In any manufacturing operation, equipment maintenance is crucial for ensuring smooth production processes and minimizing downtime. With the Advent of digital solutions like Odoo 17, managing equipment maintenance during production has become more efficient and streamlined. Equipment maintenance in production involves a series of activities aimed at presenting the functionality and reliability of machinery and tools used in the manufacturing process. These activities include preventive maintenance and corrective maintenance. This blog explores how Odoo 17 facilitates effective equipment maintenance within the production workflow.
Enhancing the lifecycle of machinery hinges greatly on meticulous maintenance protocols. Odoo 17's Maintenance module services as a comprehensive solution, alleviating any concerns related to maintenance tasks. By leveraging Odoo ERP, users can seamlessly orchestrate the intricacies of maintenance workflows, spanning from establishing maintenance stages and dedicated teams to managing maintenance requests and coordinating schedules via calendars. This holistic approach not only streamlines maintenance operations but also ensures optimal performance and longevity for industrial equipment, thereby maximizing efficiency and minimizing downtime.
Maintenance Teams and Work Centers
The maintenance team plays a pivotal roll in ensuring the smooth operation of mechanical equipment and machine within a company. Among its primary functions are performance monitoring, routine maintenance, and thorough inspection to preemptively address potential issues. Within the Odoo 17 Maintenance module, users can efficially allocate equipment maintenance tasks to designed teams.
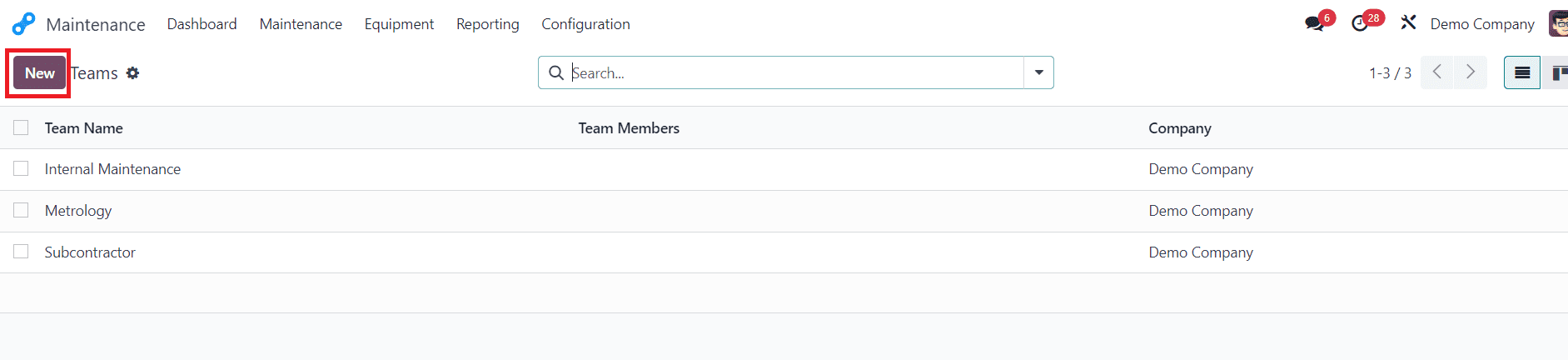
To initiate this process, users navigate to the Maintenance Teams menu within the Configuration tab. From there, they can easily create new maintenance teams by clicking on the New icon, as illustrated in the accompanying screenshot.
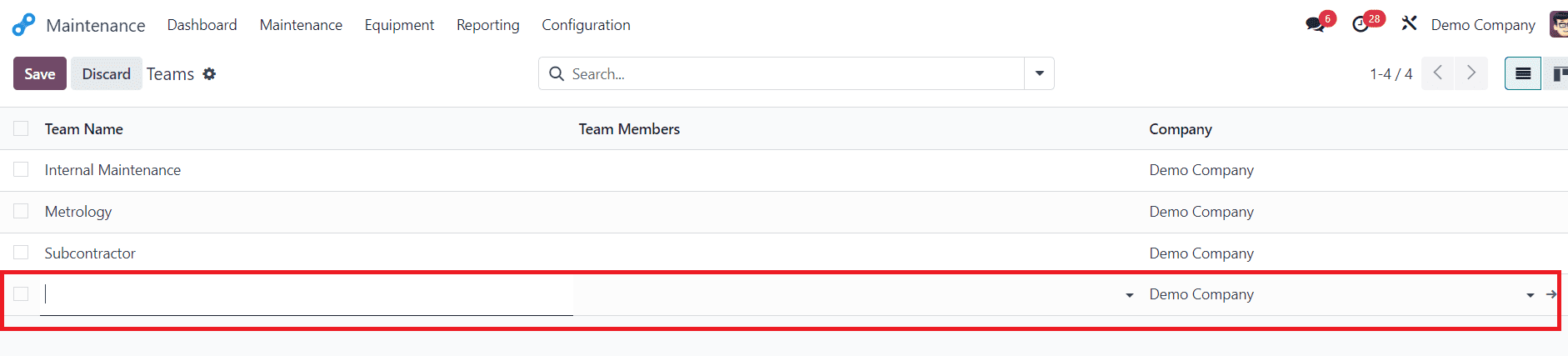
Upon clicking the New icon with the Maintenance Teams menu, users are greeted with a new space at the bottom of the Teams window, facilitating the seamless creation of new maintenance teams. Within this space, users are prompted to input essential details such as the Team Name, associated company, and designed Team Members, mirroring the layout depicted in the given.
To estate various work centers for the machines within your company, navigate to the Work Centers menu located under the Equipments tab within the Odoo 17 Maintenance module.

To introduce a new work center tailored to your company's specific requirements, simple click on the New icon, as highlighted in the promoted screenshot. This initiates the creation process, allowing users to input certain details such as the name of the work center, Tag, alternative work centers, working hours, associated cost per hour, OEE target, capacity, and any additional relevant information.
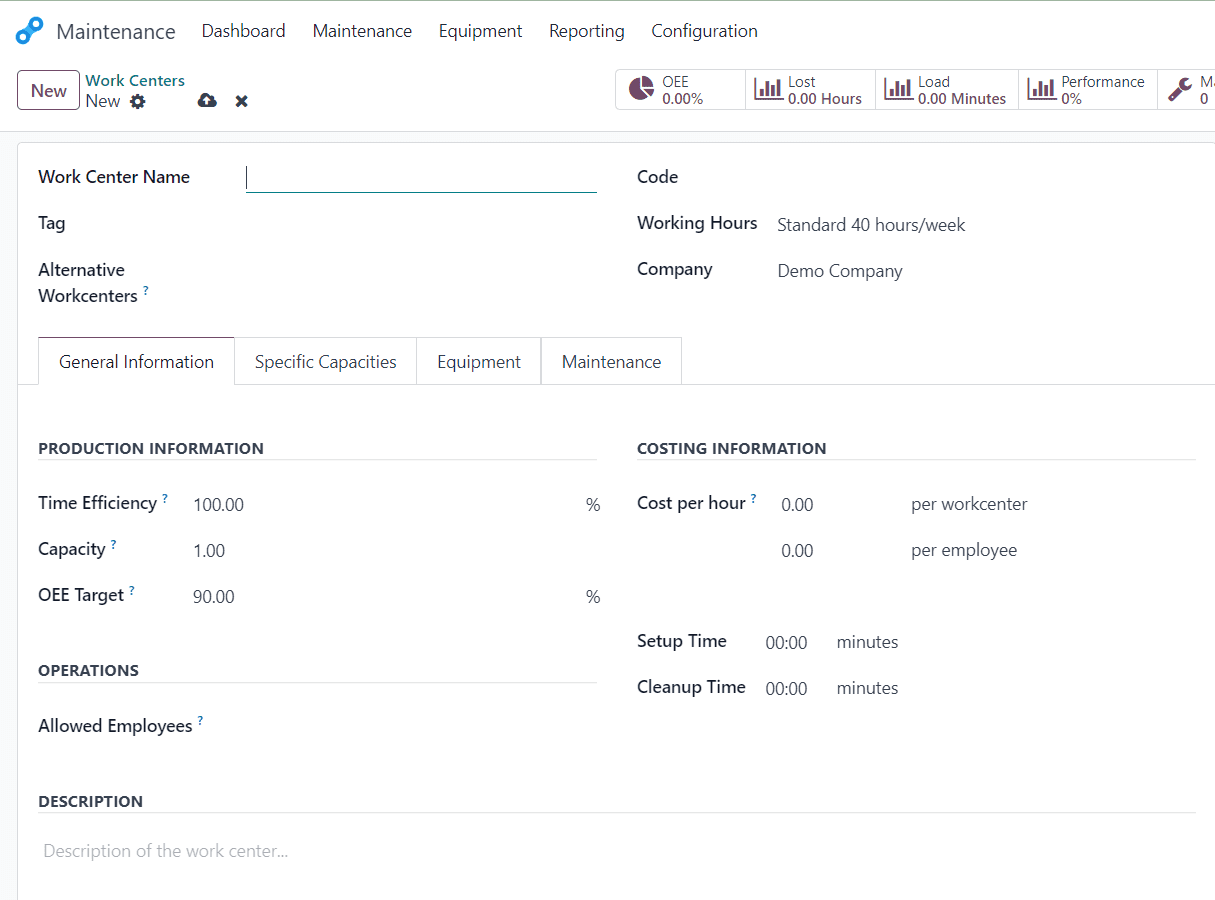
After establishing work centers for your company's machines, protected to input the respect machines within each work center by navigating to the Equipment tab. To do so, click on the "Add a line" option, which enables users to popular the Equipment tab with pertinent details.
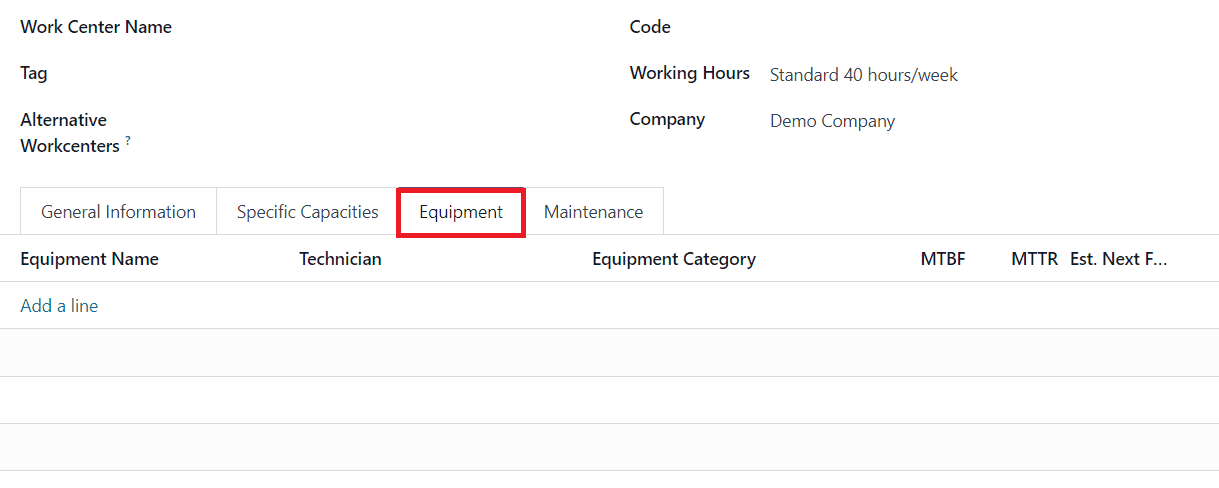
Within the Equipment tab, users can conveniently view essential information such as the Equipment name, Equipment category, and Technician details, as depicted in the given. By systematically organizing this information, users can effectively manage and monitor the status of each machine, streamline maintenance activities, and ensure optimal performance across the manufacturing operation.
Equipment Categories
Within the Odoo 17 Maintenance module, equipment category offers a structure approach to organizing machine based on specific criteria. Managing equipment categories is streamlined and intuitive, empowering users to categoryize equipment easily.
To begin categorizing equipment, users navigate to the Equipment Categories menu located within the Configuration tab. Here, users can access a comprehensive list of equipment categories, as illustrated in the provided screenshot.
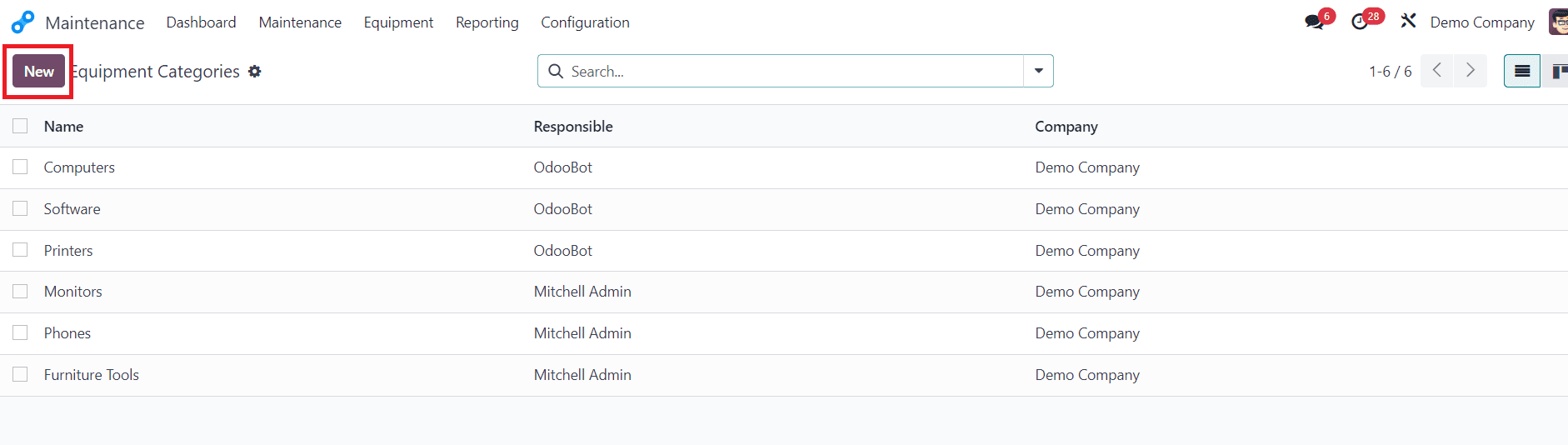
By using this interface, users can easily define and manage equipment categories according to their unique organizational needs and operational requirements.
To create a new equipment category for a specific machine, users can utilize the New icon with the Equipment Categories menu in the Odoo 17 Maintenance module. By following these steps, users can efficially define a category tailored to their organizational needs.
*Click on the New icon with the Equipment Categories menu.
*In the promoted space, enter "Monitors" as the Category Name to designate this category for monitors.
*Select the appropriate company from the available options.
*Choose the Responsible person who will oversee the maintenance and management of monitors within this category, ensuring accountability and efficient handling of tasks.
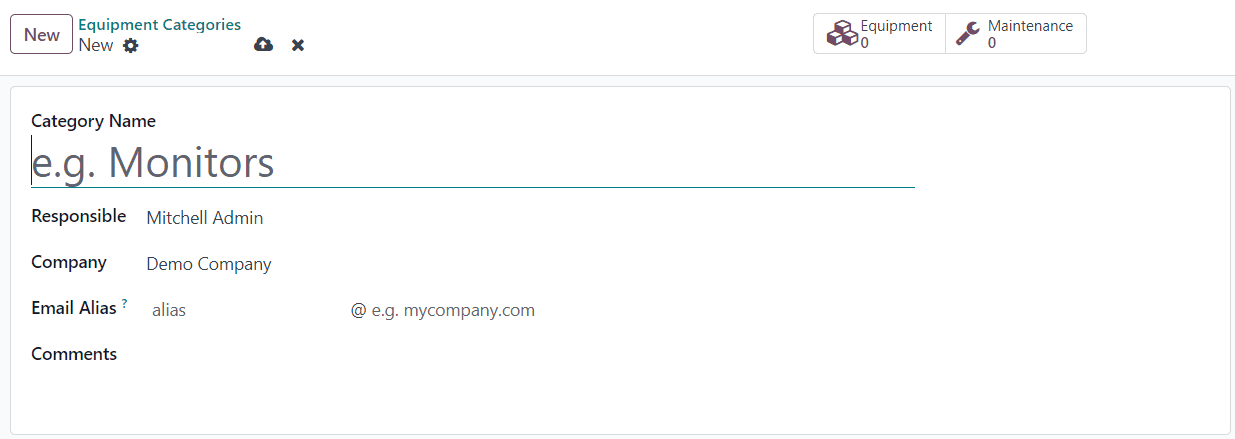
By inputting these details, users estate a new equipment category specificly dedicated to monitors within their organization.
Record Equipment in Odoo 17 Maintenance
To incorporate essential equipment needed for maintenance within your firm, users can seamlessly navigate to the Equipment window within the Odoo 17 Maintenance module. Within this interface, access the Machines & Tools menu under the Equipments tab to initiate the process of adding new equipment details. By clicking on the New icon with the Machines & Tools menu, users embark on creating comprehesive equipment tailored to their organization's needs.
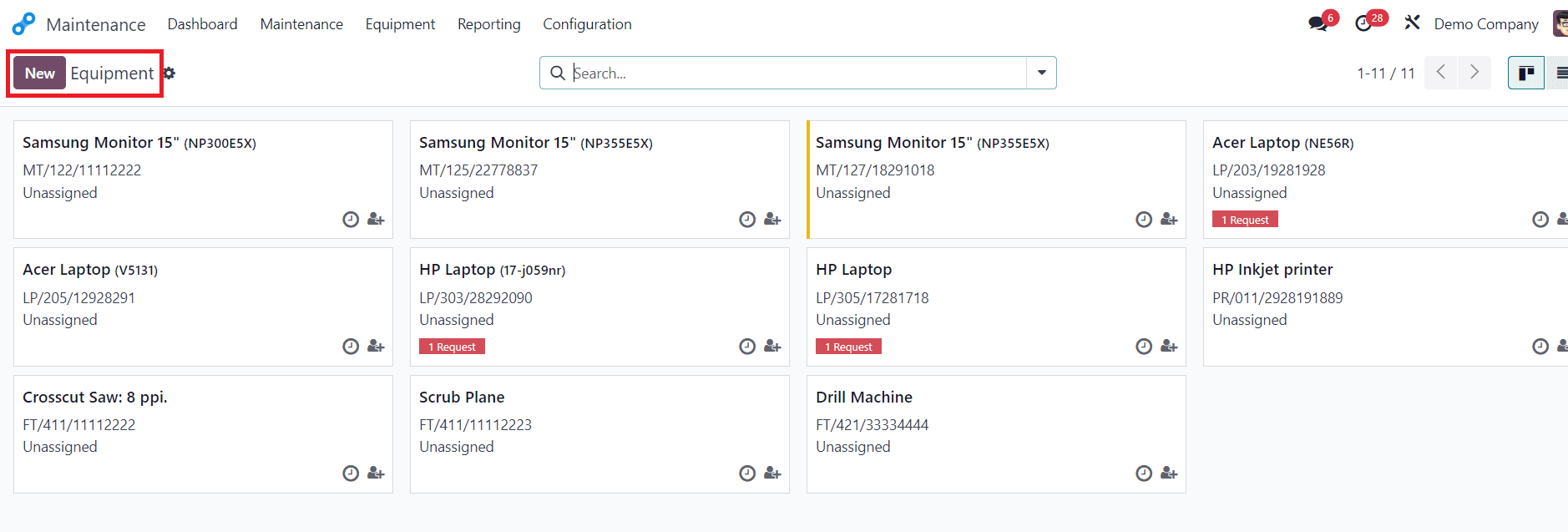
Within the creation interface, users can input a wealth of details to enrich the equipment profile. Alongside fundamental information such as the Equipment Name and Description, users can specific the Equipment Category, Company, Used By, Employee, Work Center, and Product Information.
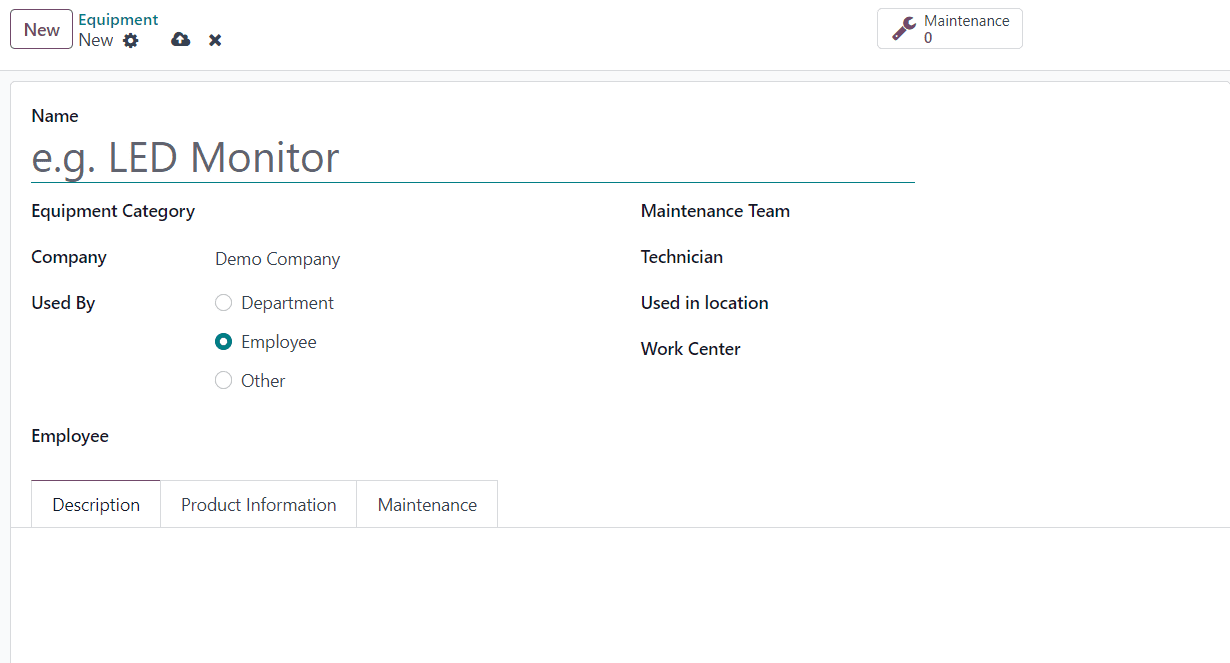
Within the Equipment window, users have the flexibility to specific individuals utilizing the equipment for company purposes through the "Used By" field. This field offers classification options such as Department, Employee, and Other, allowing for precise identification of equipment.
Upon selecting "Employee" from the "Used By" field, an Employee Field became visible, enabling users to designate the specific employee organized with the equipment. Users can easily select the revant employee from a dropdown menu popularized with employee profiles. Additionally, users are proposed to specific the company organized with the equipment, ensuring account record-keeping and organizational alignment.
Click on the dropdown menu with the Maintenance Team field and select the appropriate maintenance team from the list of available options. This team may include technicians, engineers, or maintenance personnel specially trained to handle maintenance tasks for the sealed machine.
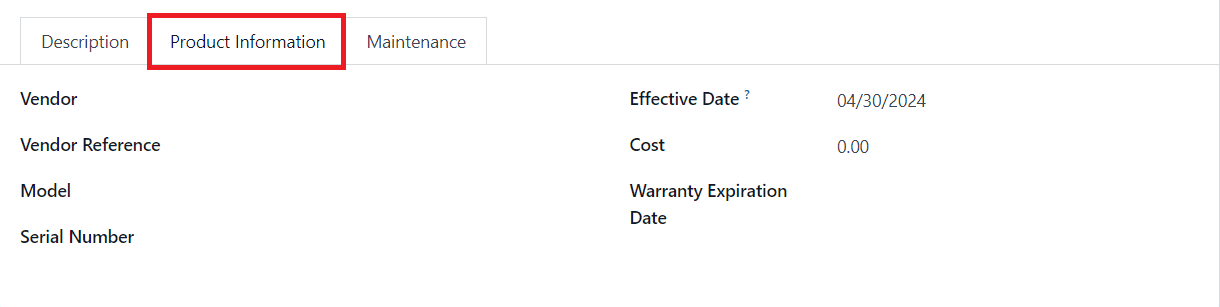
Below the Product Information tab, users have the option to input additional details about the machines. They can enter information such as Vendor, Model, Serial Number, Vendor Reference, Effective Date, Cost, and Warranty Expiration Date as shut in the example screenshot above.
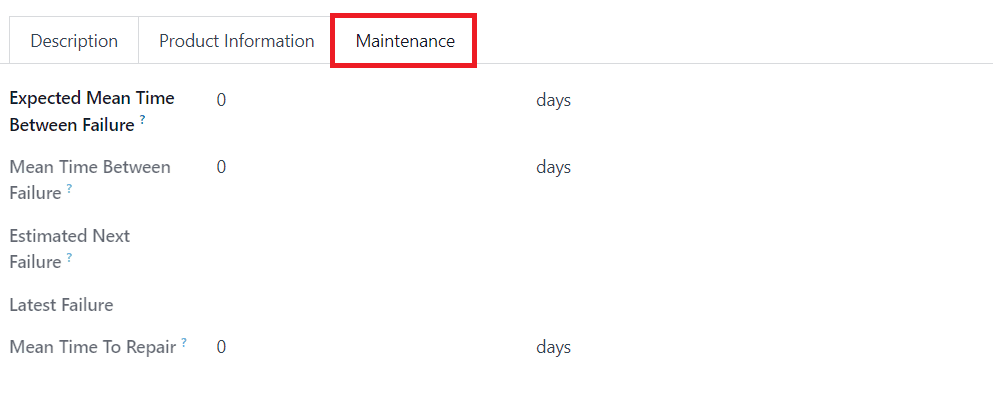
Under the Maintenance tab, you can find several key metrics for assessing equipment reliability and performance. Expected Mean Time Between Failures represents the average time expected between equipment, providing insights into the equipment. Mean Time Between Failure calculates the average time elapsed between filures based on historical data, offering a practical measure of equipment. Estimated Next Failure predicts when the next equation failure is likily to occur based on past performance and maintenance patterns. Latest failure logs the most recent equipment failure, allowing users to track and analyze the equipment's performance over time. Mean Time To Repair measures the average time requested to repair the equipment after a failure,aiding in assessing maintenance efficiency and downtime management.
This is how we record equipment details in the Odoo 17 Maintenance module.
Maintenance Request for an Equipment
Once your equipment records are set up, navigate to the Maintenance Requirements menu. Here you can manually create maintenance requests for specific equipment.
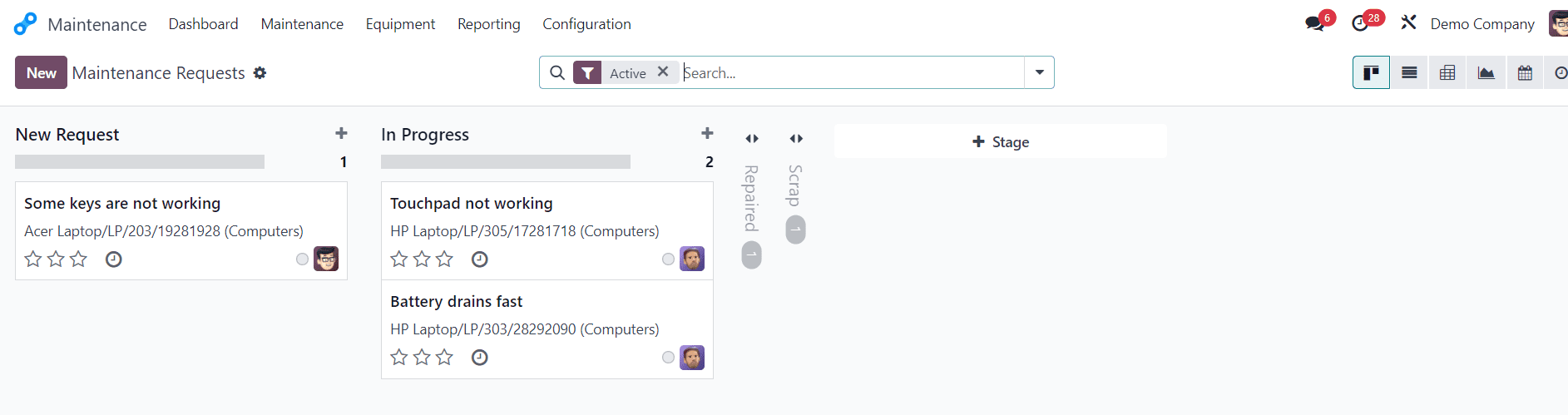
To manually create a maintenance request, click on the "New" button and fill in the requested details such as equipment, maintenance type, description of the issue or task, priority, Scheduled Date, Duration, Company, and any other relevant information.
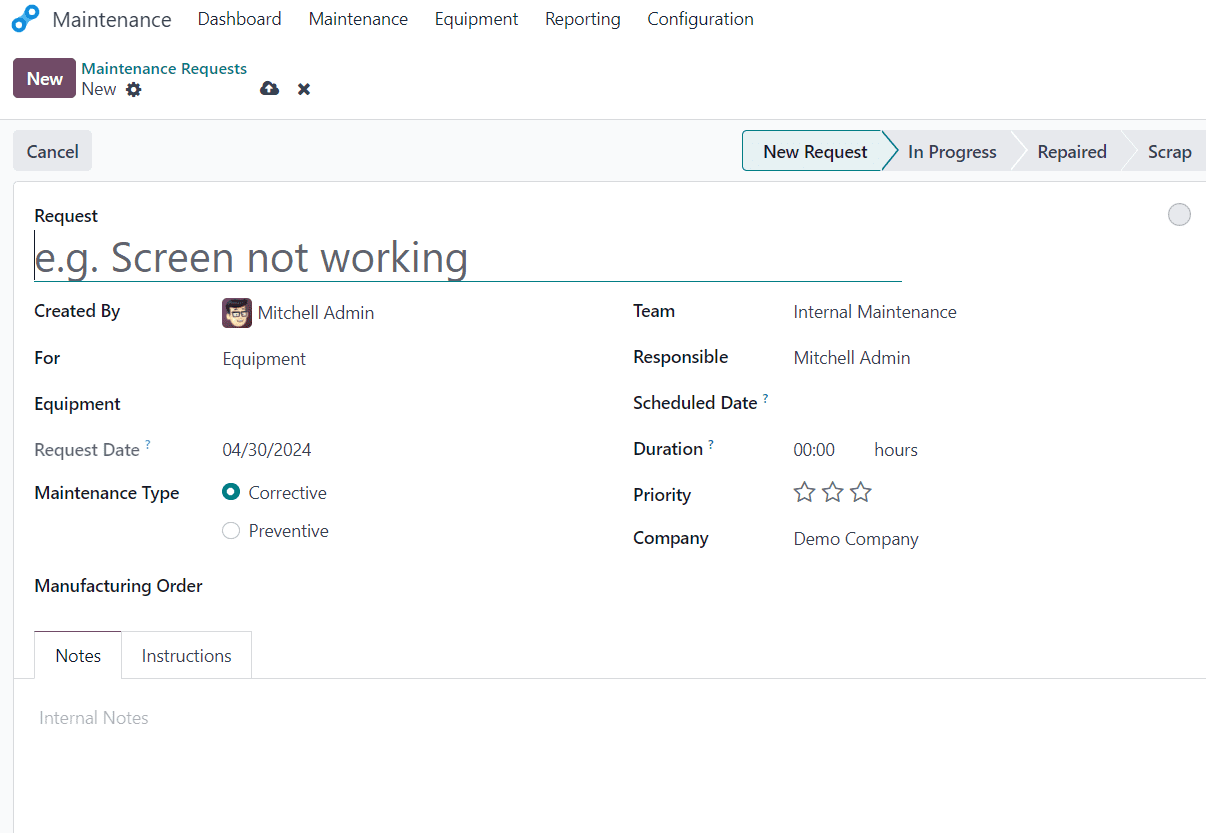
In Odoo, the Maintenance Type is categoryized into Preventive and Corrective. Preventive maintenance involves scheduled tasks aimed at purchasing equipment and prolonging asset lifespan, while Corrective maintenance address issues that have already, focusing on repairing or restoring equipment to normal operation after a failure. In Odoo, you can dynamically change the stage of maintenance requests based on the progress of equipment. In this way, you can general maintenance requests for equipment in Odoo 17.
Effective equipment maintenance is essential for ensuring the smooth operation of production facilities. With Odoo17, businesses can streamline maintenance processes, minimum downtime, and enhance overall operational efficiency. By leveraging the platform's features and best practices, organizations can effectively manage equipment maintenance during production production production production production production production, ultimately driving productivity and profitability. To read more refer to How to Maintain Equipment with Odoo 16 Maintenance App