Odoo ERP in inventory management business is not only inevitable but also pivotal. Odoo’s functional features simplify the whole process of managing and tracking the stock level of business, thereby improving the efficiency of an organization.
ERP for Inventory management simplifies the process of stock level managing and tracking, thus paving the way for improving the company efficiency and productivity. With the help of effective stock methods in Odoo Inventory, one can efficiently manage all the internal operations happening within a company.
Sometimes, an inventory management turns out to be hectic, missing all real-time information necessitating for the next action. In the absence of an ERP software, an inventory management business/company may face numerous challenges like Product stock-outs arising the situation of backorders, secondly the increased use of warehouse spacing and product maintenance, thirdly the lack of product traceability resulting failure in meeting the demands of customers and last but not least the inability to find exact location leading to loss of time and other resources, etc.
With the implementation of ERP solutions like Odoo, one can avail open source alternatives for a complete inventory management for any business size and complexity. Odoo ERP’s advanced features like double-entry inventory with no stock input, total traceability on products, Drop-shipping, Cross-docking, Multi-warehouse management, Routing, Product shipping management and other exquisite features make it an all-inclusive suite of application for your inventory management. For further enhancement, Odoo inventory also comes fully integrated with other applications like Purchase, Sale, Accounting, Manufacturing and Repairs, Shipping connectors for executing better efficiency in managerial functioning.
This blog explains the role of routing in warehouse management and how efficiently Odoo transacts the routing function.
Routing is all about the process of order picking where the products are retrieved from specified storage locations based on the customer orders. Route defines the path a product must follow. And routes are made applicable depending on the products, sales order lines, warehouses etc. To fulfill a procurement (i.e. the necessity of certain quantity of product to a specified location), the system will search for rules belonging to routes that are defined within related product/sale order.
This process is considered to be the most laborious process in warehouse management. It almost constitutes sixty percent of the total labor activities in a warehouse. Especially in the distribution sector, the routing is always carried under time constraints causing orders to arrive late, or the orders getting shipped the same day at pre-fixed departure times leading to peak loadings in warehouses.
Odoo eradicates this problem and thus smoothly transacts the warehouse workflow. In Odoo, the route comes as a collection of procurement rules and push rules where the procurement rules describe how procurements on specific locations should be fulfilled e.g.: where the product should come from (source location), whether the procurement is Make to Order or Make to Stock. And push rule trigger when the products should enter a specific location. They automatically move the product to a new location.
Odoo facilitates for advanced push /pull configurations like management of manufacturing chains of products, managing the default location per products, defining routes according to business needs such as quality controlling or after sale services and also automating return moves for rented products by customers.
Let us see how it works.
Warehouse management is often challenging as it revolves around optimizing the stock levels, managing the physical space, tracking the orders and deliveries. However, with the expansion and growth of a company, the warehouse challenges gets multiplied as there comes the additional number of warehouses to manage. In Odoo, warehouse constitutes the building or place where the stock items are stocked. In Odoo, one can easily set up multiple warehouses and create smooth and transparent moves between the warehouses.
You can add any number of warehouses under your company.
Inventory -> Configuration -> Warehouse Management -> Warehouses -> Create
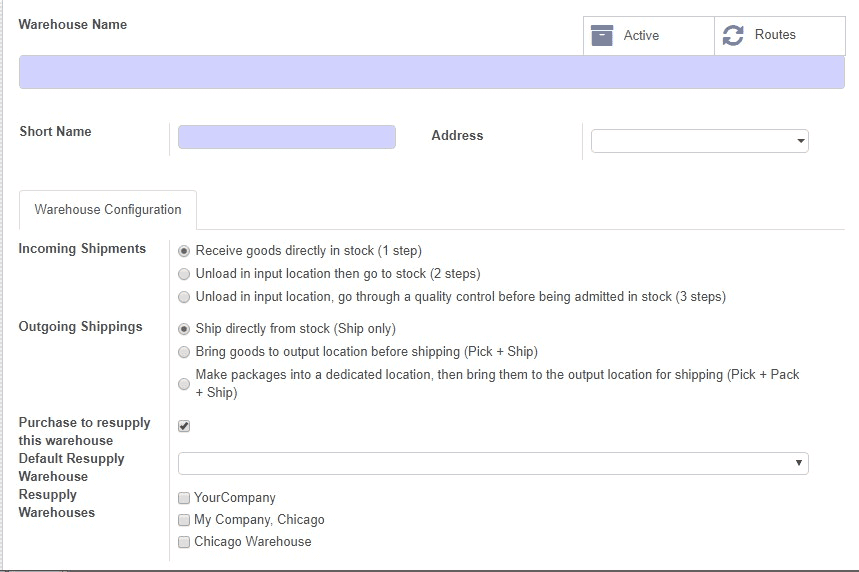
By clicking the Incoming Shipment and Outgoing Shipment option, one can choose any of your existing warehouses for re-supply.
In Odoo, Location constitutes a specific space within the warehouse just like a shelf, a floor or an aisle. The location is part of the warehouse and one can configure single or multiple locations under one warehouse. Every In and Out transactions are carried and recorded through Locations.
There are 3 types of locations:
1. Physical Location: These are locations within your warehouse, where the loading and unloading of your warehouse take place. E.g.; Shelf or a department.
2. Partner Location: This location not under your warehouse but space, within a customer or vendor’s warehouse.
3. Virtual Location: This is a virtual location which may not be physically available, but comes handy when you want to place the lost products out of your stock due to inventory loss or when you want to take into account the products that are on their way to your warehouse (Procurements).
Inventory -> Configurations -> Locations
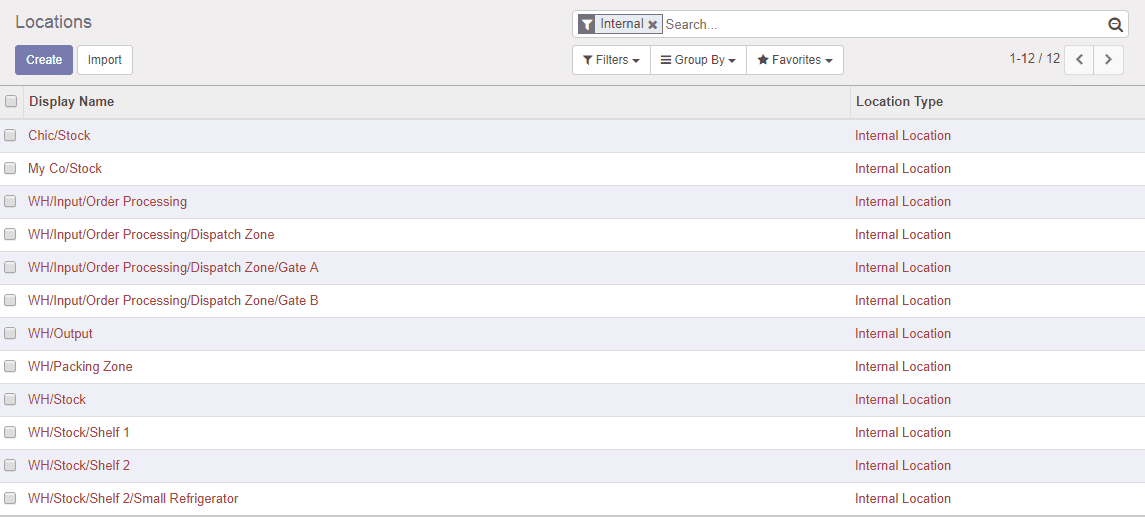
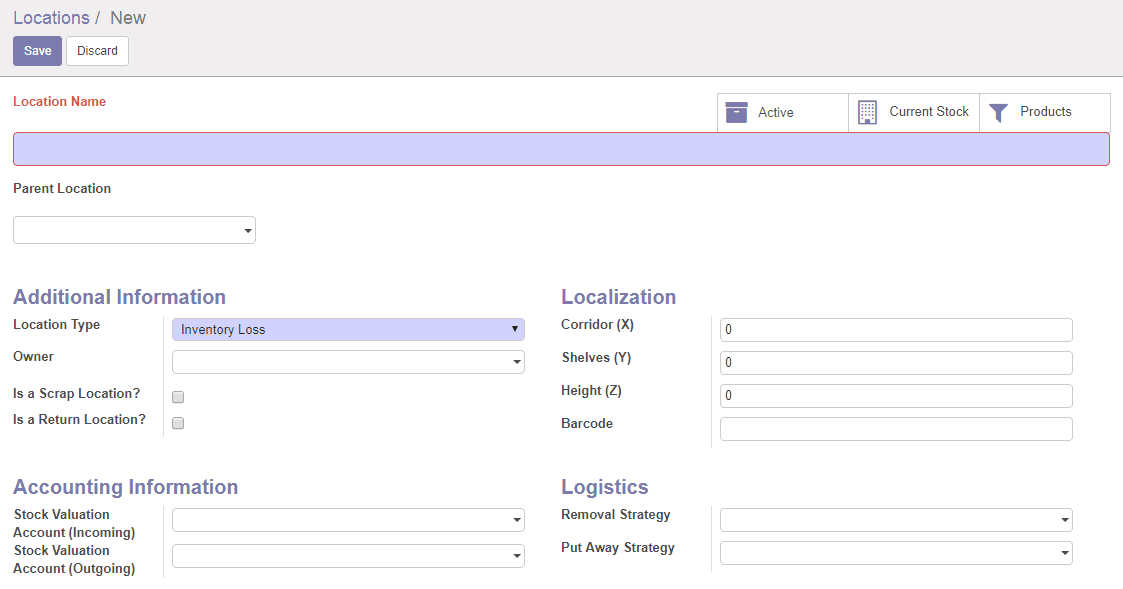
Routes are defined as different possible ways through which a product is acquired or sold from your warehouse. One can simply follow a single step process (like vendors warehouse to your warehouse) or can configure multiple step routes.
You can see a field asking the Route while creating a Product in Odoo. Route ensures a sale or purchase product is properly tracked.
You may define new Route rules from
Inventory -> Configuration -> Routes -> Create
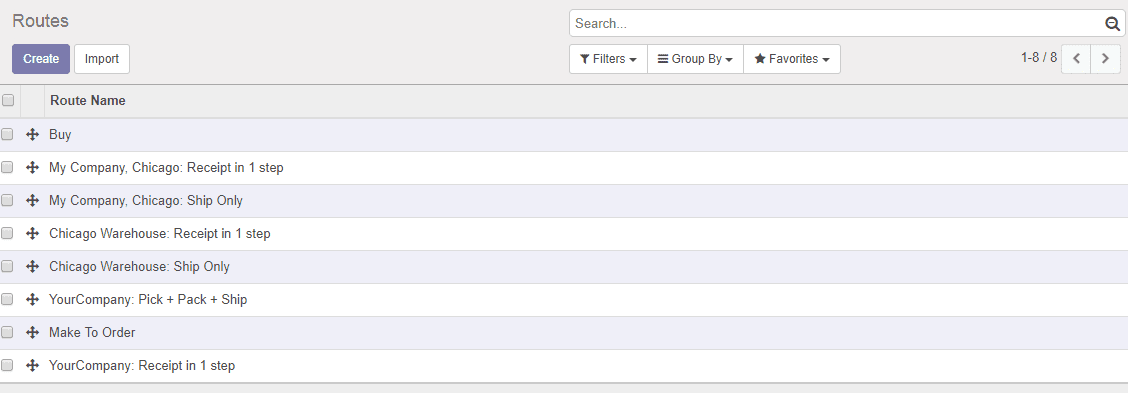
Procurement rule in Odoo
The procurement inventory control begins with a customer's order. Here the companies can seamlessly conduct the request by making only sufficient product that needs to fulfill customer's order. The advantage that procurement rule brings along is that there will be no excess of inventory that needs to be stored. This helps in reducing the inventory levels, the cost of carrying and storing goods.
Under the procurement rule, there are three types of actions possible.
* Move from another location rules
* Manufacturing rules that will trigger the creation of manufacturing orders.
* Buy rules that will trigger the creation of purchase orders.
All these rule settings help in keeping the inventory levels to a minimum. It initiates for only a requisite quantity of inventory that is needed to meet the customer demand. Thus the Make to Order system can eliminate the waste by reducing the amount of storage space required for inventory storage and also the costs required for storing the goods.
Push rule in Odoo:
With push rule, a given quantity of product is moved to the source location, according to the parameters set like destination, location, any delay or movement type. It can be triggered both automatically and manually.

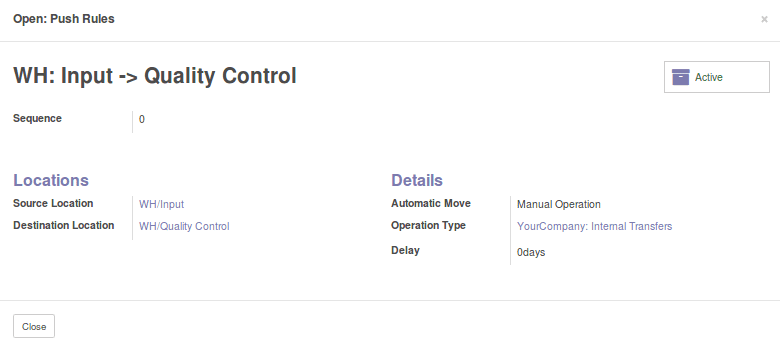
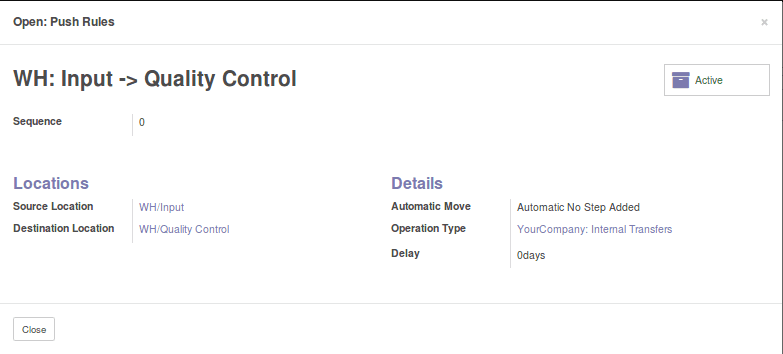
With Odoo push rule, the companies can easily predict the quality of products purchased by the customers.


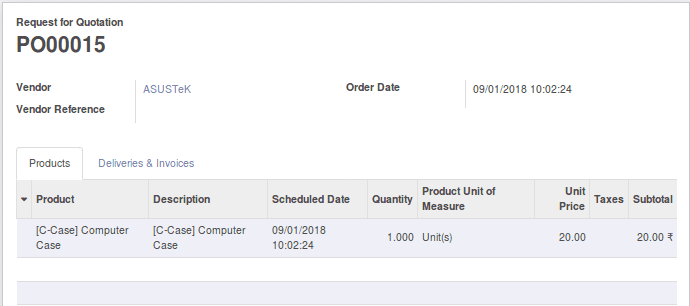

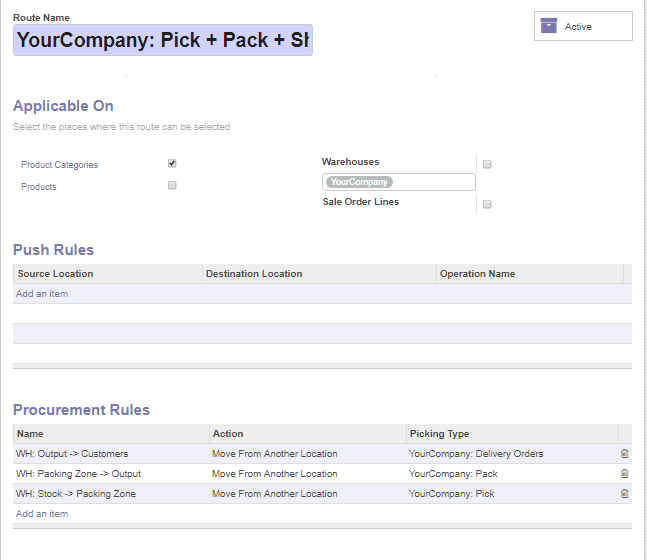
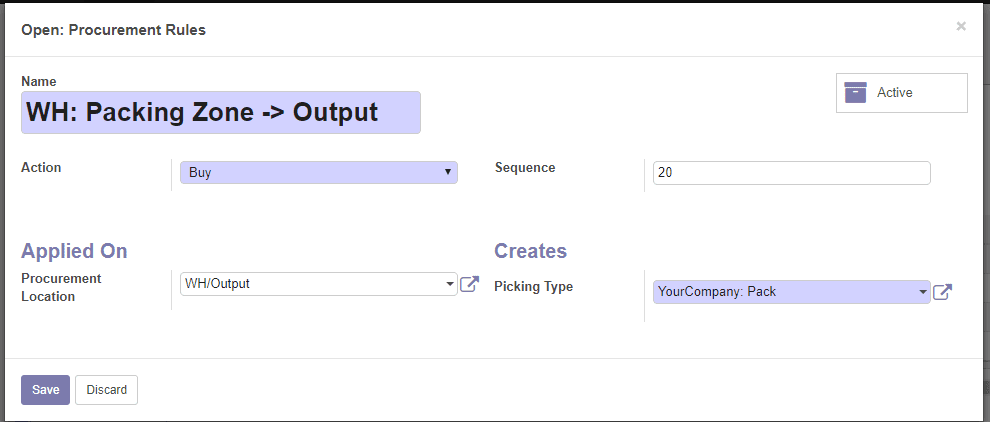
Reordering Rules in Odoo:
Reordering rule is a kind of custom rule that helps to replenish the inventory automatically.
For example, if you wish to re-order a product when the stock reaches 10 units. You can set a Rule, and when you Run Scheduler system will check this Rule and take appropriate action automatically. In short, the reordering rule helps in maintaining a backup of a minimum quantity of stock for each specified item.
In case, if you have some demanded items, and you don’t wish to face an out of stock situation or you just want to keep a very limited quantity in stock, Odoo reordering rule comes handy. It allows keeping minimal stocks by creating the rule by mentioning minimum quantity and maximum quantity.
Minimum Quality specifies the minimum number of the quantity that should be kept in an inventory space.
Maximum Quantity specifies the maximum number of quantity i.e. the upper limit for a product quantity. And thirdly the quantity multiple with the lowest number of items that can be ordered at once.
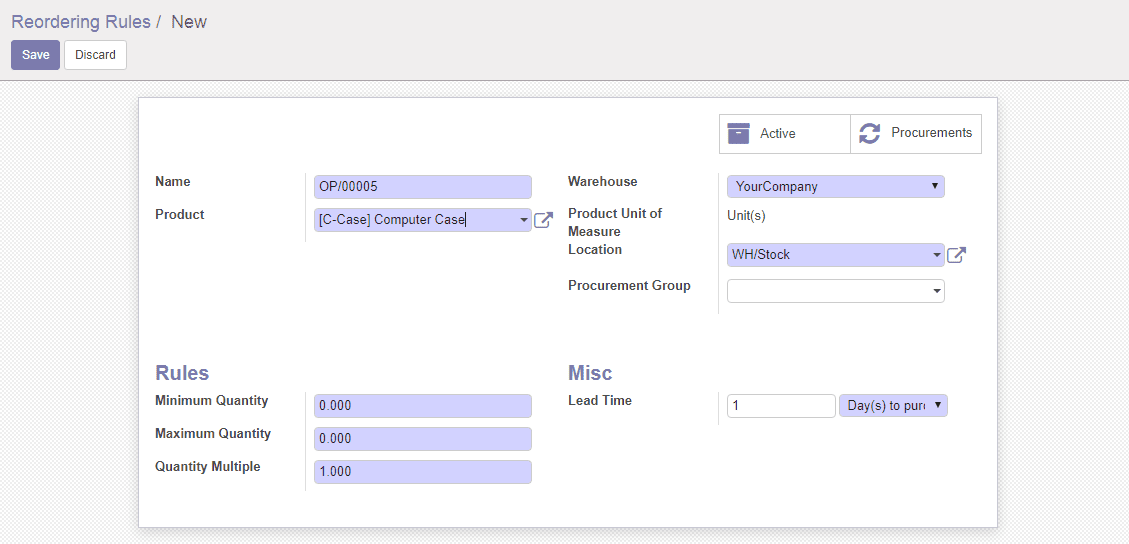
With the option of Procurement Group, one can also set the procurement and picking option For a product.
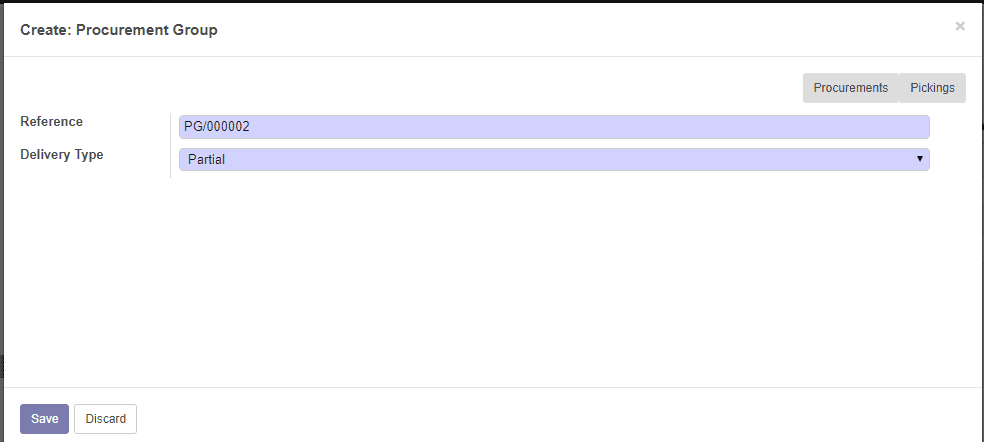
The other product shipping management rules in Odoo includes-
Firstly the Cross-docking, which is a practice in the logistics of unloading materials from an incoming semi-trailer truck or railroad car and loading these materials directly into outbound trucks, trailers, or rail cars, with no storage in between.
Secondly, Drop-Shipping which move products from the vendor/manufacturer directly to the customer (could be retailer or consumer) without going through the usual distribution channels. Products are sent directly from the vendor to the customer, without passing through one’s own warehouse.
Removal Strategies in Odoo are implemented during the product picking operation to assure the deliverance of the best product to the customers. It helps in optimizing the distance for a worker to retain the quality of every product they carry. Whenever a product movement is to take place, Odoo helps in finding the suitable and available products and later initiate the action of product shipment. Odoo’s removal strategy is based on the product category or on the basis of location.

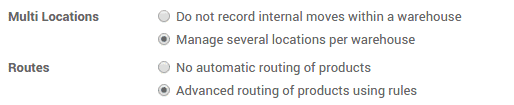
Here you can see the options like Lots and serial numbers, where one can efficiently manage several locations per warehouse and advanced routing of products using the rules.
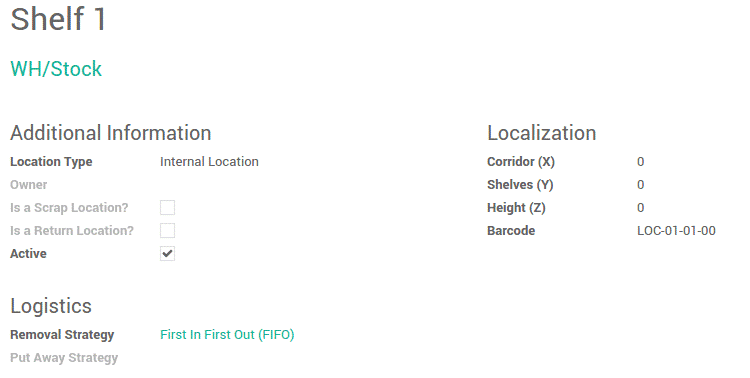
A First In First Out(FIFO) strategy implies to the situation where the products that stocked first will be moved out first. The companies especially the one selling the perishable goods must use the FIFO method to assure the quality check of their product deliverables. Also, the FIFO method is highly beneficial for the companies that sell the products with short demand cycles like clothing. Implementing the FIFO method, in this case, assure that no outdated styles( clothes) are stuck in the inventory.
A Last In Last Out(LIFO) is a strategy used when the products entered last are to move out first. LIFO is mainly used in the shipments of products which do not have a shelf life Eg: Liquor.
In First Expiry First Out(FEFO) warehouse management, the products are dispatched from the warehouse according to their expiration date. While clicking the available option, define Expiration date on serial numbers, one can easily manage the movement of products based on the expiration dates. In Odoo if you set the removal date on a lot or serial numbers it helps in picking the products with early expiry dates.

It will allow you to set best before date, end of life date, alert date and removal date on the serial number.
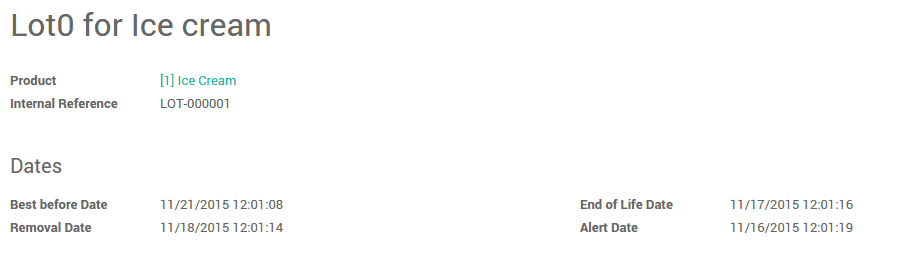
Best before Date: This option sets the date on which goods with the particular lot/ serial number start deteriorating. It acts as a call for action before the product turns dangerous to consume.
End of Life Date: This option helps with setting the data on which the goods with particular lot/serial number turns dangerous and not fit for consumption.
Removal Date: Helps in specifying the date on which the goods with particular lot/serial number should be removed from the stock.
Alert Date: Specifies the date on which an alert should be notified about the goods with a particular lot/serial number.
And in last, the Putaway Strategies decide to which location a specific product should be set when arriving somewhere.
In nutshell, Odoo Inventory Management ensures full traceability from supplier to customer with Odoo double entry inventory management. Everything is moved on time and nothing is lost midway.