Every manufacturing industry may not be interested in manufacturing every single item required for the industry. Instead, they may outsource some of the works and focus more on assembling the particles purchased from the outsourced firms. Such operations are called sub-contracting. Though the term sub-contracting sounds simple, it is not so when it comes to reality. It involves a lot of procedures if the process is handled manually. However, when it comes to outsourcing, it can be handled efficiently with the support of an ERP solution.
Odoo, with a dedicated module for manufacturing, offers the complete solution for subcontracting worries. This can be used in simple steps.
For making use of the sub-contracting feature of Odoo, you have to first install Odoo Manufacturing.
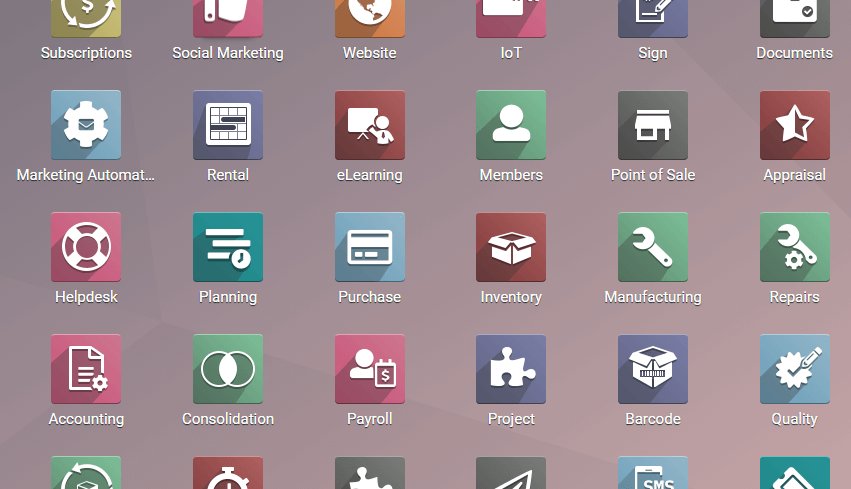
Odoo manufacturing will enable the user to manage the inventory of raw materials at the subcontractor’s place, it also helps to shop raw materials for the subcontractors taking into account the forecast. You can also make use of the ERP to keep track of all manufacturing operations performed at the location of the sub-contractor. It will help you to control the quality of incoming goods. It also enables you to Control subcontractors’ bills.
Now let us take a look at the configuration of sub-contracting in Odoo.
Go to Manufacturing> Configuration> Settings
Here, you can find the operations tab under which there is a subcontracting option. Enable this box to make use of the subcontracting feature.
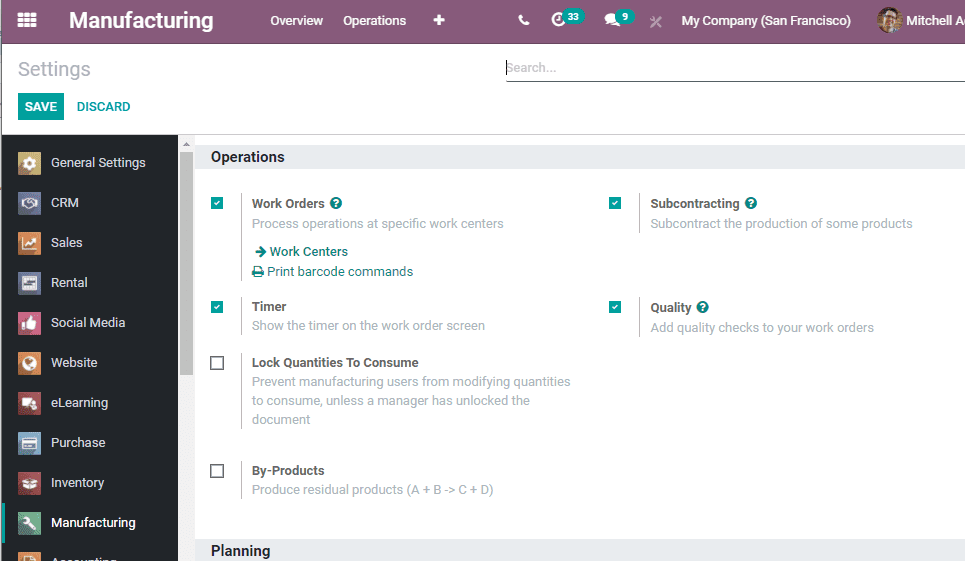
Now, go to Manufacturing -> Products -> Bill of materials and we can find subcontracting enabled at the Bill of Materials.
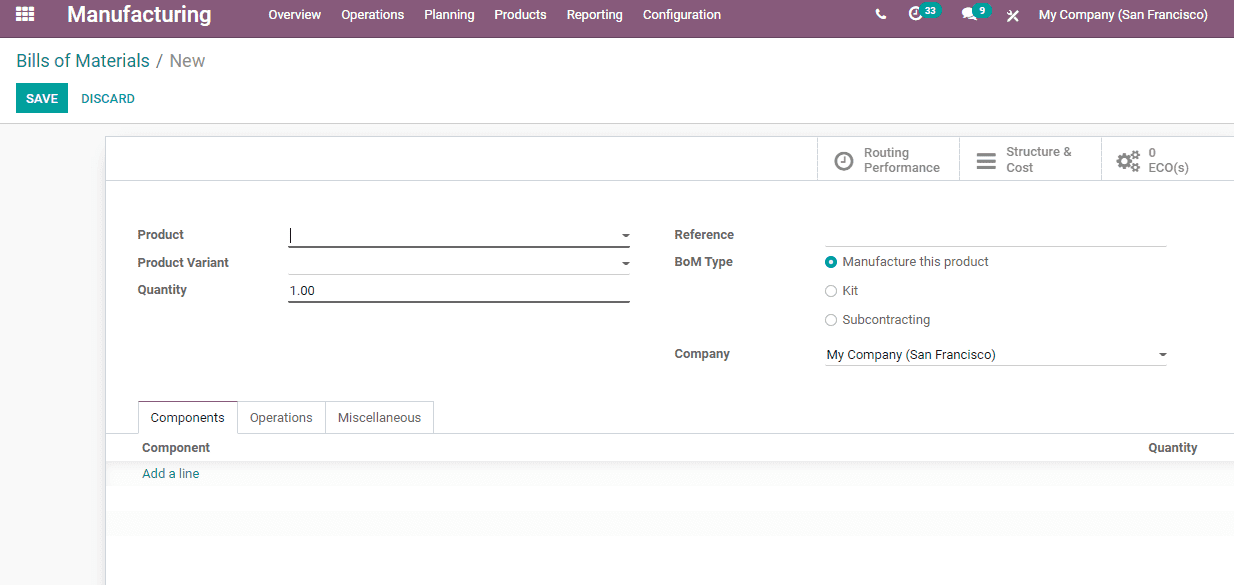
Now you can enable the subcontract option and select the subcontractor or subcontractors from the list.
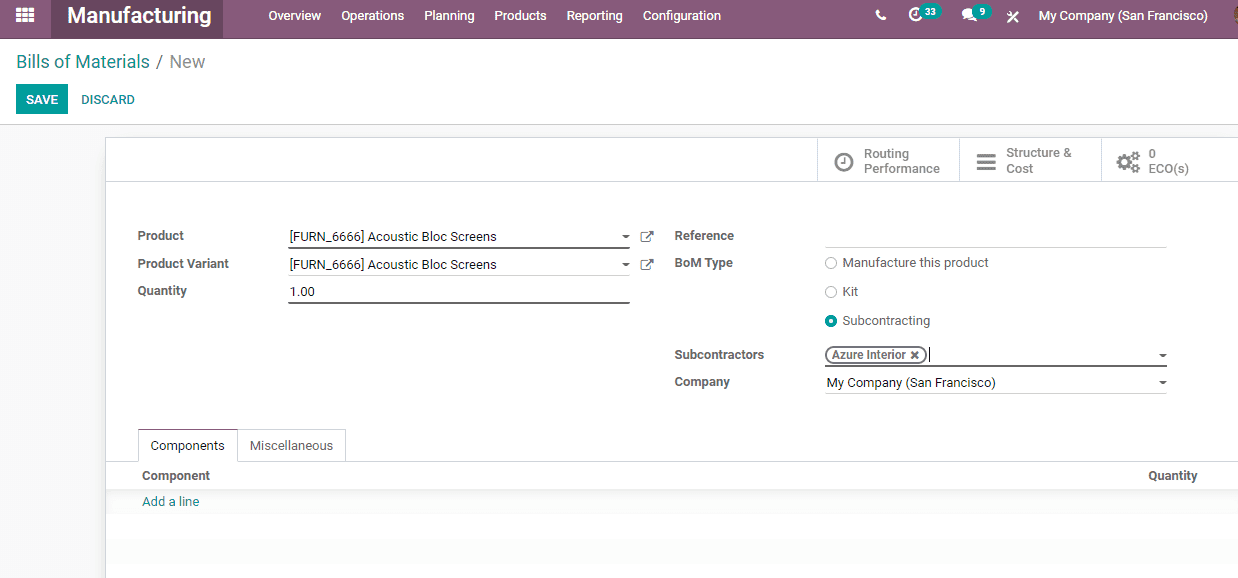
A user can list the raw materials or components for the subcontractors by adding new lines under the components tab. The user can register the components for completing the costing process accurately.
Here, the user can also be able to add the details of the product including the product quantity required. This helps the subcontractor identify the exact number of products that you want.
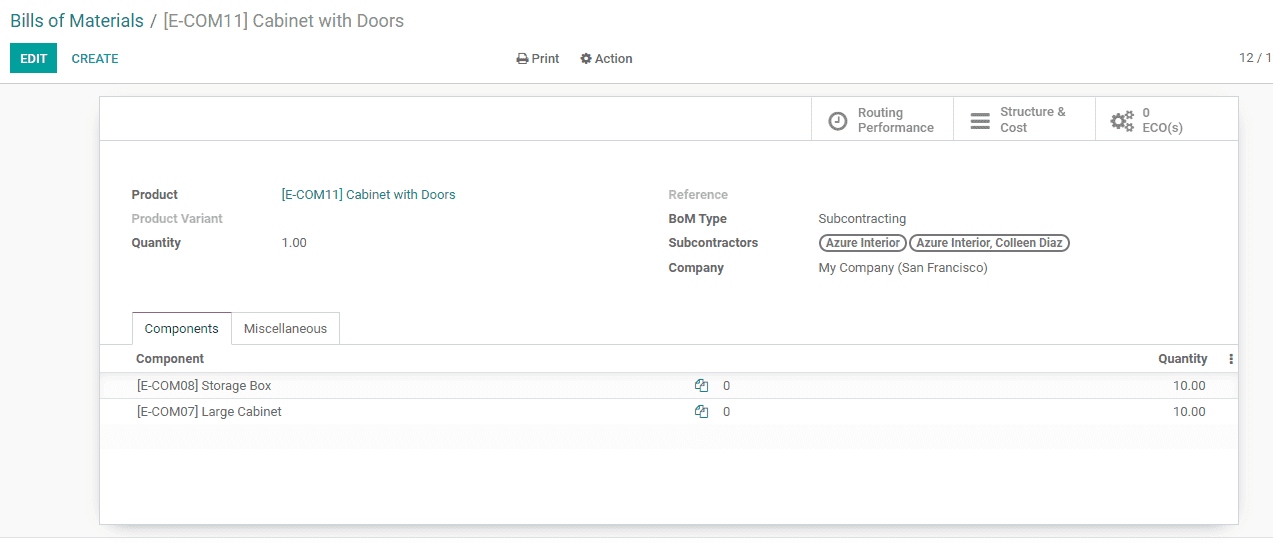
To buy the products back from the subcontractor you have to prepare a purchase order. For this install Purchase App and then generate a Purchase order to the vendor who has been identified as the subcontractor in the BoM.
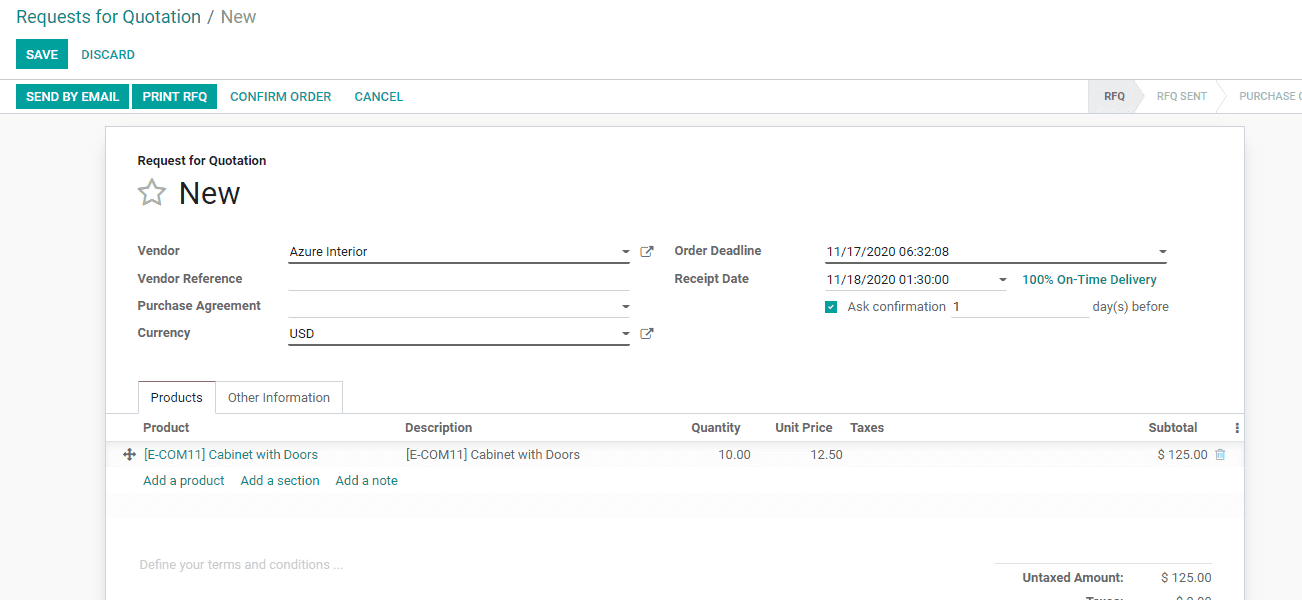
Complete all procedures for purchasing a product and then validate the purchase order
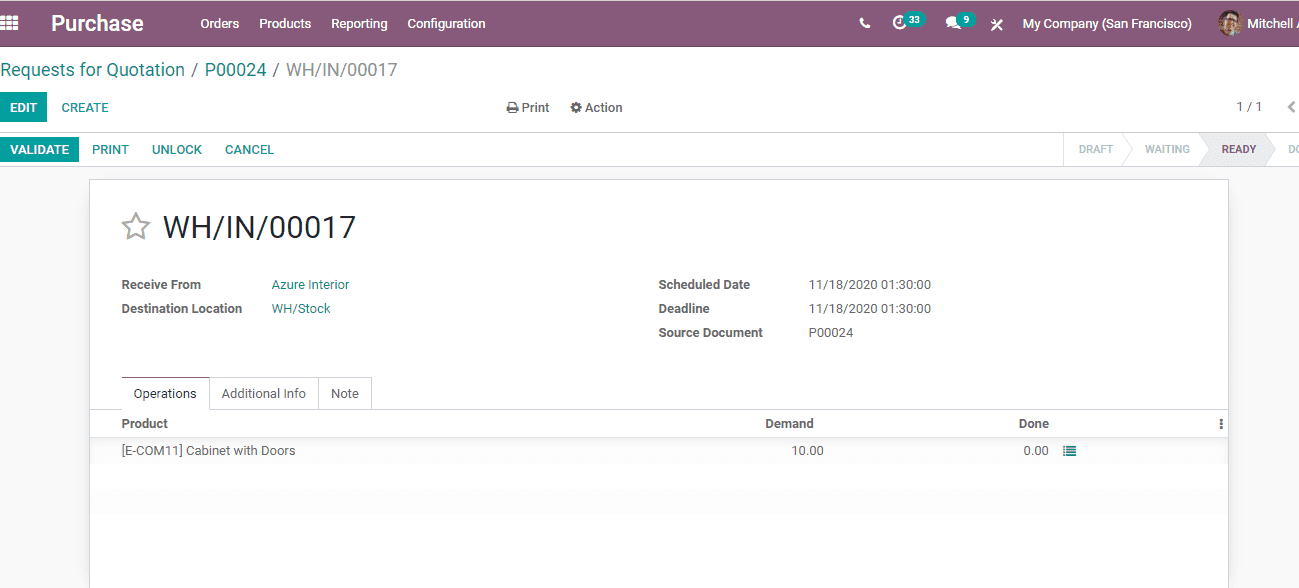
The number of products delivered can be billed. If the products are not purchased together it can be collected multiple times.
Odoo helps the user to perform all activities involved in subcontracting automatically. It also supports your activities, if you want manual operations also.
Inventory Valuation
When you are sub-contracting a product, the price of the product is decided based on the price of the raw materials.
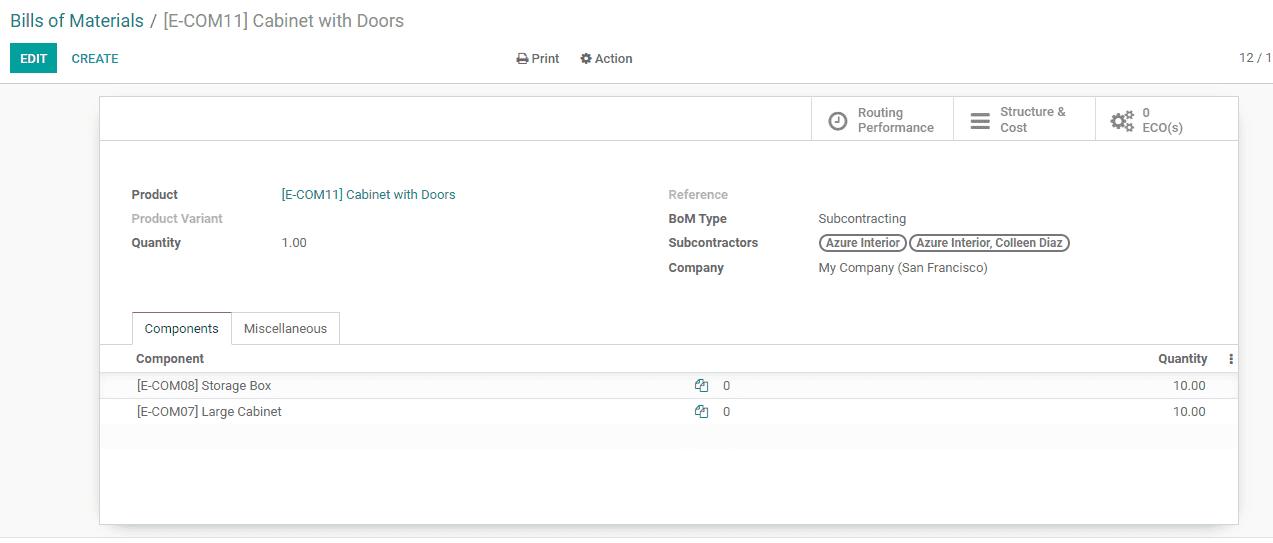
In this case, there are two components we can call them A and B. The price of the finished product will be the price of A + Price of B+ the service charge levied by the subcontractor. In case all the components are provided by your company to the subcontractor, the total cost of the product will be prepared purely based on the service charge. In case the subcontractor is sourcing some of the components directly, the price of these products will be added to the service charge to calculate the price of the product.
Traceability
Traceability can be assured by using a serial or lot number while preparing the receipt. This can help to trace the product. The serial number can be used for tracing and auditing purposes.
Automate Replenishment of Subcontractors
If you want to improve the management of resupply of your subcontractor, you can activate Multi-locations in Inventory. For this go to Inventory >Configuration> locations.
Here, the subcontractor location can be traced.
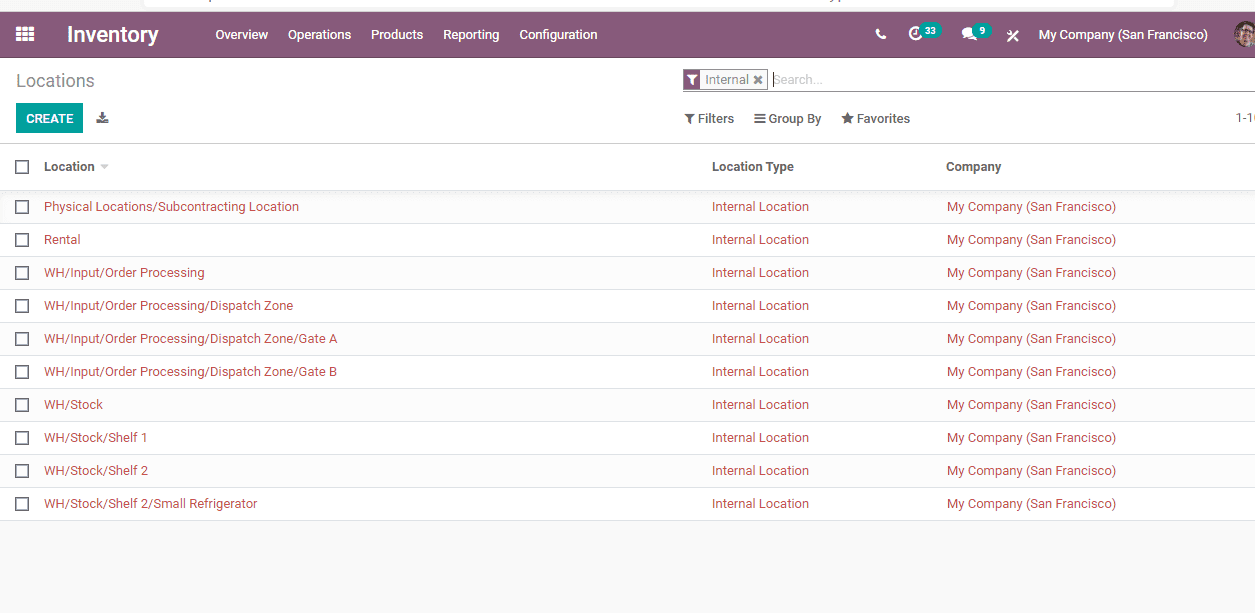
With this feature, the user can send components to the subcontractor location to ensure supply.
Replenishment from the warehouse
A user can easily resupply components to a subcontractor. For this create delivery orders and select the address of the subcontractor as the delivery address.
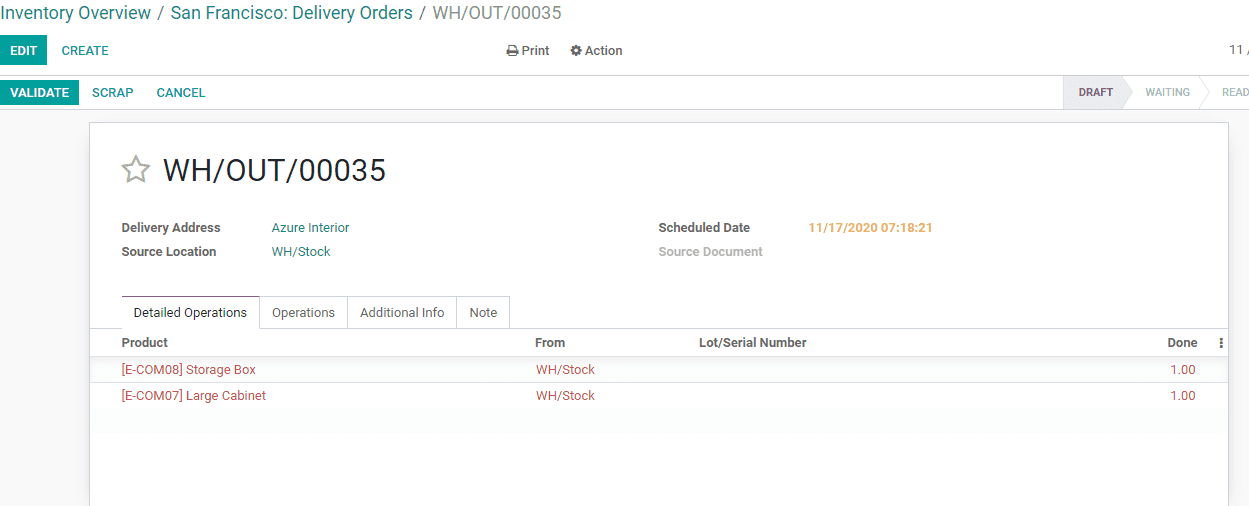
With Odoo we can automate subcontractors’ replenishment propositions. This can be done in two different ways.
1. Using Reordering rules
2. Replenish on order flow.
Here, you can define a reordering rule on the subcontracting location. For this, you have to set a minimum and maximum inventory level. On doing this a delivery order gets created the reordering rule is triggered.
If you are using the Pull flow the demand for the finished product is taken into account to replenish the subcontractor.

Replenishment from another supplier
If the manufacturer is purchasing components from other vendors to supply the items to the subcontractor, the user can directly ask the vendor to deliver the product to the subcontractor. For this enable the Drop Shipping feature in the Purchase module.
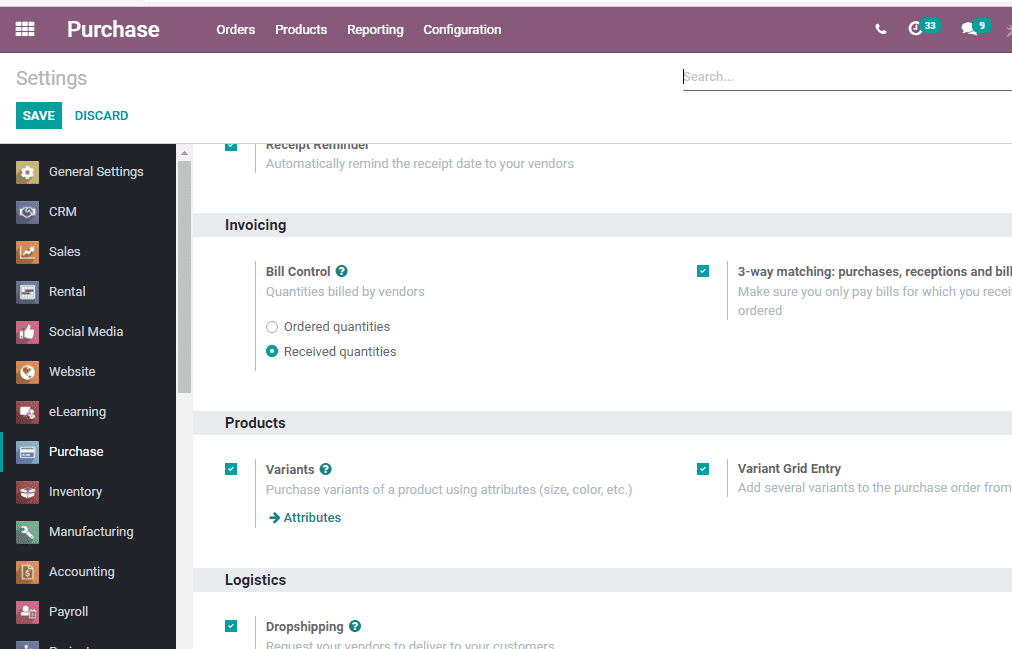
Now you can select the Dropship option while purchasing. Also, give the address of the subcontractor for shipping.
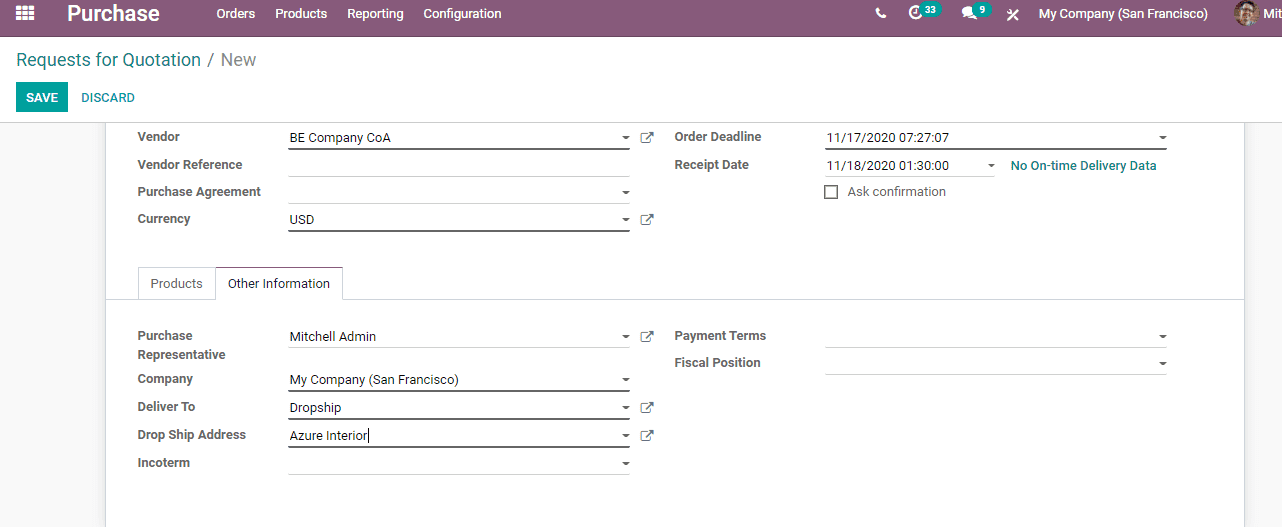
Quality Control
It is also possible to check the quality of the products manufactured by the sub-contractor using the Odoo Quality App. Normally, a quality check is performed at the manufacturing stage. But in this case, as the manufacturing is done by an outside firm, the check can be done when the product is received.
First, install a quality App and create a control point on the reception of the subcontracted product.

This is how Odoo enables comprehensive management of subcontracting. To read more about the importance of Odoo Manufacturing V14, refer to our industry page
Odoo Manufacturing V14