What is Subcontracting in Odoo 18?
In Odoo 18, subcontracting is the process of getting the product from an external source or a manufacturer. Using Subcontracting BOM in Odoo Manufacturing provides several advantages for businesses, from cost efficiency and improved scalability to streamlined workflow and better cost tracking. It helps businesses outsource specific operations to specialized vendors, allowing for greater flexibility, optimized lead times, and the ability to focus on core operations. The integration within Odoo ensures the entire subcontracting process is smooth, efficient, and easy to manage. The main advantages or benefits of Odoo 18 subcontracting are its efficiency, cost tracking, inventory management, and supplier integration. This process helps businesses track costs for outsourced work and materials.
To use the subcontracting feature, move to the inventory module and select the warehouse. Then you have the option ‘Resupply Subcontractors,’ and you can enable this option.
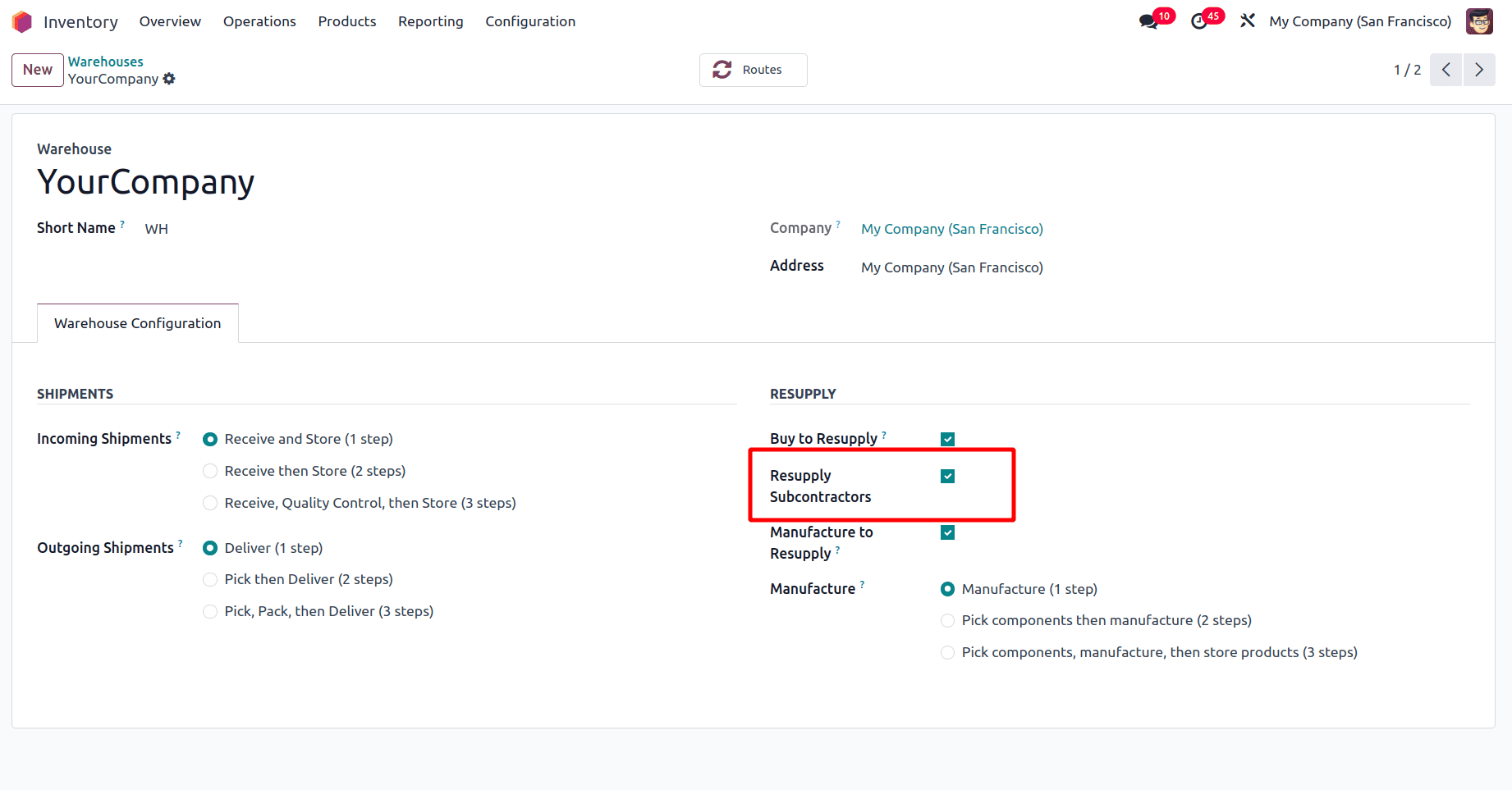
Then, the next step is to enable the subcontracting option in the configuration settings of the manufacturing module. So move to the Manufacturing module, and in the configuration settings, under the Operations section, enable the check box near the field Subcontracting.
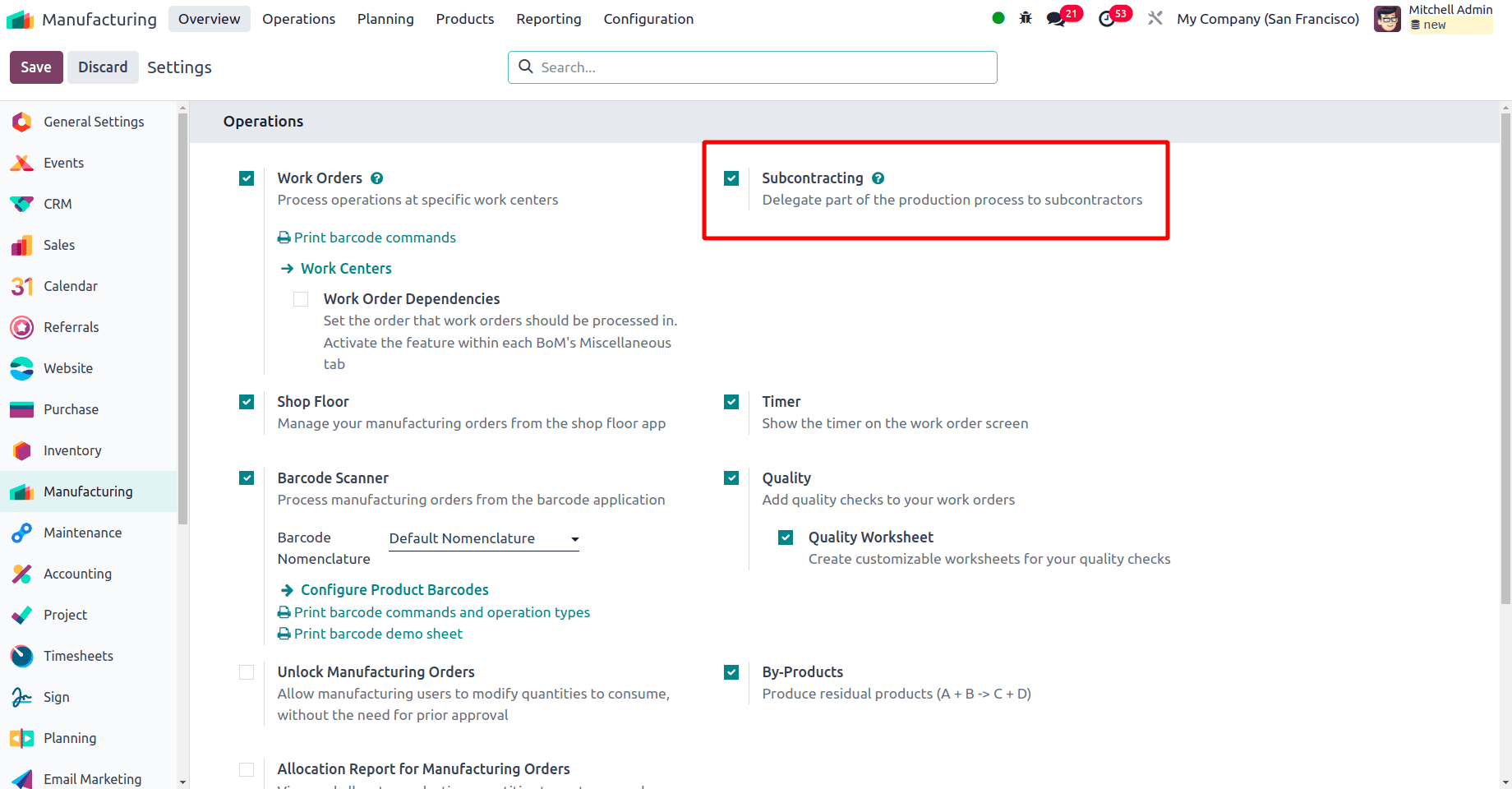
When subcontracting is enabled from the configuration settings, move to the products menu in the manufacturing module, and there will be a Bills of Materials sub-menu. Select this submenu and create a new bill of material. While creating the Bill of Material, there will be three Bill of Material types to use, which are Manufacture this Product, Kit, and Subcontracting.
* Manufacture this Product: Used to manufacture a finished product.
* Kit: used for assembly products that are sold as a set of items, or kits.
* Subcontracting: used when certain manufacturing operations are outsourced to an external supplier or subcontractor
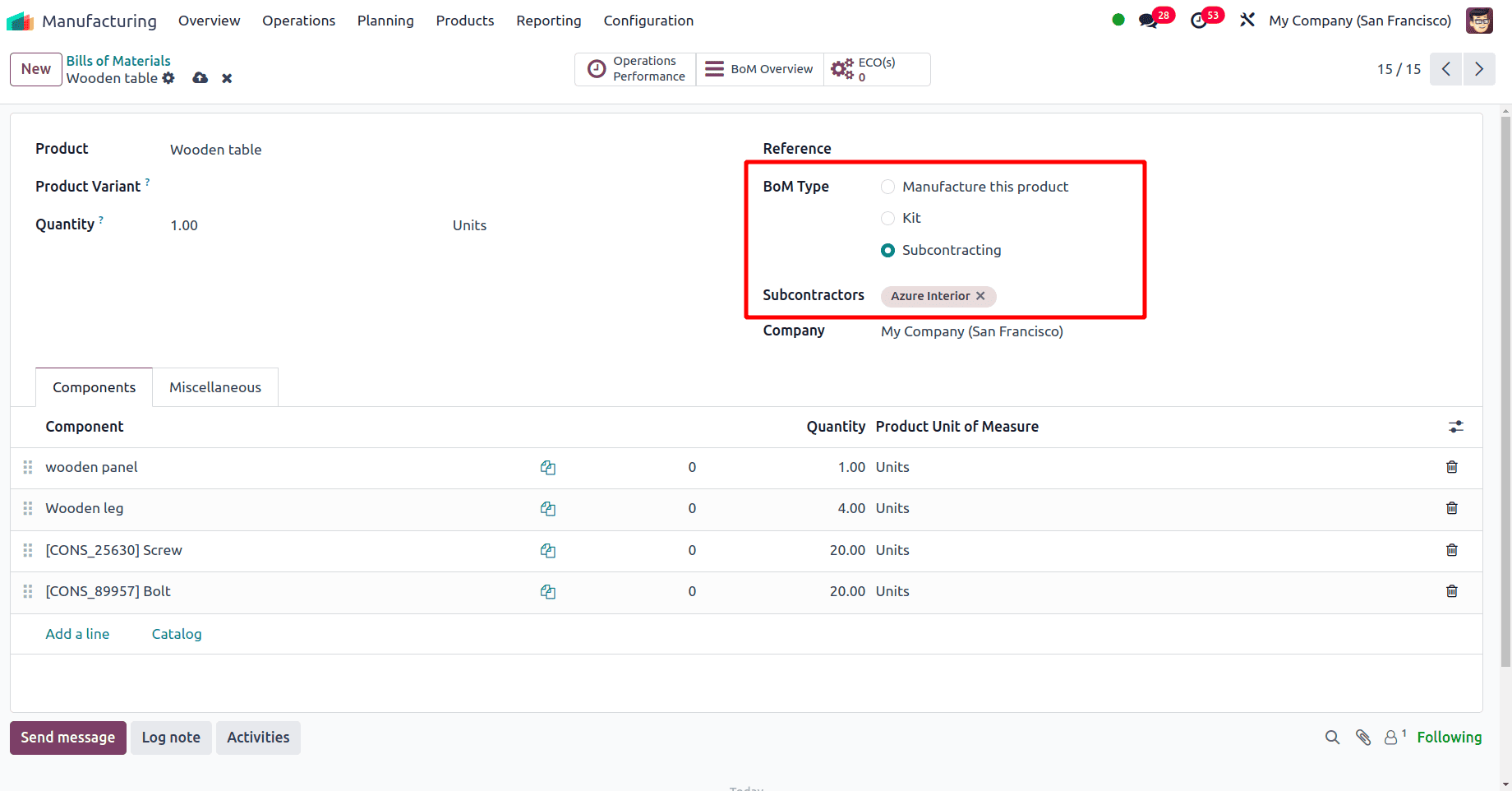
While creating the bill of material, there will be an option to select the BoM type. For this BoM, select the BoM type as Subcontracting. Then a new field has been added here, Subcontractor. Select the subcontractor of your product here. Then, click the save icon to save the BoM. For the components, select the vendor as the subcontractor. Then, the next step is to set the route for those components and for the product. Set the route in the product form as Resupply Subcontractor on Order.
On moving to products, open the form view of all the components used in this subcontracting order, move to the inventory tab, and set the route Resupply Subcontractor on Order.
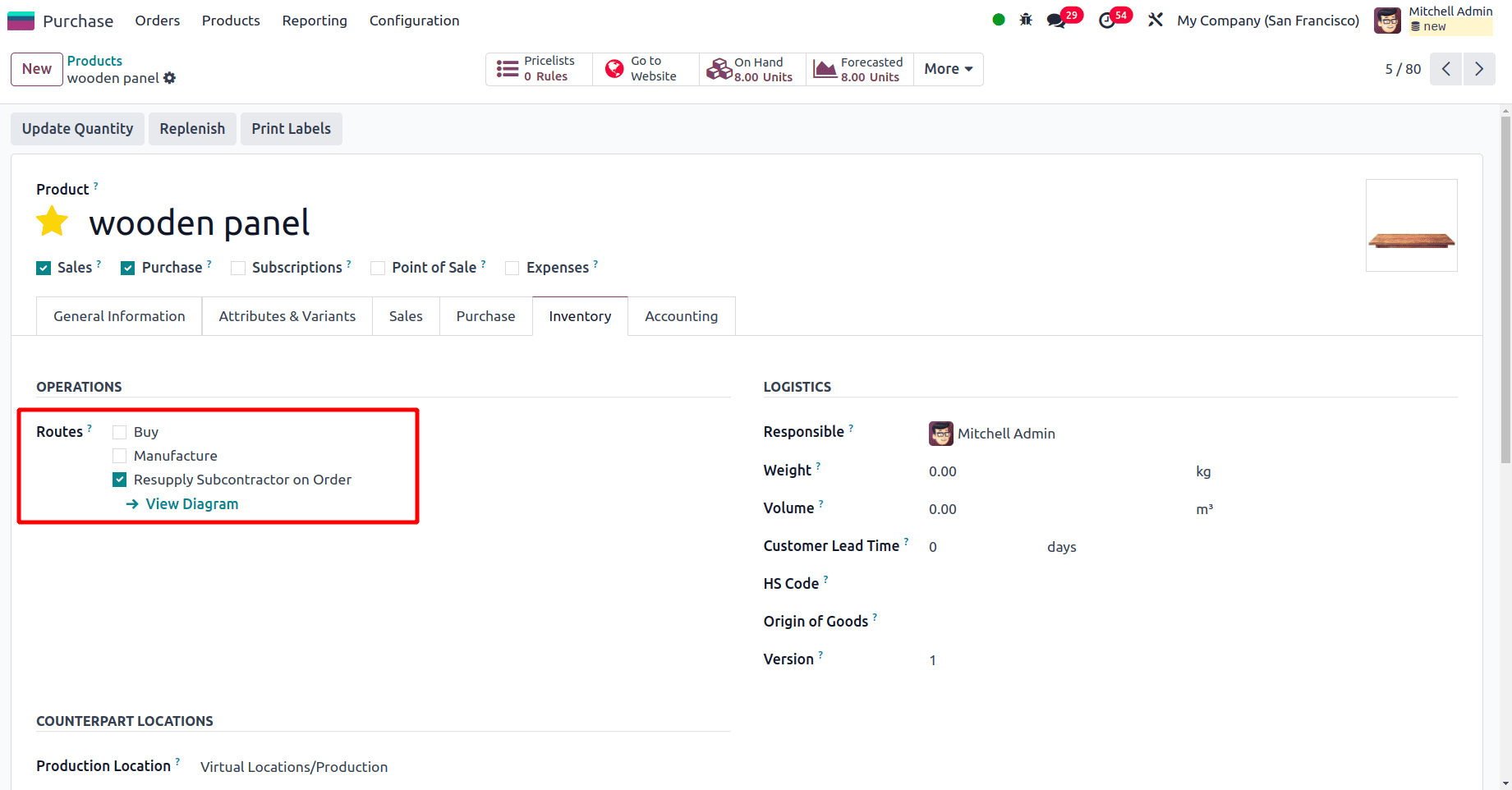
Similarly, set the route ‘Resupply Subcontractor on Order’ for all the component products in the Bill of Material. Then set the route ‘Buy’ for the main product in the Bill of Material.
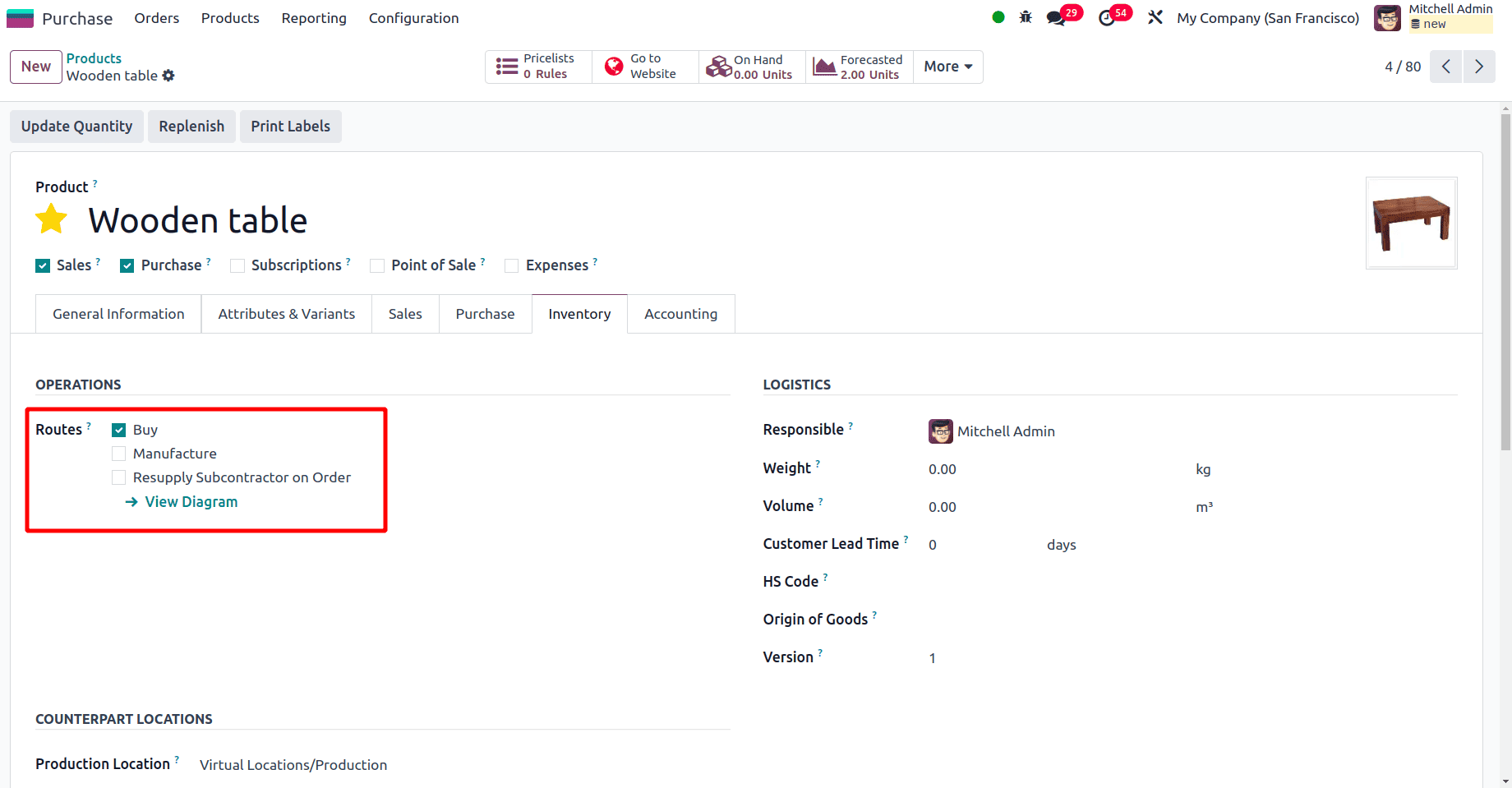
Then move to the form view of the components as well as the main products and set the subcontractor of the Bill of material as the vendor of all these products.
On moving to the purchase tab of the product, there will be the option to add the vendor of each product.
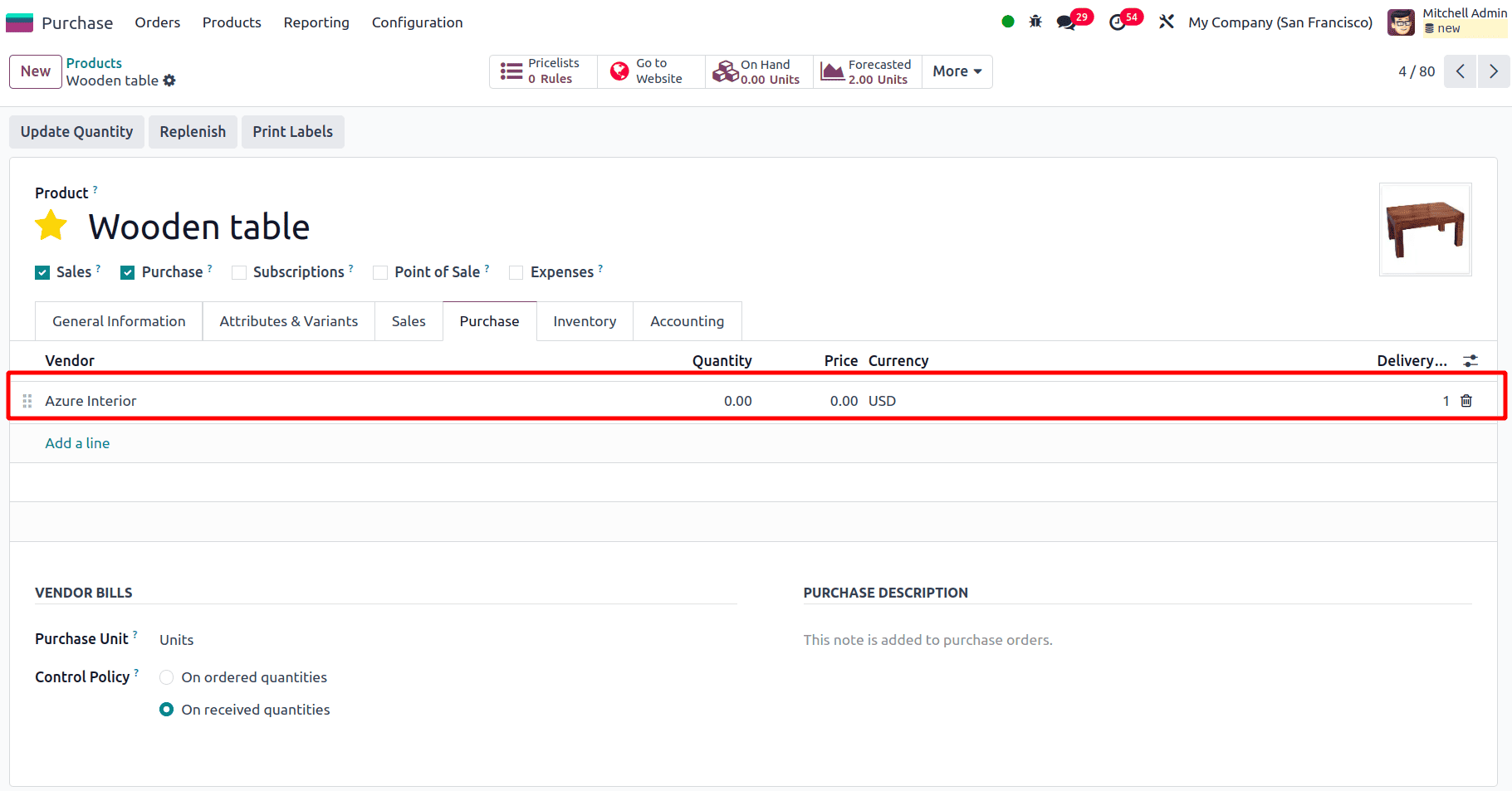
Similarly, you can set the vendor for each and every product separately. Once a vendor is set here, this vendor will be the subcontractor of that product.
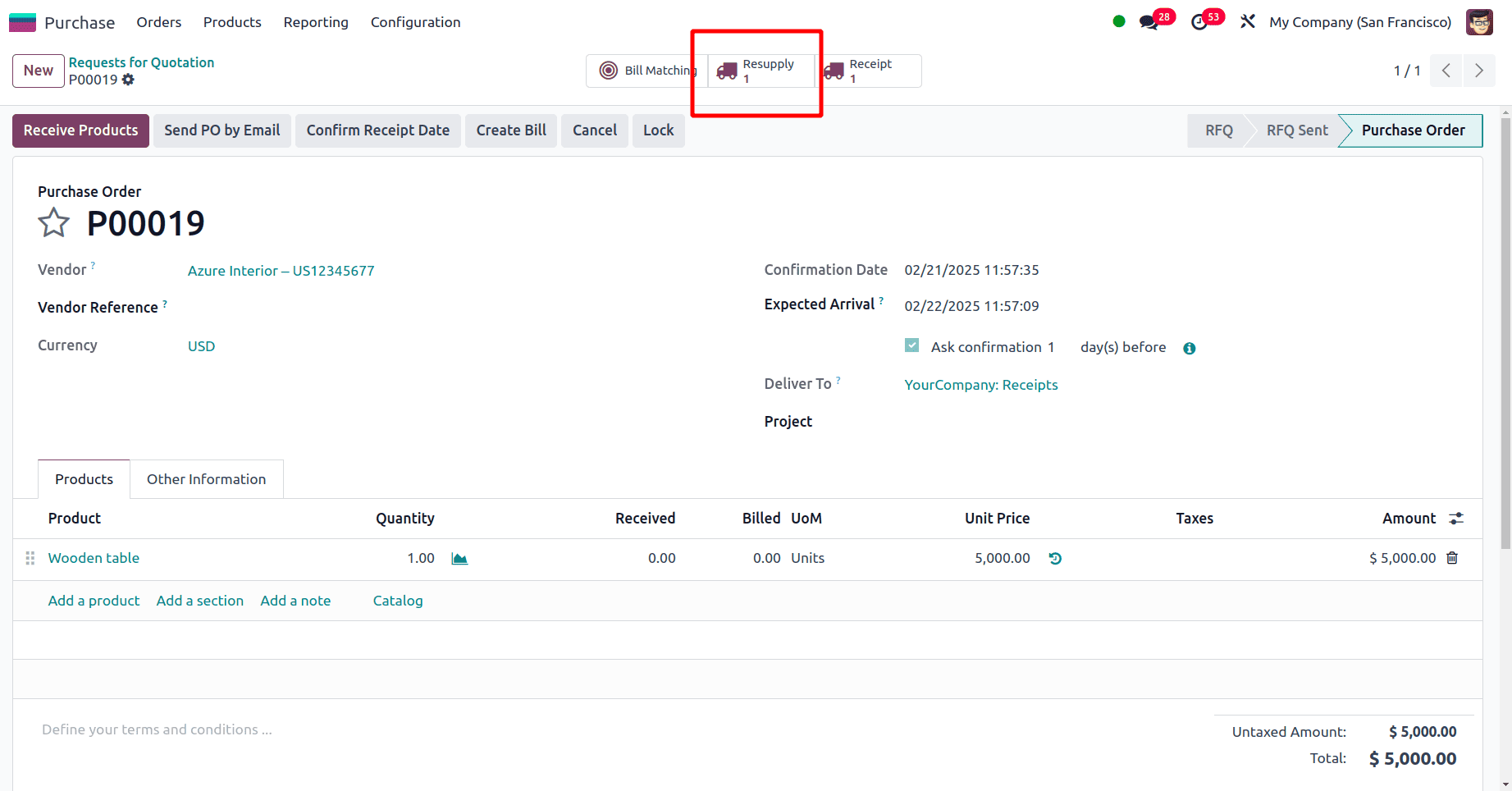
The next step is to create a new Purchase order for this product. While creating the purchase order, add the subcontracted product in the order line. Once the purchase order is confirmed, there will be a Resupply smart tab at the top, as shown in the screenshot above.
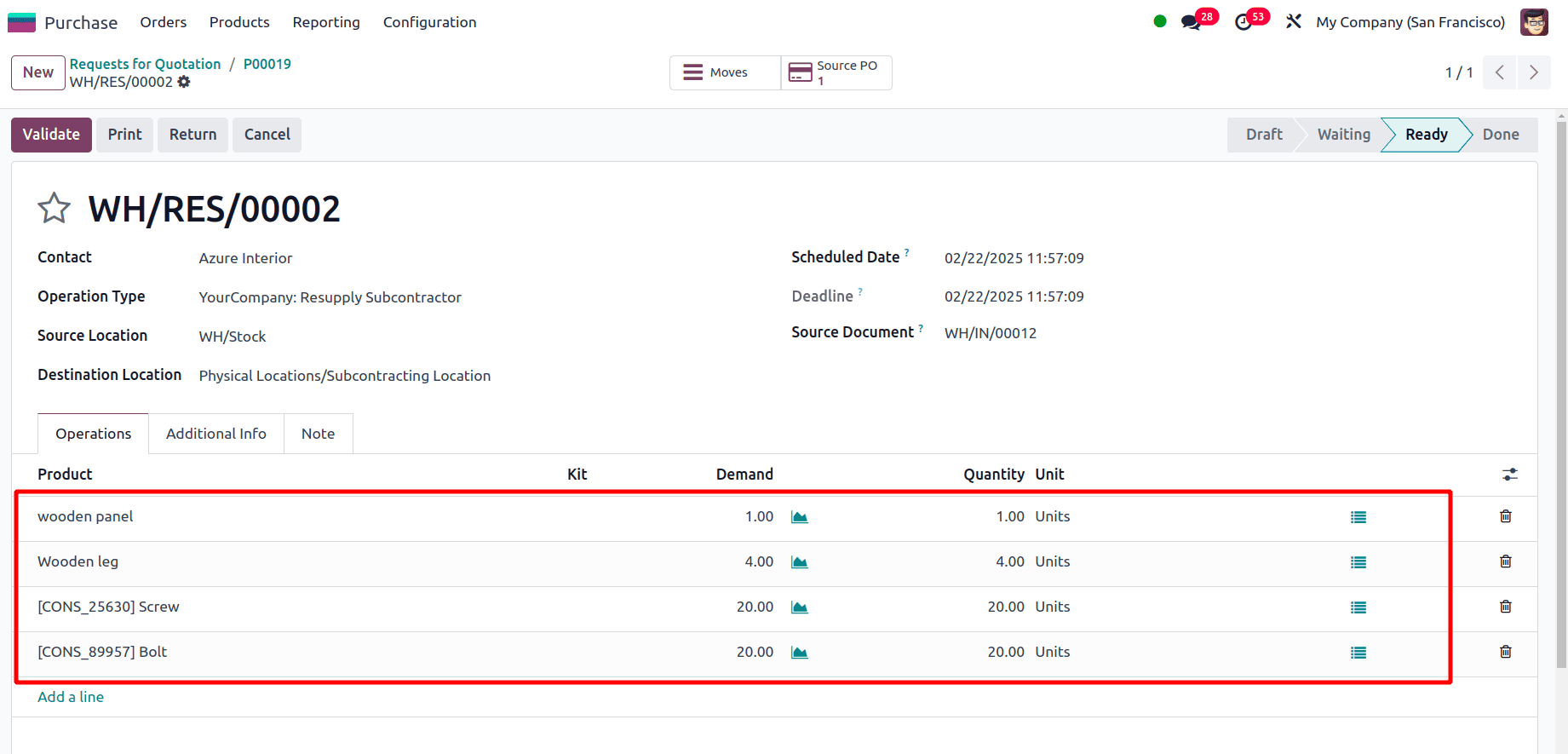
On clicking the resupply smart tab, the details of the resupply operation will be shown, and there the destination location will be the subcontracting location. In the product line, the product and the quantity needed will be shown. There will be a validate button to validate the resupply operation. On clicking the validate button, this operation will be validated.
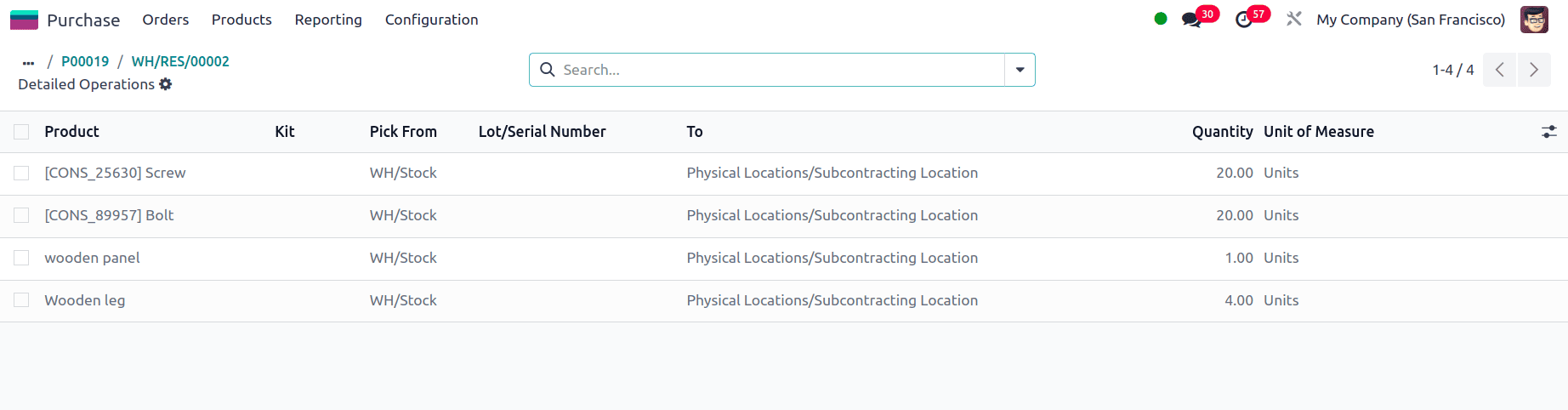
On moving to the Moves tab, all the components in the BoM will be listed, and where the products are picked is also mentioned there.
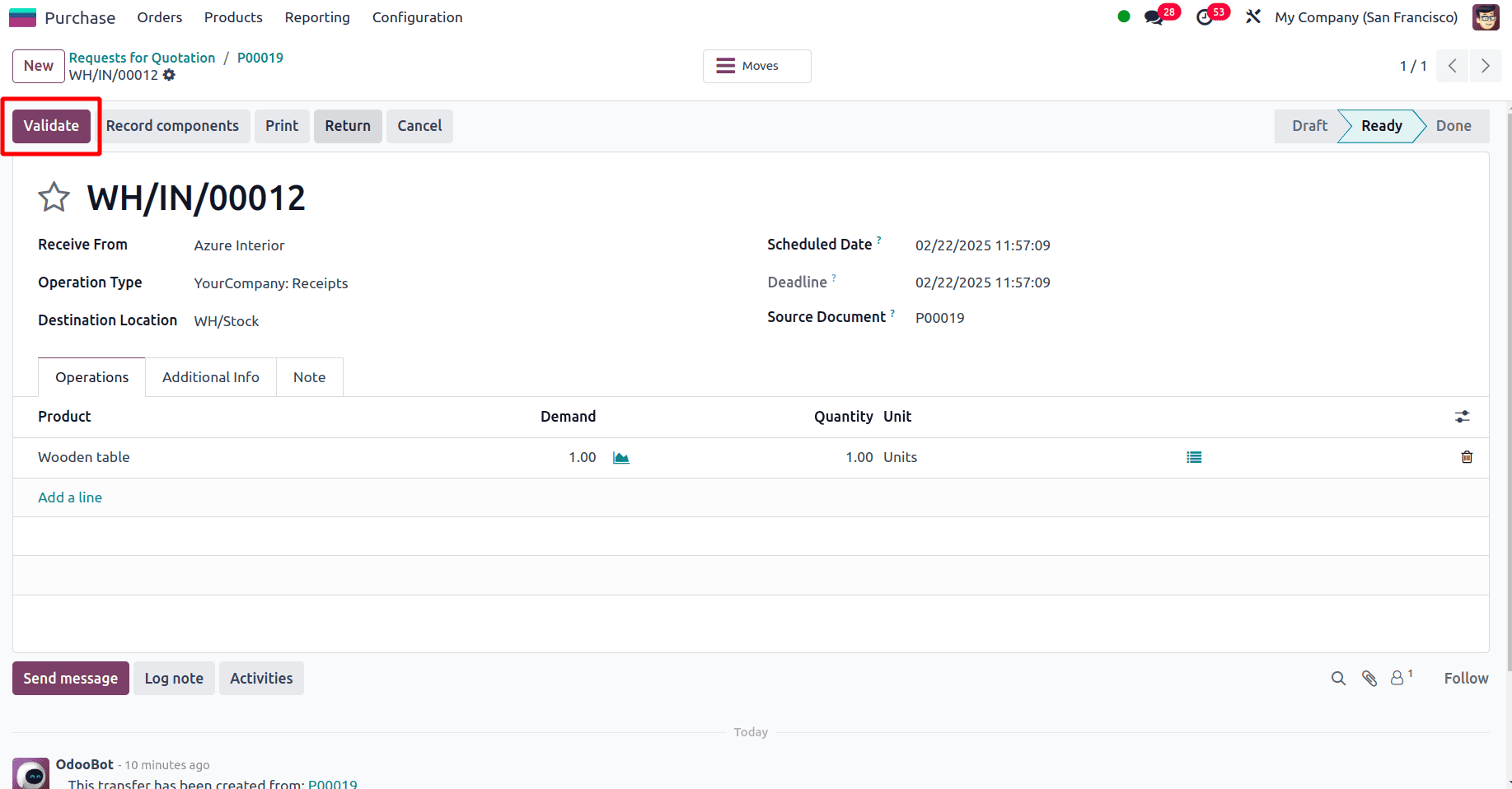
On moving to the purchase order, there will be the option to receive the main product and validate the purchase order. When the purchase order is validated, the purchase process of the Wooden table product with a bill of material subcontracting is completed.
When manufacturing a product, certain operations might be better handled by external vendors rather than in-house due to cost or expertise like packaging, assembly, or special machining. By using this Subcontracting BoM type, you can specify that a particular operation is to be subcontracted and assign it to a specific supplier. When using subcontracting, Odoo helps track the flow of materials sent to the subcontractor and their return after processing. The materials can be tracked within the system as they leave the company and return after the subcontracted operations. For instance, if a part is sent to a subcontractor for assembly, Odoo will keep track of the stock movement as the components are shipped out and the finished product is received back. The subcontracting process also manages the inventory so that the materials sent to the subcontractor are deducted from the company’s inventory, and finished products returned from subcontractors are added back to the inventory.
To read more about how to set up Subcontracting in Odoo 17 Manufacturing, refer to our blog post How to Setup Subcontracting in Odoo 17 Manufacturing.