The process of disassembling a product involves the removal of its individual parts. In certain exceptional circumstances, a manufacturing enterprise may find it necessary to disassemble a product, which may occur as a result of procurement activities. Maintaining accurate records of such disassembled orders is imperative in such scenarios. The Odoo 17 Manufacturing platform facilitates the creation of disassembled orders for previously manufactured products.
Why Should Manufacturing Facilities Unbuild a Product?
* Reclaiming damaged parts or raw materials.
* Handling returns.
* Repurposing parts for new manufacturing.
* Adjusting inventory levels.
* Reassembling parts for new products if defective.
* Accurately recording deconstructed materials and parts.
Benefits of Product Unbuilding in Odoo 17
* Maintains precise inventory levels, reducing waste and optimizing resource use.
* Saves costs by allowing salvage of valuable components from defective or returned products.
* Supports sustainability by minimizing waste and promoting material reuse.
* Enhances traceability by linking unbuild orders to original manufacturing orders.
Unbuilding a Manufactured Product
To initiate this process, navigate to the "Unbuild Orders" option within the "Operations" menu. Here, a dedicated interface for managing Unbuild Orders independently will be provided, allowing for the creation of Unbuild Orders for acquired goods.
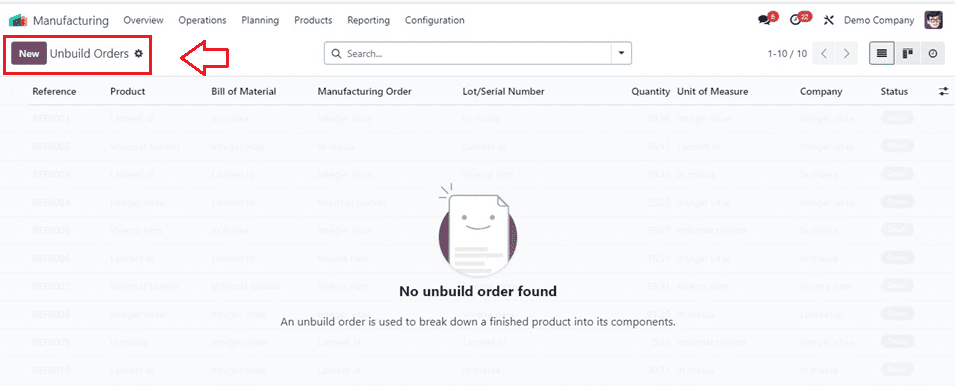
Within the "Unbuild Orders" interface, a dashboard displaying order References, Product, Bill of Material, Manufacturing Order, Lot/Serial Numbers, Quantity, Unit of Measure, Company,jn and Status details of every unbuild order will be present. To create a new configuration, simply click on the "New" button to access the configuration form.
The newly opened configuration form enables the configuration of new Unbuild Orders. Here, input fields are provided to specify the Unbuild Order Name, Product, Bill of Materials, Quantity, Manufacturing Order (if applicable), Source Location, Destination Location, Lot/Serial Number, and Company details as shown below.
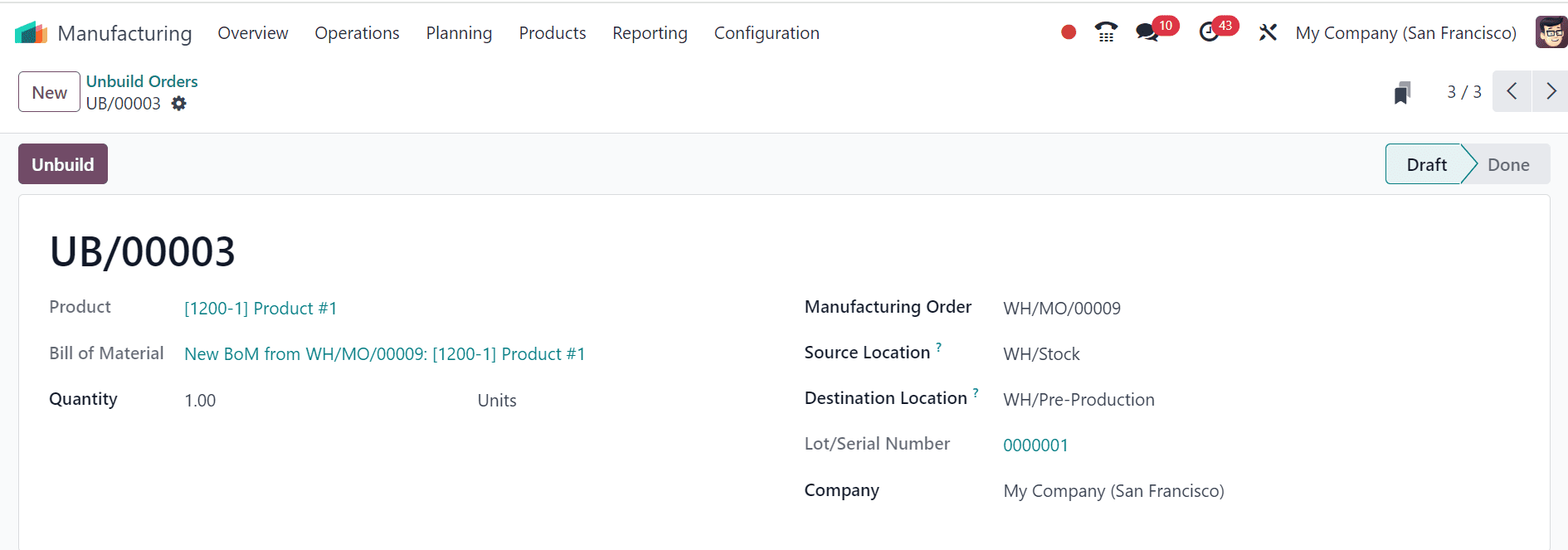
Upon completion of the configuration, clicking the "Unbuild" button, that initiates the unbuilding process.
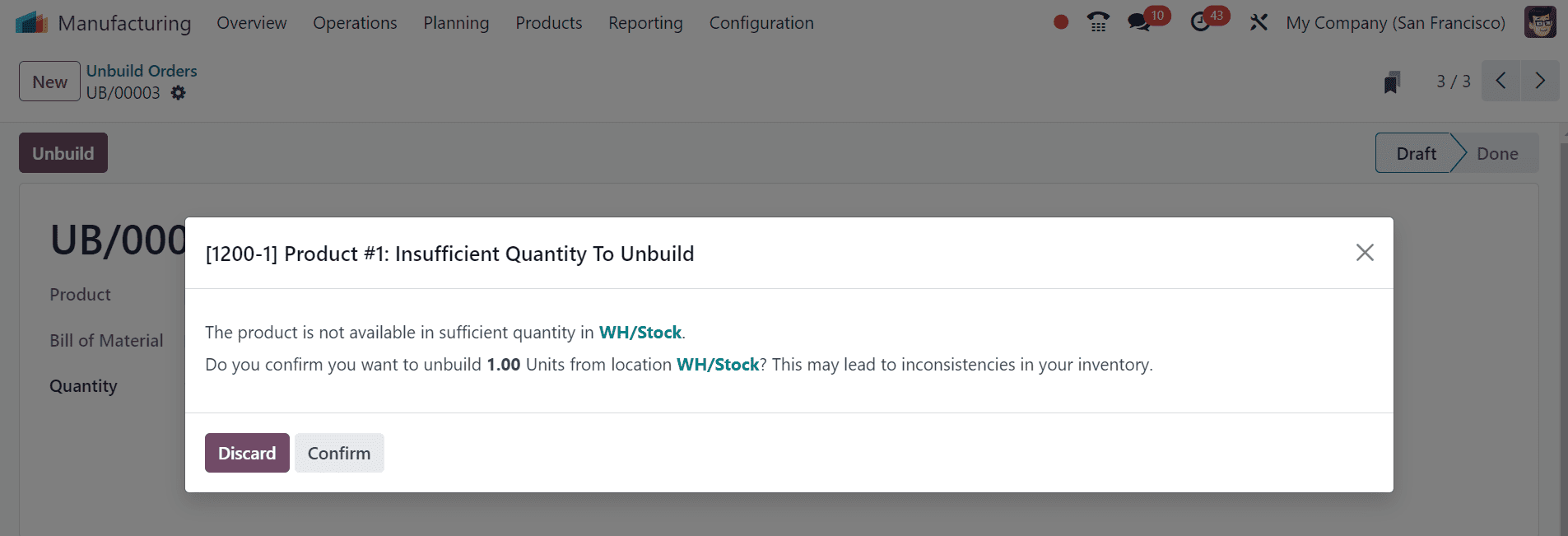
The Unbuild Order is then stored within the Odoo database, and a "Products Move" smart button is displayed within the configuration form, allowing access to details of every component utilized in the unbuilt product, presented in a dashboard format.

This "Product Moves" dashboard provides comprehensive details regarding the unbuilding date, reference, product, lot/serial number, quantity, unit, etc., for each component. Furthermore, the newly created Unbuild Order can be managed directly from the "Unbuild Orders" dashboard.
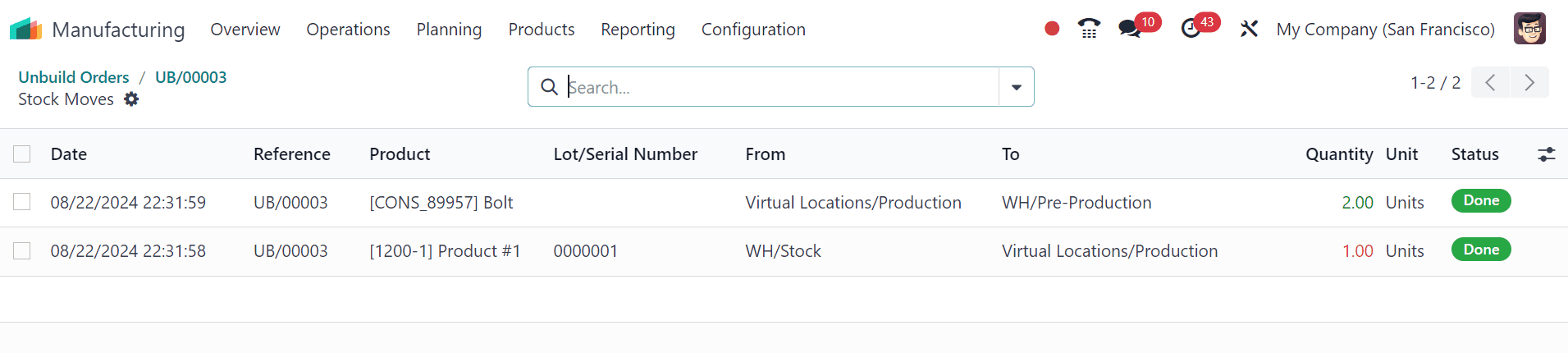
This unbuild feature is one of the most useful features of Odoo 17's Manufacturing module for inventory management, quality control, and reverse logistics. The capacity to dismantle a product guarantees that companies can effectively retrieve and recycle important resources, whether handling faulty goods, consumer returns, or component reuse. You can improve sustainability and economic effectiveness in your manufacturing operations by managing the unbuilding process with the help of this blog's step-by-step instructions.
To read more about How to Unbuild Your Manufactured Products with Odoo 16 Manufacturing, refer to our blog How to Unbuild Your Manufactured Products with Odoo 16 Manufacturing.