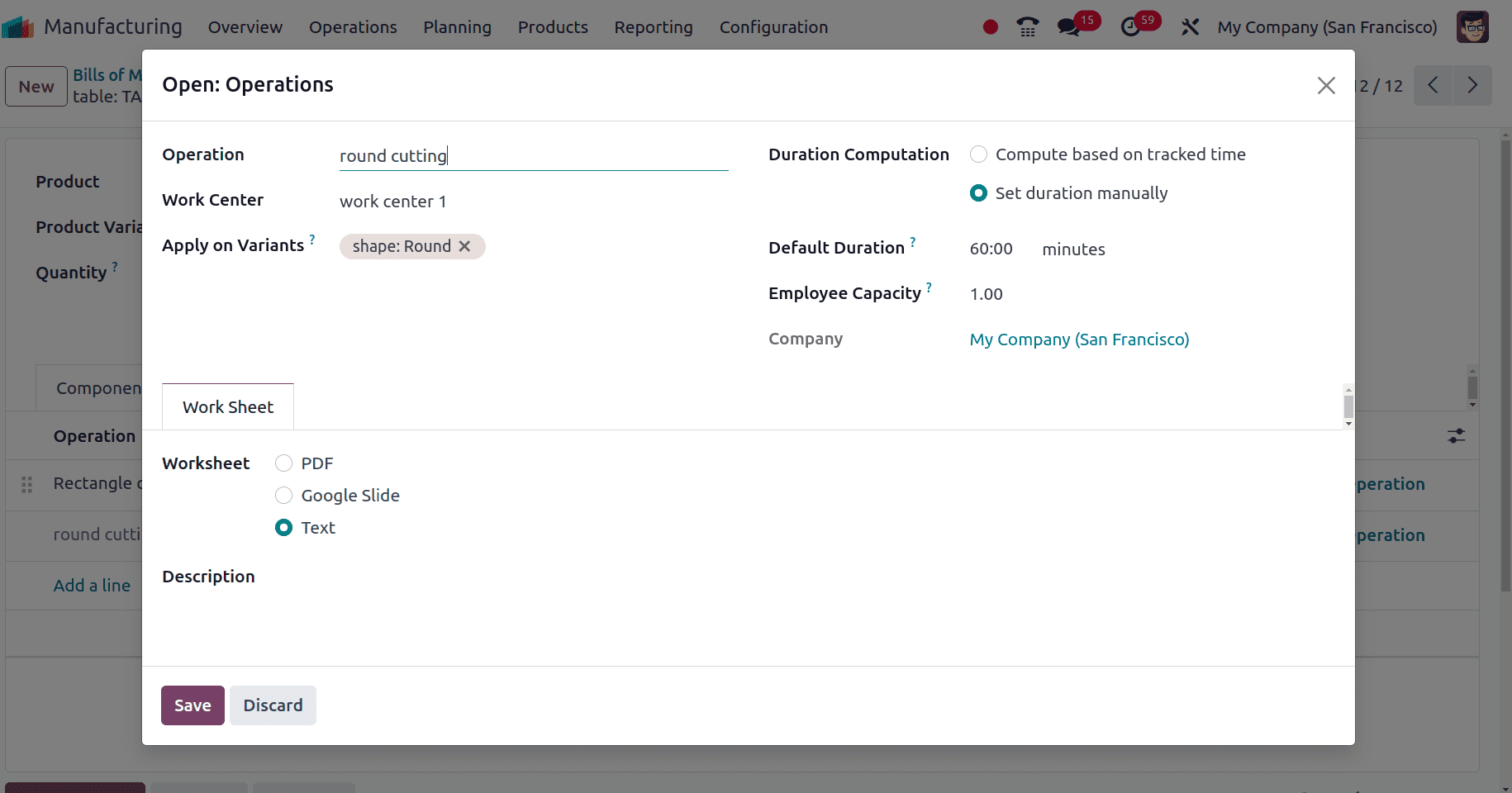
Then we have set the second operation ‘round cutting’ which takes place from the ‘workcenter 1’ and this operation is assigned to the round variant of the product.
So, here, we are conducting two operations, round cutting and rectangular cutting. Round cutting takes place from ‘work center 1’ and rectangular cutting takes place from ‘work center 2’. That is ‘Work Center 1’ for building round tables of wood and glass materials and ‘Work Center 2’ for rectangular tables of wood and glass materials.
The next step is to make a sale order for these products. So let's move to the sales application. Click the Orders menu and then click on the Quotation sub-menu to create a new quotation for the sale order. Create a new quotation and choose one of the variants of the product. For the selection of the variant, there appears a popup window. There we can see all three variants of the product, and we can configure different variant values for the product.
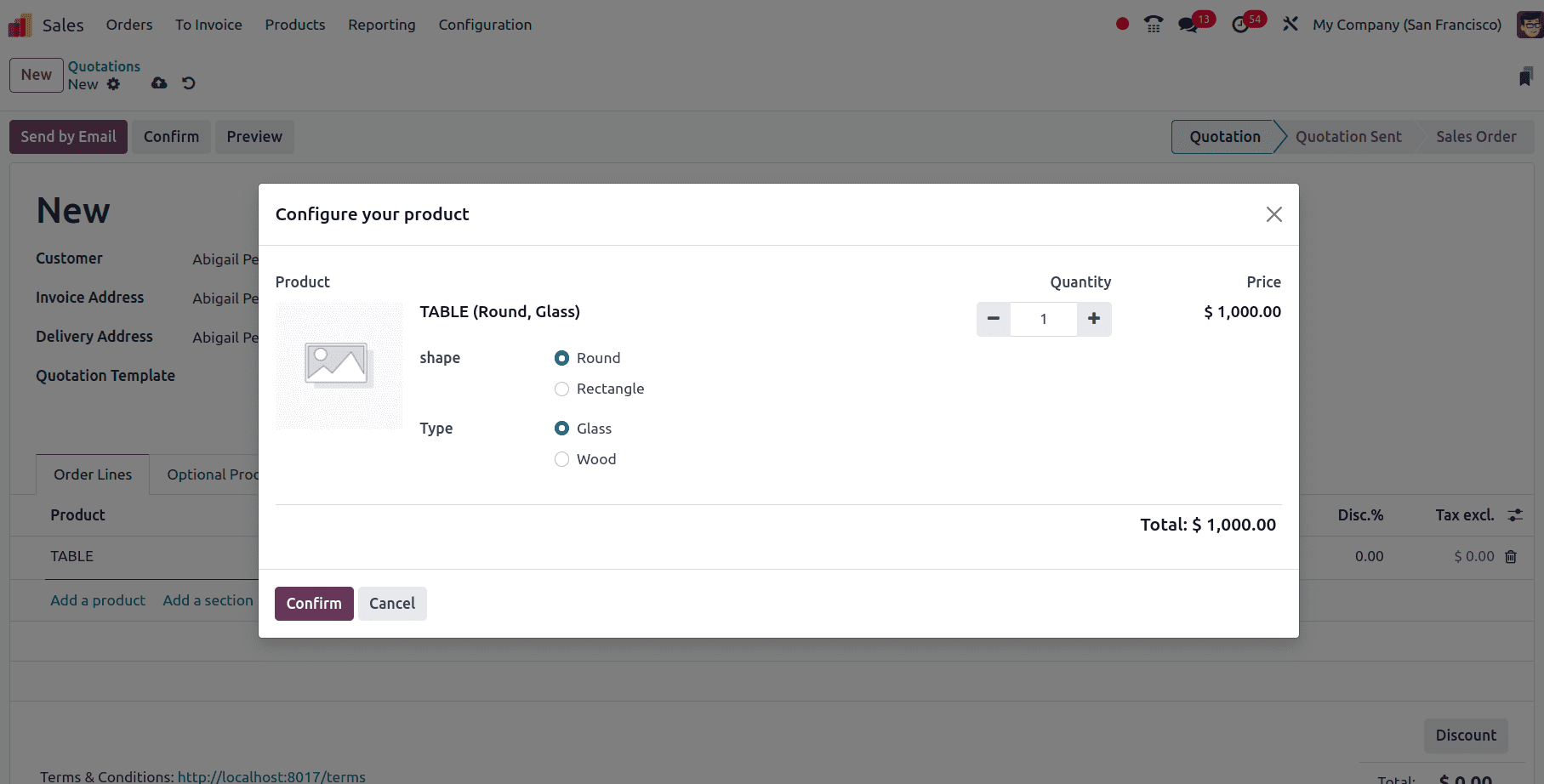
Then confirm the configured product variant in the quotation, add another three variants of the product in the same quotation, and confirm the order.
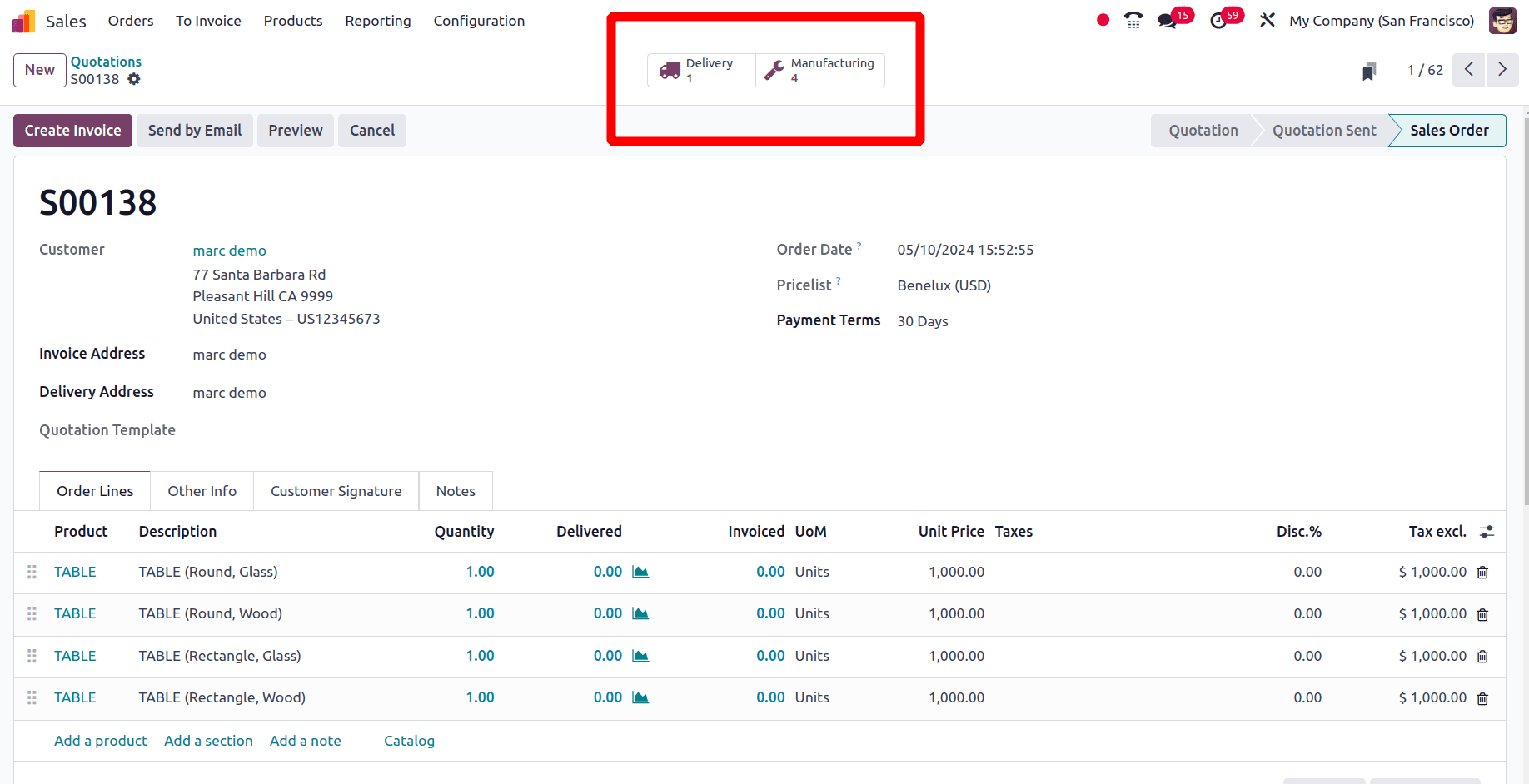
Once the order is confirmed, in the sale order form there appears the ‘Delivery’ smart tab and the ‘Manufacture’ smart tab. But in the Manufacturing smart tab, there will be four manufacturing orders triggered to manufacture four different variants. Then click on the Manufacturing smart tab and there we can see the four manufacturing orders.
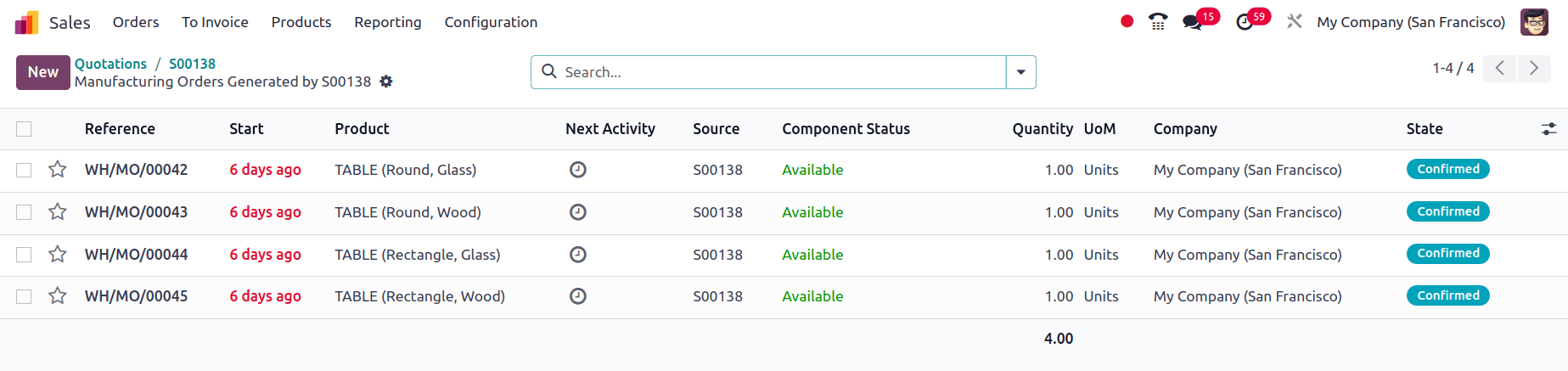
Choose each of the manufacturing orders and click the ‘Produce all’ button to manufacture the product.
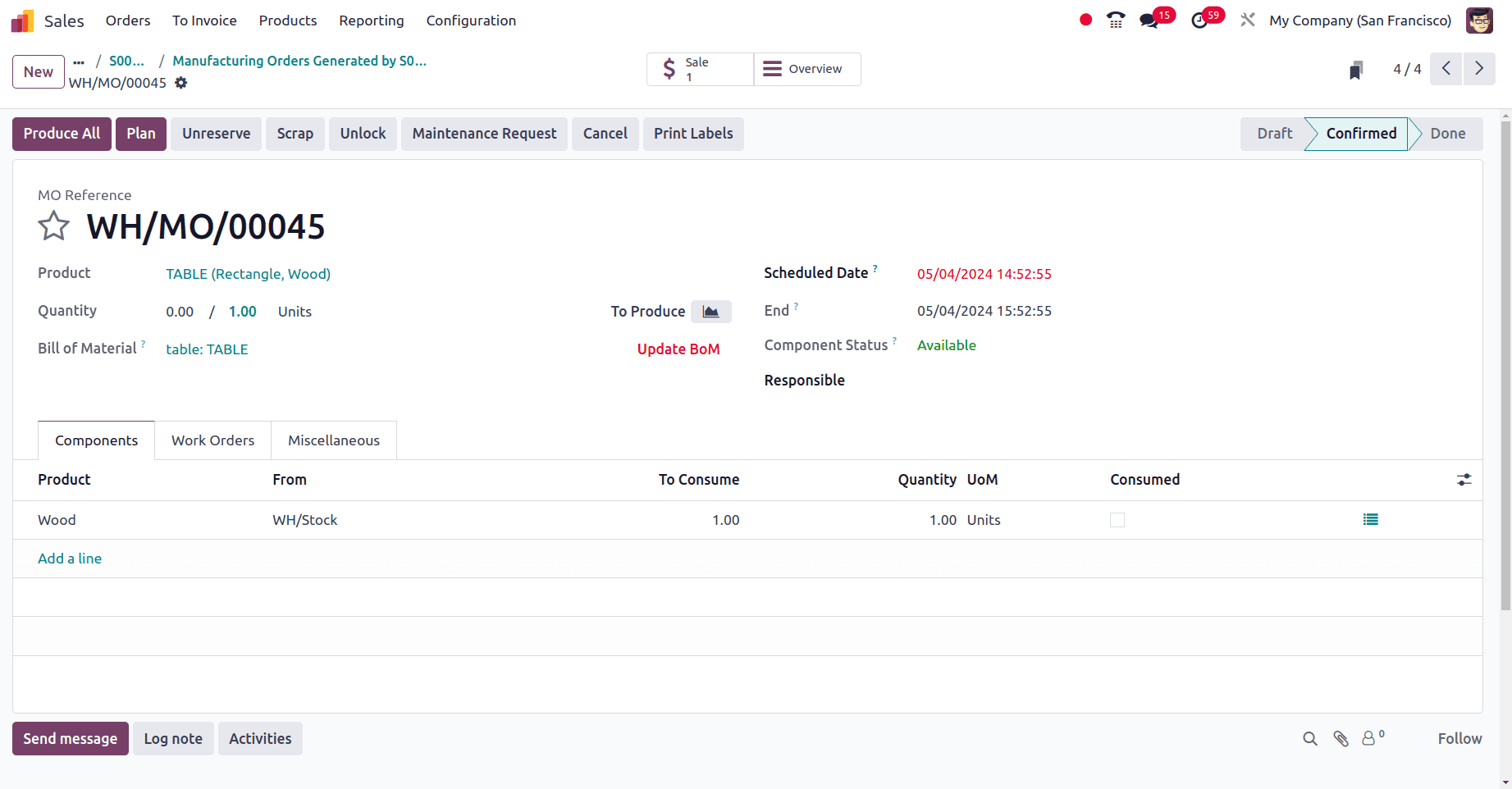
In the above screenshot, we can see that the product manufactured is a rectangular wooden table and, as the shape is rectangular. We plan to manufacture the product from ‘Work Center 2’, so to check that, we can move to the ‘Work Orders’ tab of the manufacturing order.
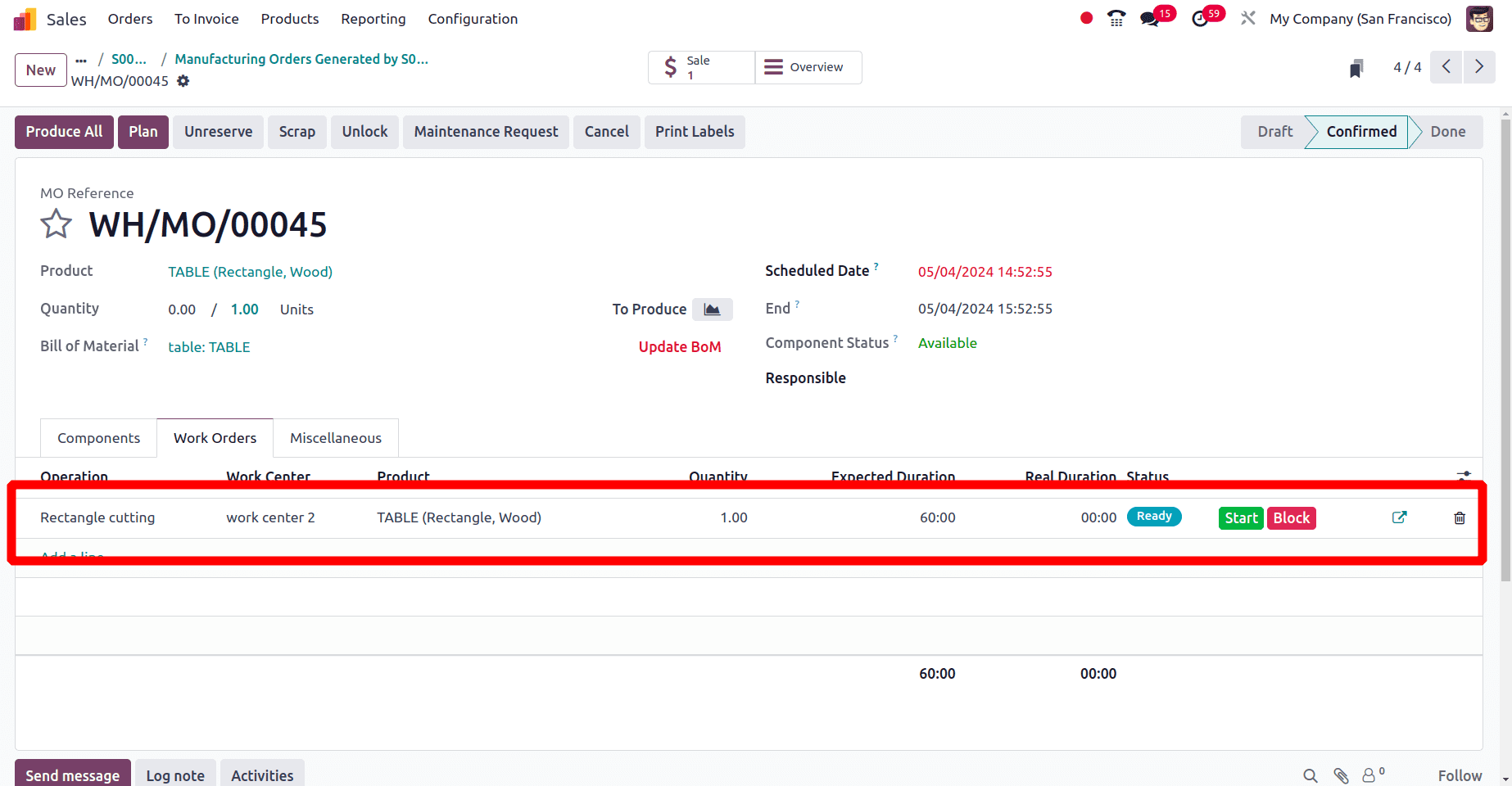
Here, we can see that the work center used is ‘work center 2’. Similarly, when we go to the manufacturing order of the round wooden table, we can see that this table is manufactured from ‘work center 1’
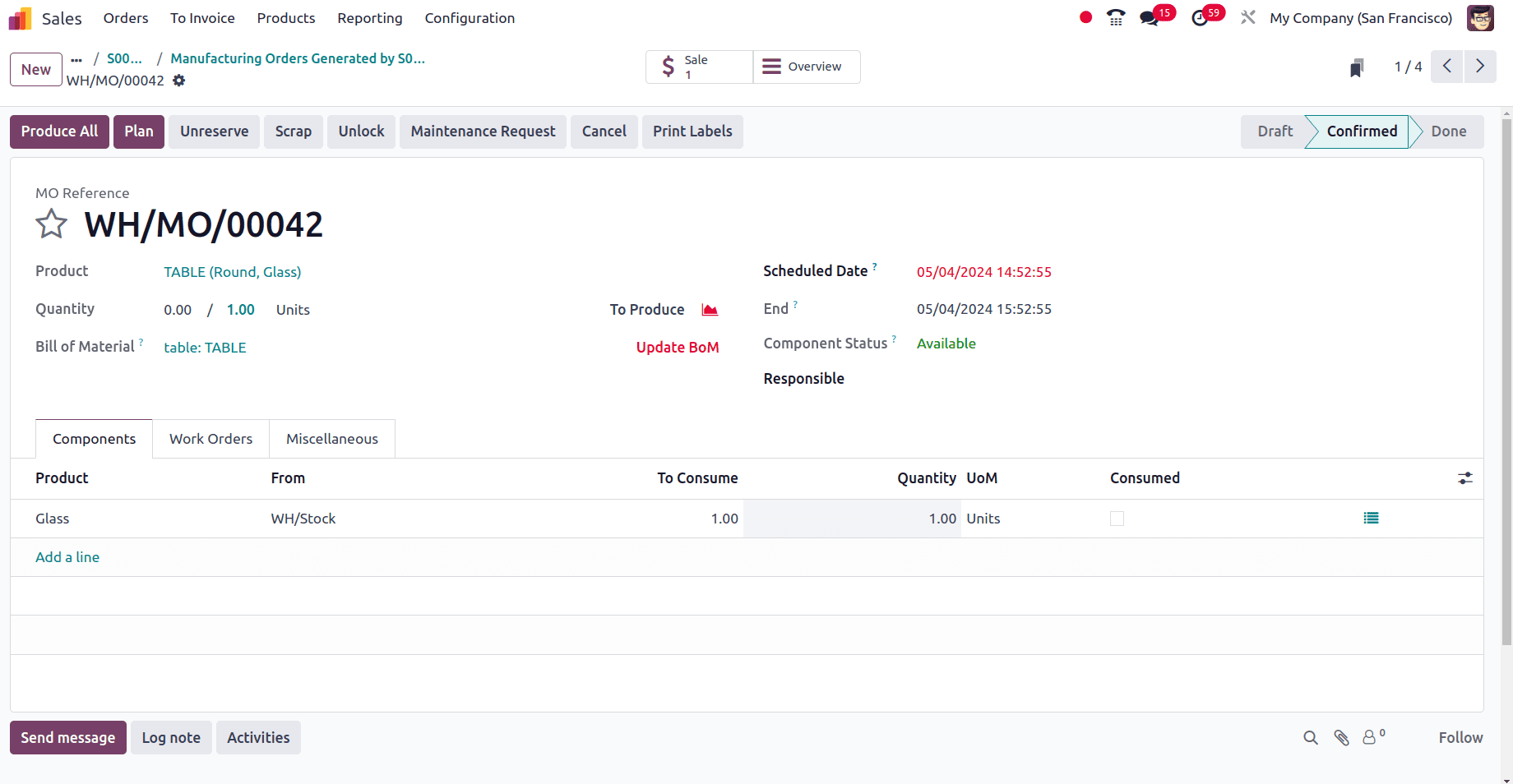
Because we have set work-center 1 for the round cutting operation or the work center configured for the manufacturing of round tables are ‘Work Center 1’
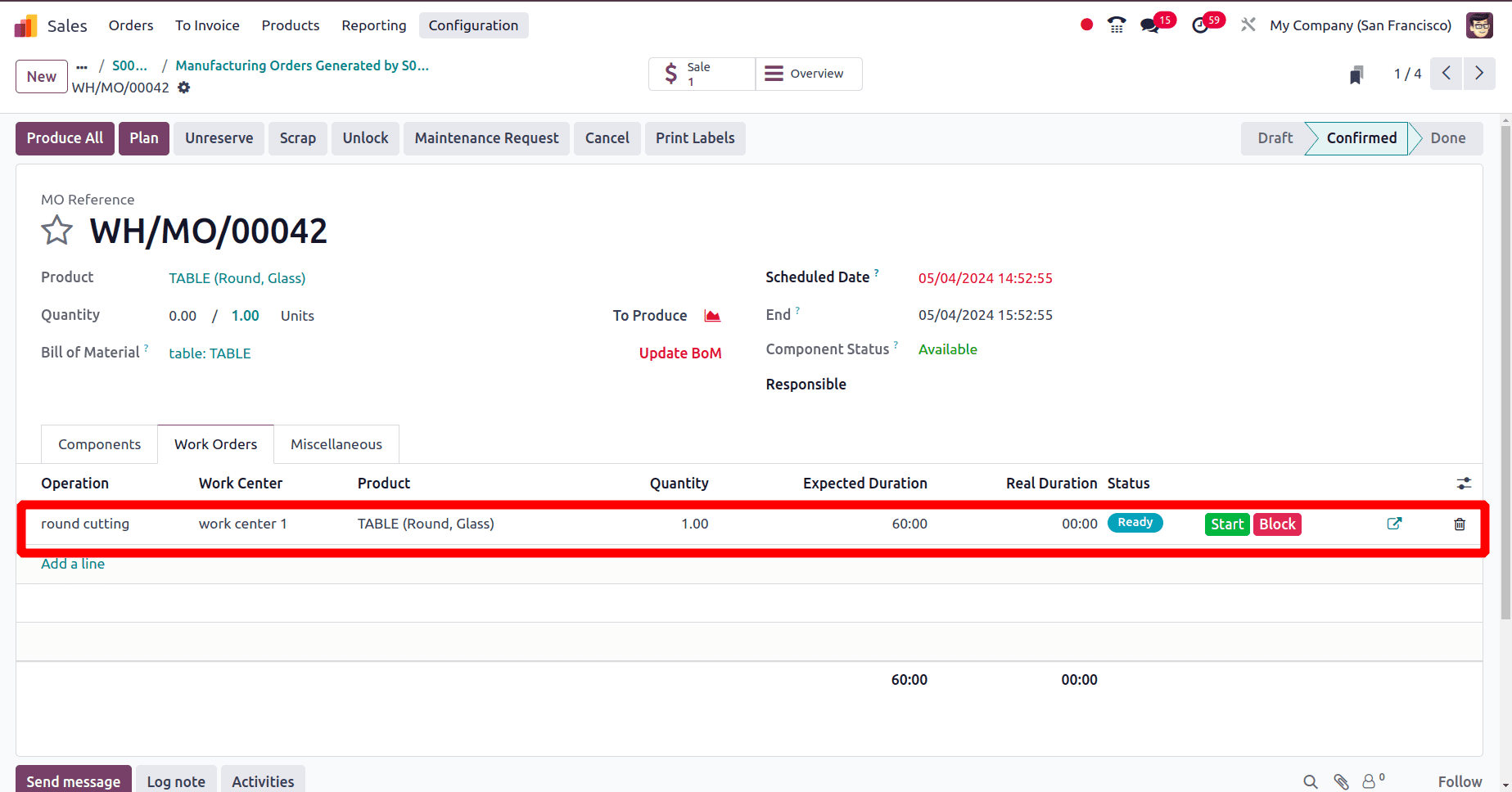
Here, the work center for the round table set is ‘Workcenter 1’ as we configured work center 1 for the round-cutting operation.
Through this, we can complete the manufacturing of the remaining 2 variants. After the production of all manufacturing orders, we can validate the delivery order.
Here a customer places an order for a table that has four different variants. And our company has 2 work centers for the manufacturing of the variants of the product. So here the manufacture of different product variants is conducted in different work centers. This feature helps a company to improve workflow efficiency. This speeds up the manufacturing process by directing each variant via its assigned work center. It also improves workflow efficiency by minimizing the production delay and Improves the overall workflow efficiency by removing the need for needless material and equipment transportation. It also reduces the setup time because each work center corresponds to a certain product type, and fewer equipment and process reconfigurations are necessary. This results in quicker changeovers and higher production flow.
So from this, we can conclude that the production of variants in different work centers in Odoo 17 helps a company to optimize manufacturing orders and to increase the efficiency and productivity of the company.
To read more about How to Configure Product Variants in Odoo 17 Manufacturing, refer to our blog How to Configure Product Variants in Odoo 17 Manufacturing.