Bill of Materials (BoM) is a list of raw materials or ingredients and their respective quantities needed to manufacture the final goods.
How to Create a Bill of Material
The relevance of BoM in Manufacturing Process
BoM is the basic building block of any manufacturing process. While creating a manufacturing order for a particular product we need to select the corresponding BoM of that product from the BoM list. So before creating a BoM, make sure that all the raw materials are already created in the product list. You can either create a BoM of a product from the product form itself by clicking on the ‘Bill of Materials’ Super button as seen in the figure.
Or you can create one from the menu
Manufacturing -> Master Data -> Bill of Materials -> Create
The final product and its quantity are required fields. Add each raw material and its quantity in the ‘Components’ tab by clicking ‘Add an Item’. After you added all the components, click ‘Save’ to save the BoM.
Reference in BoM
What is the use of reference in a Bill of Materials?
Suppose a manufacturing product has two or more bills of materials. But we can use only one BoM at a time in a Manufacturing Order. Reference is an easy way to differentiate each BoM in the list. We can assign each BoM, a reference string such that it will be easy to differentiate each BoM while creating a Manufacturing Order
If we did not give a proper reference to BoM, we can’t identify it easily.
BoM type or Kit (Phantom) in BoM
Kit (Phantom): It is a useful feature to sell a product as a component. You can set a BoM as Phantom Kit so that when you generate a Sale Order for that product the associated component quantity in Inventory will be changed according to it. A Kit-type BoM will not be available in Manufacturing.
Now we can check the miscellaneous tab, there are 3 fields.
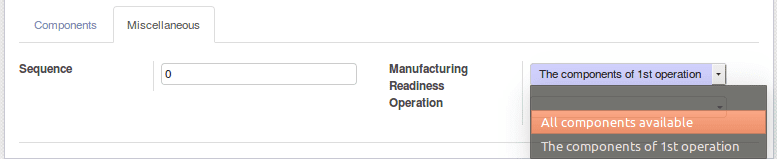
Sequence in BoM
‘Sequence’ is used to prioritize the BoM of a particular product.
Manufacturing Readiness in BoM
If we set ‘Manufacturing Readiness’ as ‘All Components Available’. Then MRP order will stay at the ‘waiting’ stage until all the components in the BoM are available. If it is set as ‘The components of 1st operation’ then the manufacturing process will be possible even if the components are partially available.
Operation in BoM
‘Operation’ is not a mandatory field. When a procurement has a ‘produce’ route with a picking typeset, it will try to create a Manufacturing Order for that product using a BoM of the same picking type. That allows defining a procurement rule which will trigger different manufacturing orders with different BoMs.
Manufacturing configuration and BoM
Manufacturing configuration can enable some extra fields in BoM, let’s check each one.
Product Variant in BoM
If we enable the Variants, then the BoM form changes as below.
Here we can see that there is an additional field ‘Product Variant’ under 'Product'. If we select a particular variant, then this BoM will affect only that particular variant.
Byproducts in BoM
Manufacturingconfiguration provides another setting to enable the “By-products”
If we enable this option, we can see that a new tab ‘Byproducts’ is appeared in the BoM form.
We can add the byproducts here. So, when we manufacture the product with this BoM the byproducts will be created automatically.
Routing in BoM
Routings and planning.
This option makes the manufacturing process more advanced. Routing allows each company to configure a more detailed manufacturing process matching their internal workflow by setting up Work Centers, Work Orders, etc.
In routing, we can specify each operation conducted in the manufacturing process and each operation will have its own corresponding work centers too.