You can build up a series of rules in the Odoo Inventory module to ensure that you never run out of stock. Using the reordering rules, Odoo will make an effort to keep your inventory of products at least somewhat full. Let's examine how Odoo 17 handles this feature. You can choose a storable product from your inventory module for this.
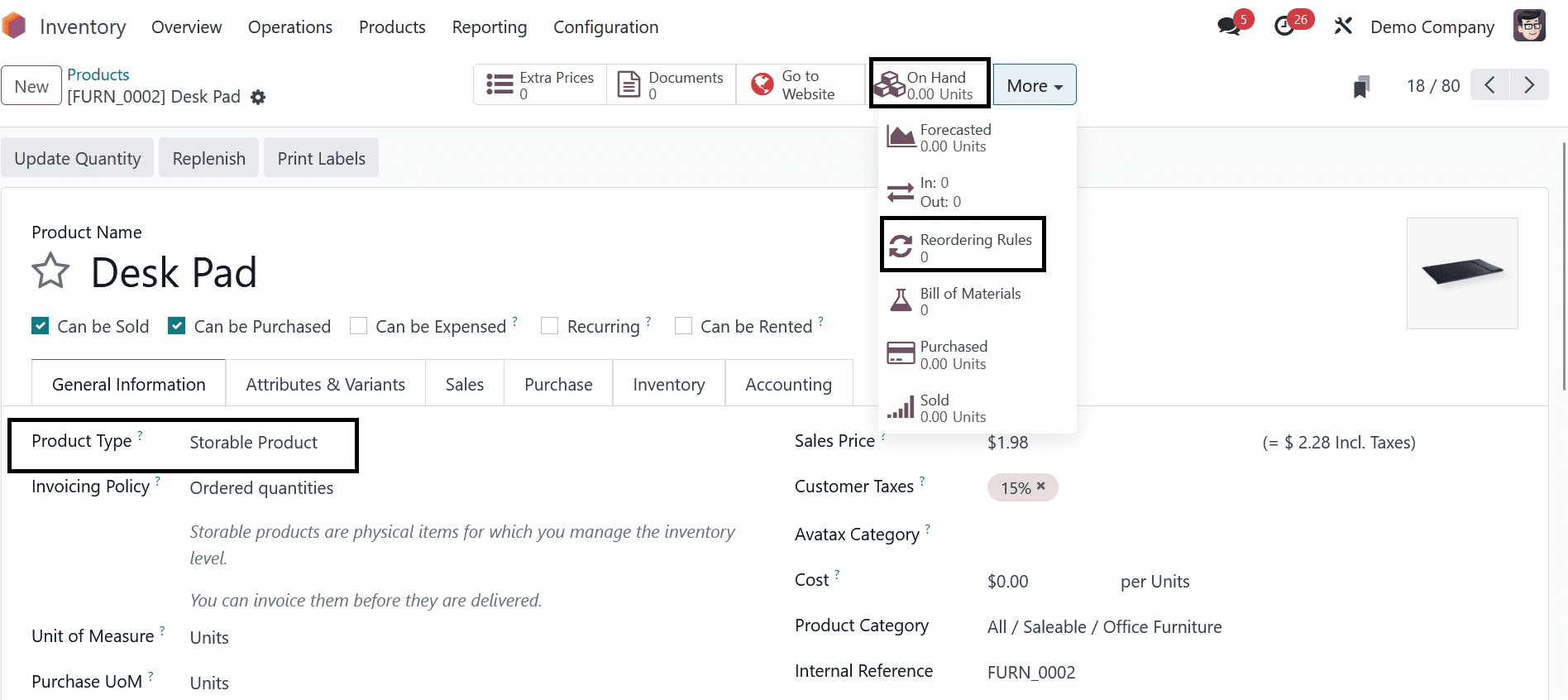
As you can see, the unit that is now in use is "0." In the screenshot above, you can set up reordering rules for this product by selecting the Reordering Rules smart button. This will open a new window for you. In order to have Odoo automatically generate requests for quotations or confirmed manufacturing orders to replenish your stock, you can specify a minimum stock rule here.
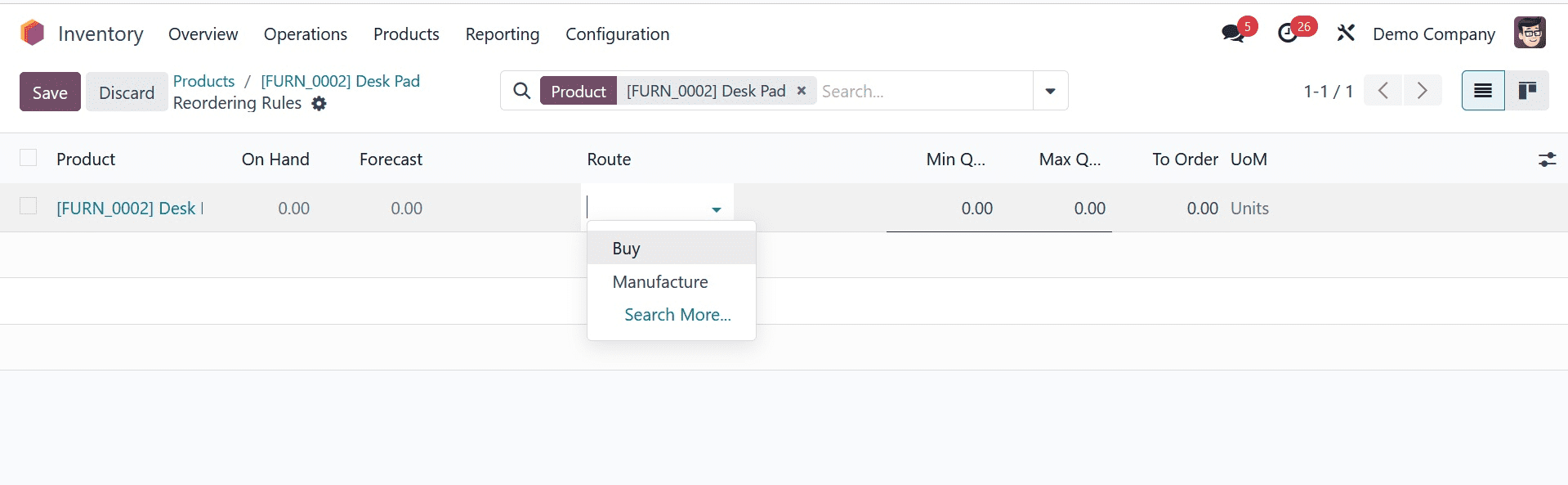
As seen in the screenshot above, as soon as you click the Create button, the name of the product, location, quantity on hand, and forecast details are automatically displayed. You can specify the path to reorder the product in the Preferred Path area. It can be Buy, Manufacture, Resupply/Subcontractor on Order, or Replenish on Order. In this case, we decided to buy the preferred way. In the appropriate field, mention the vendor's name.
The Min Quantity box allows you to choose the lowest amount of the product that has to be kept in stock. In order to replace the stock quantity, Odoo will automatically issue a purchase order to the relevant vendor when the product quantity falls below the specified minimum quantity. The maximum amount of the commodity kept in stock is known as the maximum quantity. The smallest amount that ought to be bought from a merchant is known as To Order. This implies that the quantity we provide in the purchase order will consistently be greater than the quantity to be ordered.
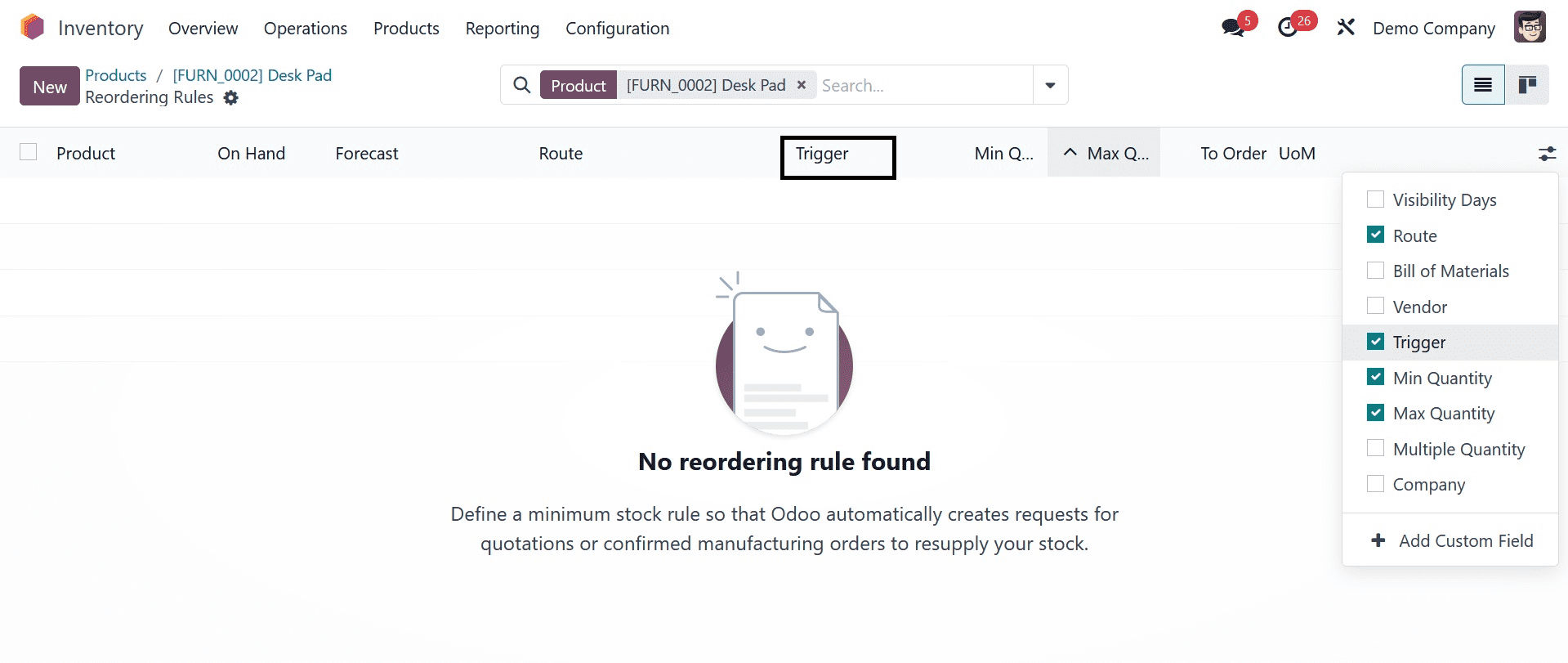
By turning on the Trigger field from the additional fields, as seen in the above image, you may add it to the list view. The reordering rules can be applied both automatically and manually. To initiate the process manually, use the Run Scheduler function from the Operations menu after setting the trigger to Manual.
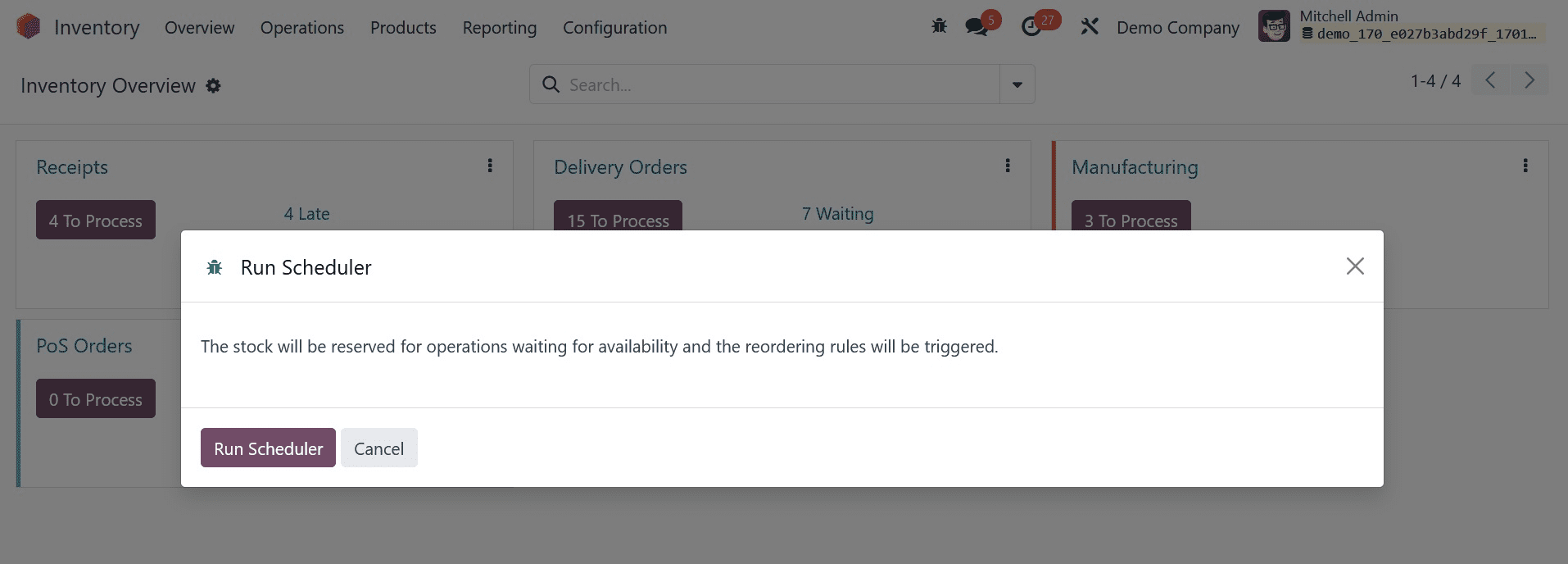
By selecting the Run Schedule option, the stock will be reordered and held for operations while it awaits availability.
You can locate the order to replenish the product by looking at the Replenishment menu.
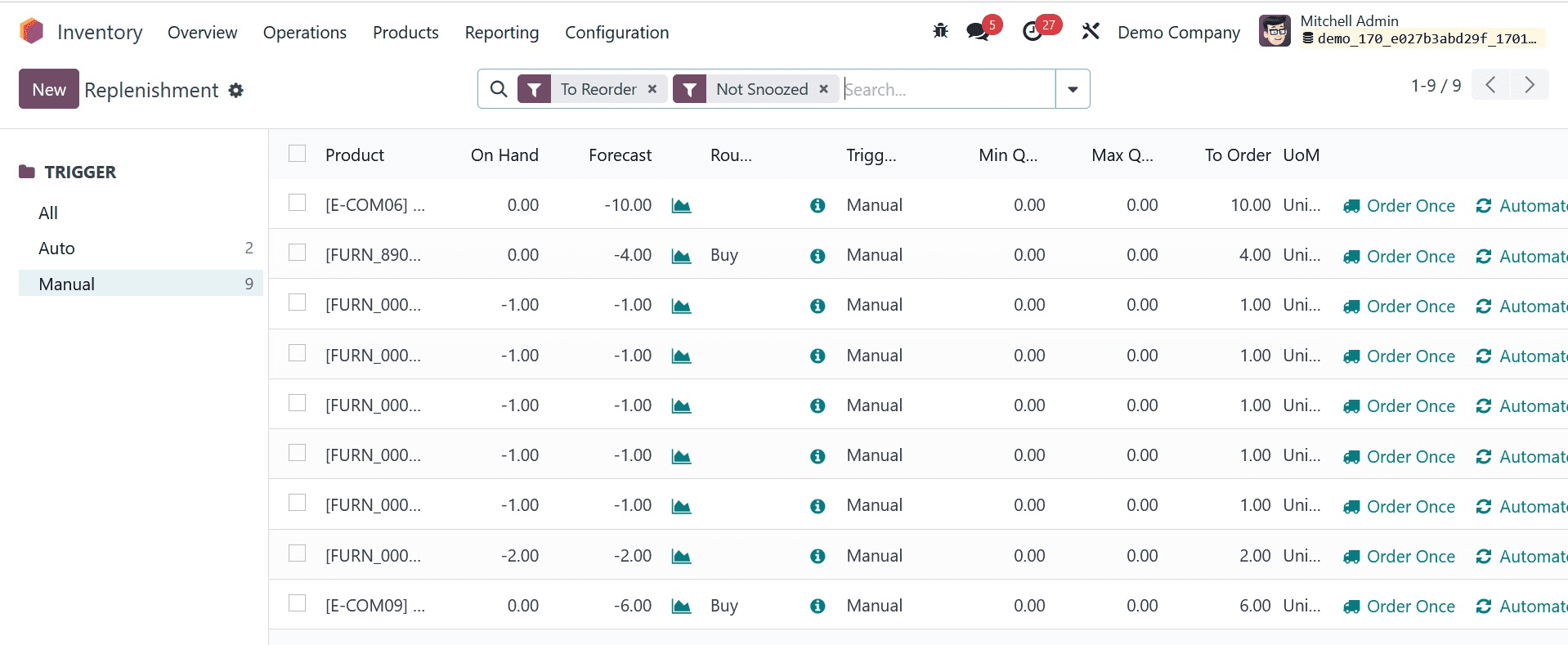
An RFQ will be generated and sent to the relevant vendor upon clicking the Order Once button. The product's request for quotes (RFQ) is shown in the Purchase module, as seen below.
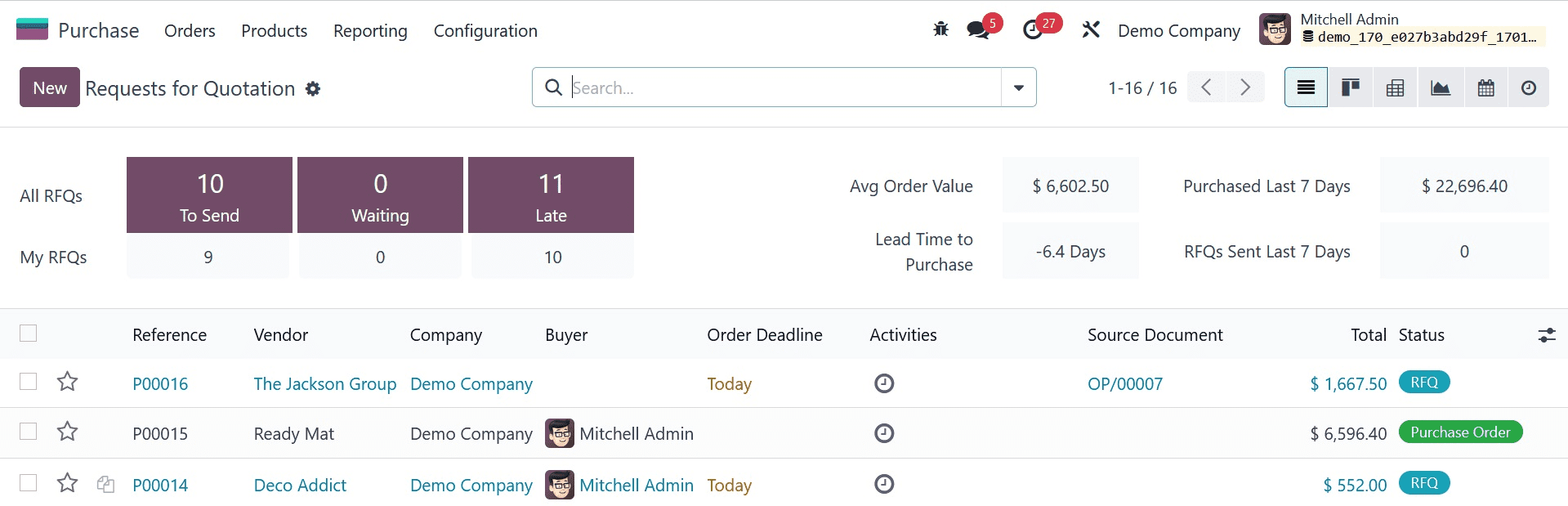
The Odoo Purchase module allows you to verify the Purchase Order and Receive the product.
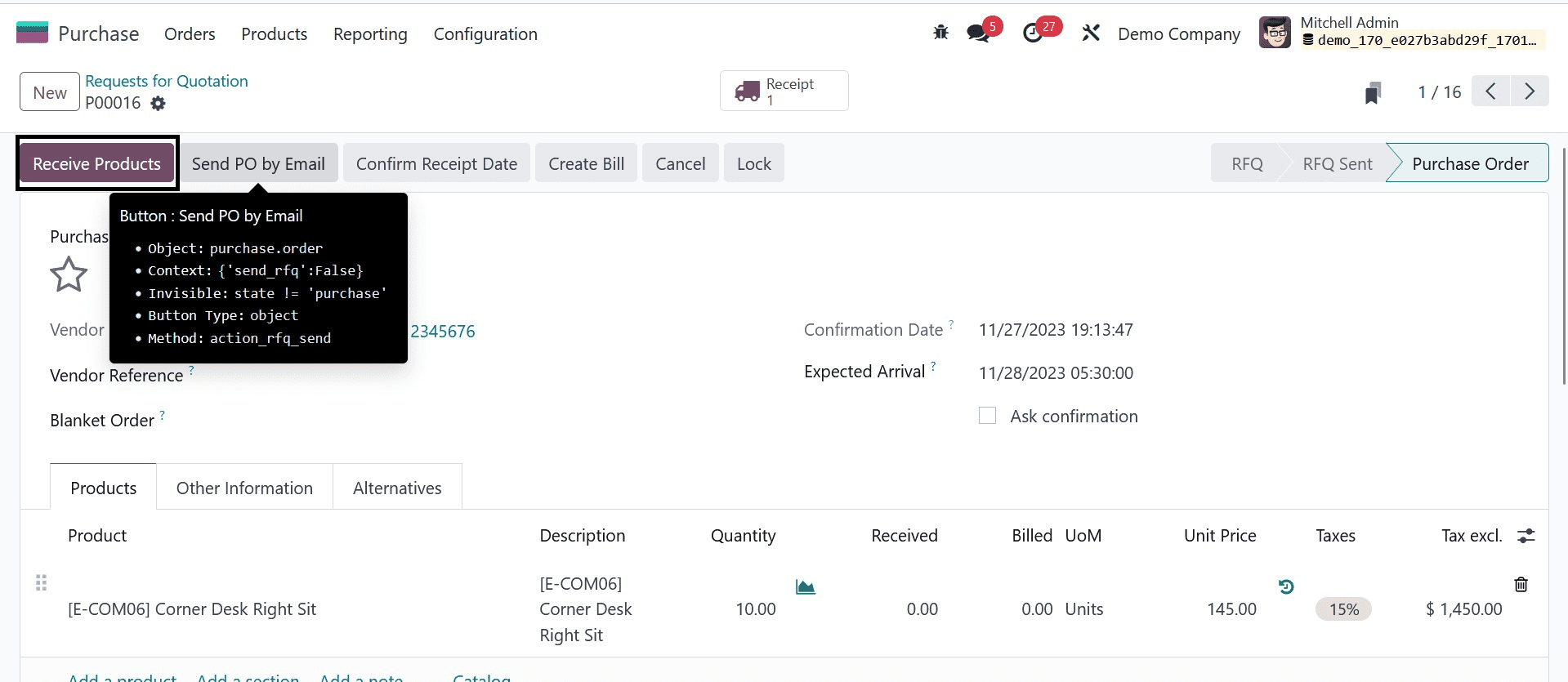
To add the goods to your inventory, click the Receive goods button.
You may see that the quantity on hand has changed in accordance with the reordering rule when you examine the product detail form.
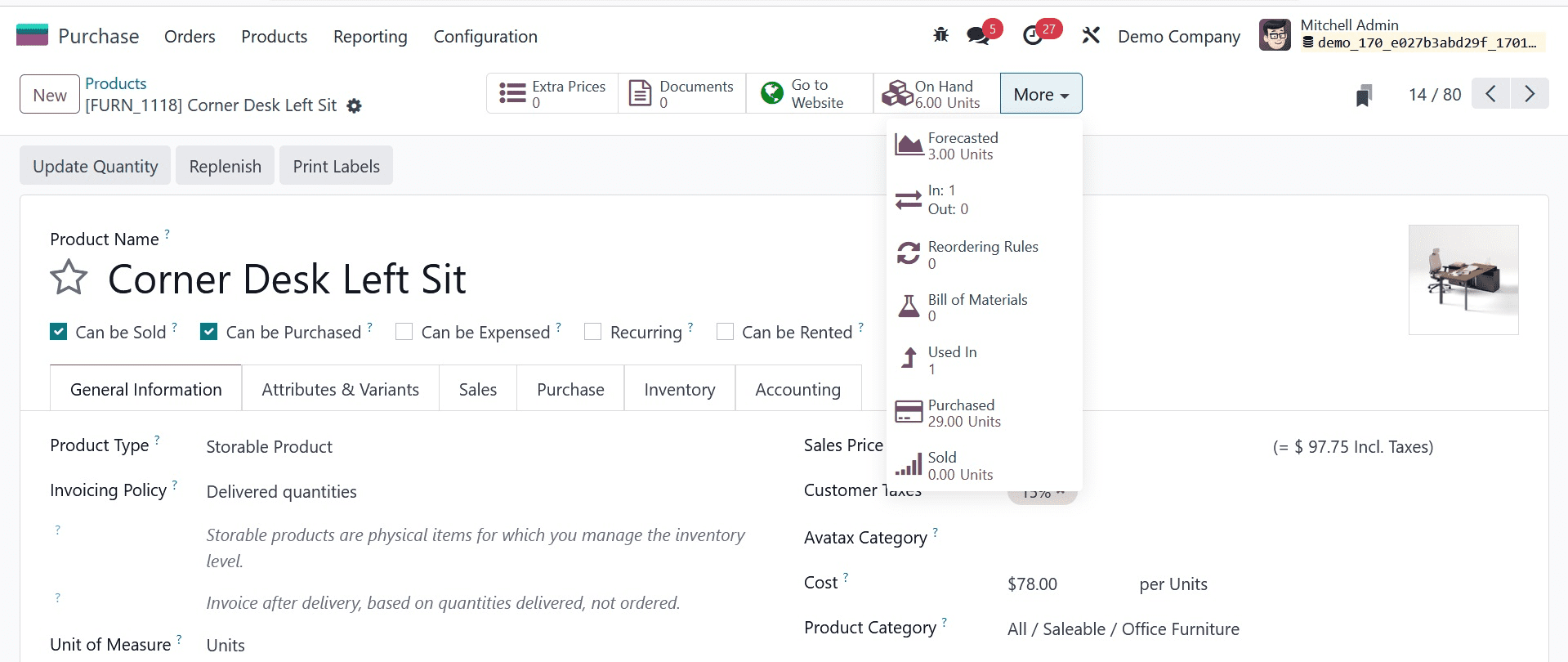
To handle all reordering rules in one location, select the Reordering Rules option found in the Inventory module's Configuration menu.
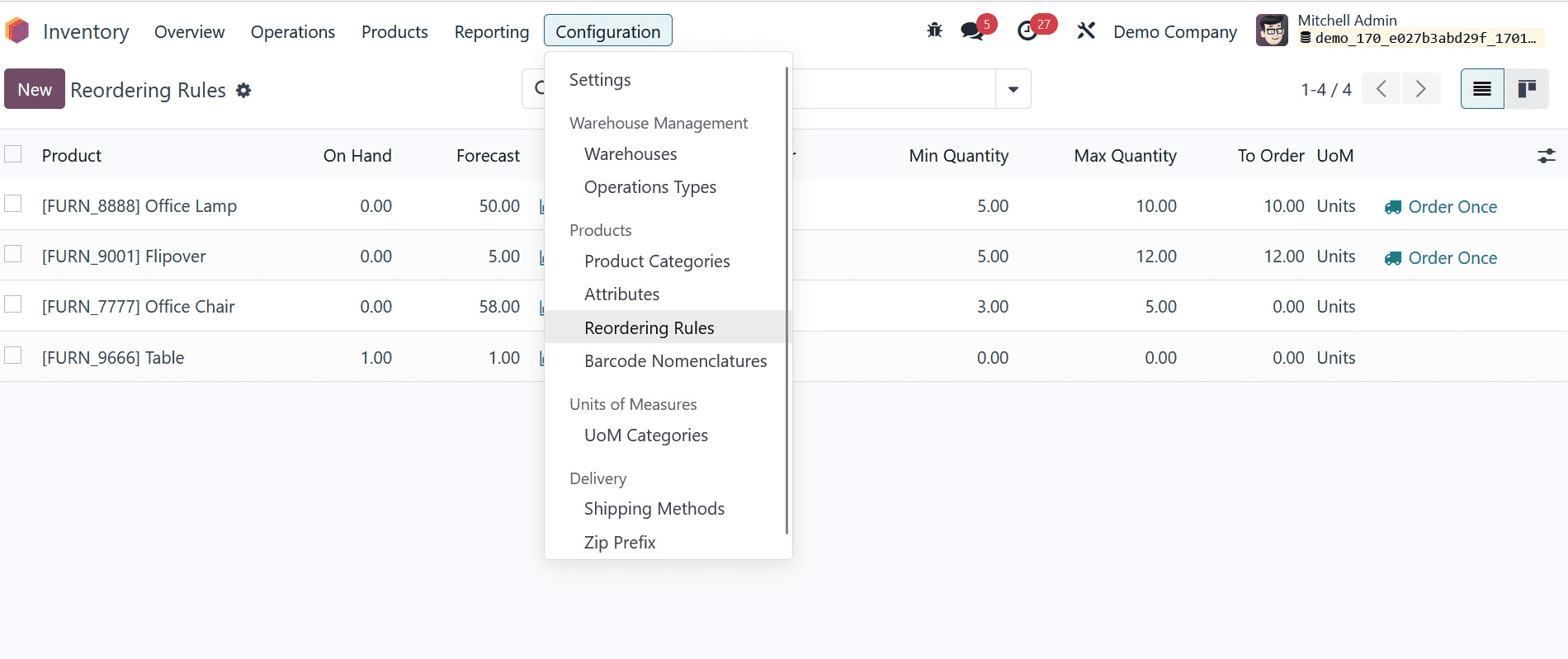
Using the New button, you may immediately from this window create Reordering Rules for products. And that's all about reordering rules in odoo 17 Inventory.