Quality maintenance is one of the principal objectives of every manufacturing company. The quality of an organization’s products and services has the power to decide its future in the market. Ensuring the quality of each product is very essential to the existence of the company. The customer will never compromise the quality of the product and services they purchase from a company. Many products lost market value only because they failed in satisfying the customers with their quality. The major reason behind the decline in profit is that many business firms are not taking the necessary actions to ensure the quality of their products at every stage of manufacturing and delivery.
The products must be tested and meet the quality standards before delivering them to the market. To do all these actions to keep quality products, companies must have an organized and efficient system to manage the quality checks. Many companies are not doing quality control in the right way and they need the assistance of an efficient quality management system. Odoo offers you the Quality module to organize the quality checks and maintain the quality management at each stage of manufacturing and delivery of the product. You can examine the quality of the product through the various testing processes using the Odoo ERP system.
If the product fails in the quality tests the Quality management system will help you to generate quality alerts that guide you in the actions to improve the quality. The Odoo quality management module is an amazing platform that encompasses all the measurements to ensure good quality in the product being produced in the company. You are allowed to create new quality points, manage the quality plans and monitor the quality controls. It will guarantee a high standard in quality management of each product manufactured by your company.
This blog will give you an insight into how Odoo helps to test the quality of a product.
To implement quality control plans, you need to generate quality control points in the Quality module. These quality control points will help to monitor the quality of your product at various stages of production. You can set the Quality Control points in the Quality module in Odoo.
Before that, to configure the quality check on the products we must enable the ‘Quality’ option in the Manufacturing module. Go to the Manufacturing module, select the Settings option under the Configuration menu and enable the ‘Quality’ button in the Operations tab.
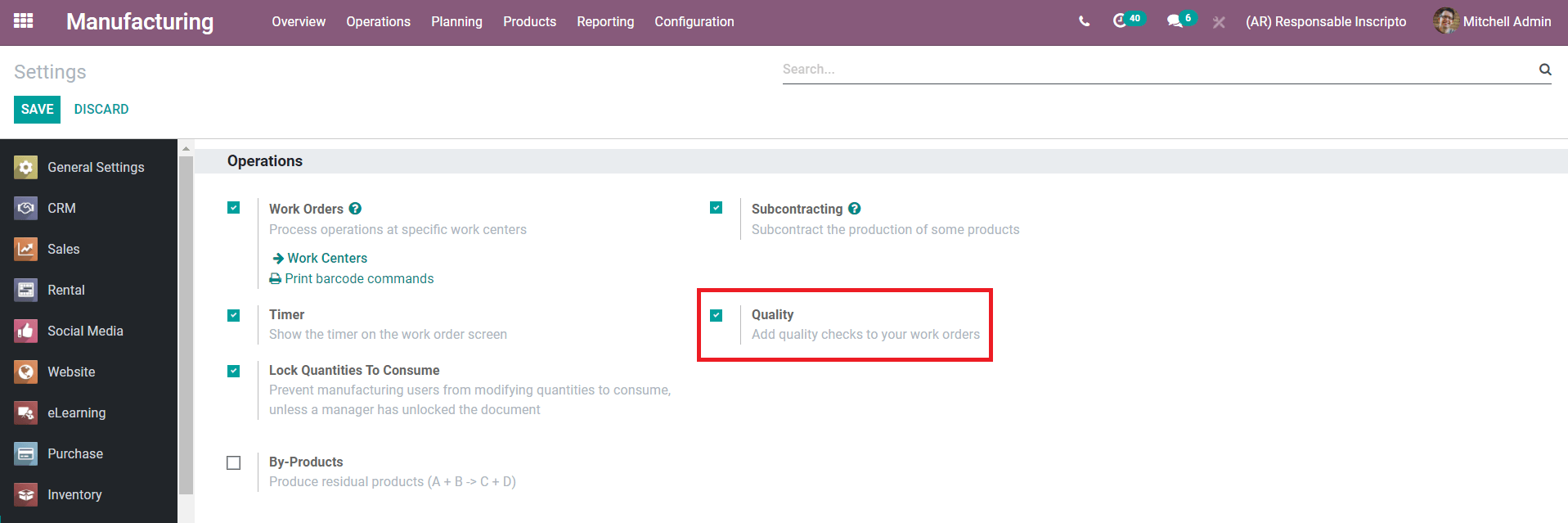
Enable the ‘Work Orders’ also to facilitate the better performance of the quality management.
The quality checkpoint will start to work when the product moves from one stage to another stage. The actions will be taken according to the instructions in the respective Quality point of the product. These points are set in the Routing and Work Centers of the manufacturing module. Let’s take a look at the working of the quality points on the product at different stages of manufacturing.
Create Quality Control Points
Create Quality Points under the Quality Control option in the home dashboard of the Quality module. This quality point is used while implementing the quality checks.
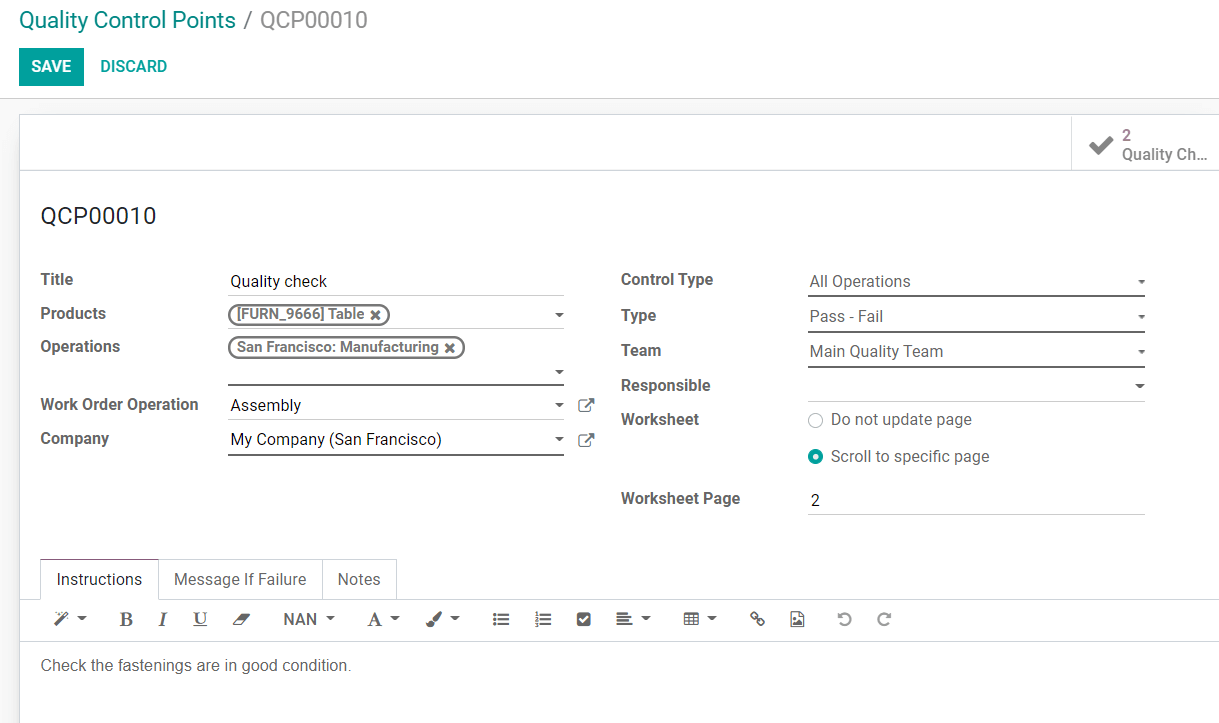
Add Title and select the Product in the given field. The Operation can be specified as to when should be the quality check conducted like at the time of Manufacturing, Delivery Orders, PoS Orders, or the Receipts. Add details about the Work Order Operation, Company, Control Type, Type of Quality Check, Team, Responsible, and Instruction to the Quality Points.
Quality Checks
Create new Quality Checks from the Quality Control menu of the Quality module. The newly created quality Checks can be applied to the products specified.
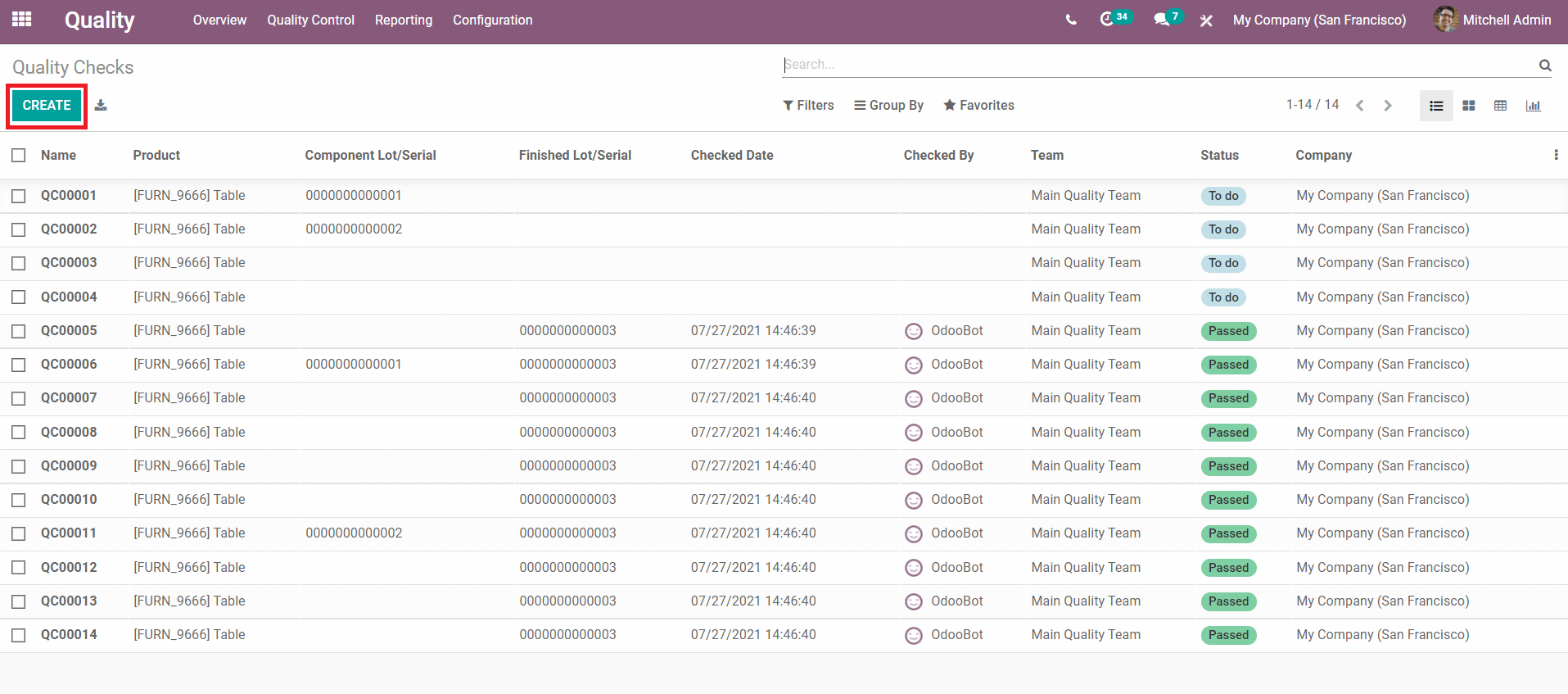
You can see the list of all available quality checks on the screen. The status of the quality test can be understood from the list itself. Choose the ‘Create’ button to create new Quality Checks.
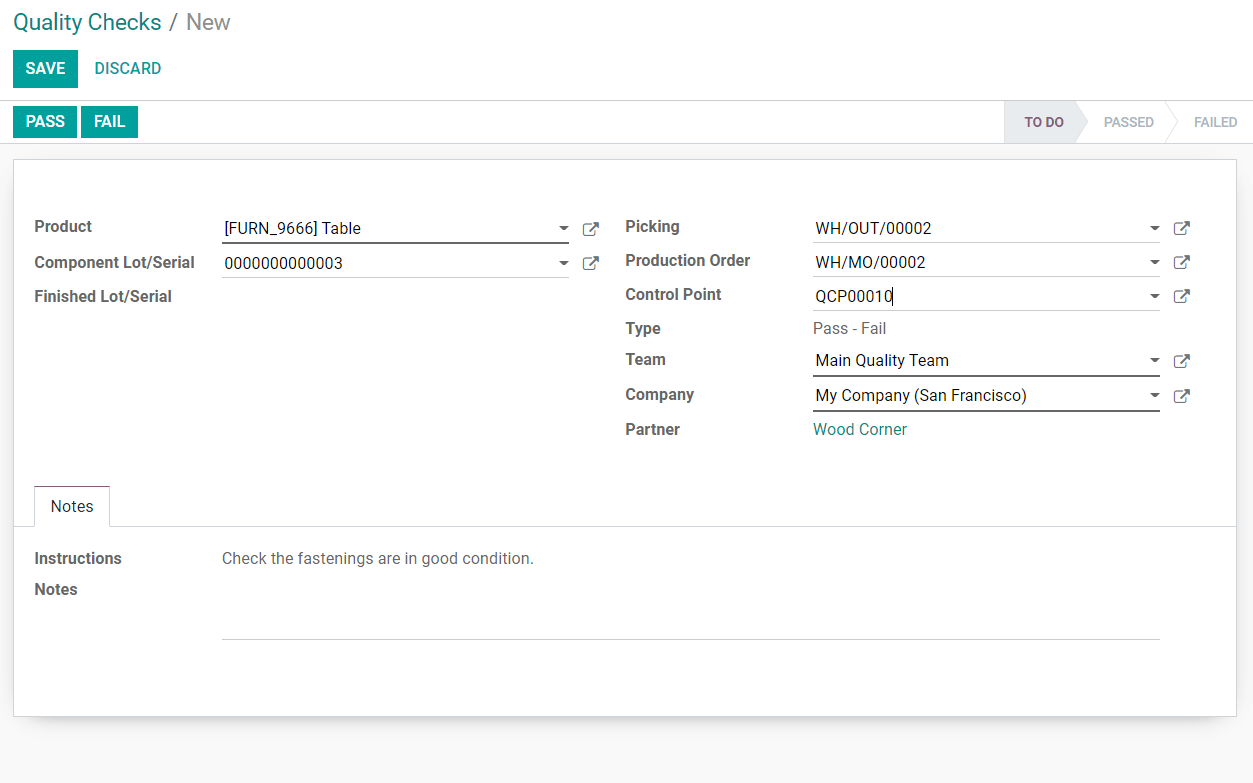
Specify the Product name, Lot/Serial number, Picking, Production Order, Control Order, Type of Quality Checks, Team, Company, and Partner in the given fields. You can select the control point of the specific product that we have created earlier. If you have any instructions to add to the Quality Check, you can add those in the Instructions fields. You can select the type of quality check from the drop-down menu and the methods of quality check will change according to the type you have selected.
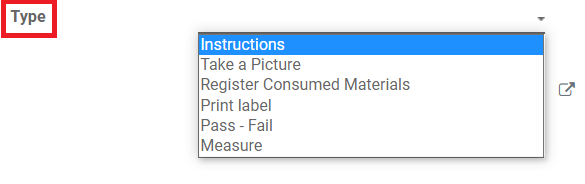
Product Quality Checking in Manufacturing
Odoo will enable you to use the Quality Checks and Points created in the Quality module to test the quality of a product in Manufacturing. Odoo integrates these actions with the Manufacturing module so that you can easily check the quality of the product from the Manufacturing module itself.
When a manufacturing order is confirmed, you will get the option to check the quality of the selected product.
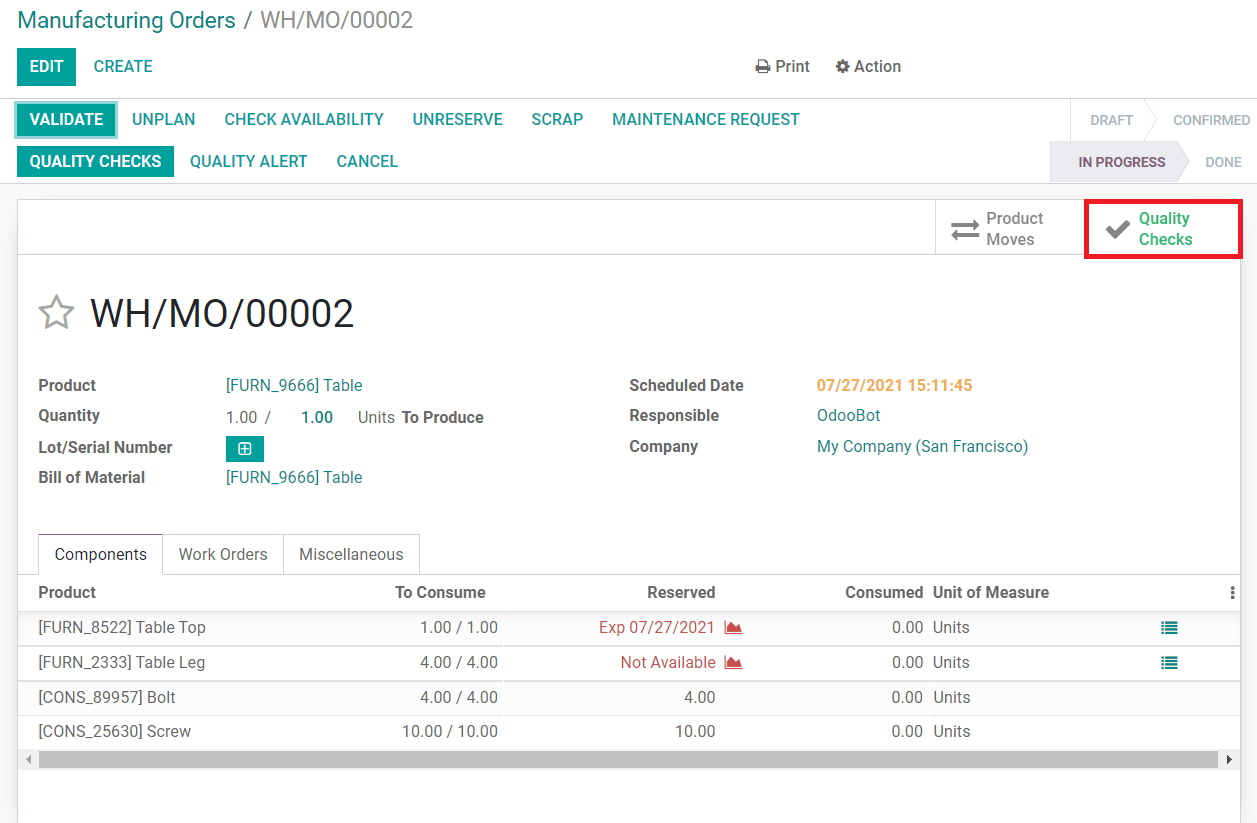
Click the ‘Quality Check’ button to proceed with the actions. You will be directed to a window containing all available quality checks in the database. You can select the most appropriate Quality Check from the list or you can create a new one for this product using the ‘Create’ button on the same screen.
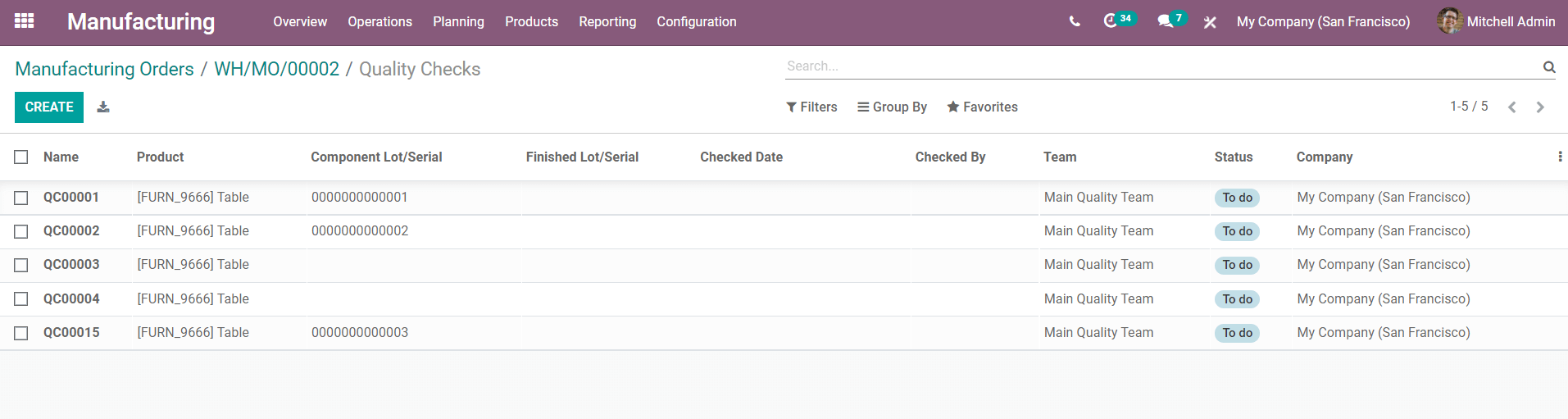
The details about the selected Quality Check will appear and you can mark it as Pass or Fail according to the quality of the product. This action will be different for different quality checks in respect of the type you have selected while creating a new Quality Check.
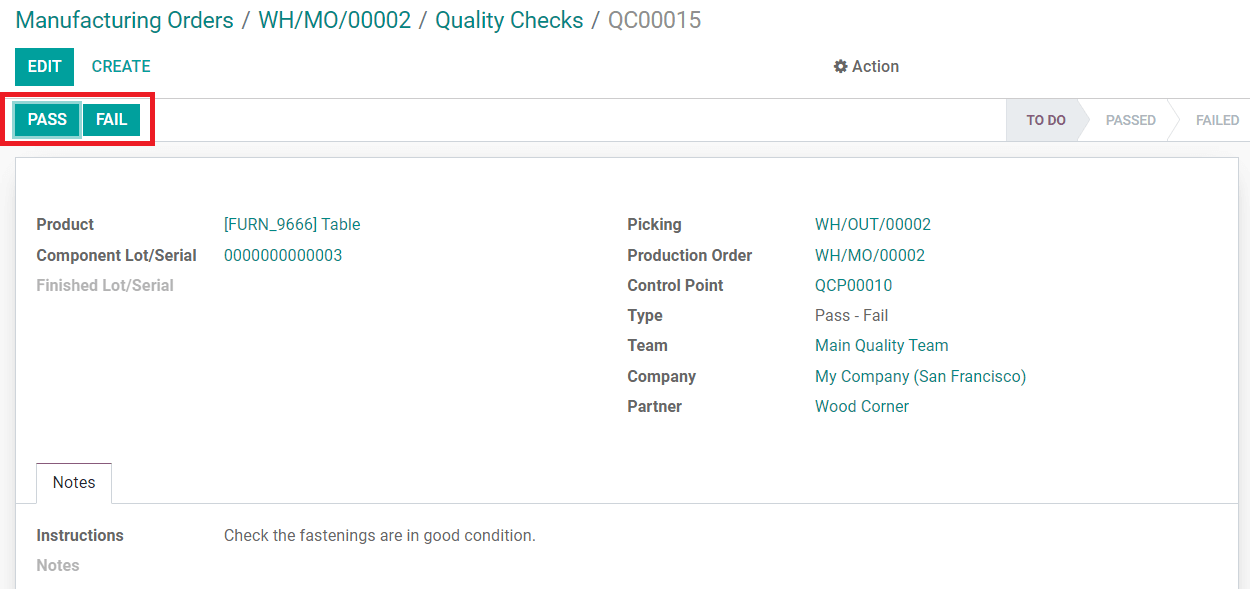
If the quality of the product is satisfying and no other major defect is detected then you can mark it as Pass. The status of the Quality Check of this particular product can be seen as ‘Passed’ in the list.
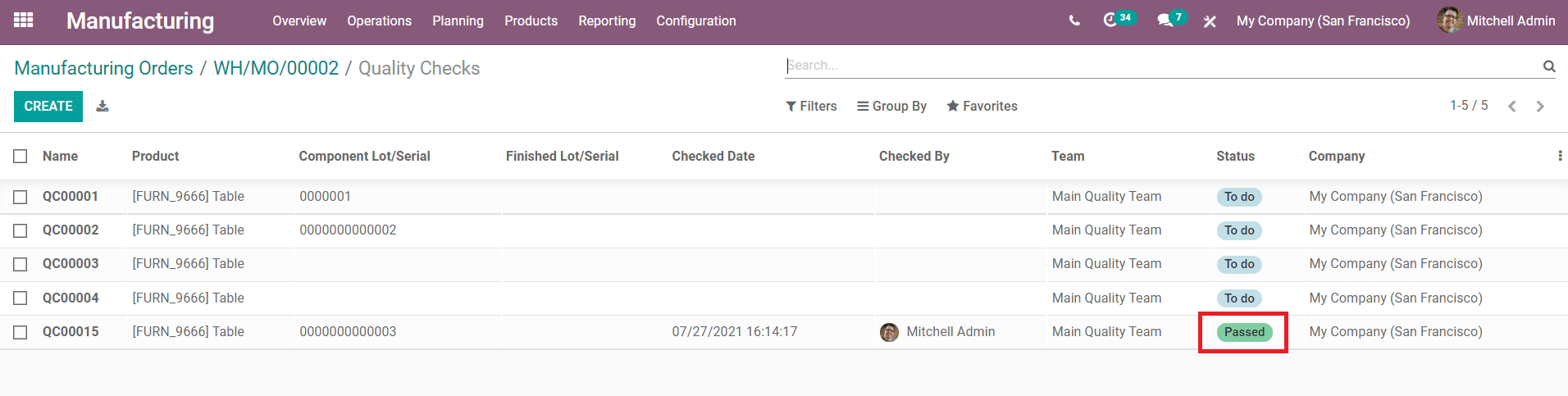
You can create Quality Alerts if the product fails in the quality tests. You can see the ‘Quality Alert’ option in the manufacturing order of the product.
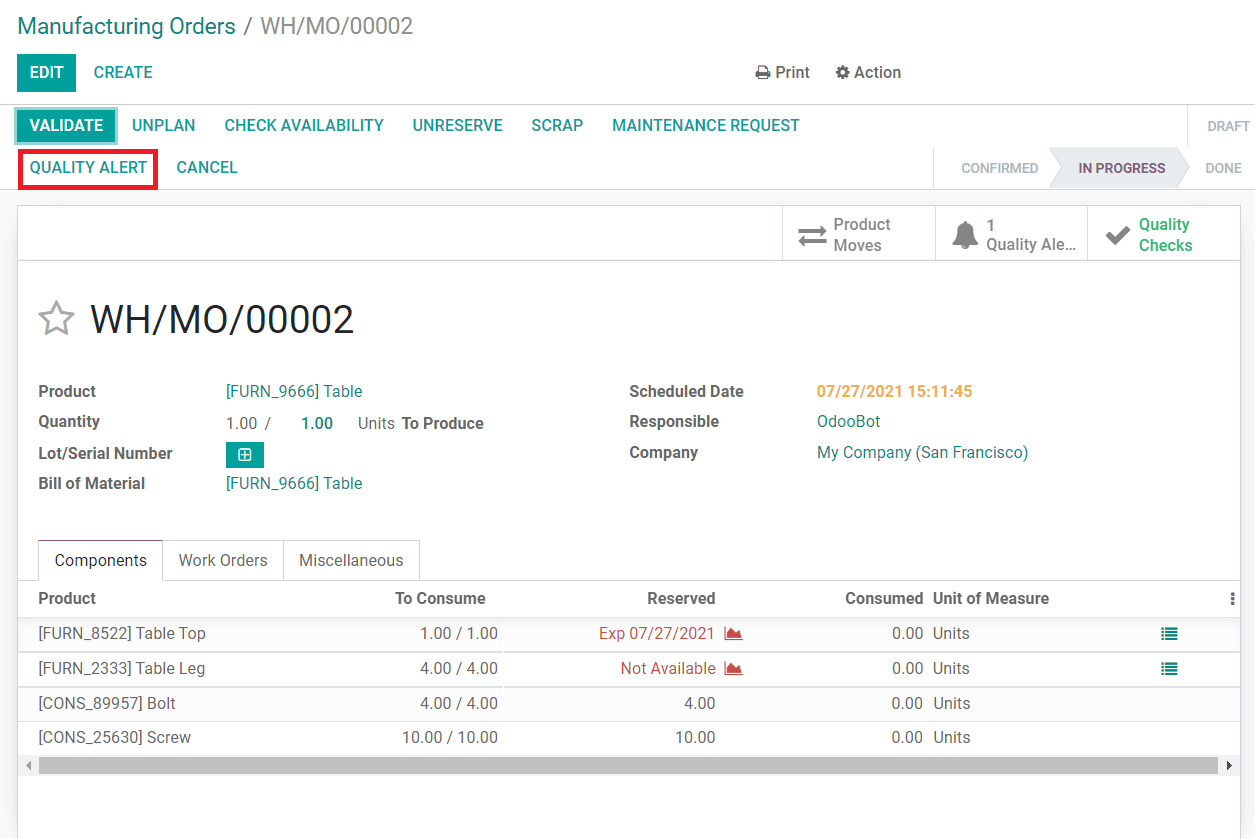
Click the ‘Quality Alert’ button and create a new alert about the quality of the product as shown below.
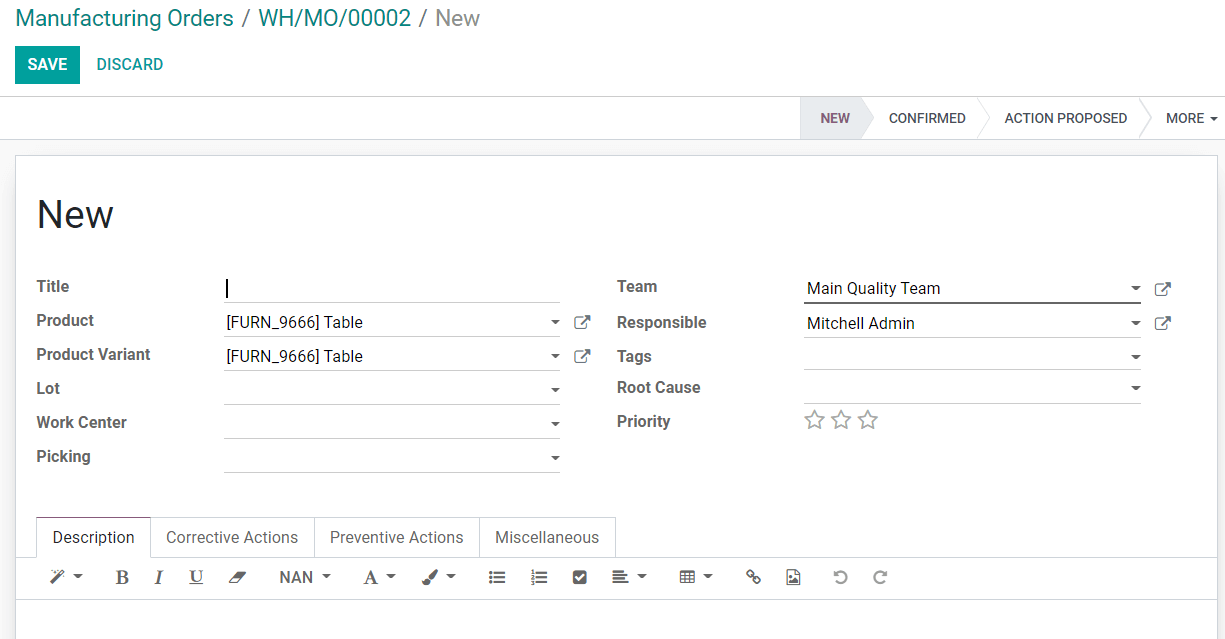
Give Title to the Quality Alert. The Product and its Variant can be seen as already mentioned in the respective fields. You have to mention the details about Lot, Work Center, Picking and Tags in the form. Mention the reason for the quality issue in the Root Cause field.
Give a description of the issue in the product in the Description tab. In Corrective Actions and Preventive Actions, you are allowed to add necessary actions to take on the product to correct the issue and prevent the issue from happening again.