We can state that both lots and serial numbers are employed to keep track of items from the manufacturing stage to the point of sale. Numerous businesses assign product numbers throughout the production process; occasionally, they are even added as the product is packaged. But lots and serial numbers are utilized for simple product identification and tracking. However, there are variations in the lots and serial numbers. Serial numbers are the unique numbers allocated to a single product, unlike lots, which are a set of numbers or codes given to a group of items with a common nature.
There are many benefits to using the lot and serial numbers in Odoo 16. The lot and serial number tracking allow you to track the movement of products throughout your supply chain. This can be helpful for identifying the source of a product if there is a recall or quality issue. The products are removed from bulk storage as they reach their expiration date as a result of Odoo's traceability function. Managing the inventory and producing the items become significantly more challenging as a firm grows. Thus, Odoo 16 makes it easy to carry out your tasks and rapidly complete them.
You can access the lot and serial number throughout the sales, purchase, and inventory modules of Odoo 16.
The configuration of serial numbers, lots, and product traceability using the Inventory module in Odoo 16 is covered in detail in this blog.
From the configuration settings of the inventory module, you can enable the traceability features to set up the lot and serial number, as shown in the below image.
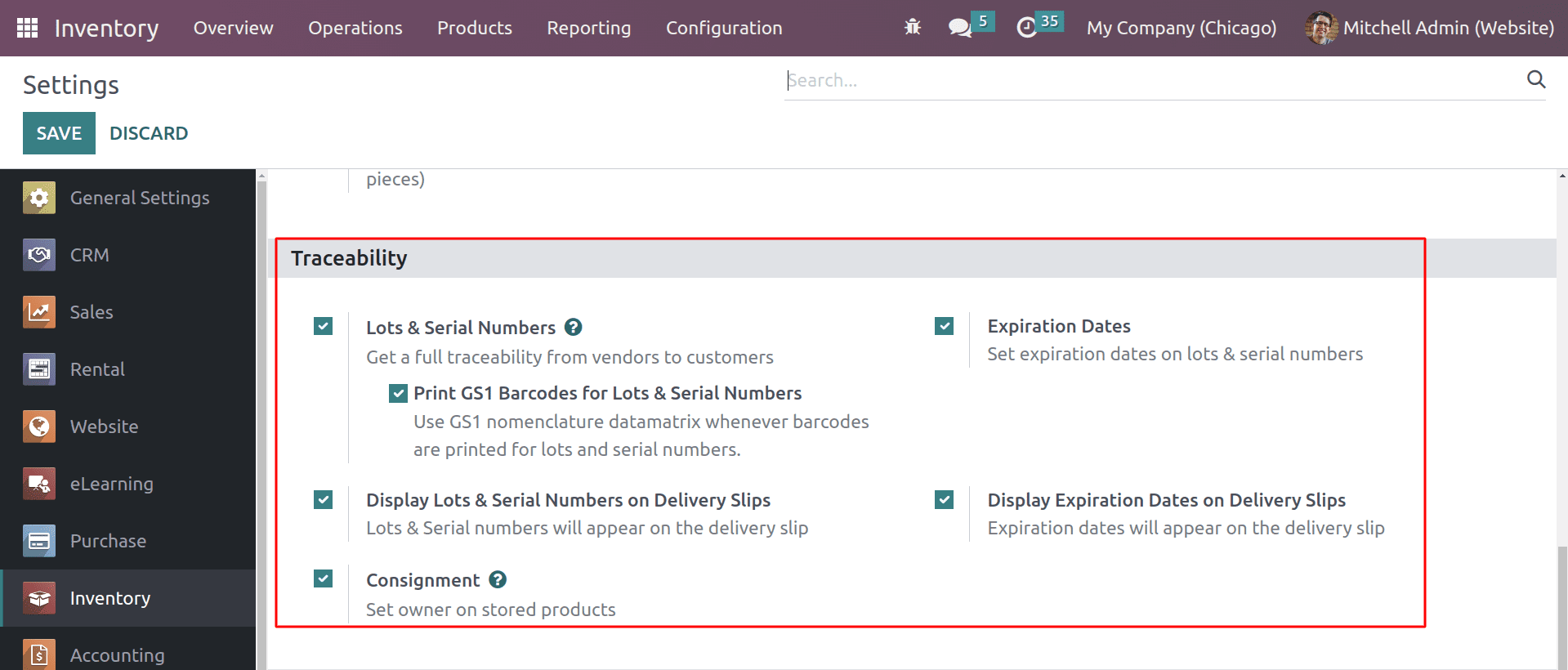
By enabling these features, you can access a product's traceability in the product form's inventory tab.
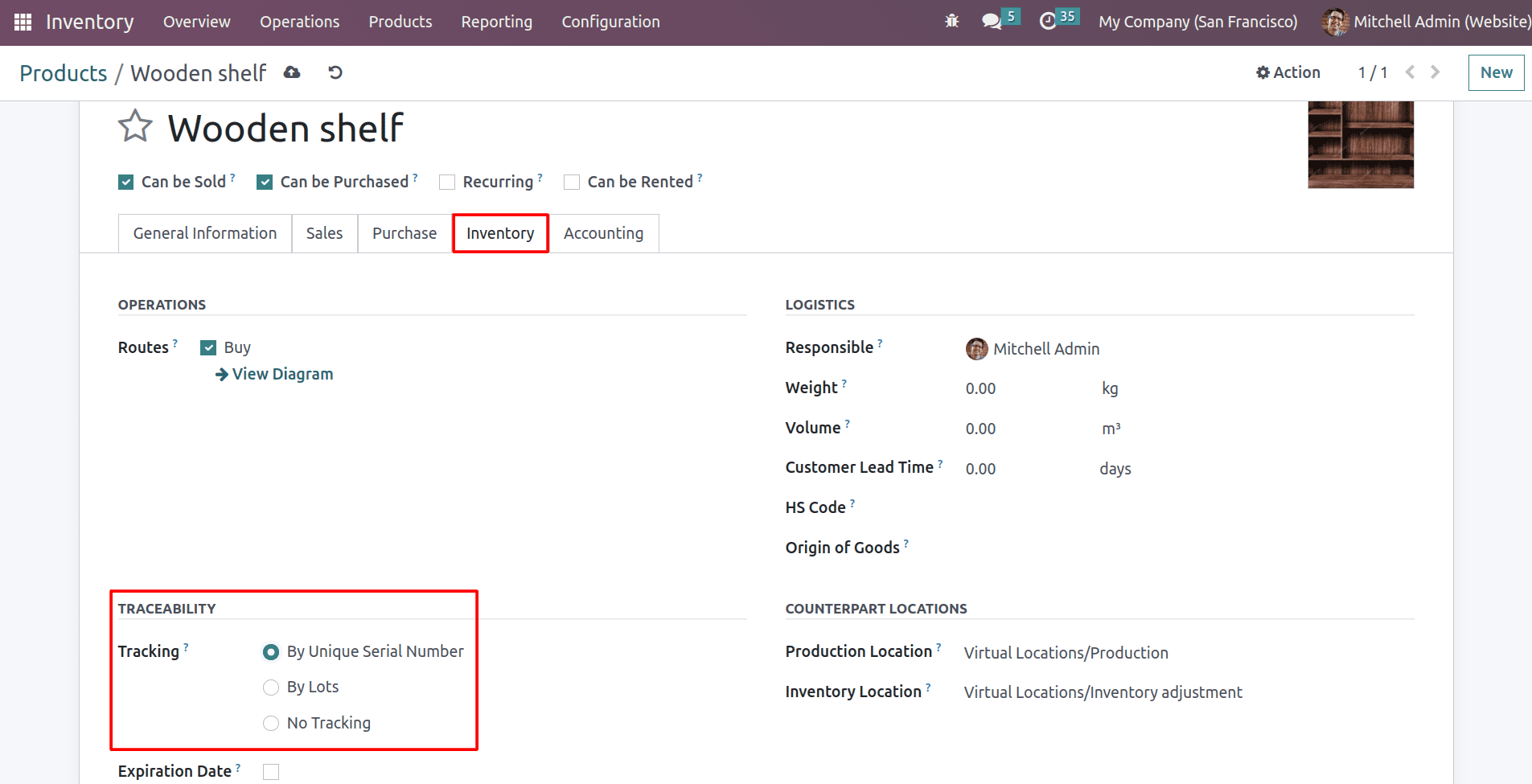
We can track our product in two different ways. By unique serial number and By lots. Both have the same functionality, although they differ in some ways. In lots, it refers to the quantity designated for particular items that are procured and stored in a single pack. And in contrast, the serial number is the unique identifying code or number required for each and every item in the stock.
And also, we have a traceability option in the operation types of Odoo 16. In the configuration of the inventory module, you can access the operation types.

In Odoo 16, operation types are used to classify different types of inventory operations. There are different types of operations like receipt, delivery, manufacturing, and internal transfer.
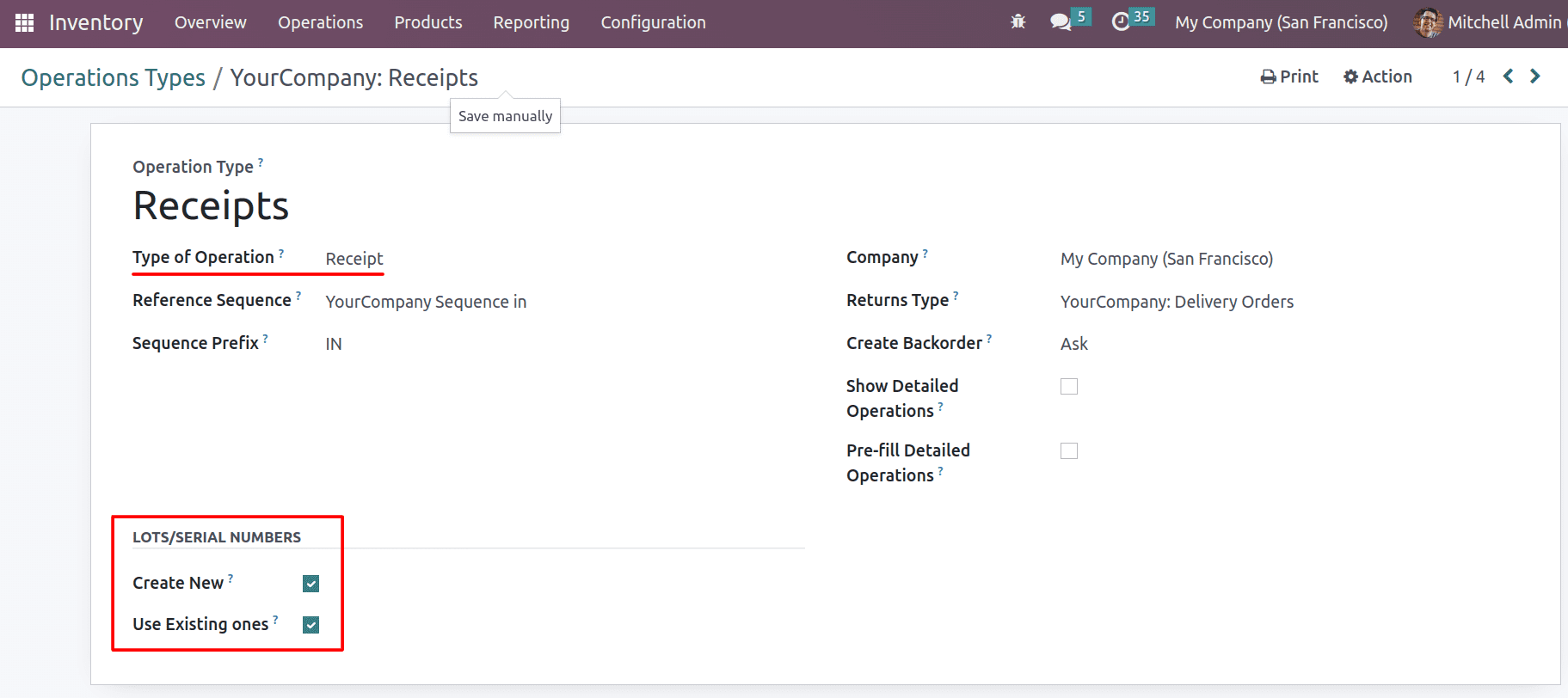
From the receipt operation types, you can see "Create new” and "Use existing” lots and serial numbers. While purchasing the product, we can either choose the existing lot and serial number or create a new one.
Tracking and traceability using unique serial numbers
Serial numbers are identifying codes assigned to a specific product to enable tracking of its history from receipt to delivery and after-sales. So next, we can purchase a product using the tracking number as a unique serial number.
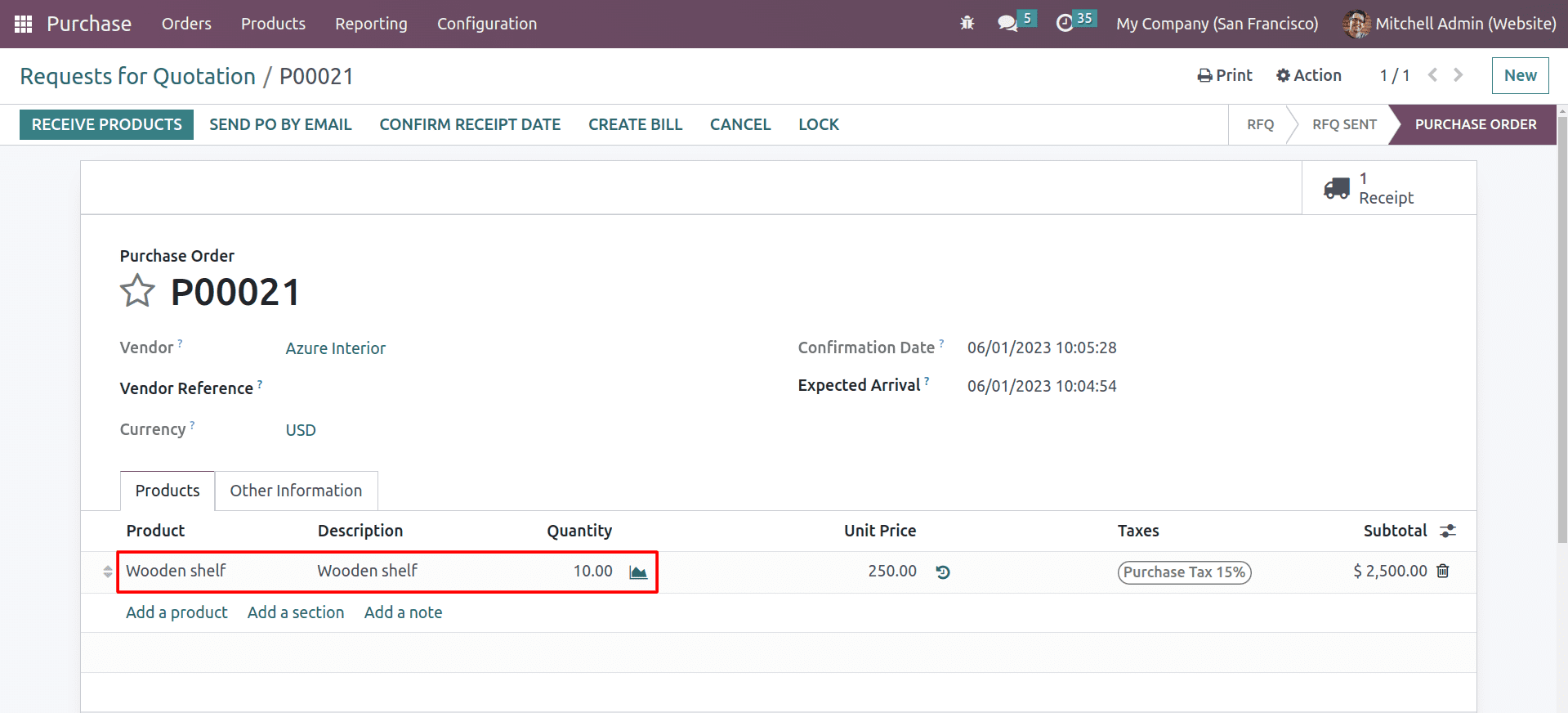
The product with tracking via a unique serial number is chosen in the above-mentioned purchase order. You can set up the serial number while receiving the product after confirming the order.
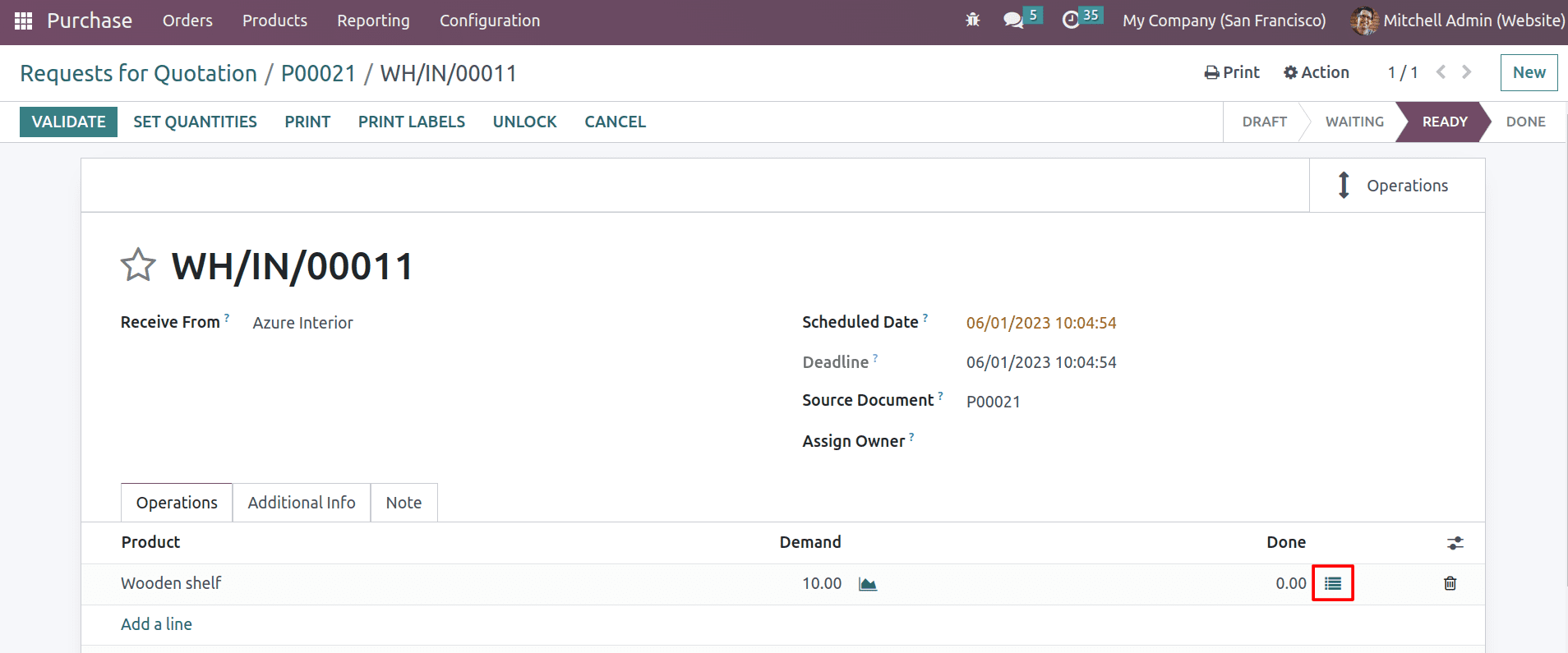
By clicking on the menu icon in the receipt form, you will be redirected to a pop-up window.
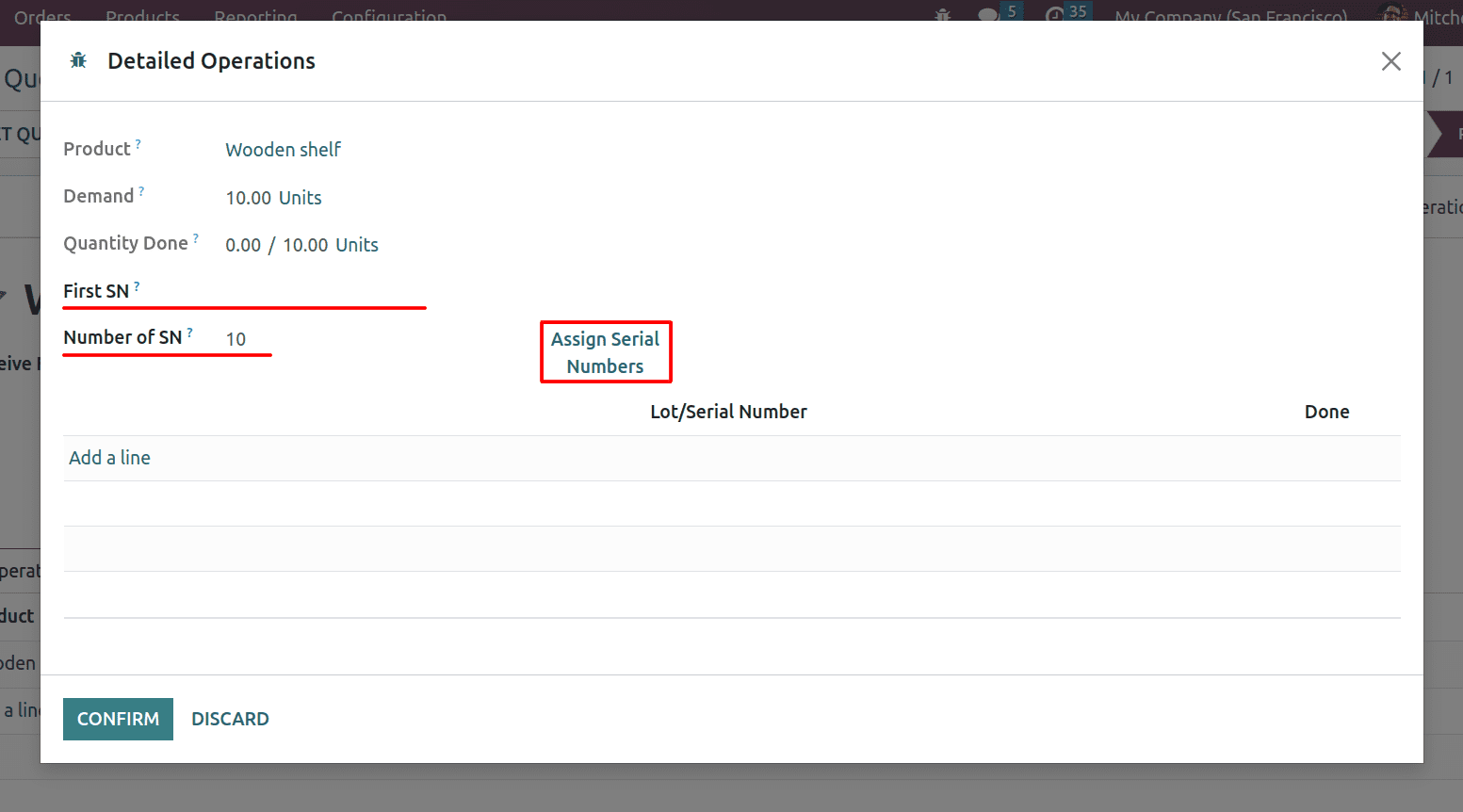
From here, you can provide the serial number. Suppose we purchase a large number of products, and assigning a serial number for each one manually will be very hectic. Odoo will automatically produce the serial number for the quantity that we are purchasing to resolve this complication. First, we need to give the first serial number (first SN) of our product and the number of serial numbers (number of SN) that we need in the corresponding fields in the above-mentioned form. After that, clicking on the Assign serial numbers button will generate the serial number for your products.
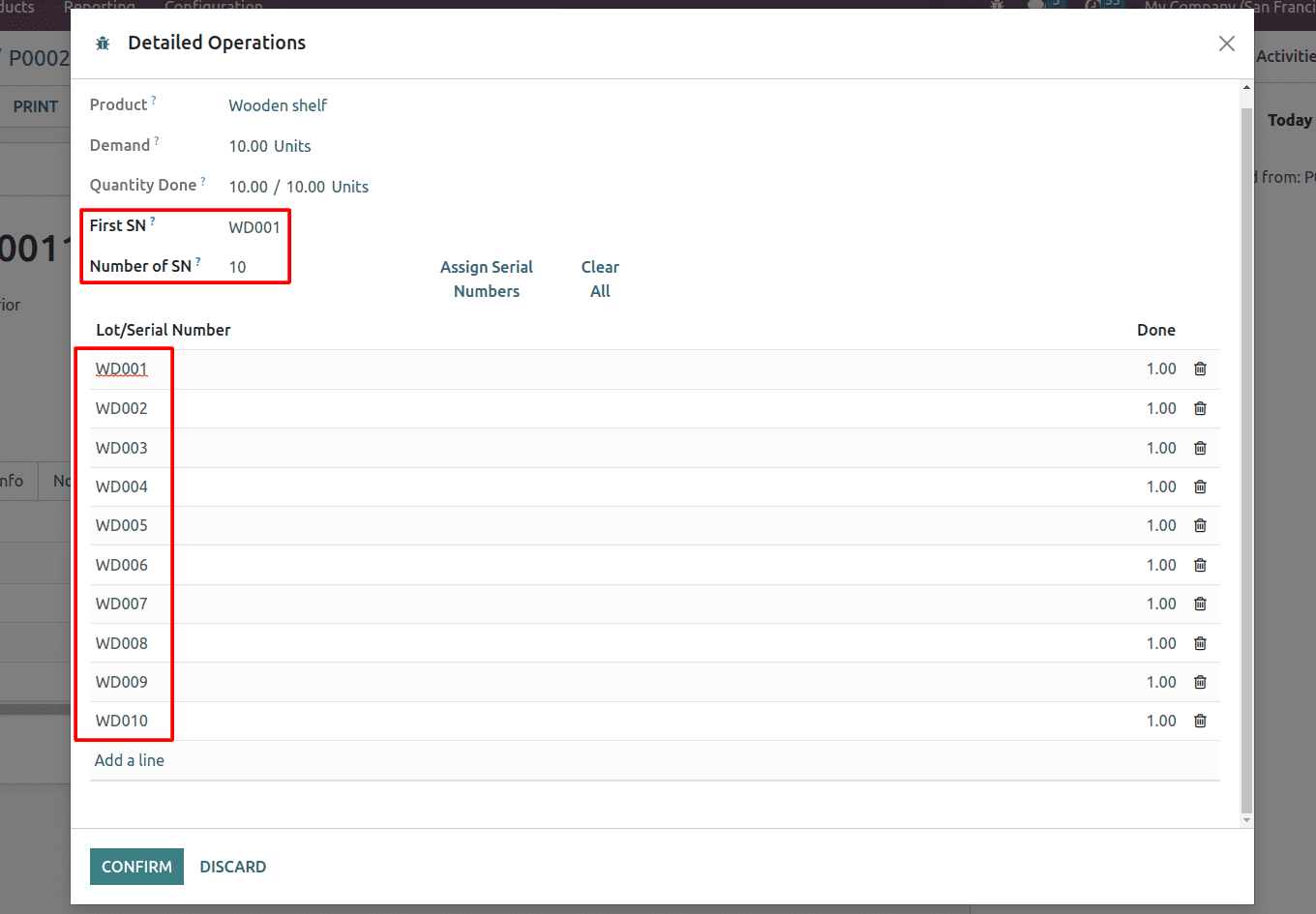
Here you can see that the serial numbers are assigned based on the given first serial number. Confirm this and validate the receipt.
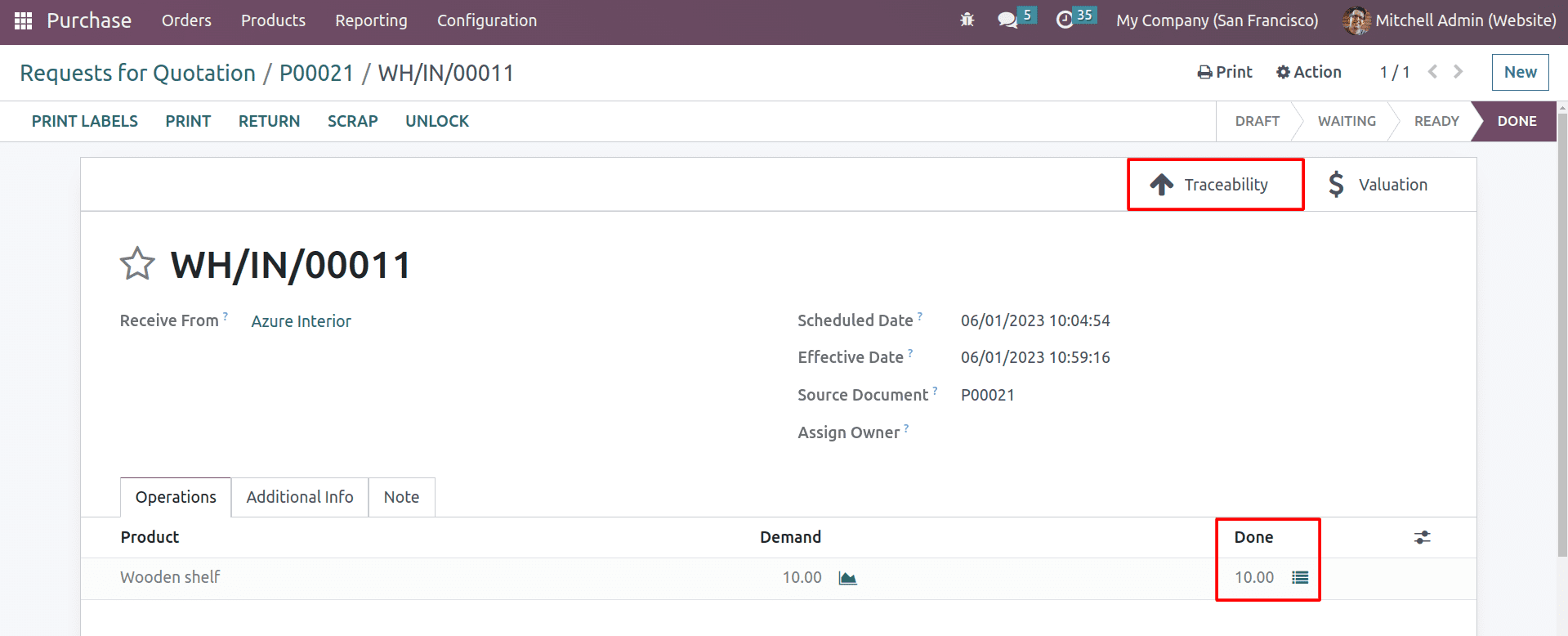
After validating the receipt, the traceability tab will appear in the receipt form.
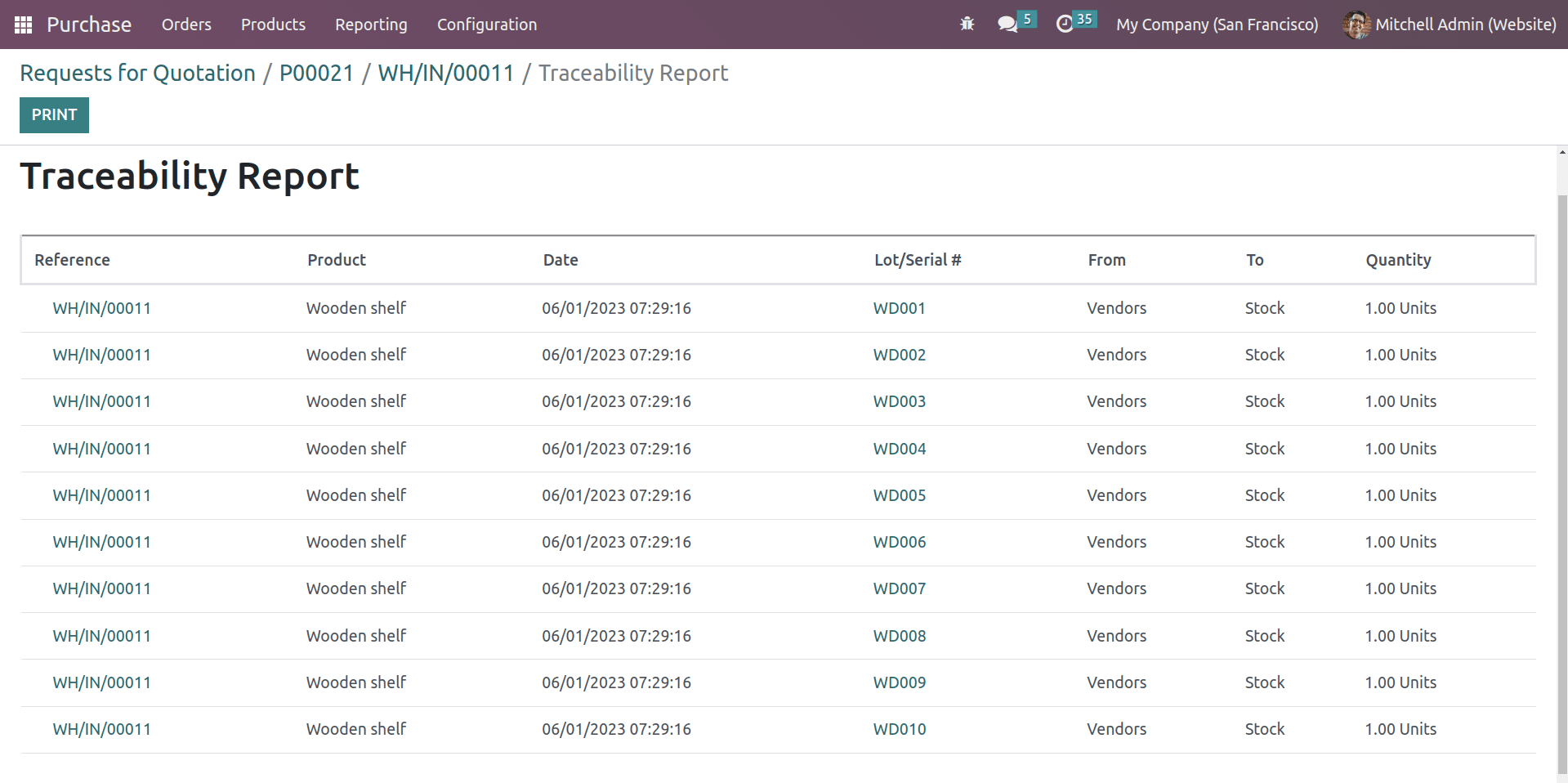
We can see the traceability report from here, with details of serial numbers and product locations.
Tracking and traceability using Lot numbers
Lot numbers in Odoo 16 are unique identifiers assigned to products. They are used to track the movement of products through the supply chain and to identify specific batches of products.
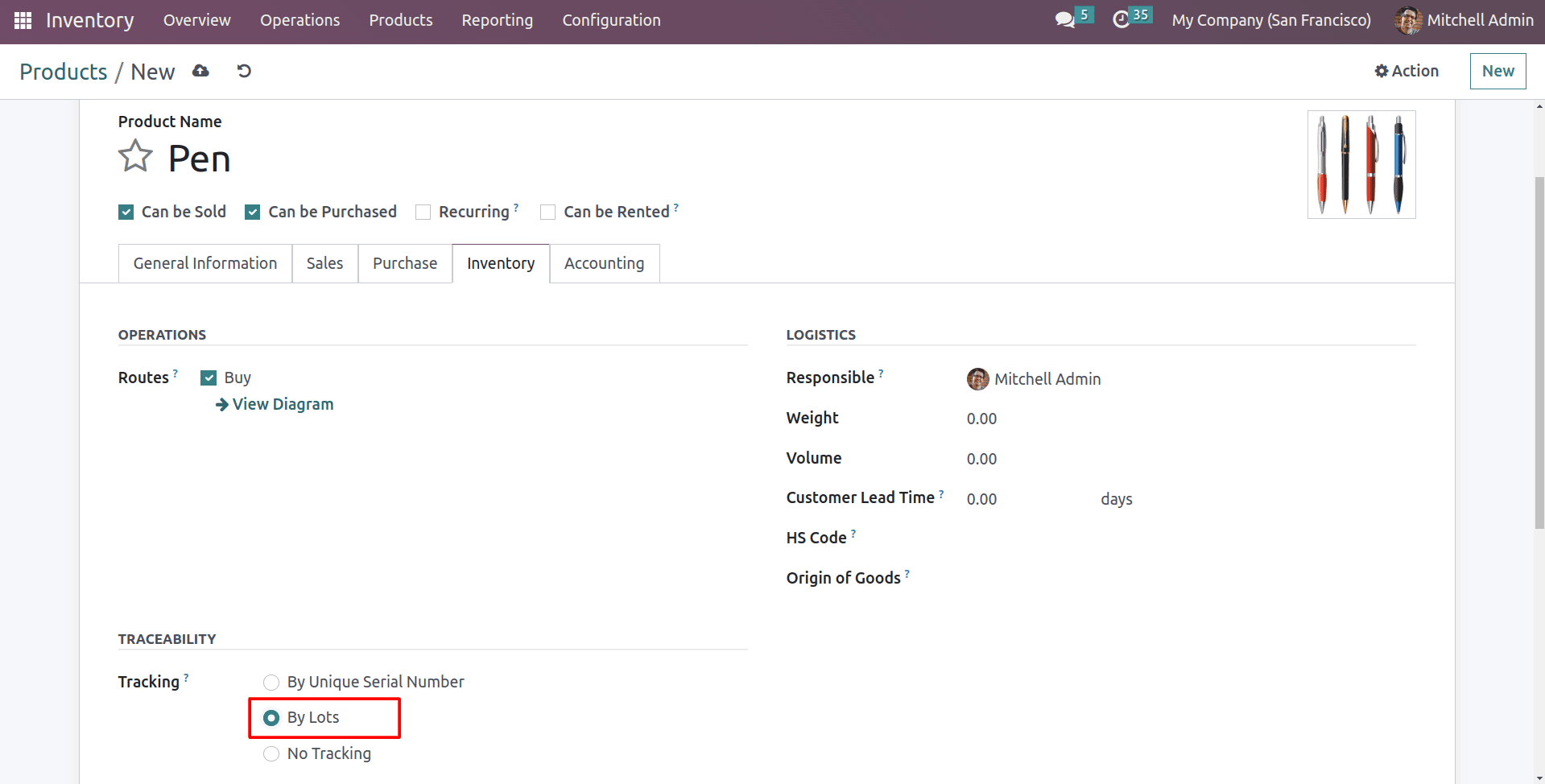
For the demonstration, we can purchase a product that tracks using the lot number. And validate the receipt.
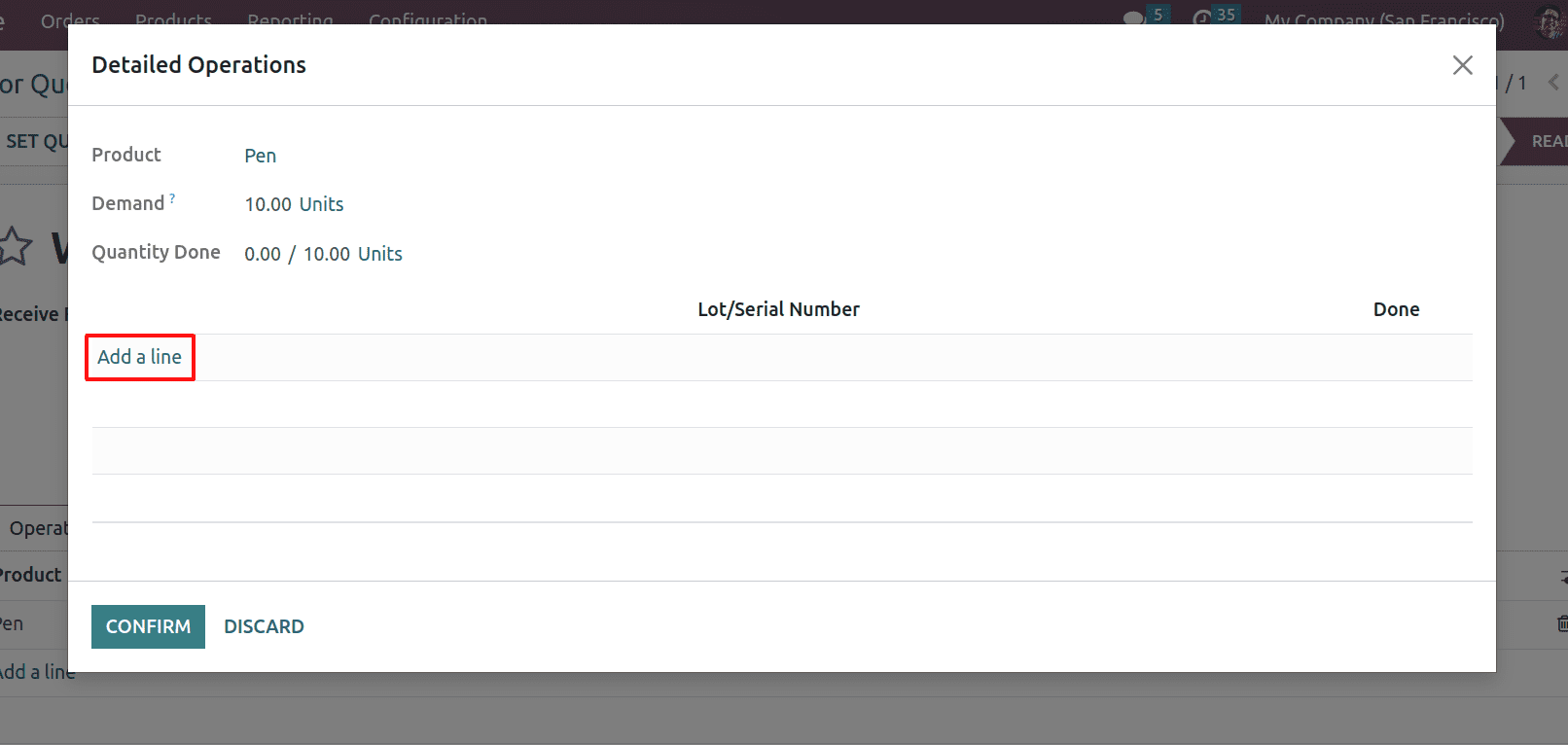
While receiving the product, you can assign the lot number as we did previously. Click on the add a line button and put the lot number that you need for this product.
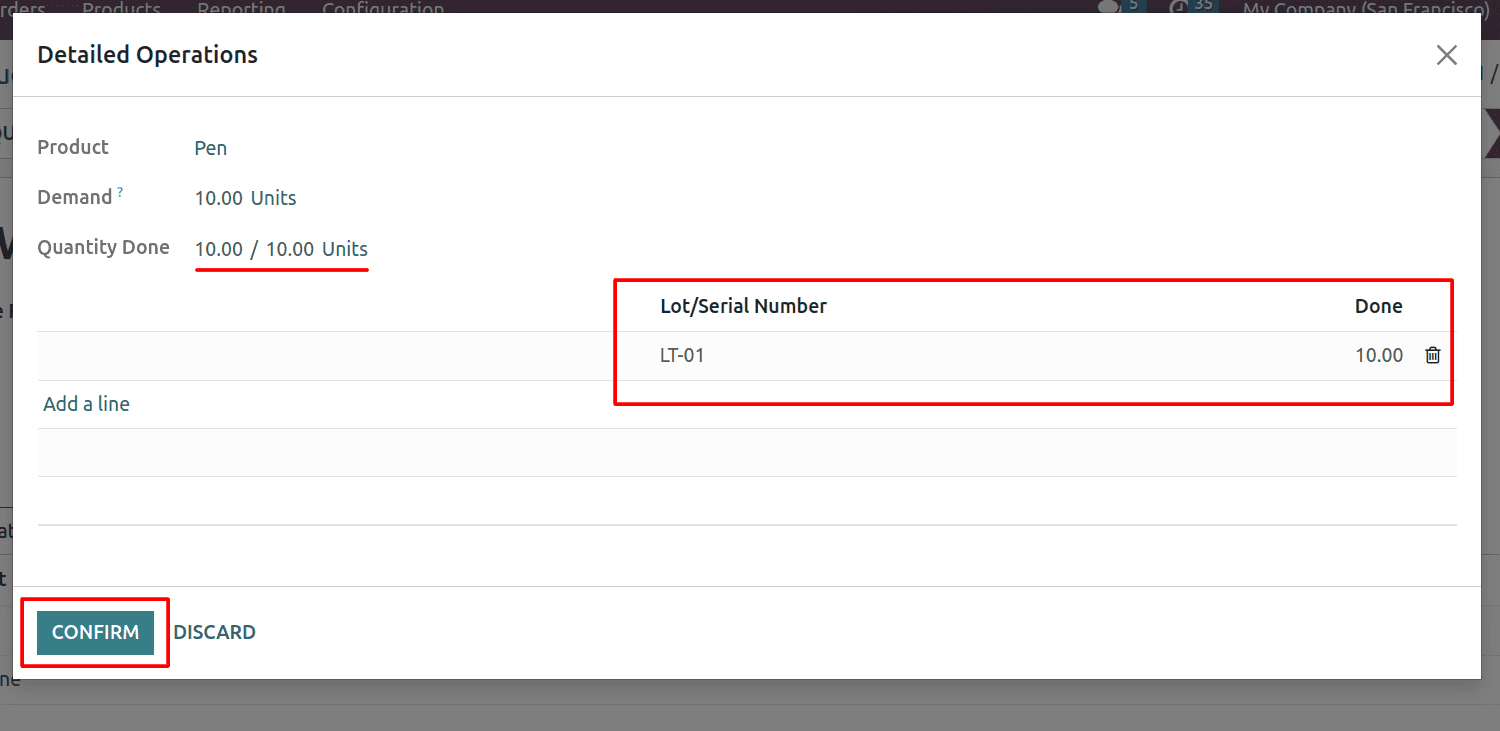
You can see that the lot number and done quantity are updated. Now these 10 quantities of pens will be identified as Lot Number LT-01. Don’t forget to click on the confirm button and validate the receipt.
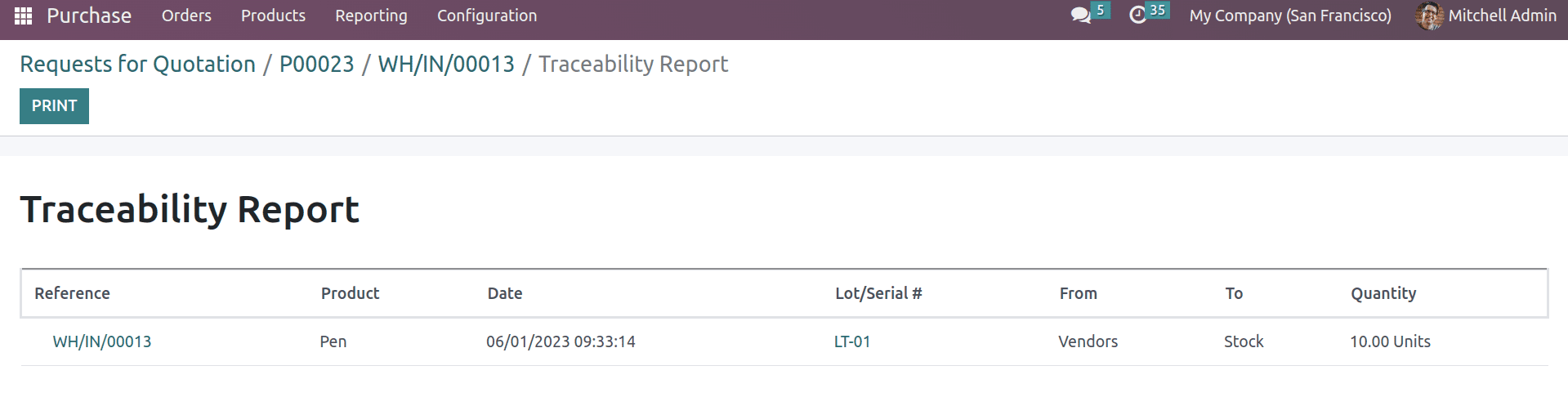
After validating the receipt, you can see the traceability report.
And as we discussed in the operation types, we can choose the existing lot/serial numbers. Make sure that the field Use existing one is enabled in the operation type. This defines you will be only able to use existing lot/serial numbers and not able to create new lots/serial numbers.
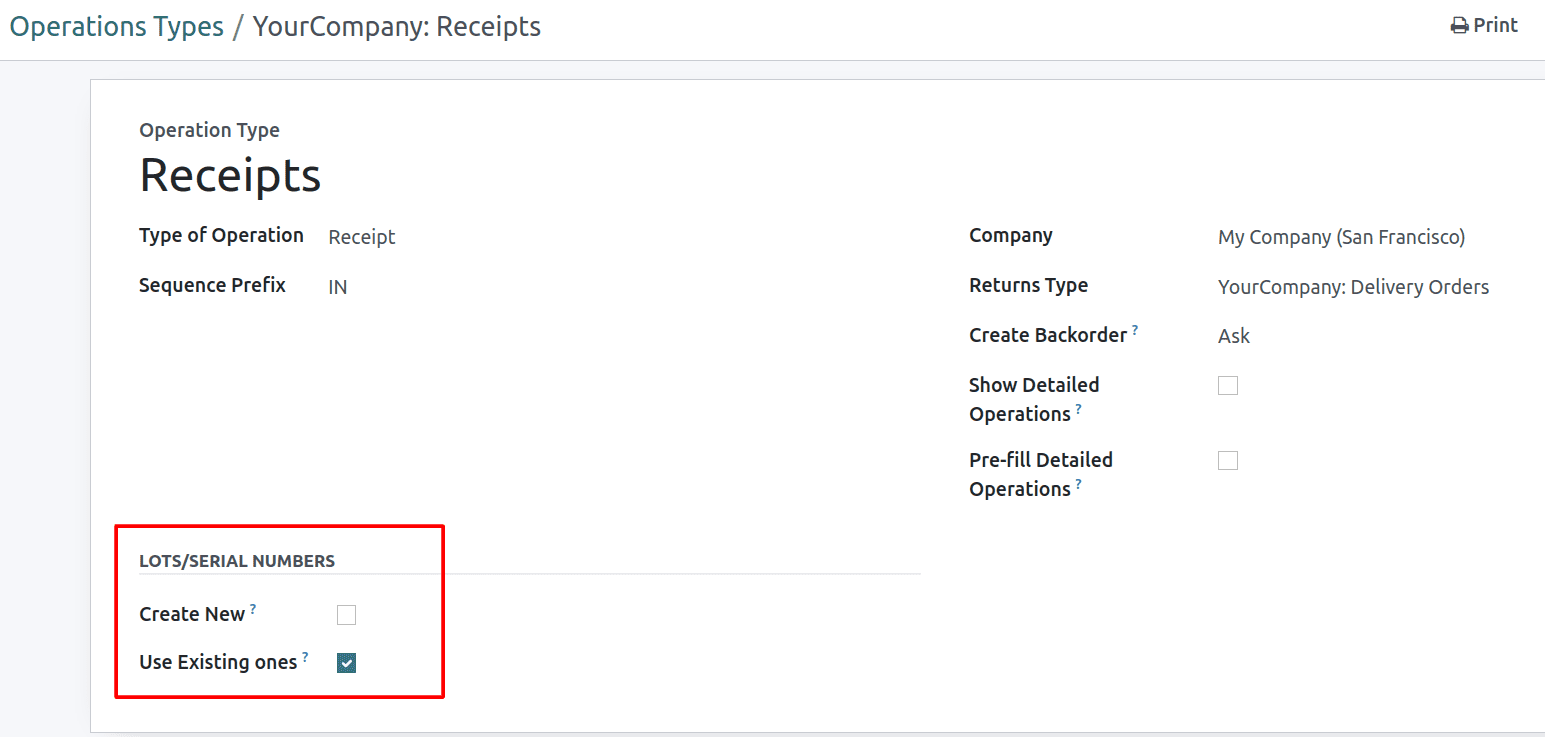
Now you can access the Lot/Serial menu from the product tab of the inventory module.
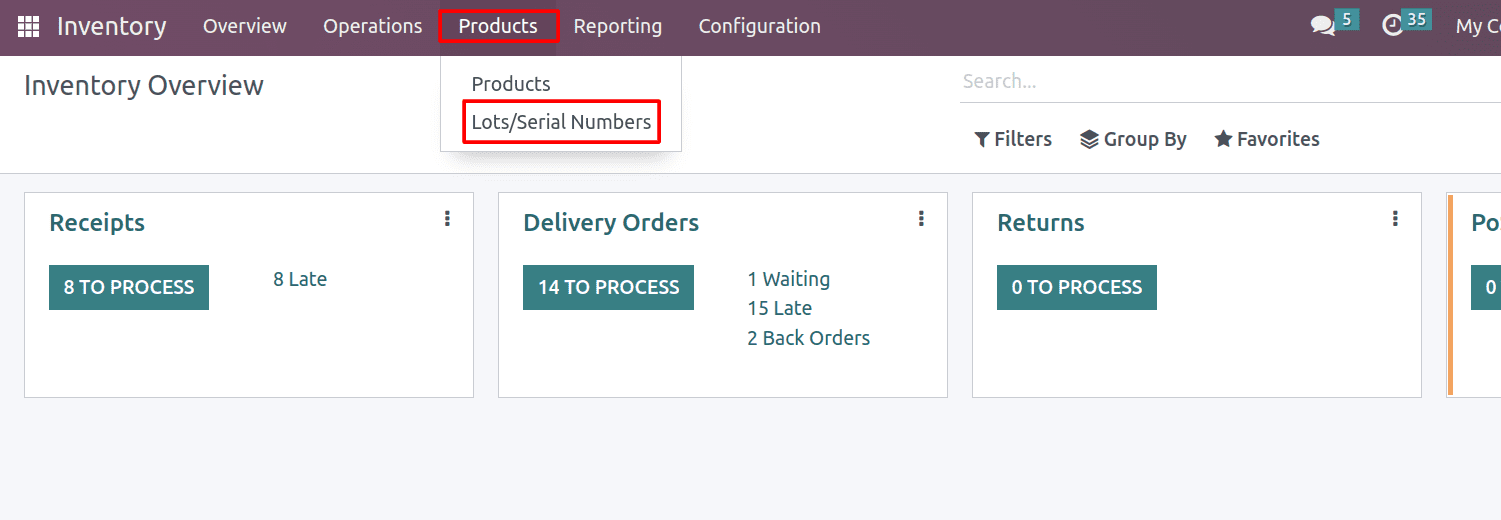
From here, you can create a new Lot/Serial number, and you can use this tracking number while purchasing the product.
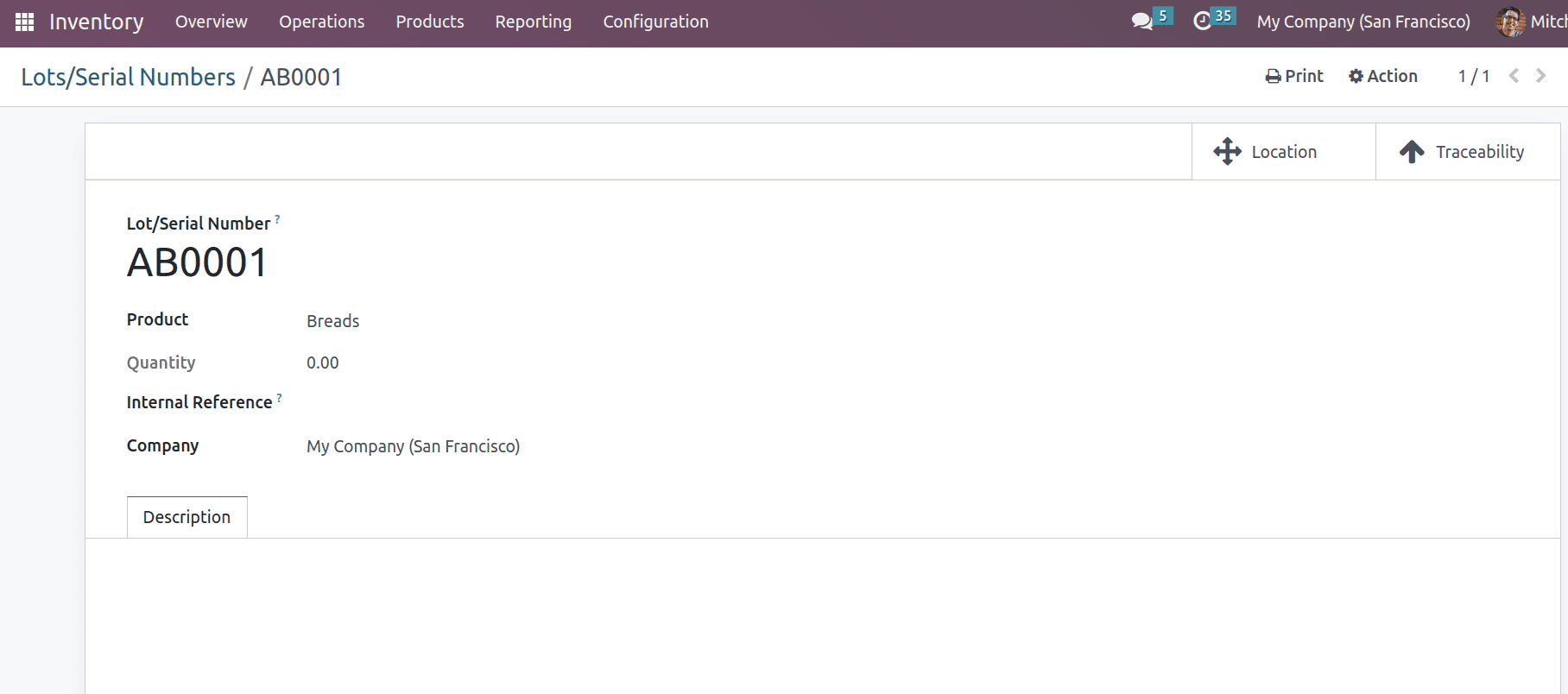
On the above-mentioned form, you can provide the Lot/Serial number and choose the product that uses this lot/serial number. And the quantity will automatically update when a product uses this lot number. Internal reference in case it differs from the manufacturer's lot/serial number.
Now we can create a purchase order and assign the lot/serial number while validating the receipt for the product Breads.
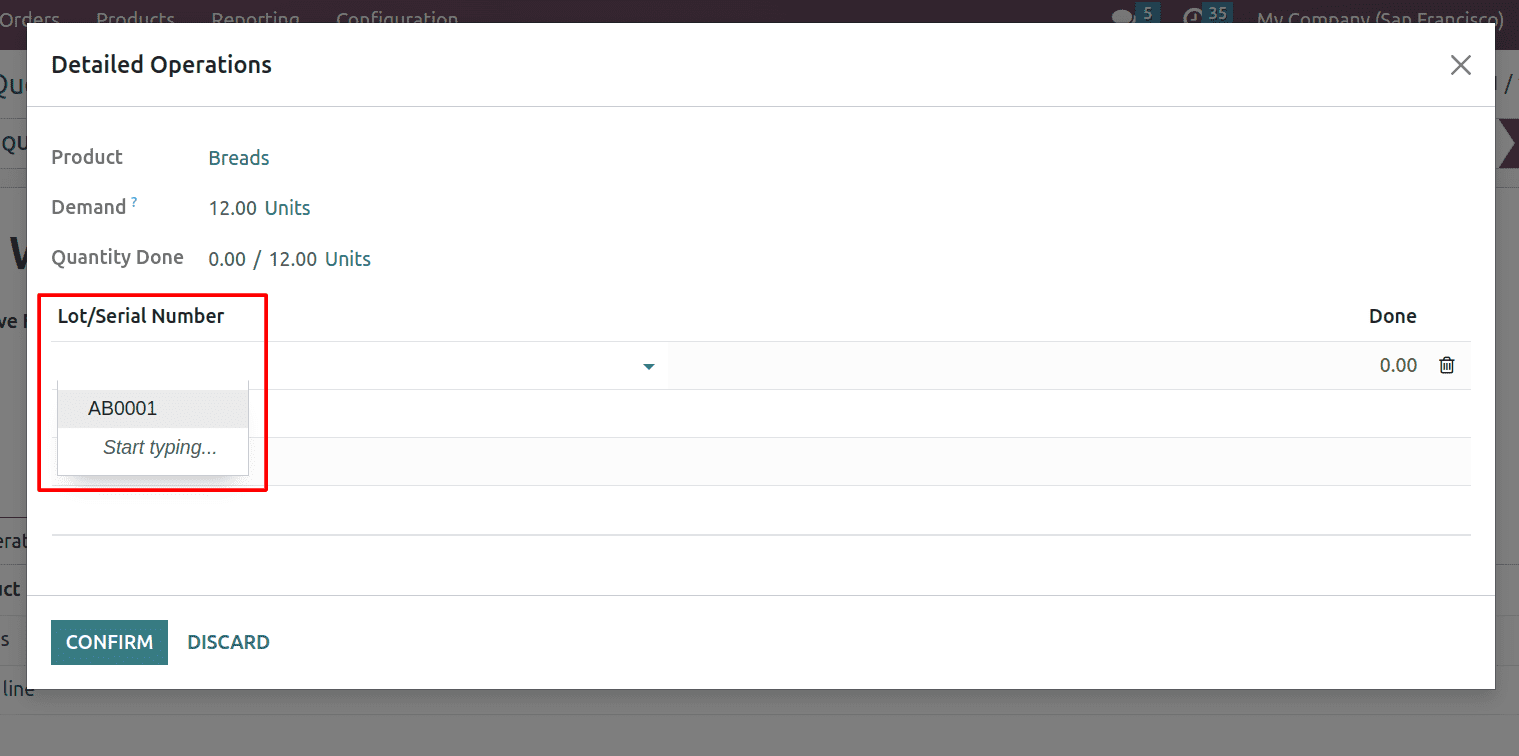
Here, you can see that the existing lot number is used while purchasing the product.
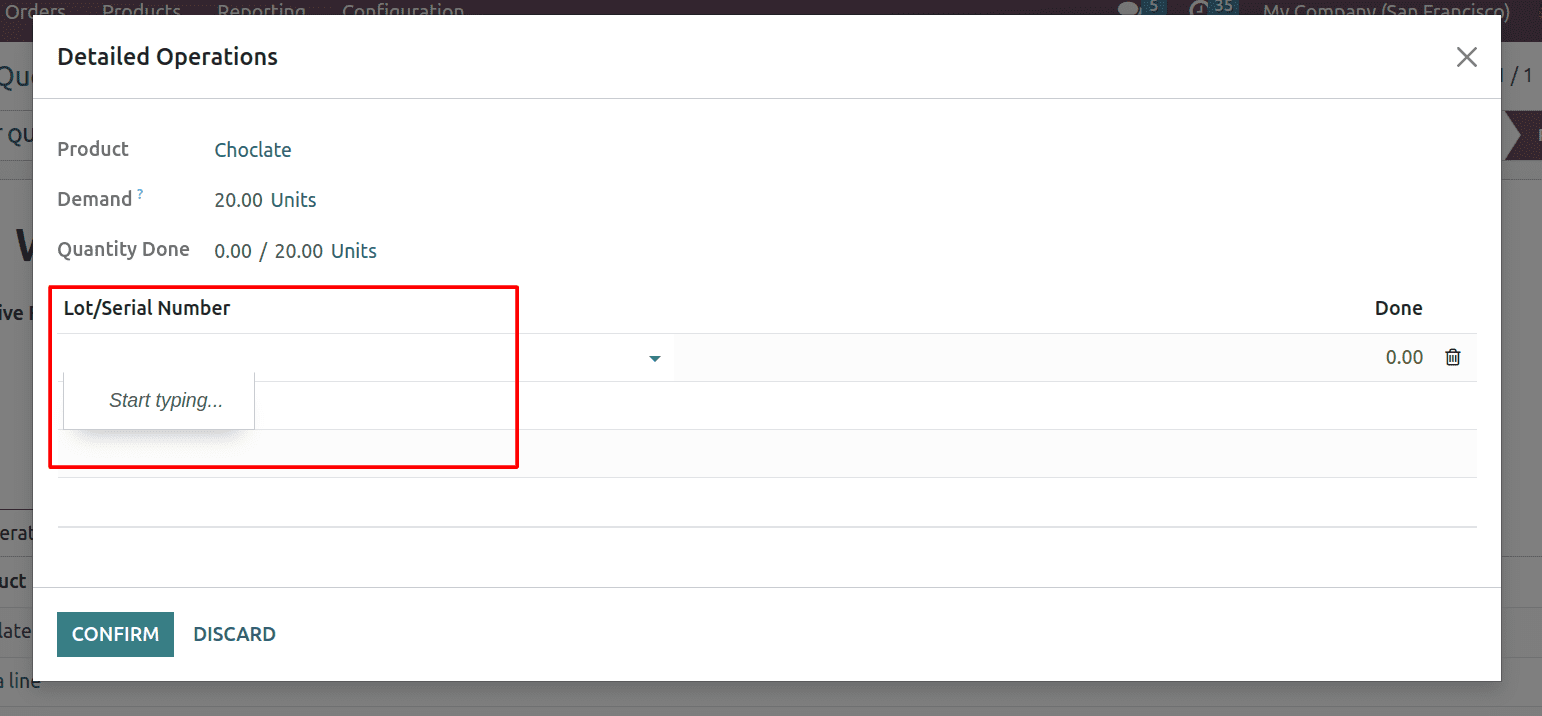
And if you try to create the lot/serial number, an error message will show that you are not allowed to create a new lot/serial number.
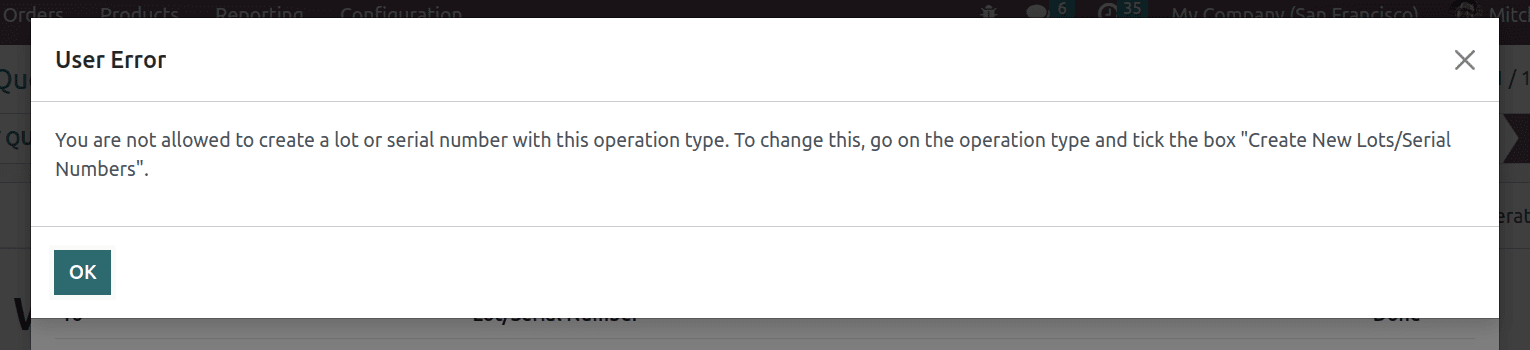
If you try to add a new Lot/Serial number to this receipt, an error will appear, as shown in the above image. Because the create new option is disabled in the operation type form.
Displaying lot/serial number on the delivery slip and invoice
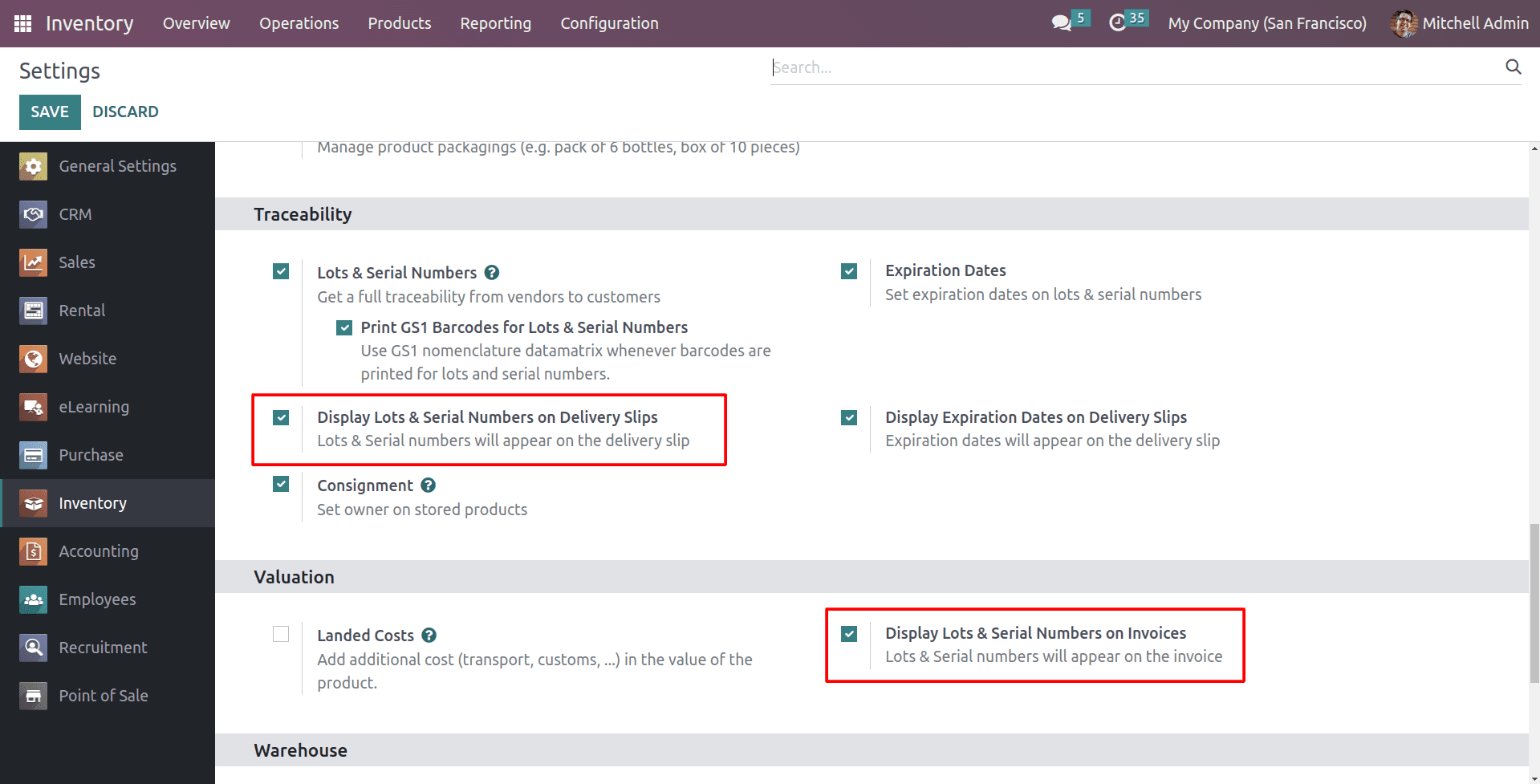
Once you have enabled this setting, lot/serial numbers will be displayed on the delivery slip and invoice for all products that have been assigned a lot/serial number. So the customer can easily identify the traceability of a product.
Create a sale order for the product for which you enabled the tracking method and validate the delivery of the product.
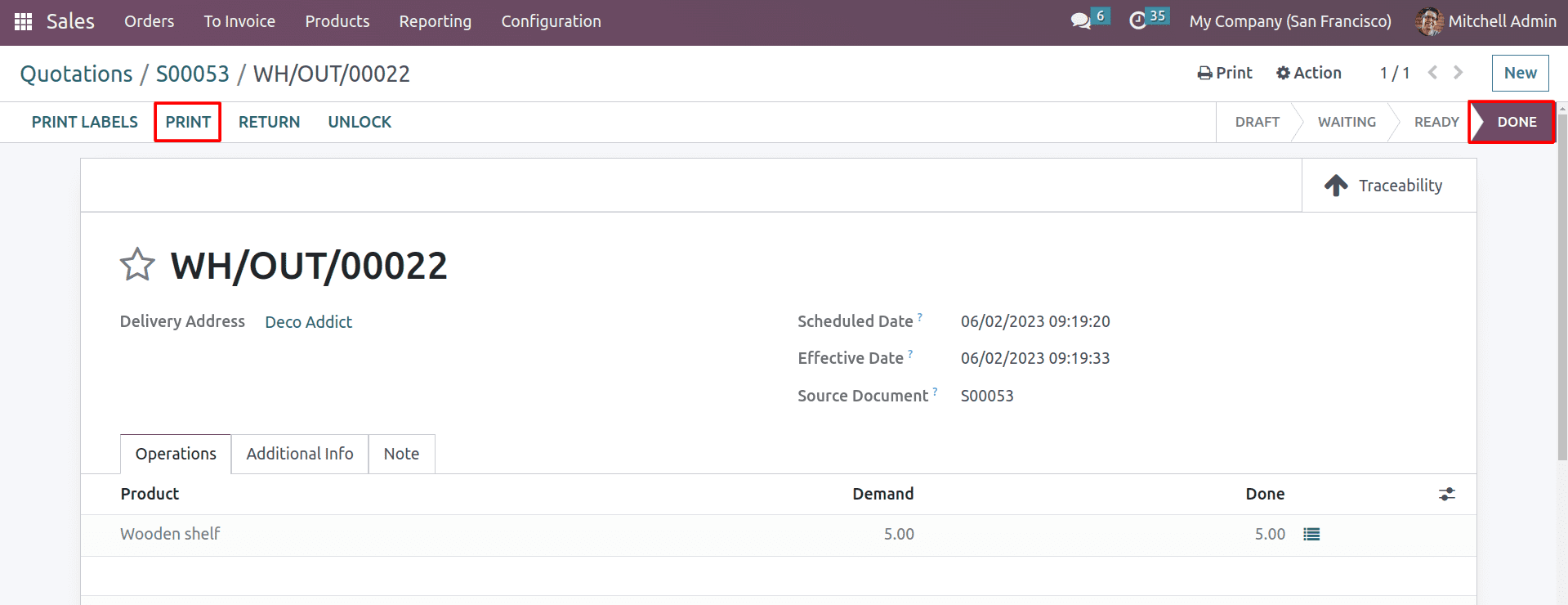
You can see that the print button has been generated when the delivery is complete. By clicking on the print button, you can generate the delivery slip.
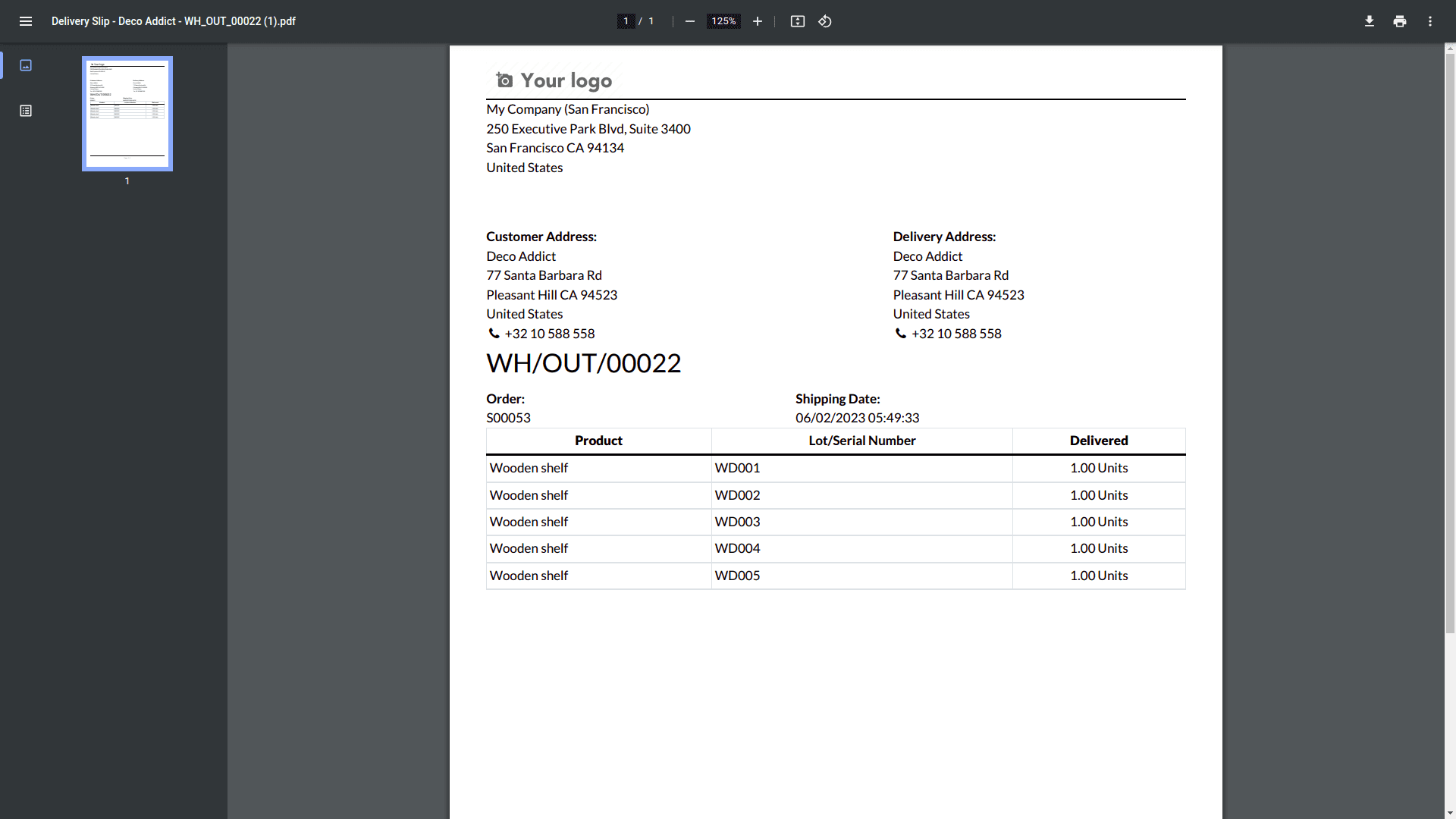
In the above-mentioned delivery slip, you can see the Lot/Serial number of the product displayed.
In a similar manner, we can display the Lot/Serial numbers on the invoices. After validating the delivery, I am creating the invoice for the order.
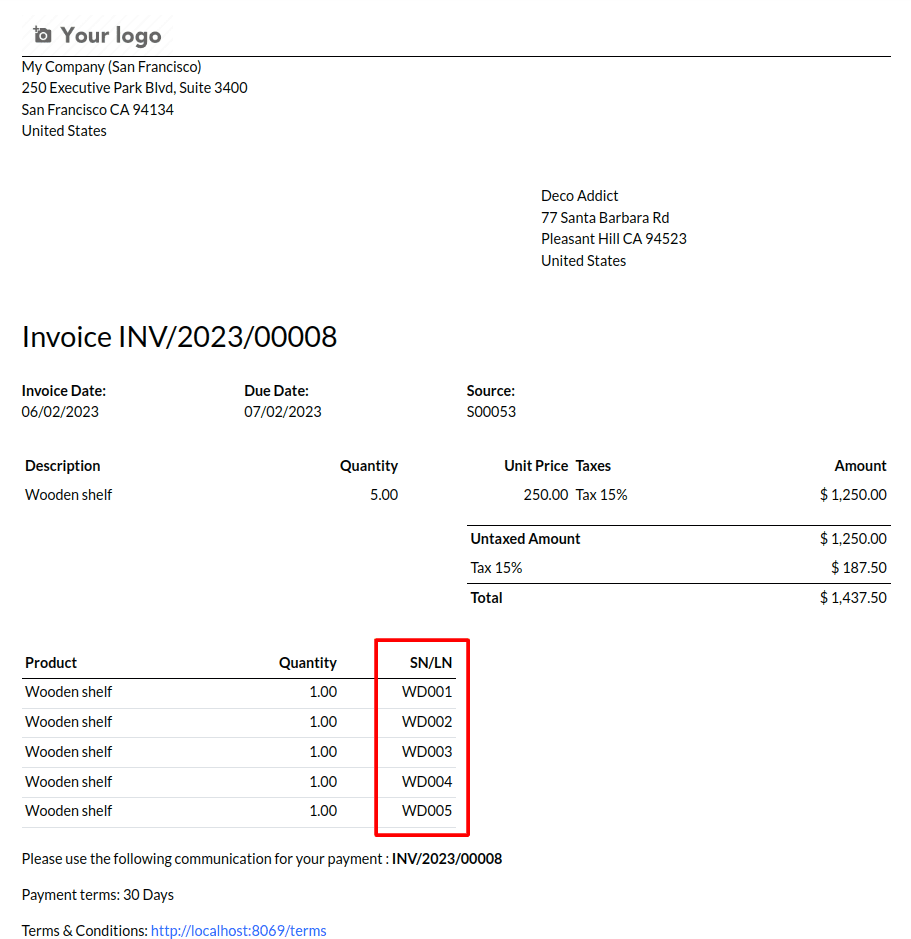
So here also, you can see the Lot/Serial number on the invoice.
Expiration dates with product Traceability
You need to activate a few additional characteristics from the General Settings of Inventory in order to assign the functionality of product expiration.
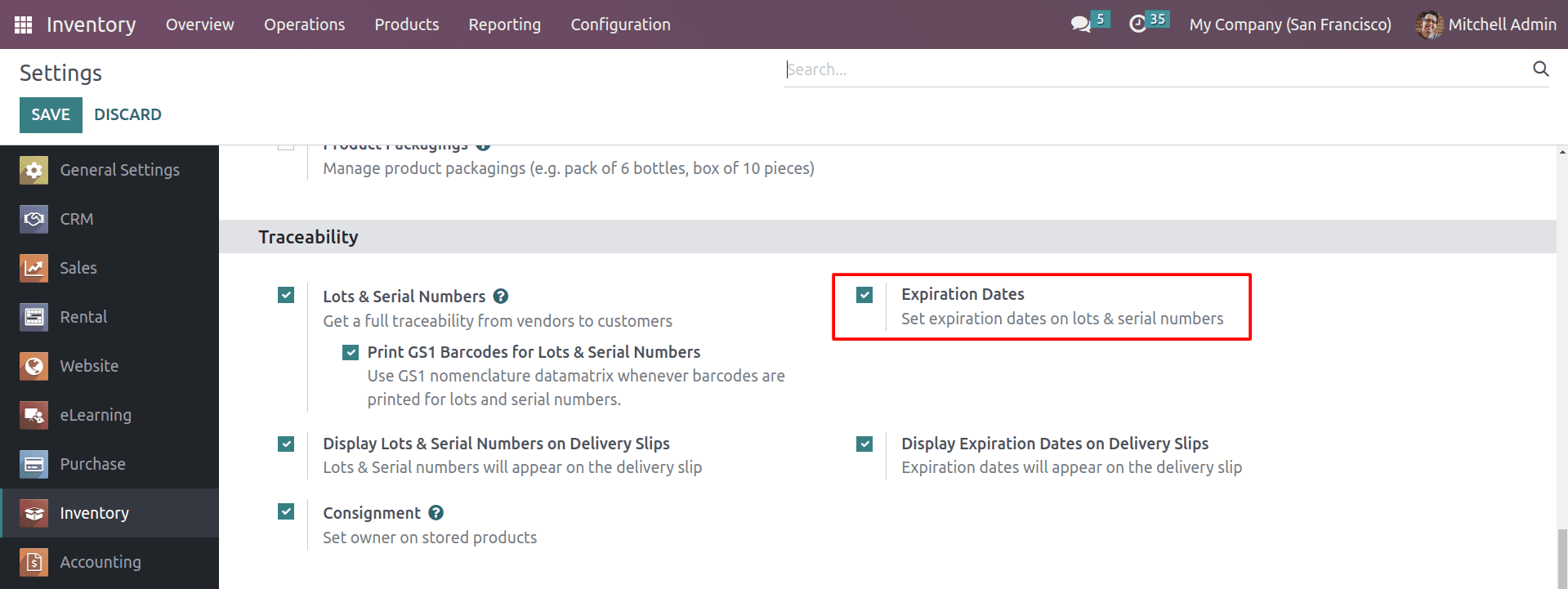
After enabling the expiration date feature in the setting, head into the inventory tab of the product form.
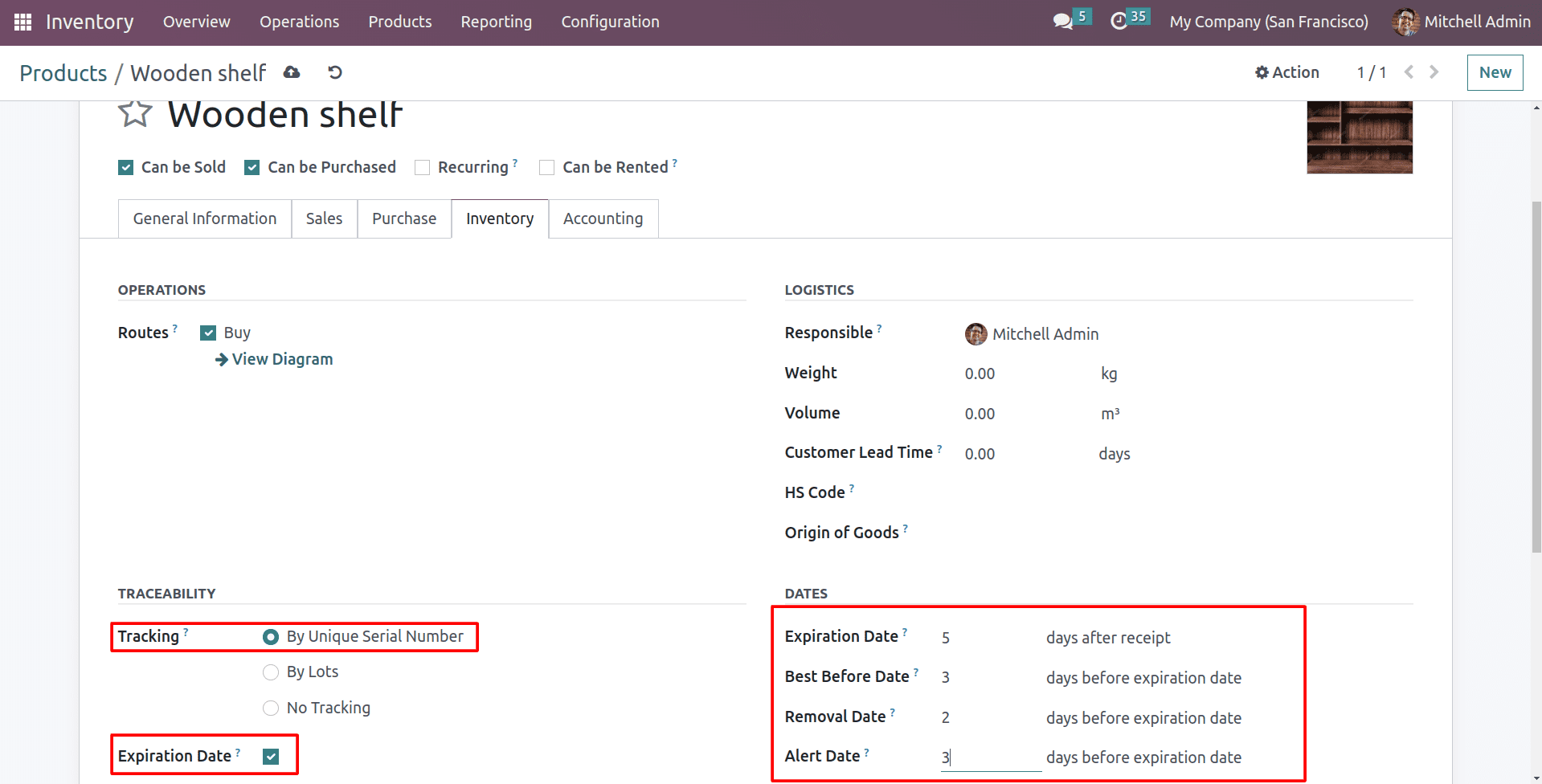
By enabling the traceability of products, you can provide them with expiration dates. And you can set up the expiration date after the receipt date, the best before date, the removal date, and the alert date for the product.
After providing the expiration details, create a purchase order for this product.
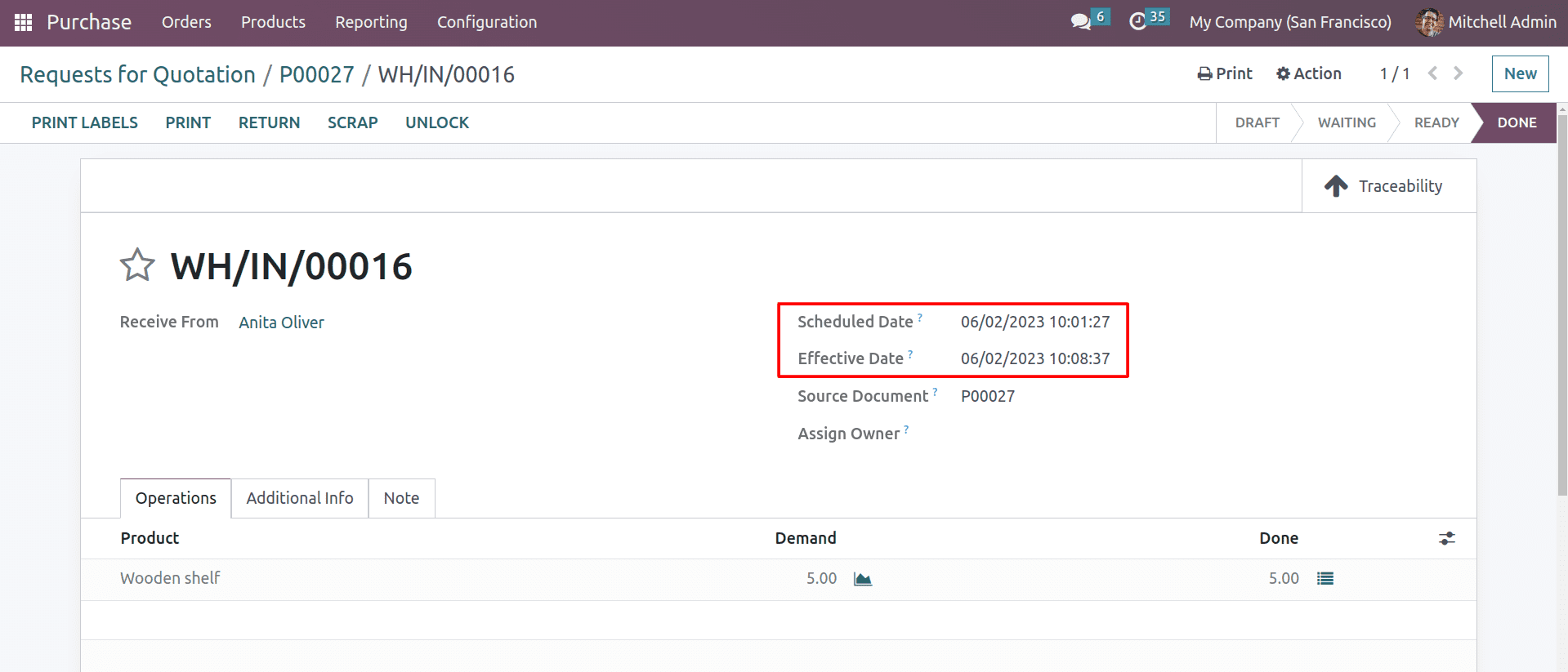
Here you can see the scheduled date for the receipt is 06/02/2023.
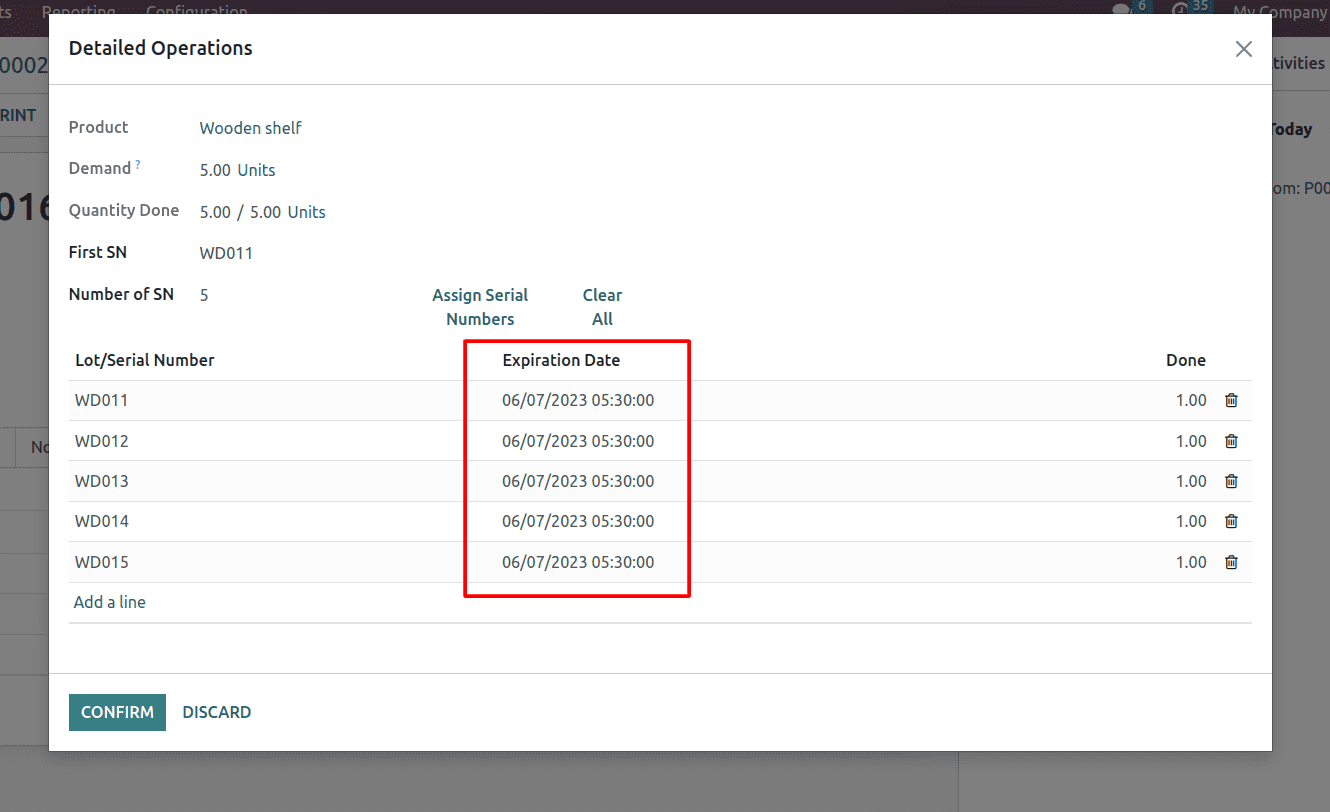
And the expiration date became 06/07/2023 because we specified that the expiration date would be five days after the receipt date.
And let’s open one of these Lot/Serial numbers from the product menu of the inventory module.
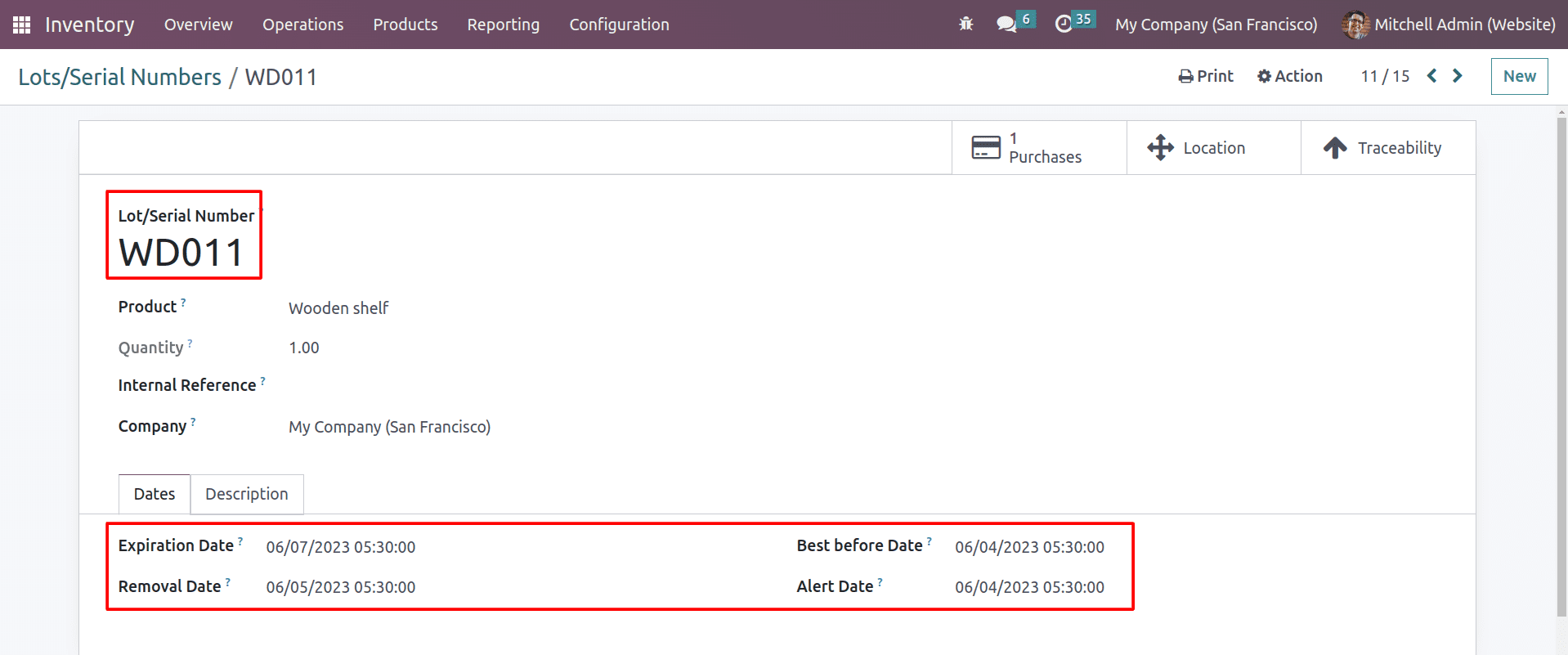
From here, you can also see the best before date, removal date, and alert date based on the days we gave in the product form.
In conclusion, lots and serial numbers are an important part of inventory management in Odoo 16. In addition to tracking product movement, lot and serial numbers can also be used to track product quality using the expiration date feature.