Equipment is crucial in the production process. The entire manufacturing process will be impacted if an equipment failure occurs while processing a work request. In order to minimize losses, the maintenance process should be started as soon as the equipment fails. The modules for manufacturing and maintenance are integrated into Odoo. Therefore, equipment maintenance is simple both before and after production. Let's look at how it functions in Odoo 16.
The maintenance module can be used to develop new equipment. Visit the maintenance module; the equipment tab is there. Then select the Machines & Tools option. Click the New button to add a new piece of equipment.
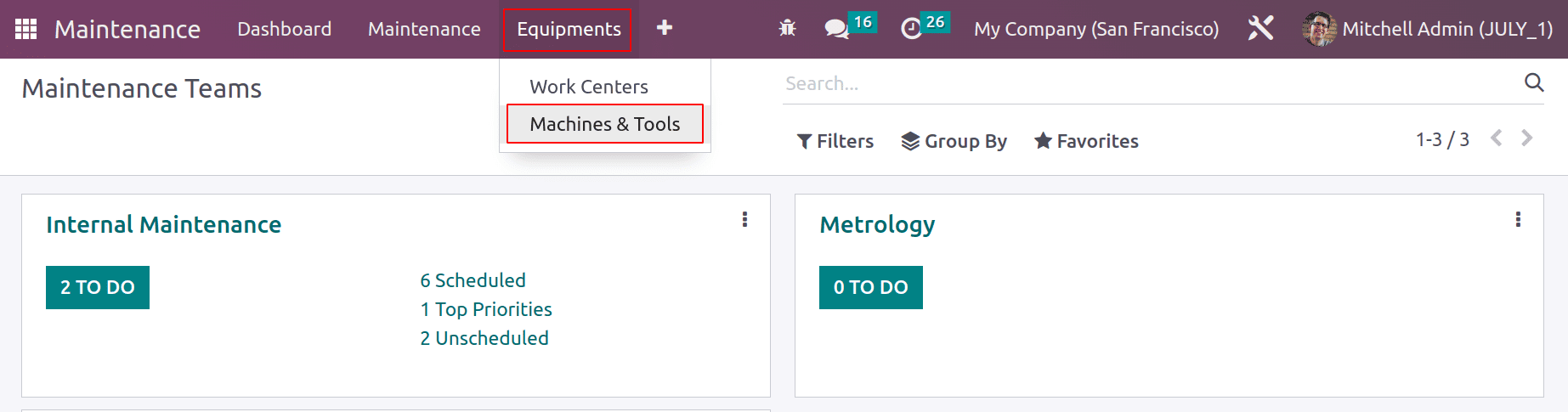
Include the equipment name in the equipment. Then include other information such as Category, Company, who used it, Maintenance Team, Technician, Assigned date, Scrap date, and place of use. The user can indicate the Work Center where the equipment will be used here as well.
The produced equipment in this instance is a spinning machine that is employed in the Garment Factory work center.
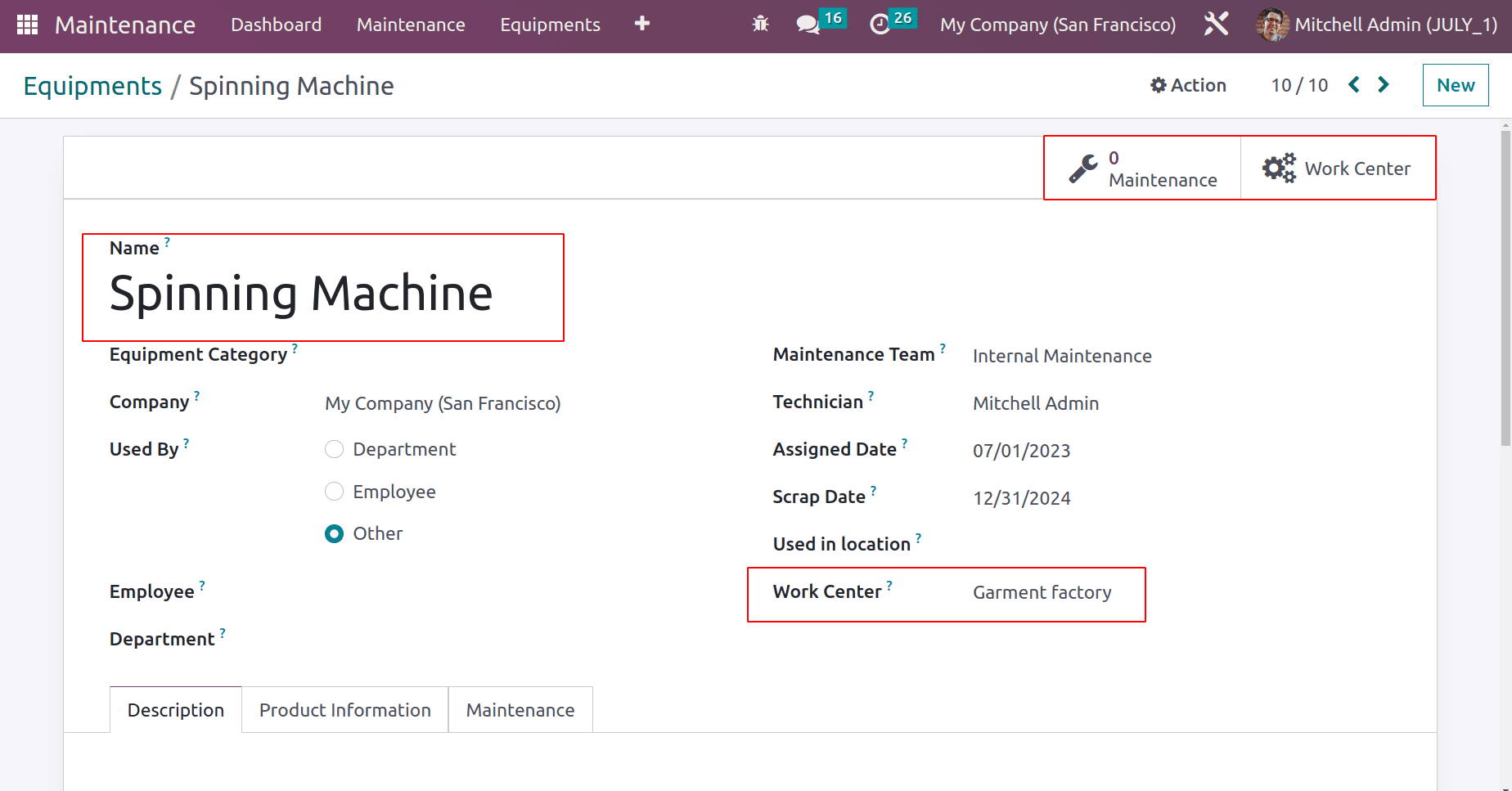
Add details about the product, such as the vendor name, Vendor reference, Model, Serial number, Cost of the equipment, Effective date, and Warranty expiration date, inside the Product Information tab. The equipment becomes operational as of that date, which is the effective date in this case.
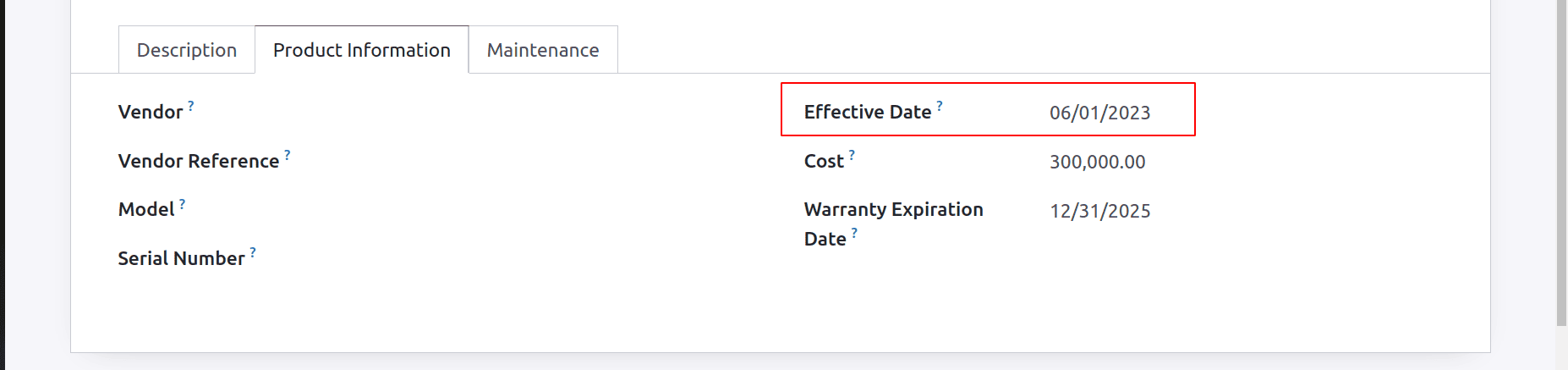
The maintenance tab will be updated with information regarding equipment upkeep. The Preventive maintenance frequency is 30 days. The next preventive maintenance date is now July 1st from the effective date to 30 days, or from June 1 to 30 days. 90 days are added to the expected mean time between failures.
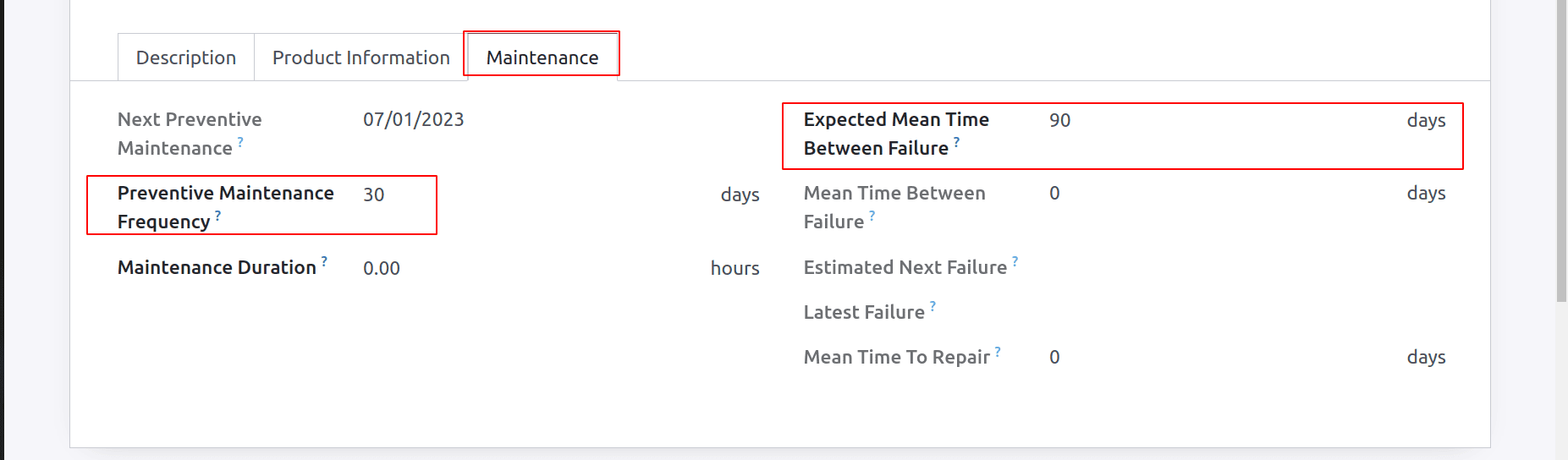
This equipment contains two smart tabs. One is Workcenter, and the other is Maintenance Request. All of the maintenance requests made for this item are displayed in the first tab. There isn't a request at the moment. A second Smart Tab Workcenter should now be opened.
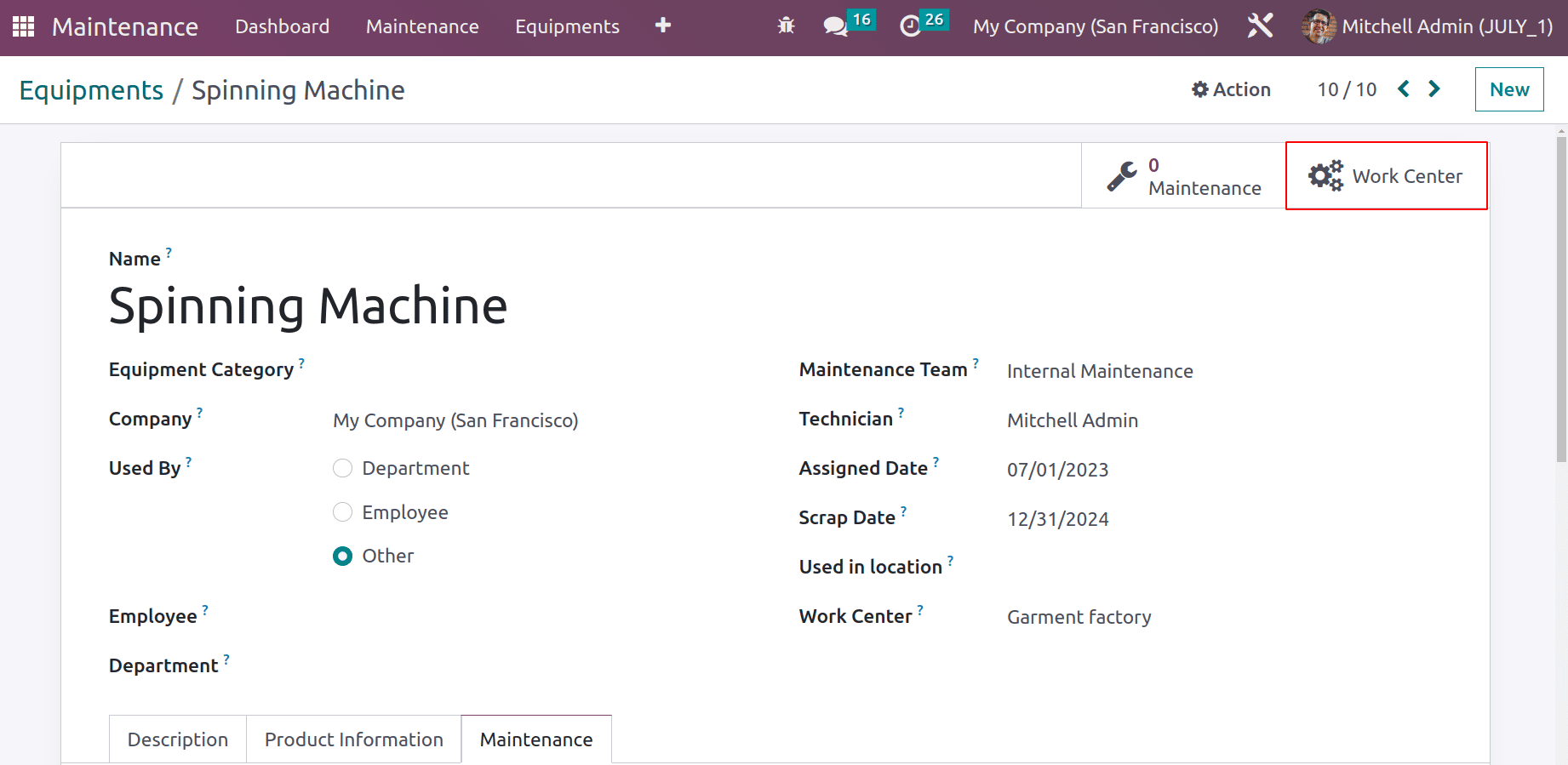
The workcenter where this equipment was added is shown. The workcenter in this instance is a garment factory. After that, a new tab inside the workcenter with the name Equipment is introduced. This includes information regarding the equipment's maintenance, such as MTTR and MTBF.
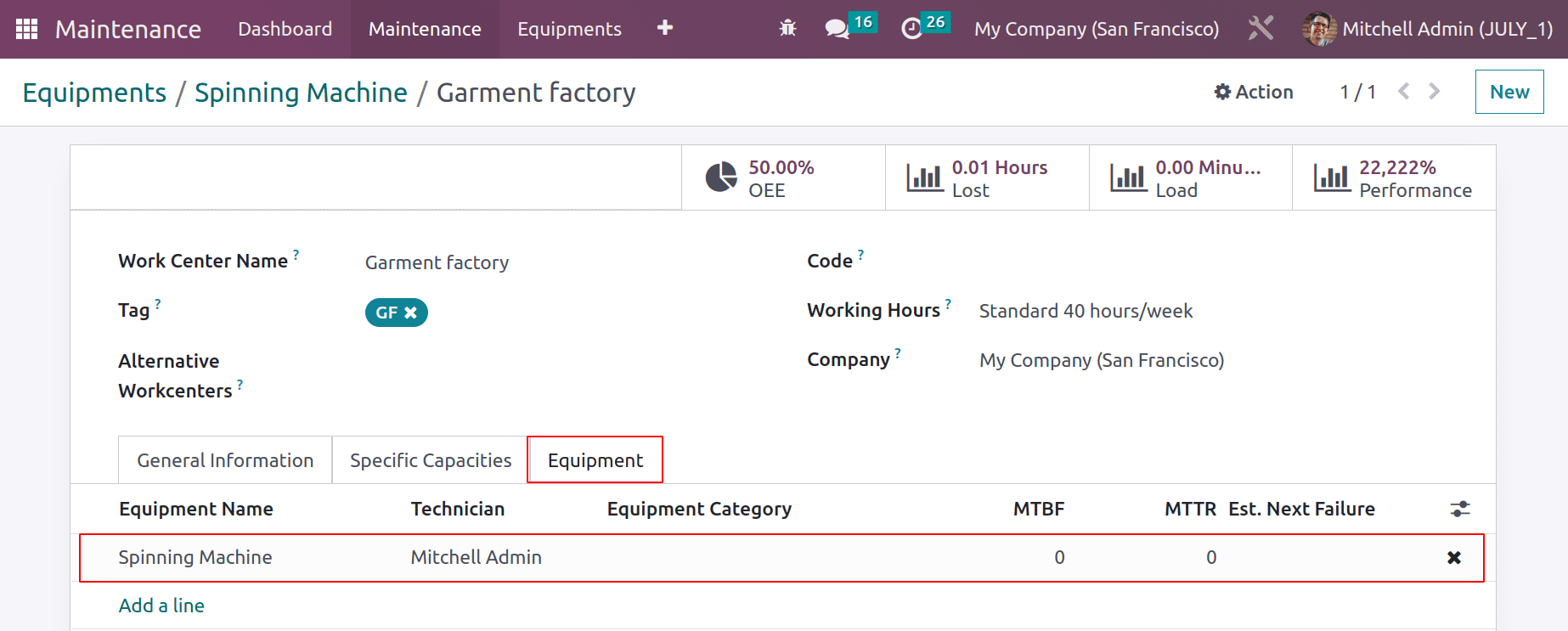
Let's put together a bill of materials for the production. Here, Cotton is the chosen product, and Cotton Fibre is the chosen component. This product's BoM Type is ‘Manufacturing this product’.
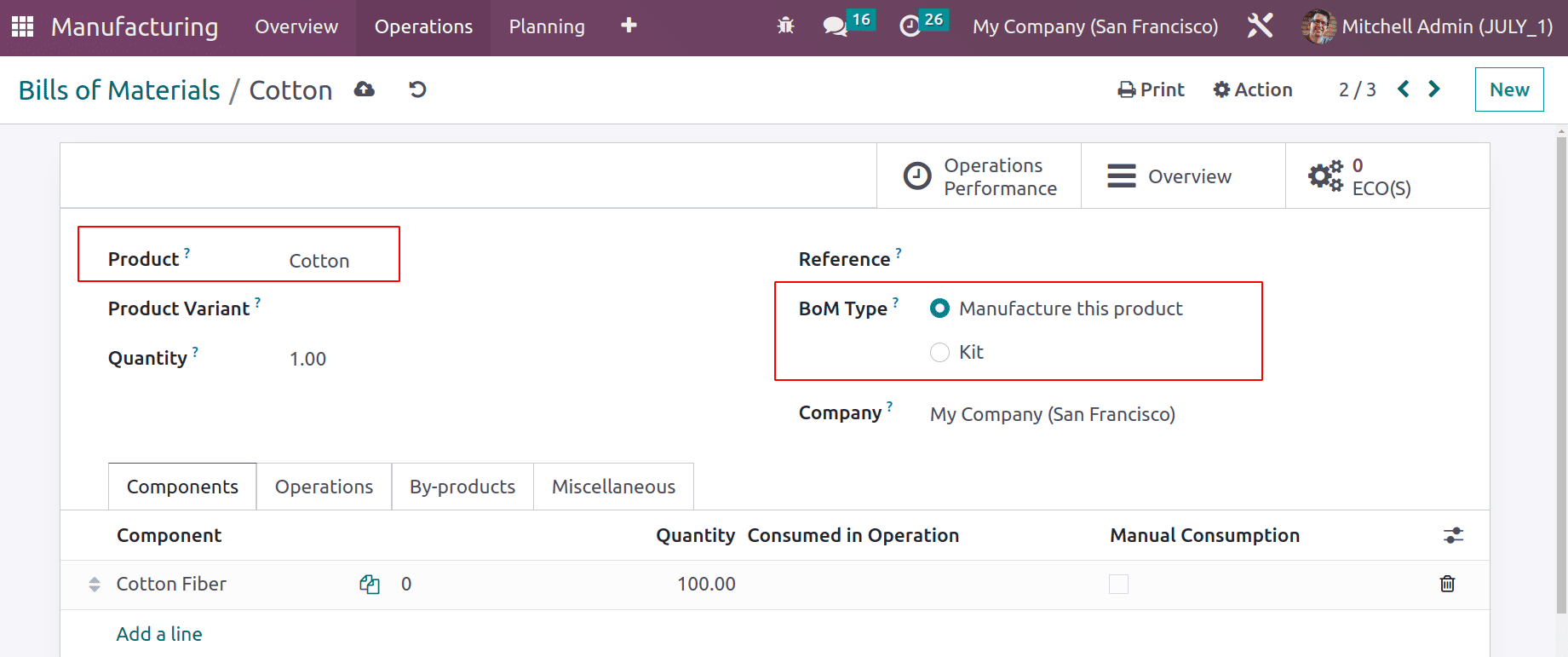
The production process requires two procedures to be finished. Here, the initial process is Ginning, which is carried out within the Assembly Line 1 workcenter. The second procedure is Spinning. Spinning machine equipment is required to do this task. Spinning machines are accessible in the workspace referred to as the Garment Factory. Therefore, this procedure was carried out inside the Garment Factory workcenter.
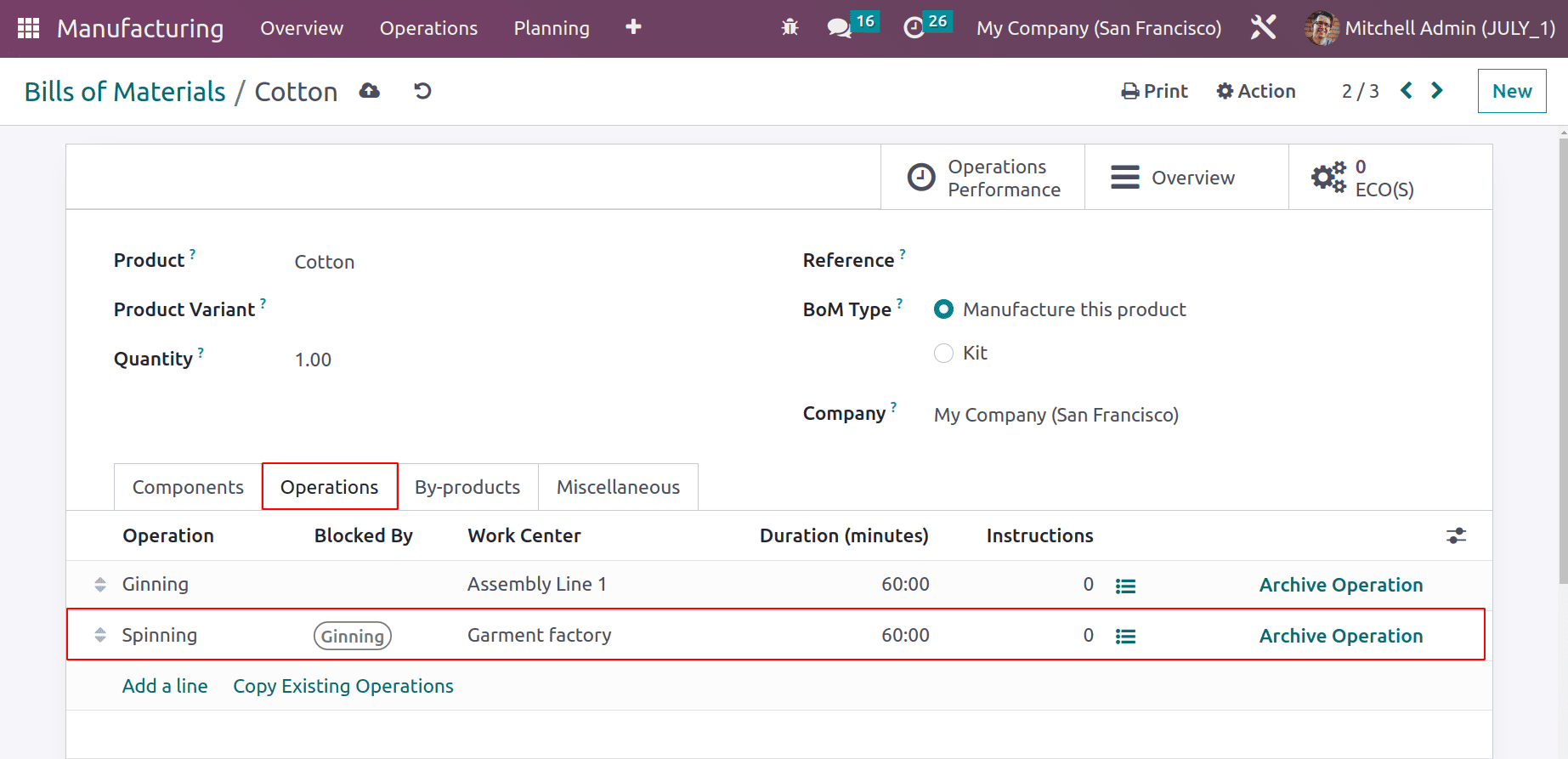
Save the bill of materials after you've added all the information, then go on to the production procedure. Click on Operations and select manufacturing orders to start a new manufacturing order. Create a new one. Select Cotton as the product. By uploading the produced bill of material, all the details added there will be updated immediately. After that, press the Confirm button.
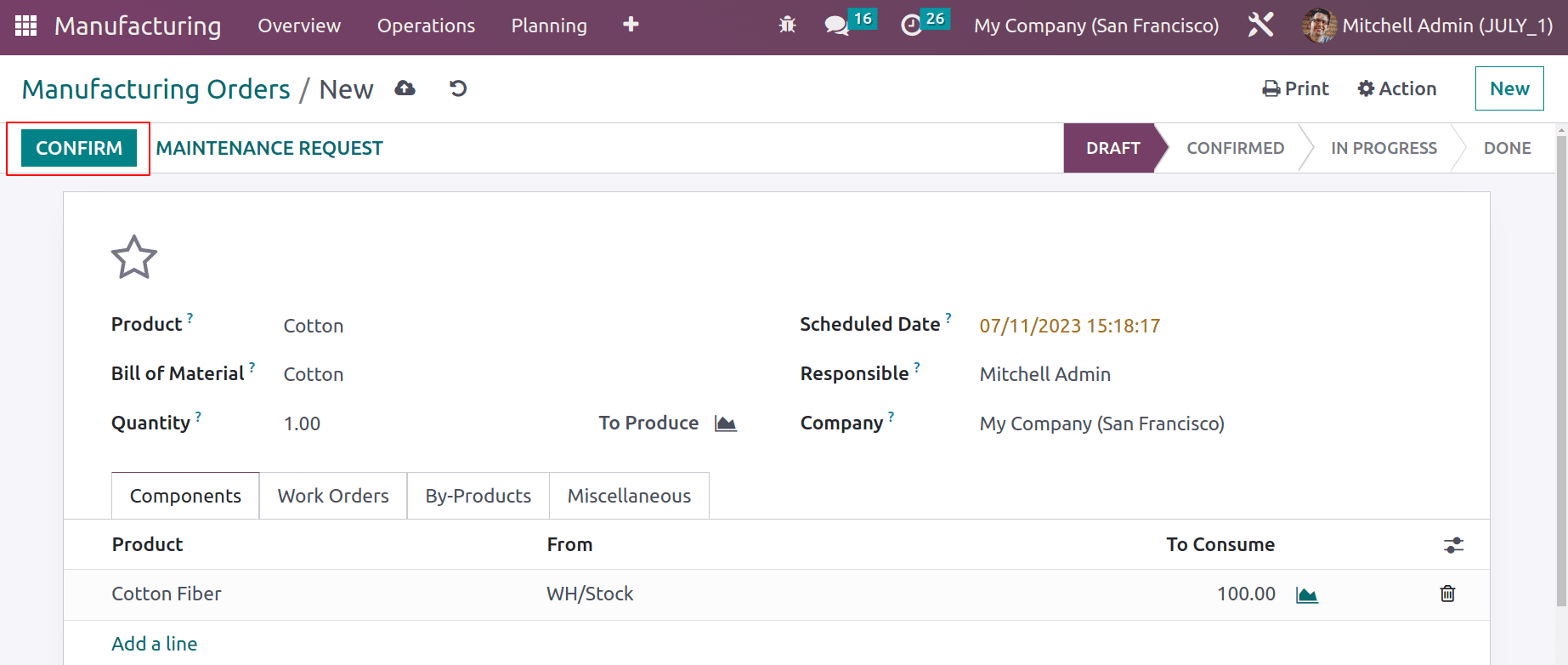
The Ginning stage is changed to Ready once the operation has been confirmed. Click the start button, to begin the process. The second operation can begin once the first has been completed.
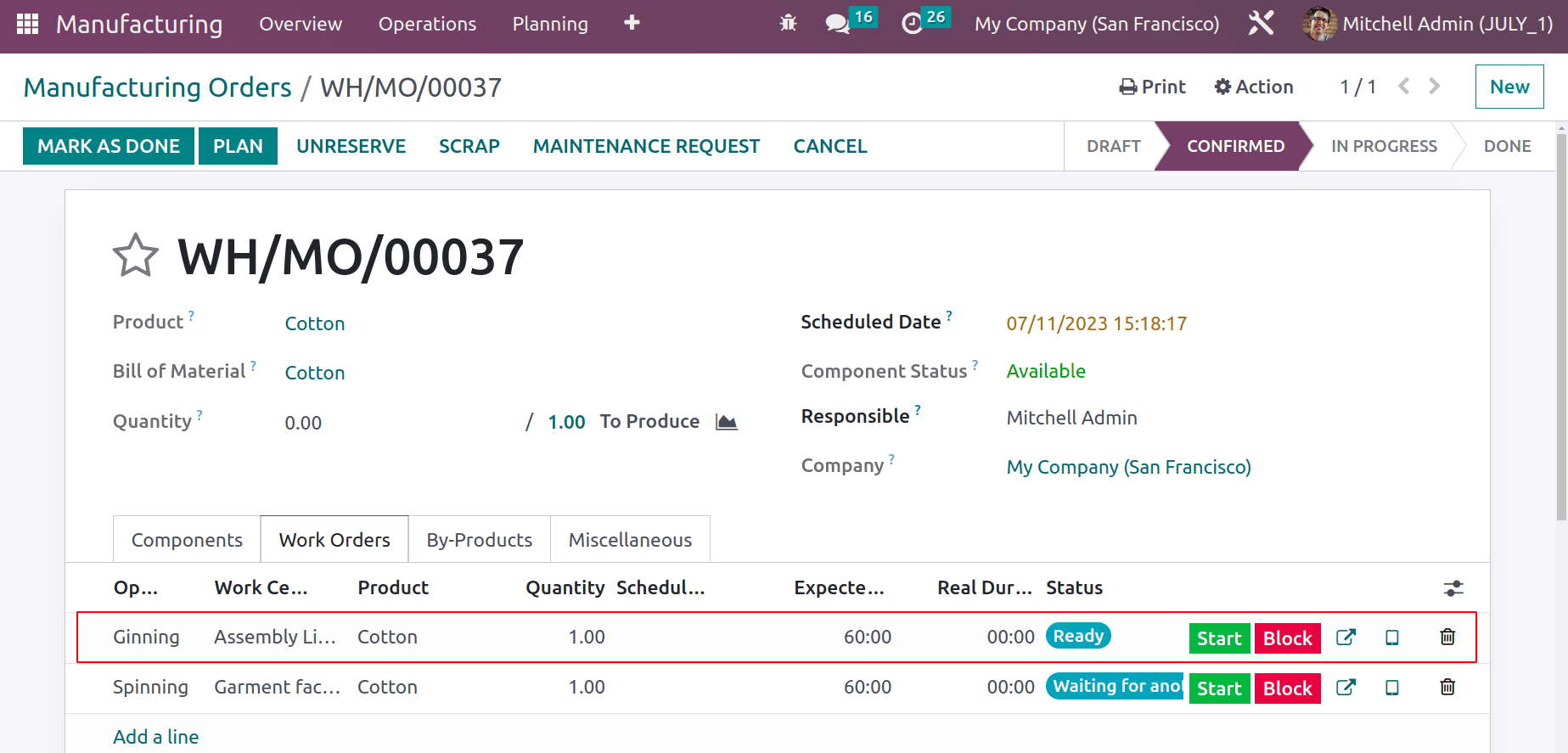
After the first operation is finished, the second one is in the Ready stage. Clicking the start button will initiate the operation.
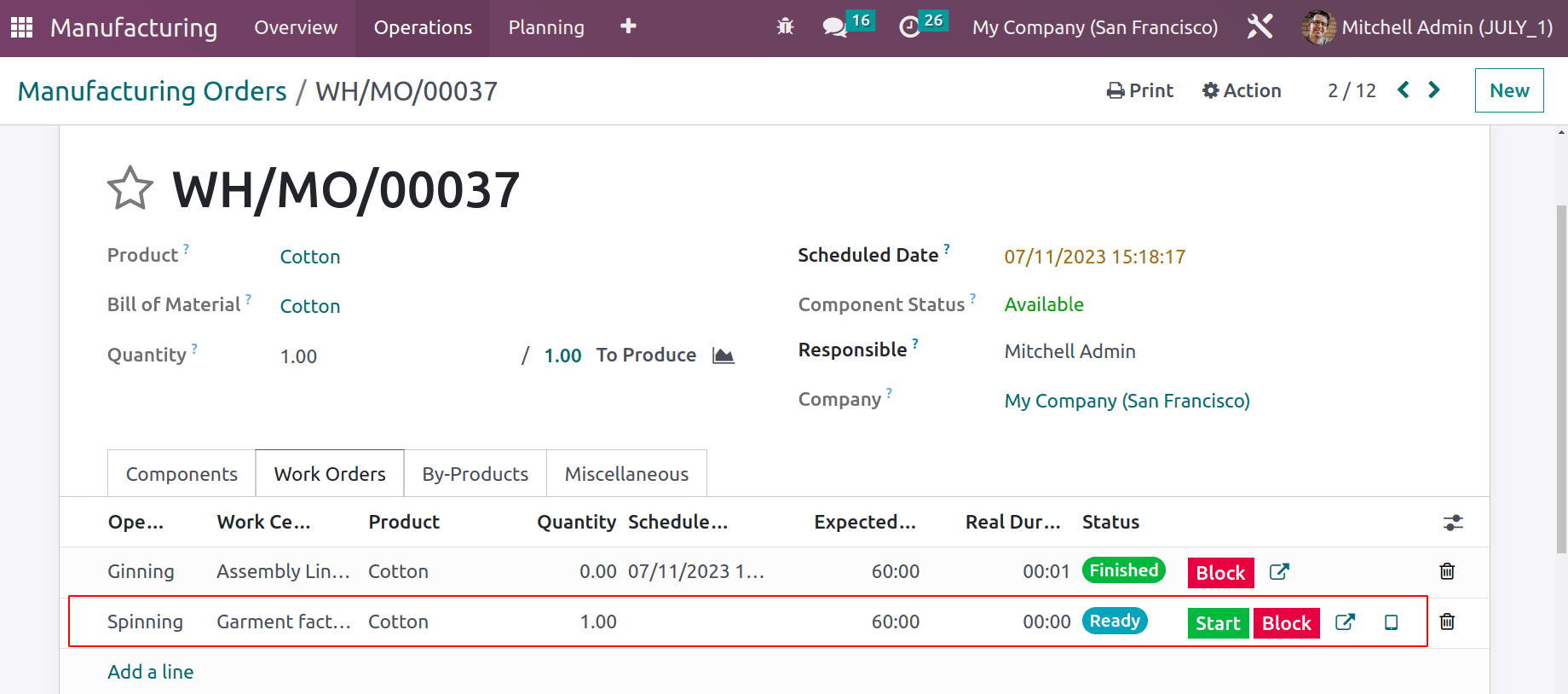
Consider that, in between the operation performed, the equipment will be damaged. So in such cases, the operator can request maintenance from the manufacturing module, which means no need to go to the maintenance module to add a maintenance request. Let's check how it happened. For that, click on the tablet view of the operation Spinning.
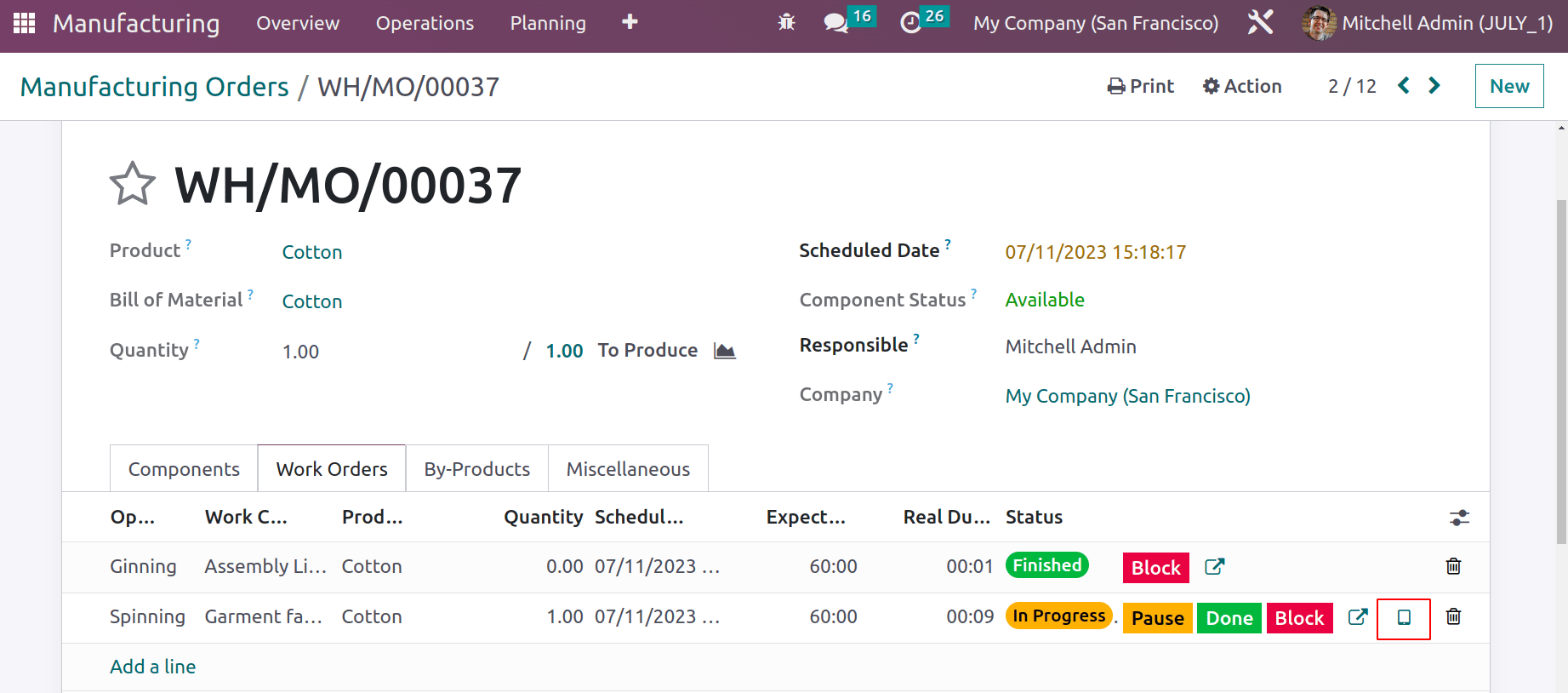
There is a button named Maintenance Request that can be used to create a new maintenance request. Click on it.
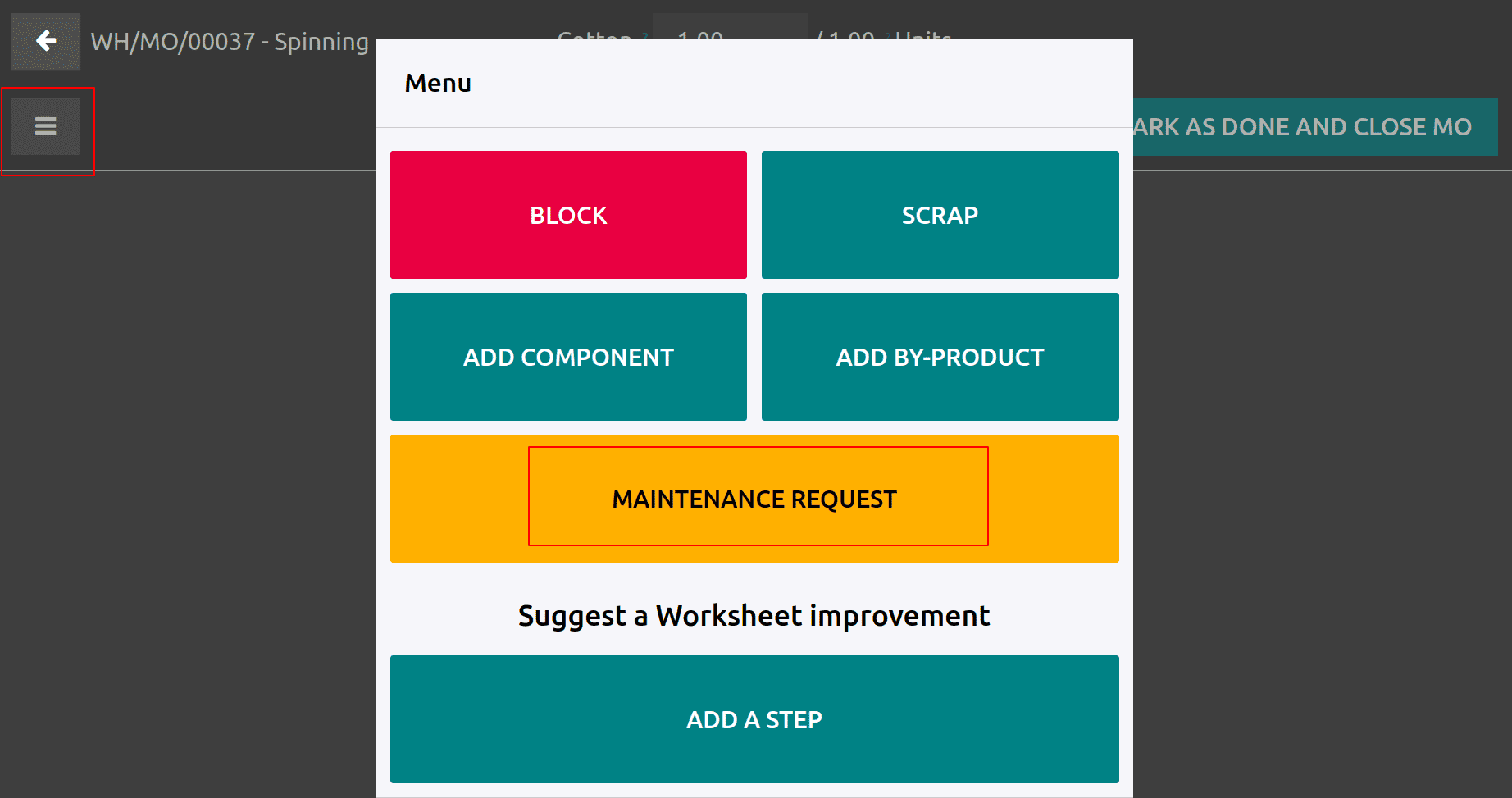
Add the request. Here choose the equipment. The details like Manufacturing order and work order are updated there. Save the request.
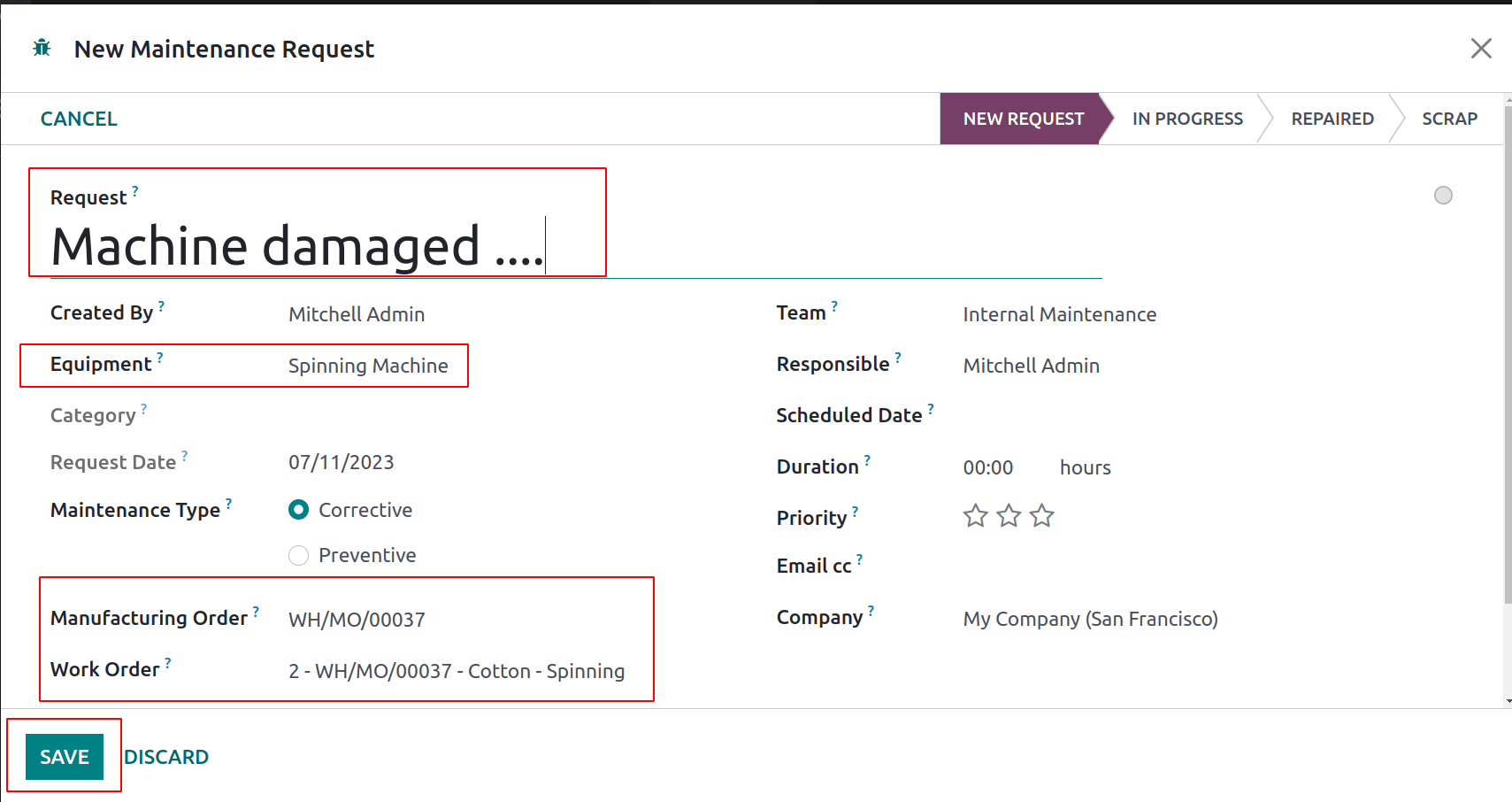
Before that, the operator can block the operation to perform. For that, click on the Block button.
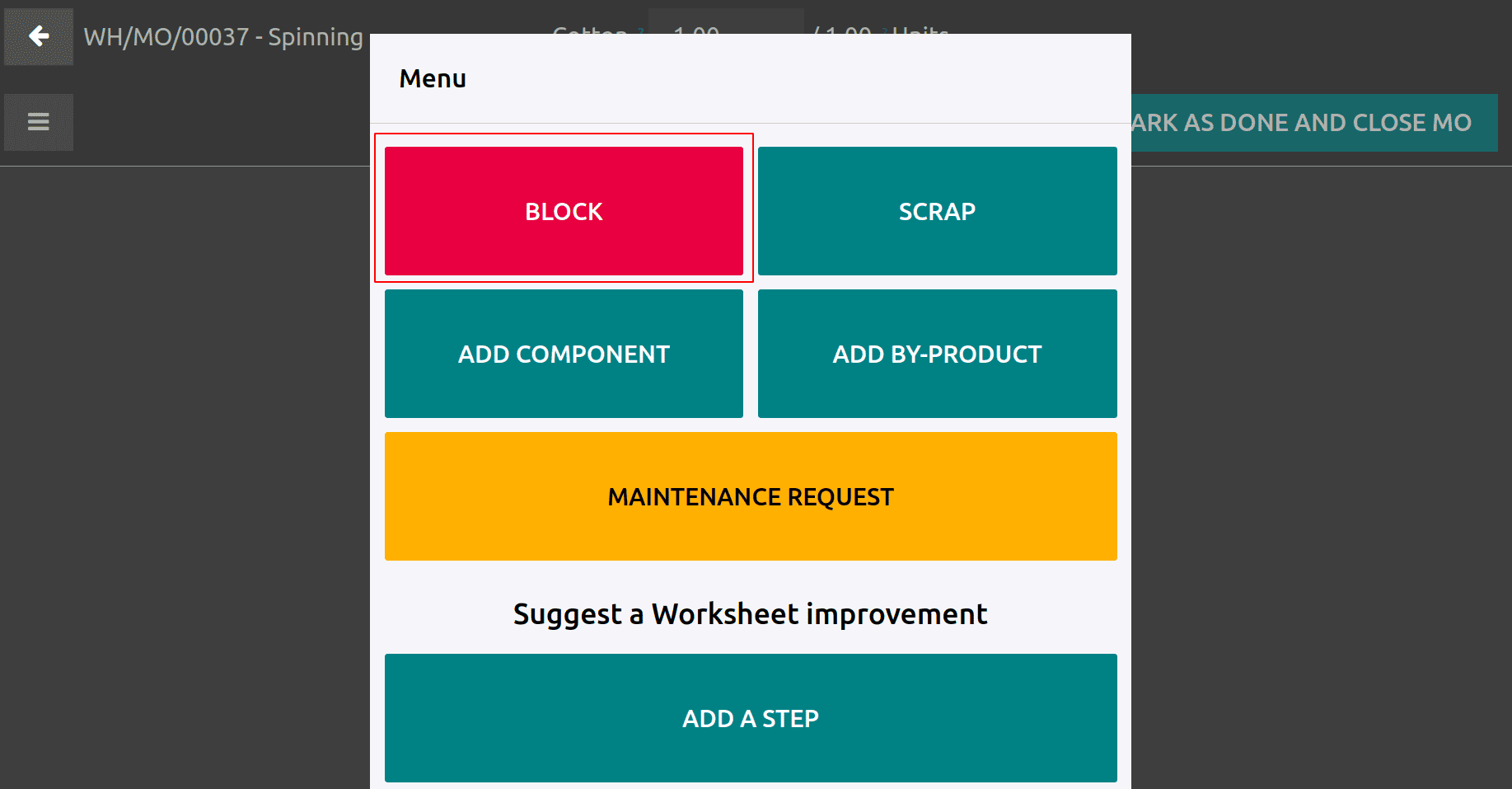
Before blocking, the operator must add a Loss reason. Here Equipment Failure is added as a reason. Click the Block button.
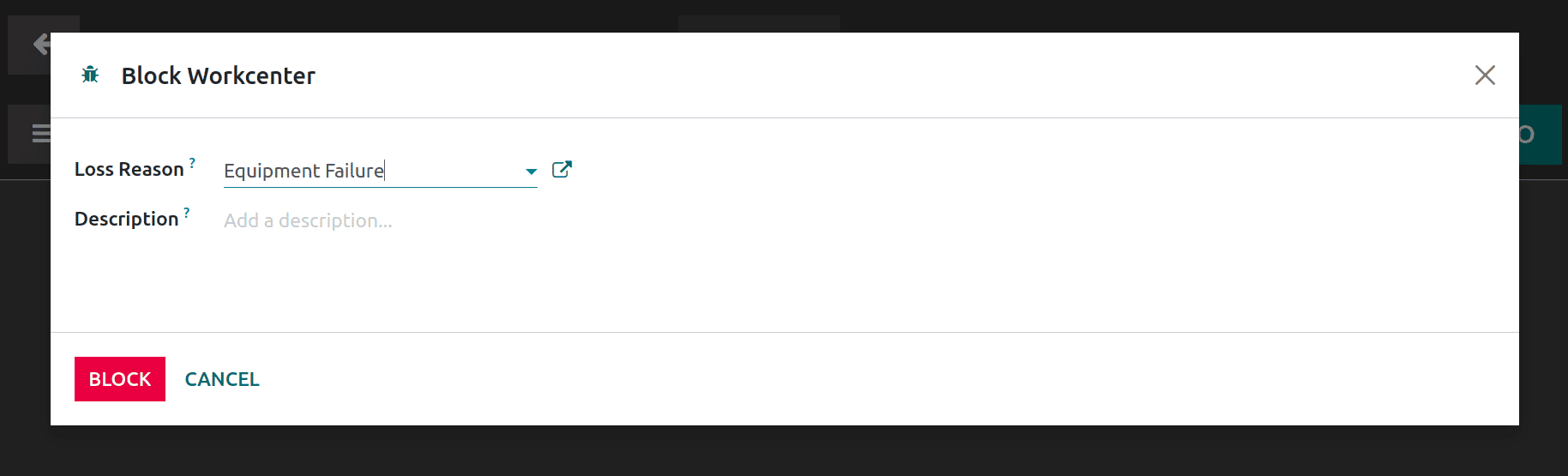
Currently, the operation is in the Blocked stage. Then raise a maintenance request with the ‘MAINTENANCE REQUEST’ option. The operator can unblock it after solving the maintenance request.
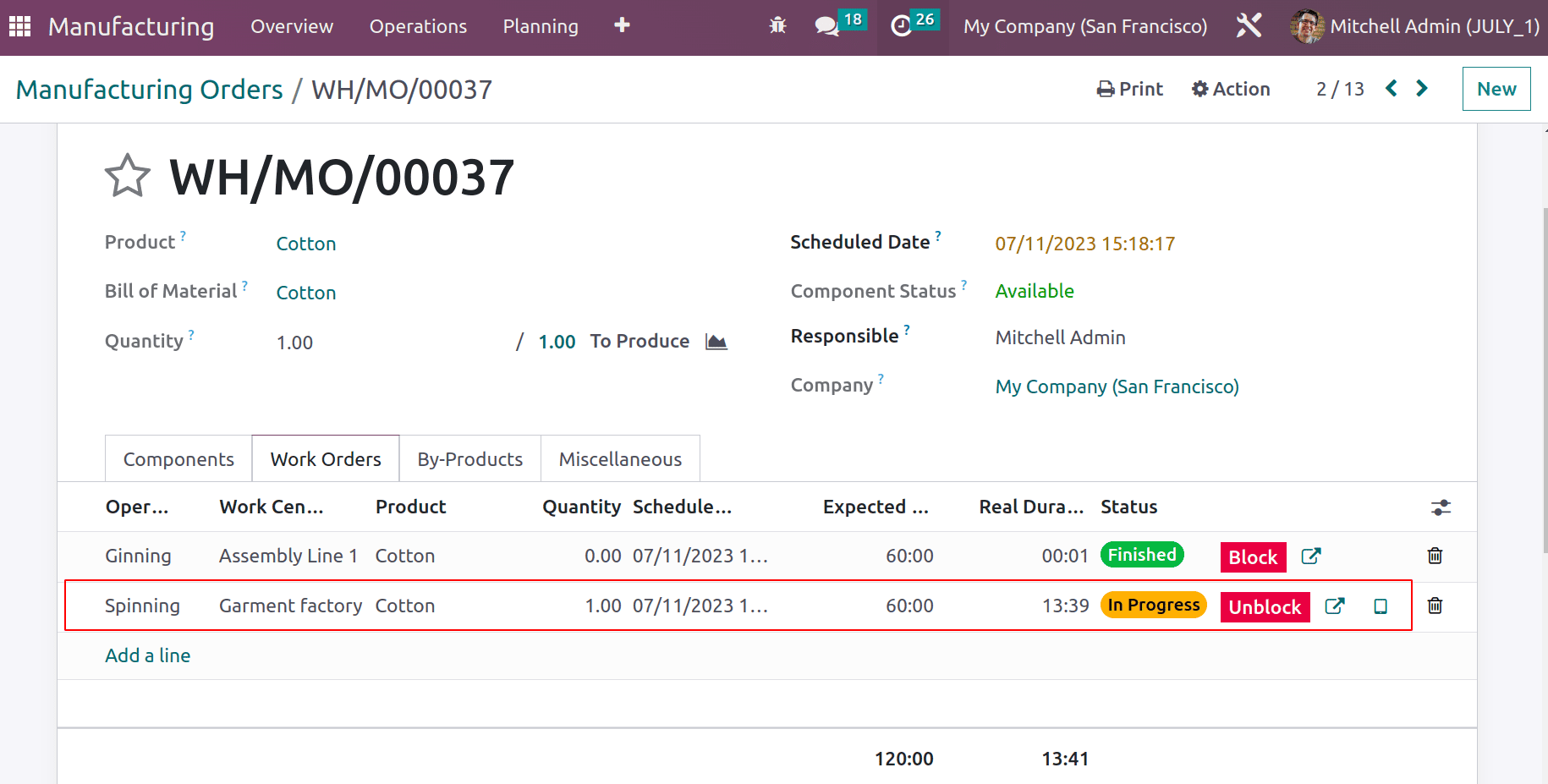
Let's check the request inside the maintenance module. Go to the maintenance module and from the Maintenance tab, choose maintenance request.
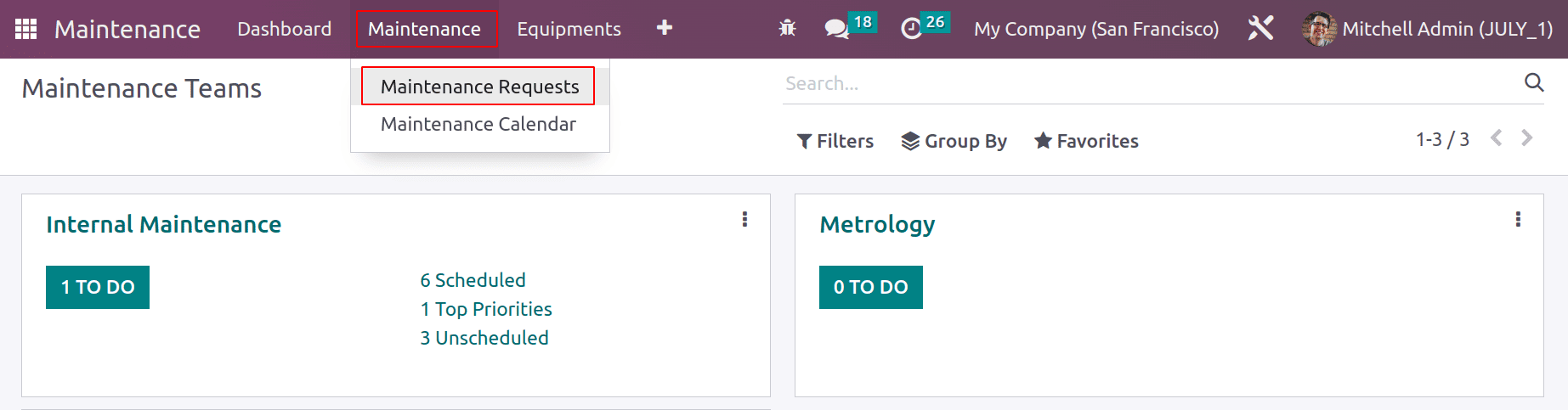
The created request is shown there in the New stage. Open the request and solve the issue.
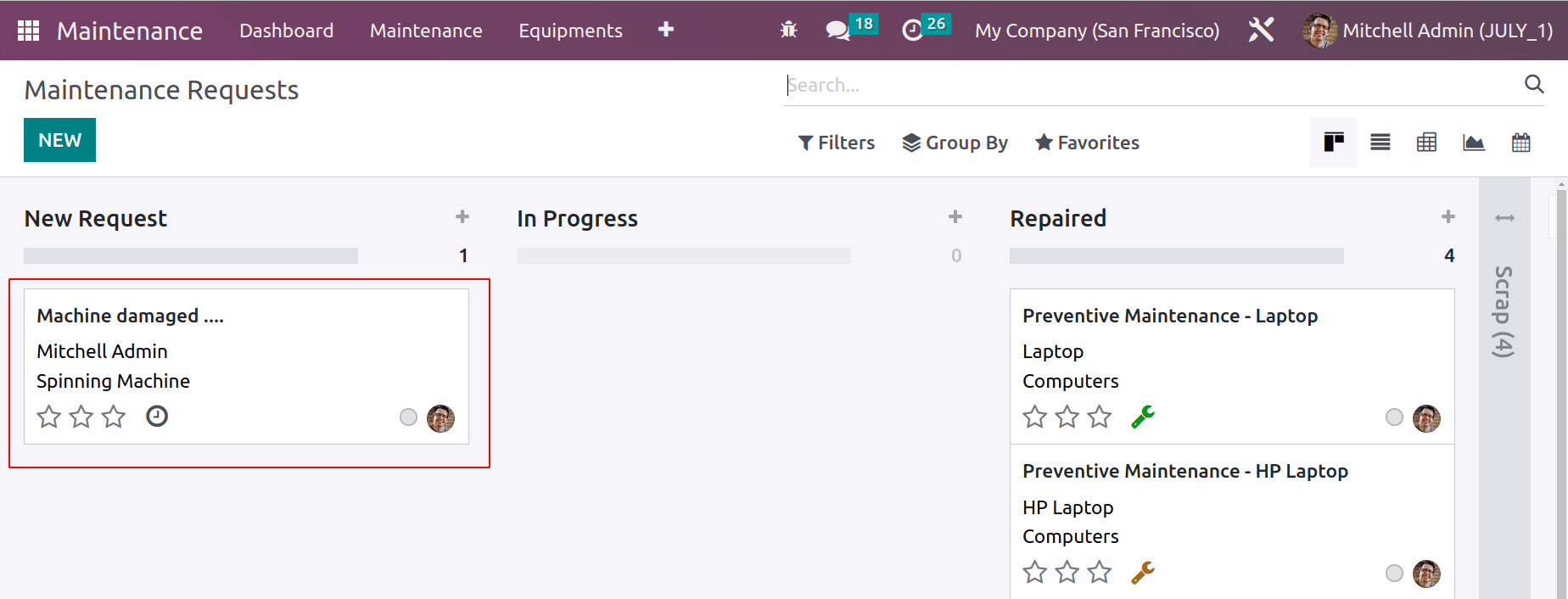
Then, change the request stage from the New Request stage to Repaired.
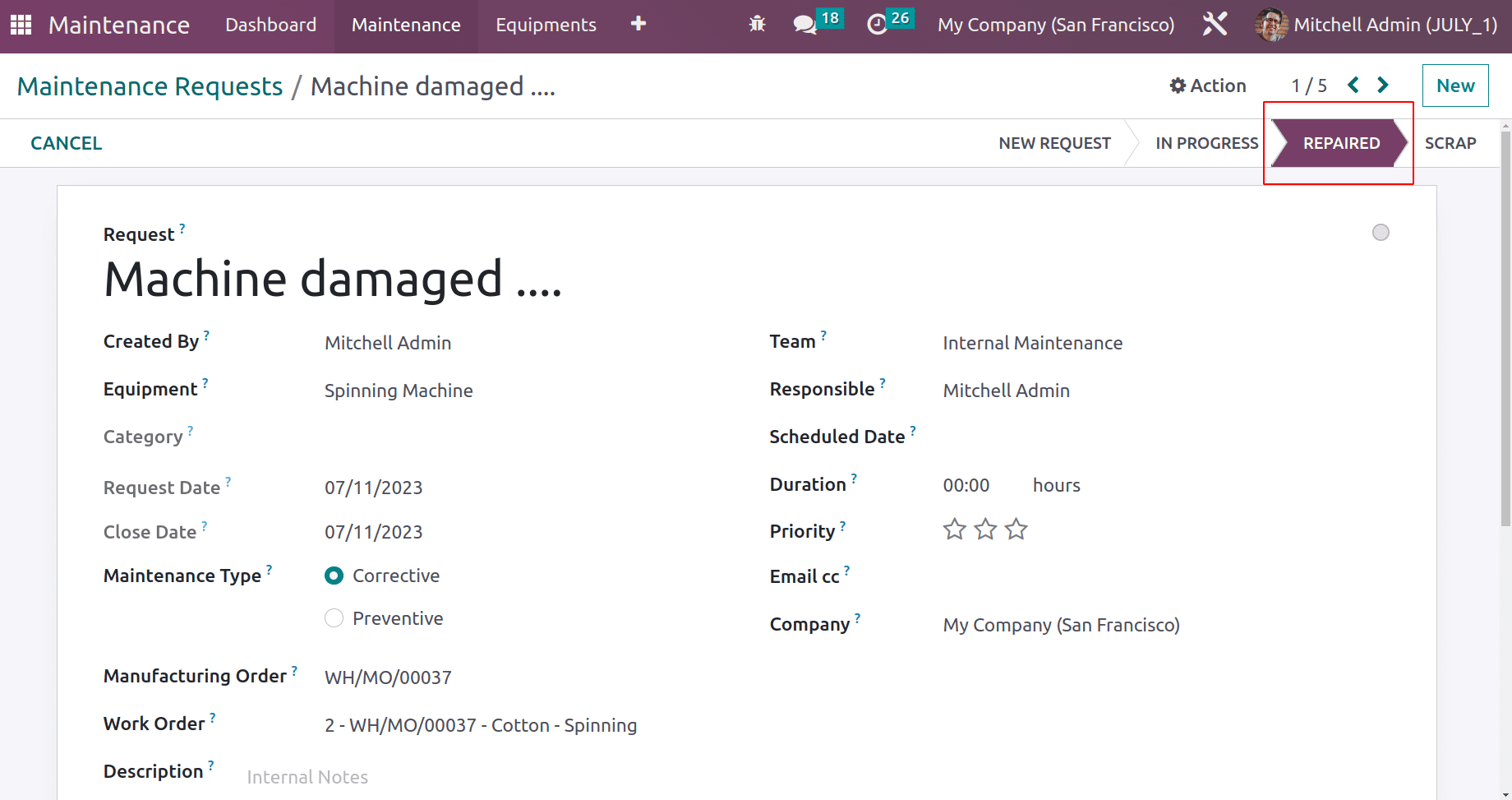
Then go back to manufacturing order and click on the Unblock button to continue the operation.
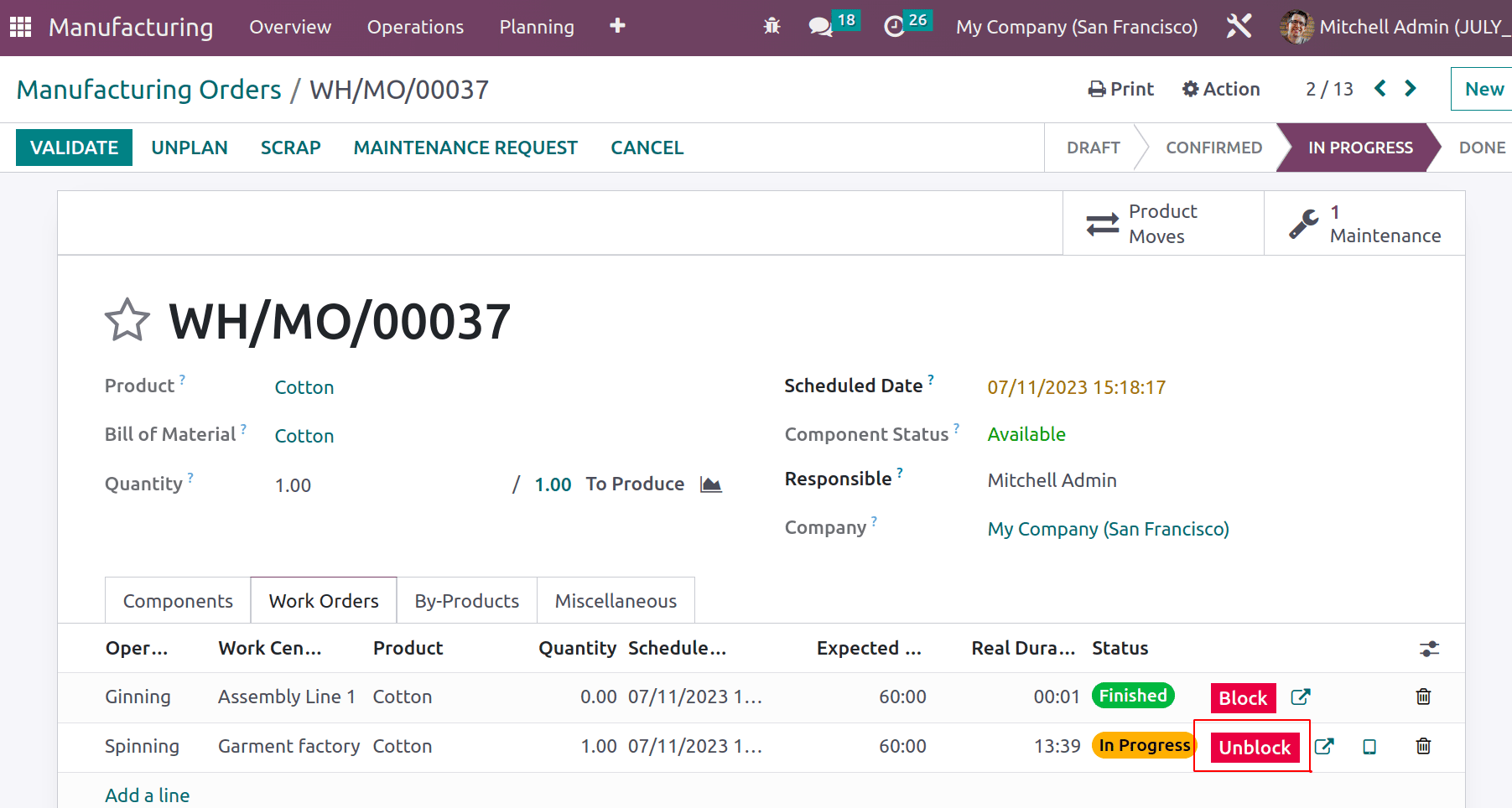
After completing both operations, click the Mark as Done button.
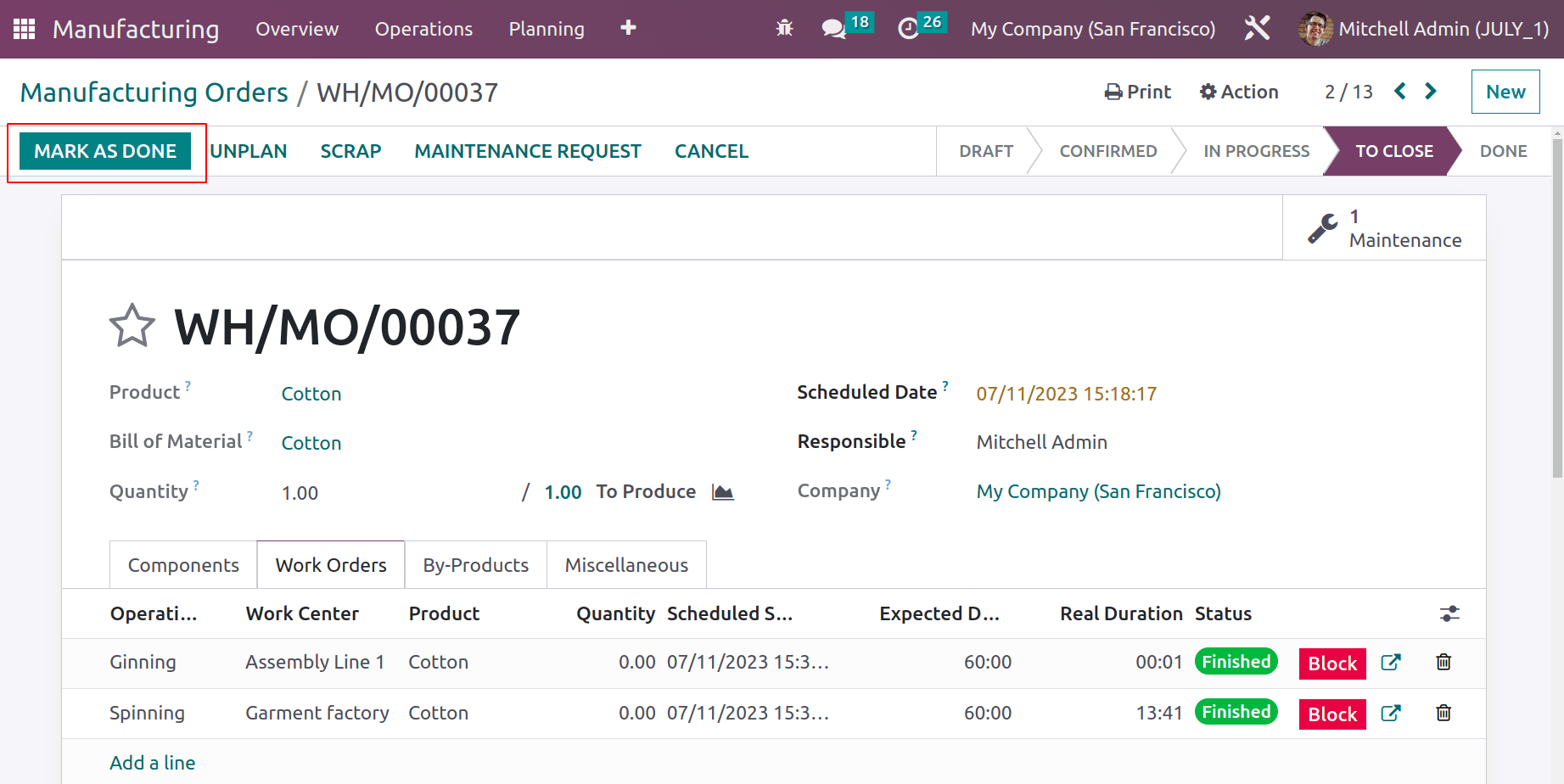
Completing the manufacturing order, a smart tab named Maintenance was added there. While open, the maintenance request created can be viewed there.
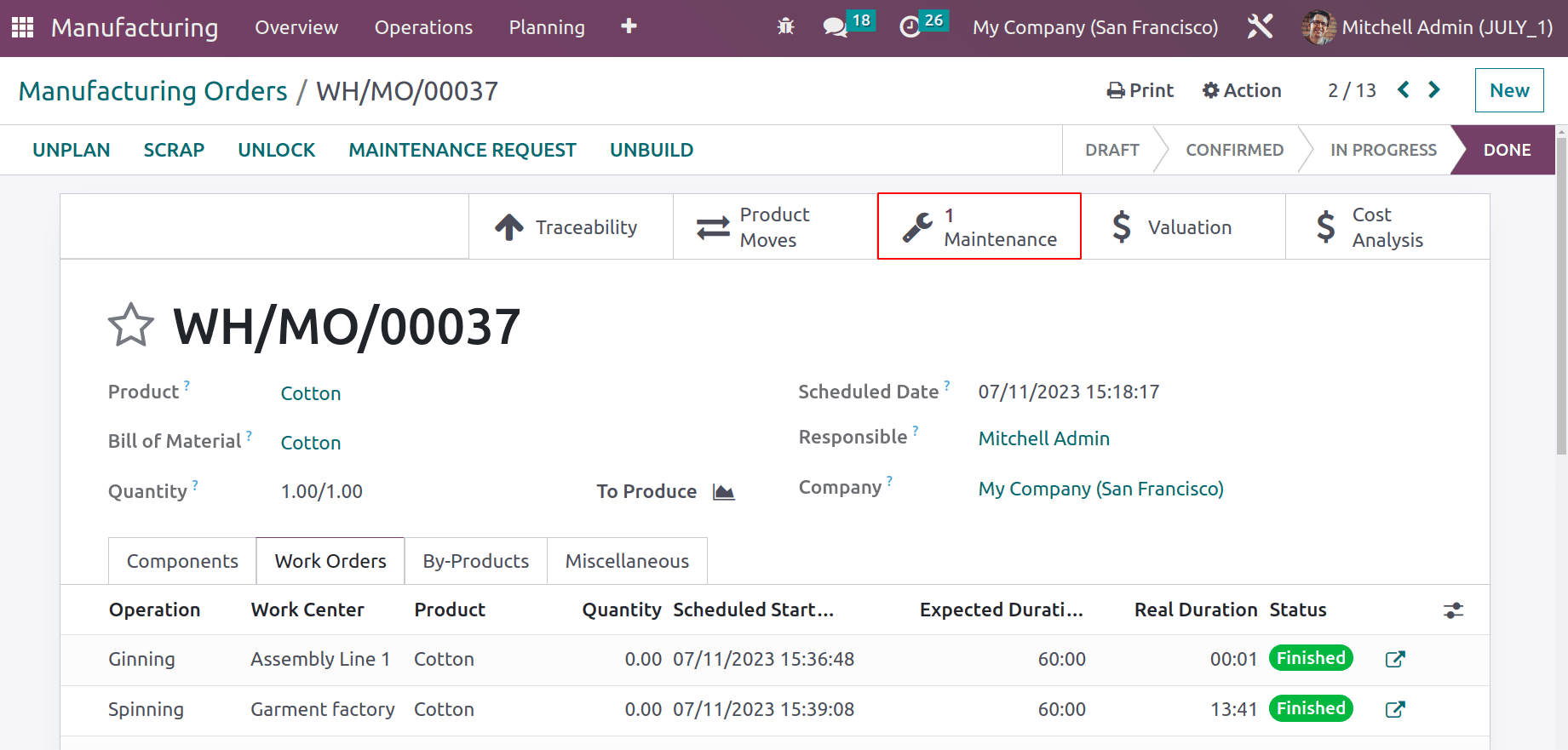
In conclusion, implementing the manufacturing module's maintenance request feature will help to speed up production and enhance the equipment's overall efficiency. To read more about How to Manage Equipment Maintenance During Production in Odoo 17 refer to our latest blog.