The maintenance module can be considered an essential tool for improving your business’s product and machinery management. The maintenance module can help you improve the health of machines and improve their productivity.
Ensuring the health of the machinery can help you plan and use the machines for productivity. It is easy to set up and use the module with your business and machinery. The manufacturing industry is a significant industry that involves the operation of many machines.
Machinery maintenance plays a huge role in the company. Maintenance ensures the proper 'health' of the devices and improves their life cycle. Instead of wasting time on unwanted mechanical errors and machine failure, you can ensure uninterrupted working at your work centers. Odoo 14 Maintenance module is the best choice to manage all maintenance-related worries.
This blog will give you a complete insight on how to request maintenance and manage them with the Odoo 15 maintenance module.
Odoo 15 Maintenance Module provides a dashboard that gives you the details of internal maintenance activities. It offers an easy-to-manage maintenance calendar and Kanban views of the activities. It offers you drag and drop facilities. The timely maintenance work gives you the best support for the effective functioning of the instruments. It also allows the different wings to speed up the processing of maintenance requests.
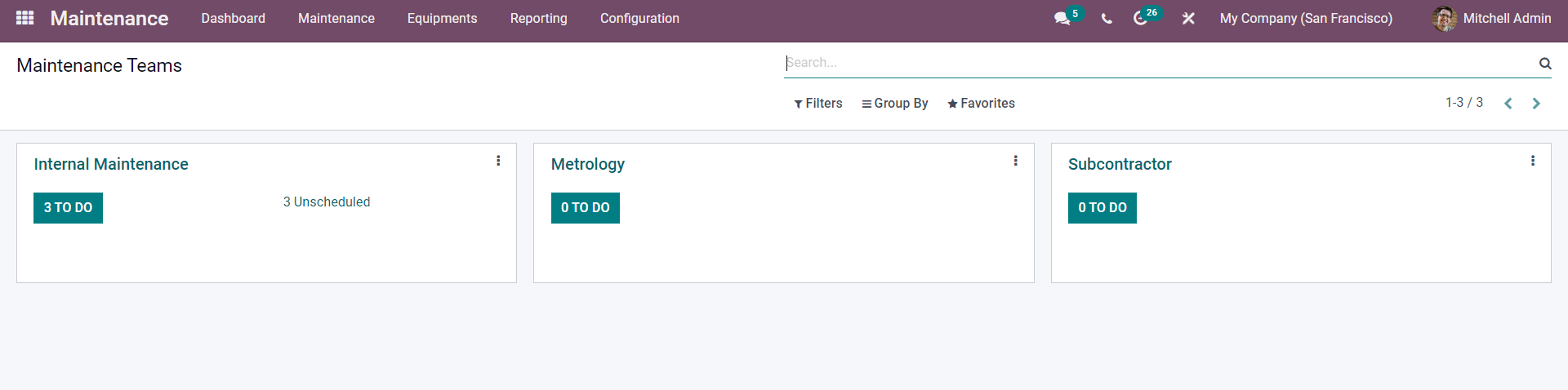
The dashboard will be filled with Maintenance teams. The requests for an instance will be shown under the maintenance teams. These are actually categories that you can create according to the nature of your machinery or business for receiving the requests. Click on any of the Teams, and it will take you to the requests as shown below.
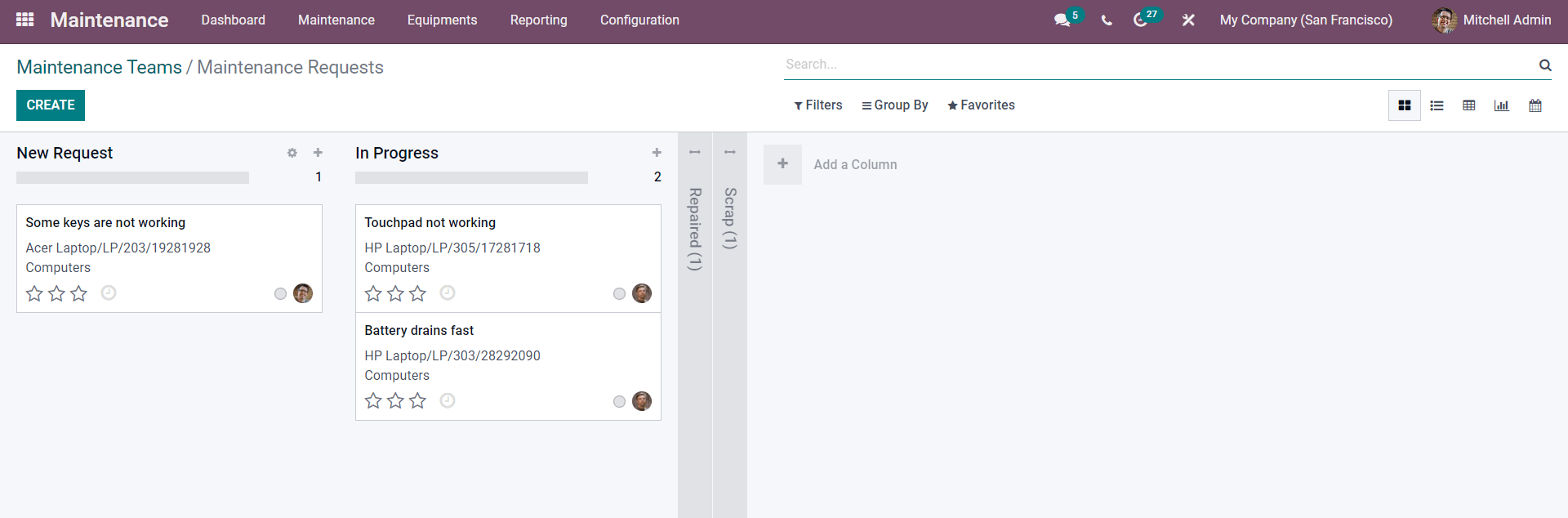
It is easy to manage the Maintenance requests in this format.
Maintenance teams and Request
You can easily configure Maintenance teams. To create a Maintenance team, go to the Configuration tab from the dashboard of the Maintenance module, and from the drop-down menu, click on Maintenance Teams. Page on Maintenance teams will open up a shown below.
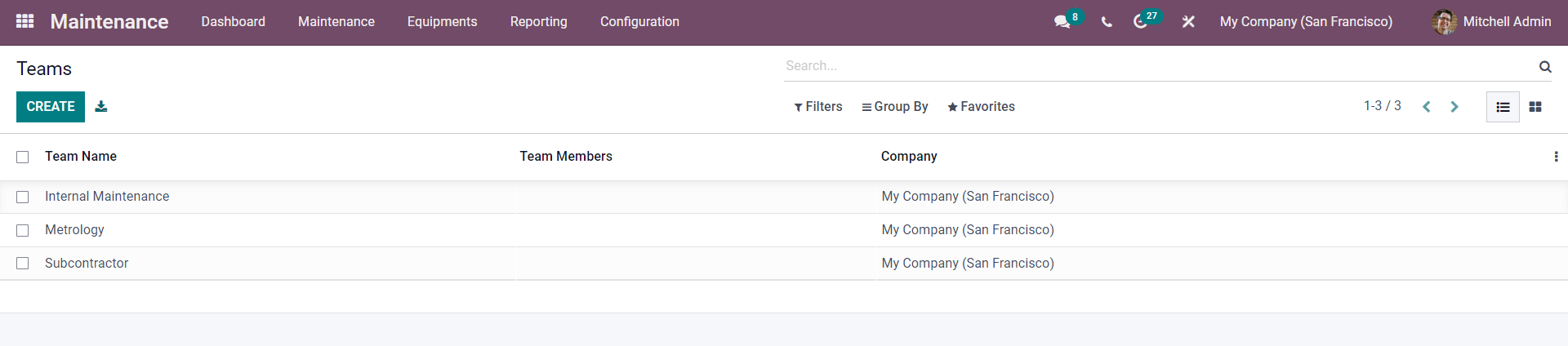
All of your created Maintenance terms will be listed down on this page. To create a maintenance team, click on the CREATE button as shown in the image given above. As shown below, an empty field to create the new Maintenance Teams will open up.

Click on the Empty field to add the Team name Team members and select the company. Press on the SAVE button after the configurations and the Team will be saved and displayed on the Maintenance module dashboard.
Creating and maintaining Equipment categories can help you manage different types of equipment more efficiently. To create and manage equipment categories, go to the Configuration tab from the dashboard of the maintenance module, and from the drop-down menu, click on Equipment Categories. A page will open up, as shown below.
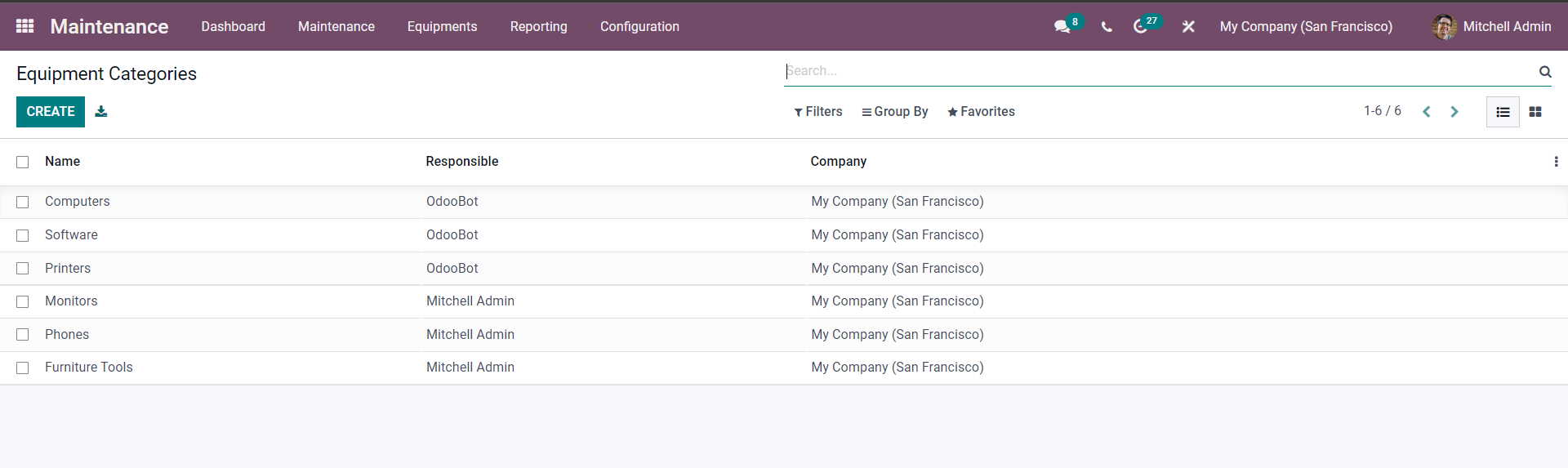
All of the created Equipment categories will be listed down on this page. To create a new Equipment category, click on the CREATE button, and a configuration page will open up a shown below to create the new Equipment category.
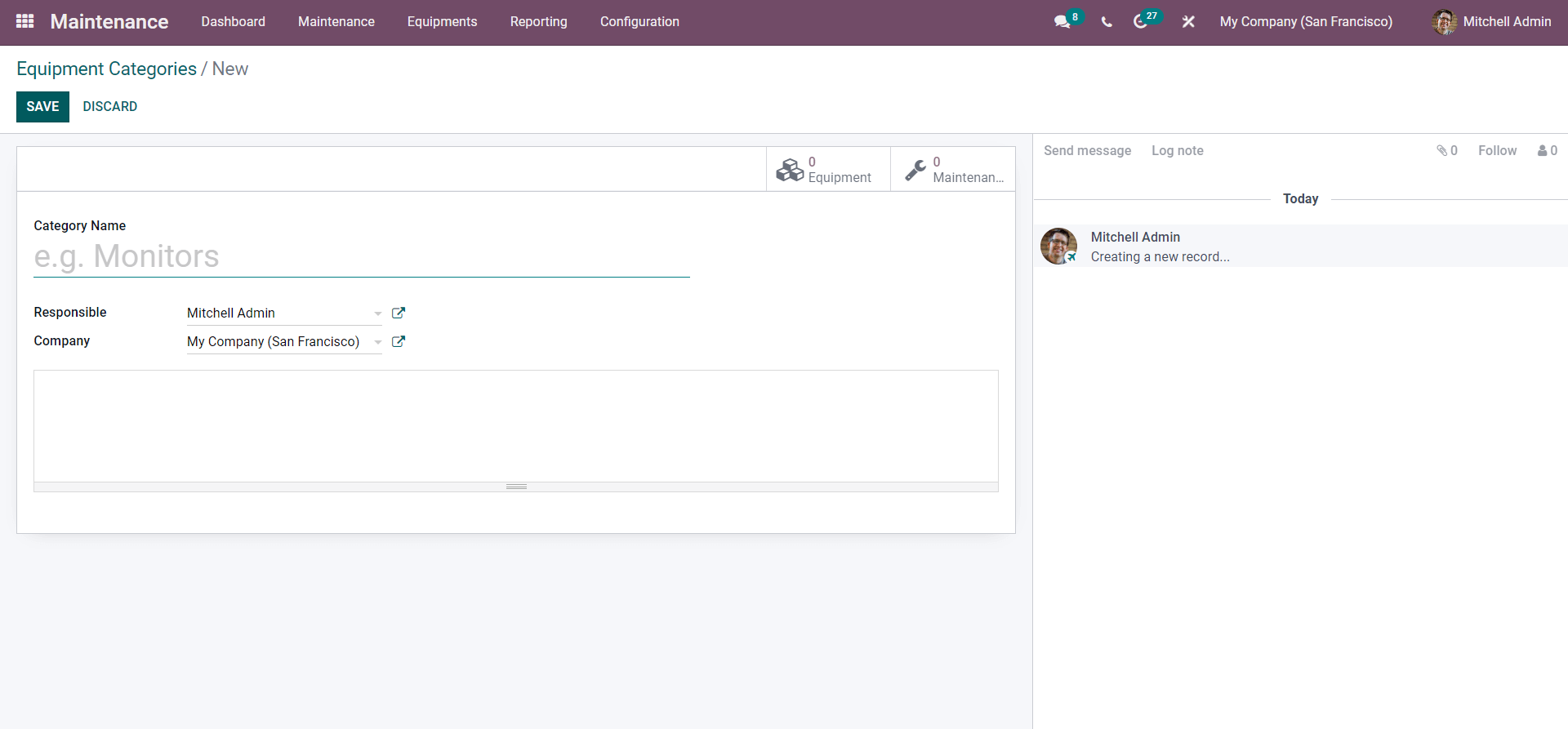
You can begin the configuration on the category by naming it under the Category name field, as shown above.
You can appoint the person responsible for the Equipment category and select the company from the Company list. For more configurations on the Responsible Person and the Company, click on the external link button next to the fields shown below.
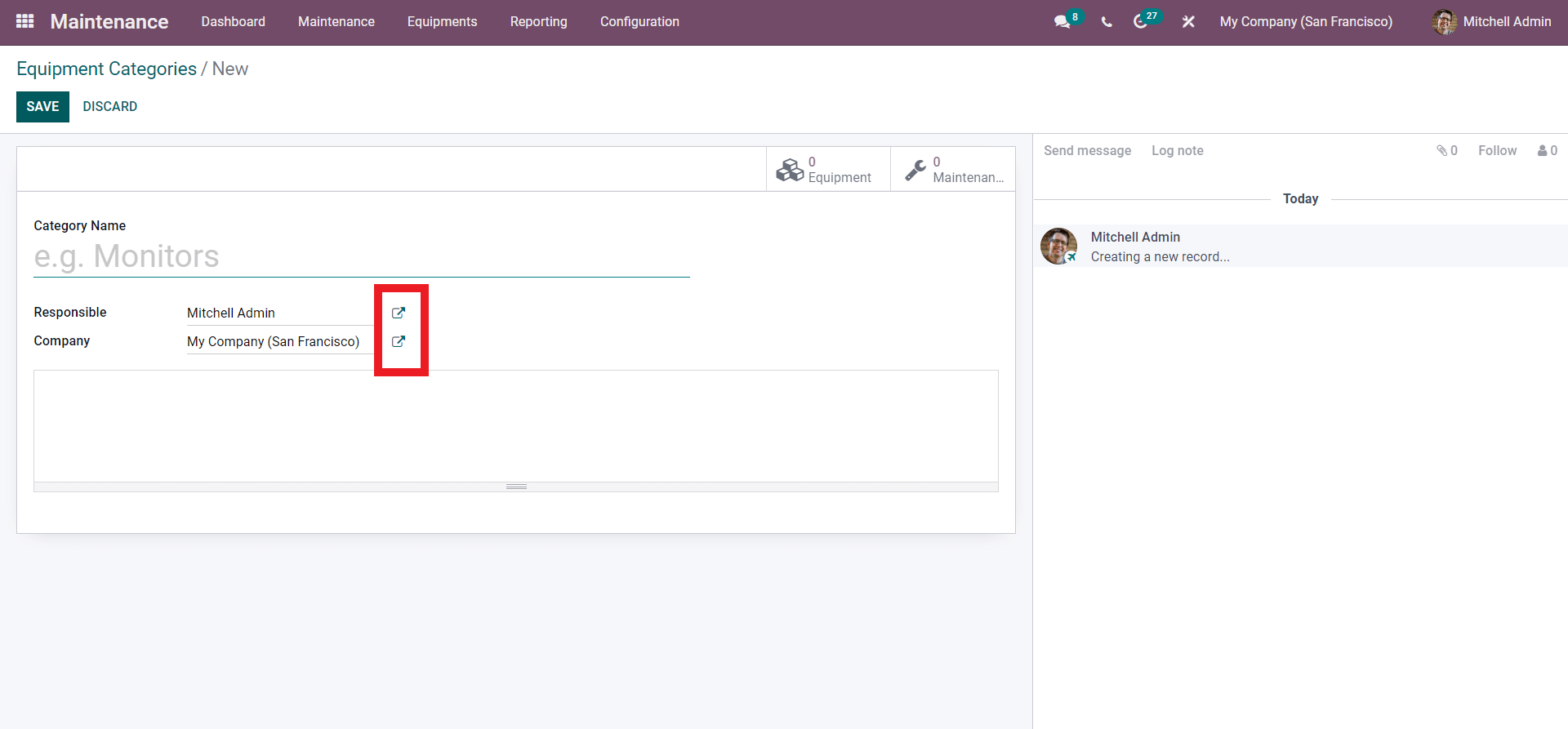
The external links will take you to the configuration sections of the concerned. You have the option to configure the company and the person responsible by going to the external link.
Maintenance requests and request management can be hectic tasks. The Odoo 15 Maintenance module has a dedicated section for request management. Go to the Maintenance tab from the dashboard of the accounting module, and from the Dropdown menu, click on Maintenance Requests, and a page will open up on maintenance requests as shown below.
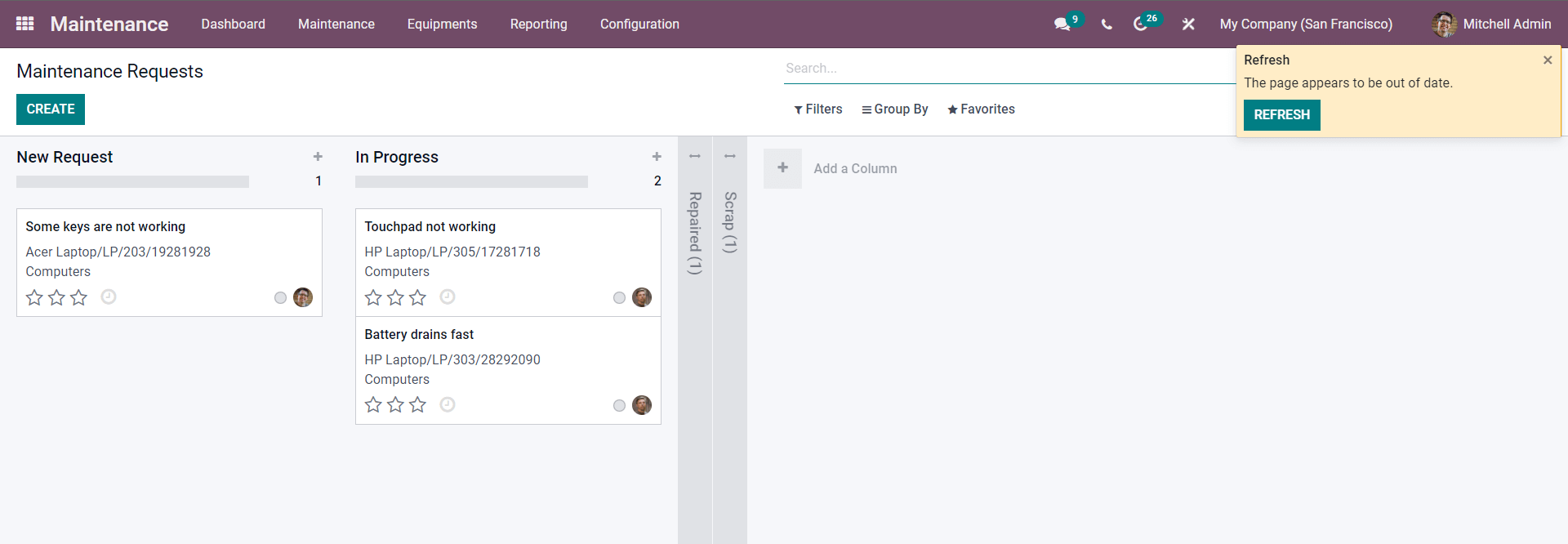
You can prioritize the request by rating the Requests using three-star emoticons under the requests. Click on it, and the stars will be filled to note the importance of the requests.
From here, click on the CREATE button to create a new Maintenance request. From the preceding, as shown below you can create the new request.
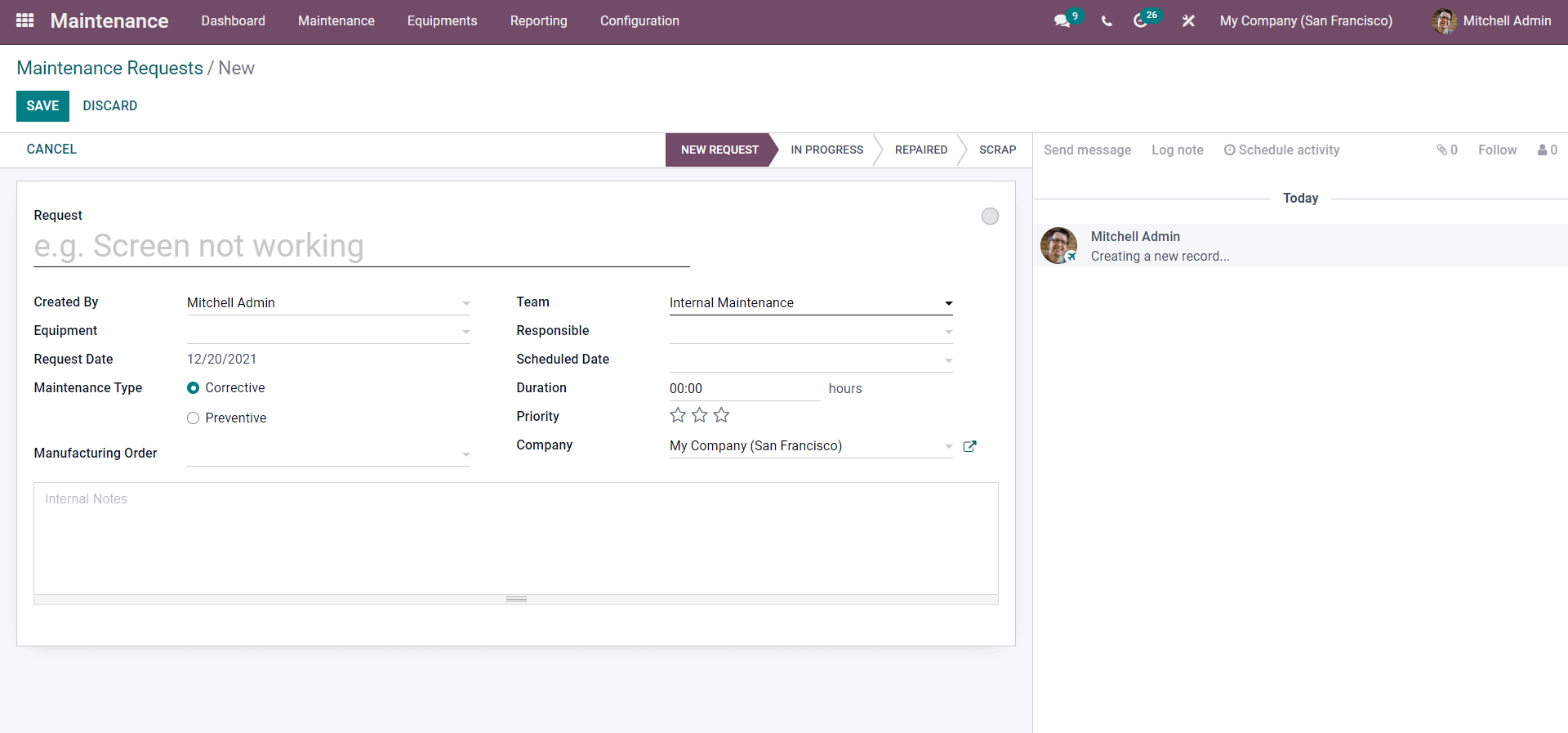
Here, under the Request field, you can enter the reason for the Maintenance request. After this, enter the person’s name, who creates the demand, and the team under which the person is working. Click on the Equipment field, and a drop-down menu of Equipment will open up, as shown below.
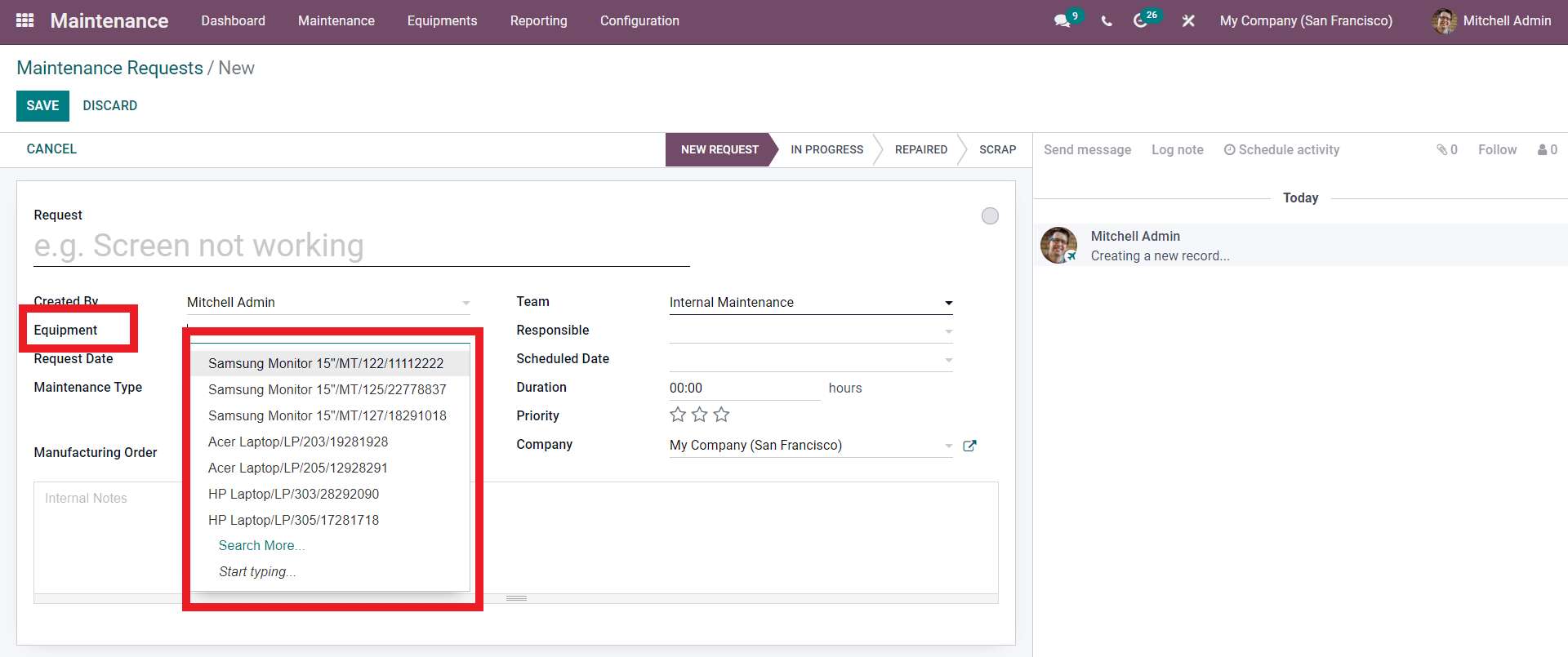
From the drop-down options of the Equipment, as shown above, select the equipment you want to request the Maintenance on. Click on the Search more button to search for more equipment. A tab with all of your equipment will open up for you to choose from. After entering the Equipment, add the Equipment from the Responsible field, from the drop-down field, and add the person responsible for the process.
Enter the date of Request in the Requests date field and the scheduled date in the Scheduled date and Duration. You can rate the priority of the Request by rating it using the Star emoticon next to ‘Priority.’ You can choose between the two maintenance types the Corrective and Preventive Maintenance.
Preventive Maintenance
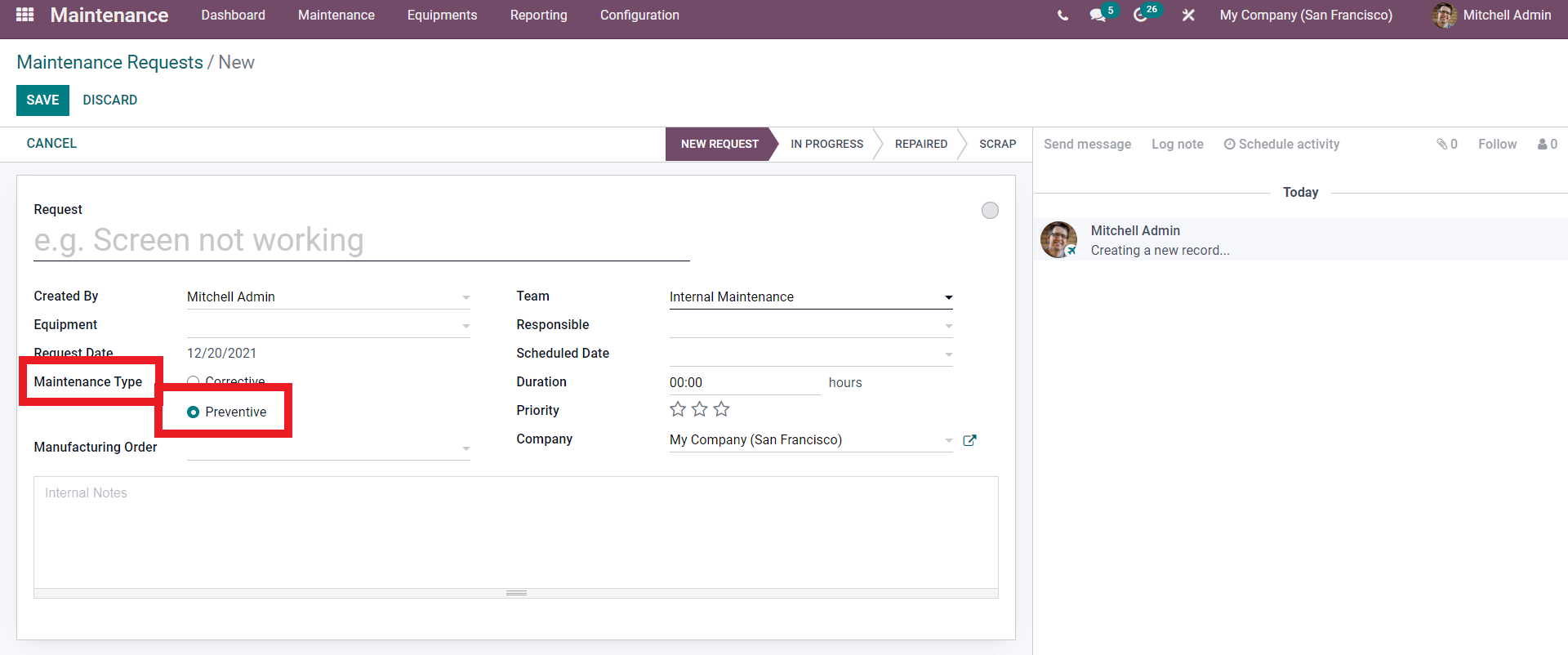
Preventive maintenance is used for standard maintenance procedures or operations. The preventative Maintenance type will let you schedule maintenance activities in time by ensuring maximum utilization of the machines and preventing them from unexpected damages. Every instrument ranging from computers to complex manufacturing machines can be managed in this method.
Corrective maintenance

Even with regular maintenance works, it’s common for the machinery to run into issues and defects. These machinery issues require immediate attention, and this is where Corrective maintenance plays its role. The problem will be reported to the maintenance team to work on it immediately. Choose between the maintenance types and if you want to apply a manufacturing order to the Maintenance request, click on the Field next to ‘Manufacturing order,’ and from the drop-down options, select the manufacturing order.
If you want to add any notes or instructions, enter them under the configuration tab on the Internal notes section. After the configurations, click on the SAVE button, and the requests will be added into the New Request stage a shown below.
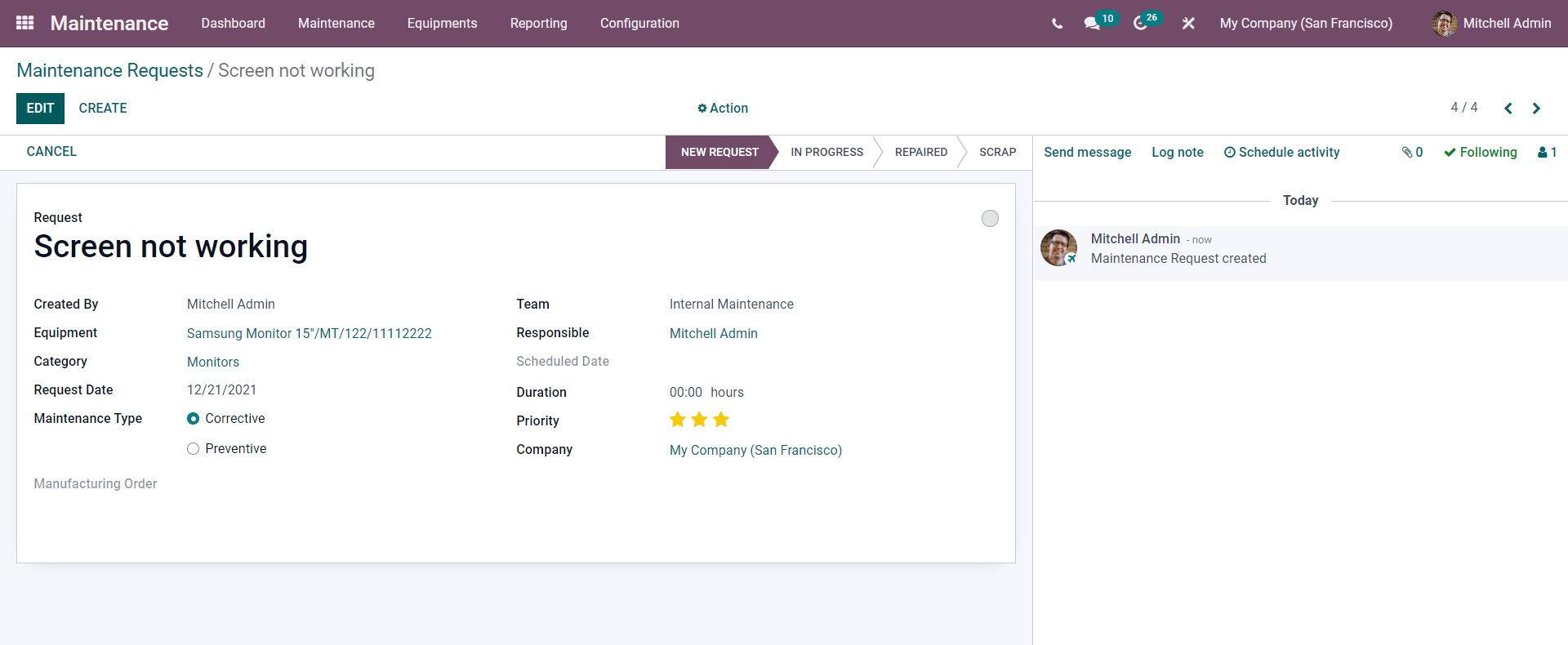
The new maintenance request will be displayed in the Maintenance requests section, as shown below.
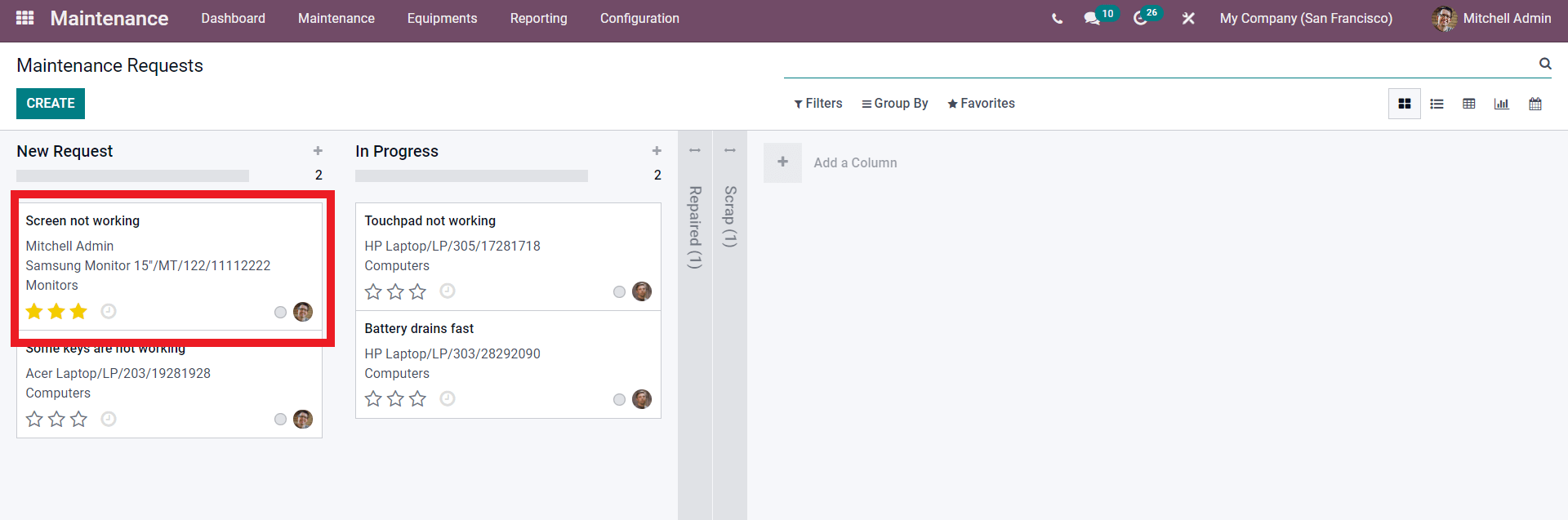
Drag the request to different stages to update the Maintenance process.
Maintenance calendar
The maintenance calendar can be accessed from the Dashboard of the maintenance module under the Maintenance tab. Select the Maintenance calendar from the drop-down menu, and the calendar will open up as shown below.
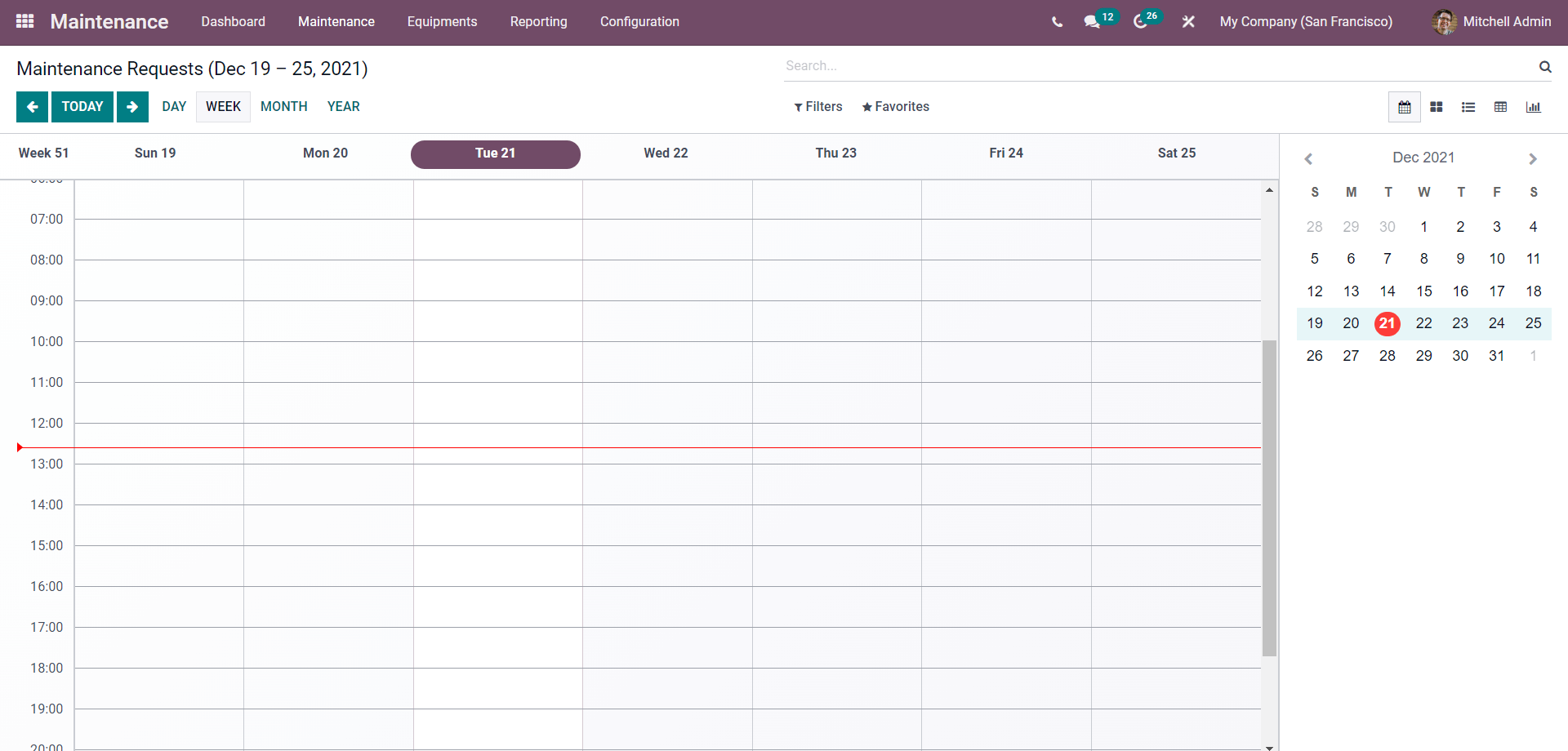
All maintenance requests will be shown here concerning their dates. You can set the calendar to Daily, Week, Month, and Year. If you click on any of the dates on this page, then a tab will open up as shown below to create new maintenance requests.
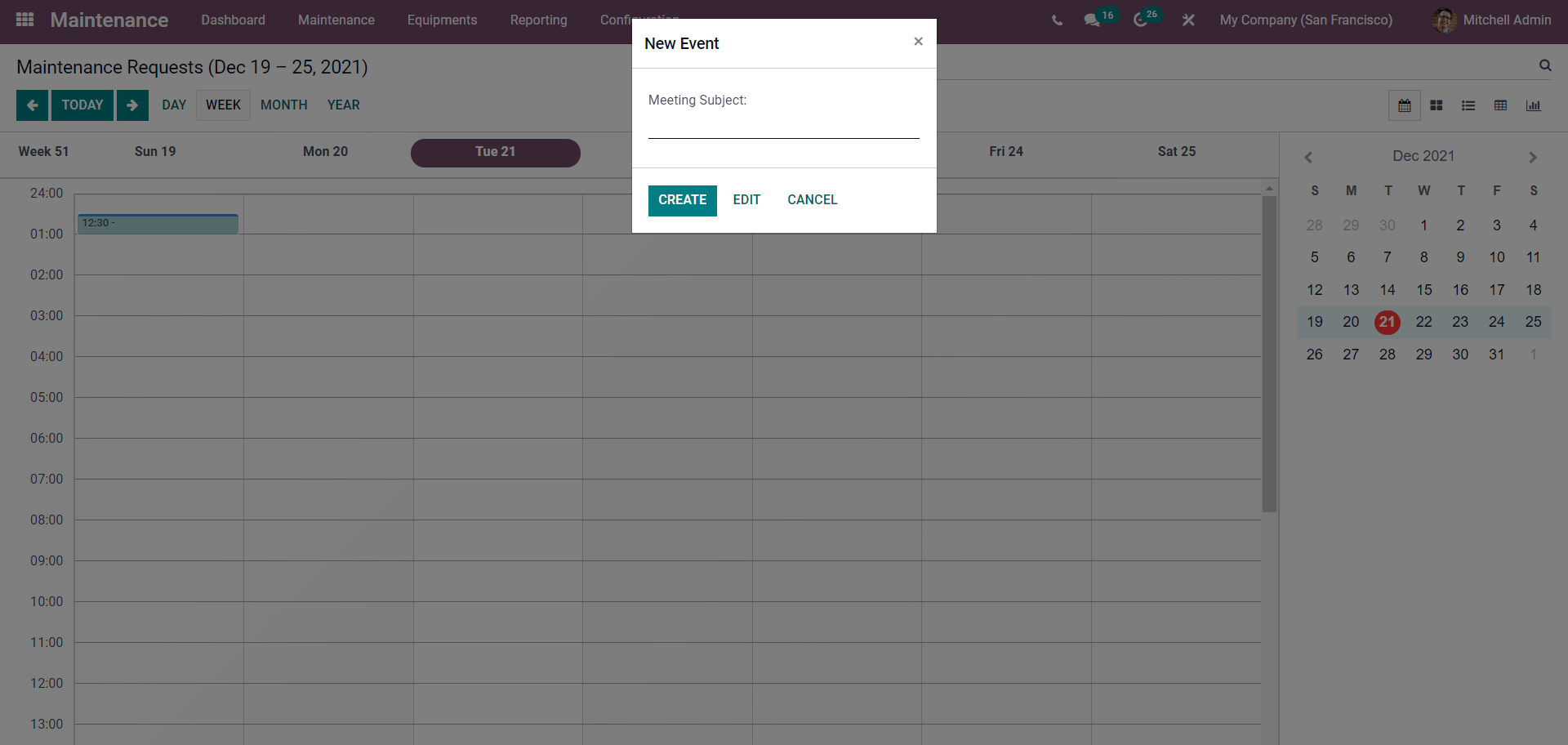
Click on the CRETE button to create the maintenance requests for a particular date.
You can use the advanced filtering option to filter the Maintenance requests. You can access the filtering options from the Filter tab, as shown below.
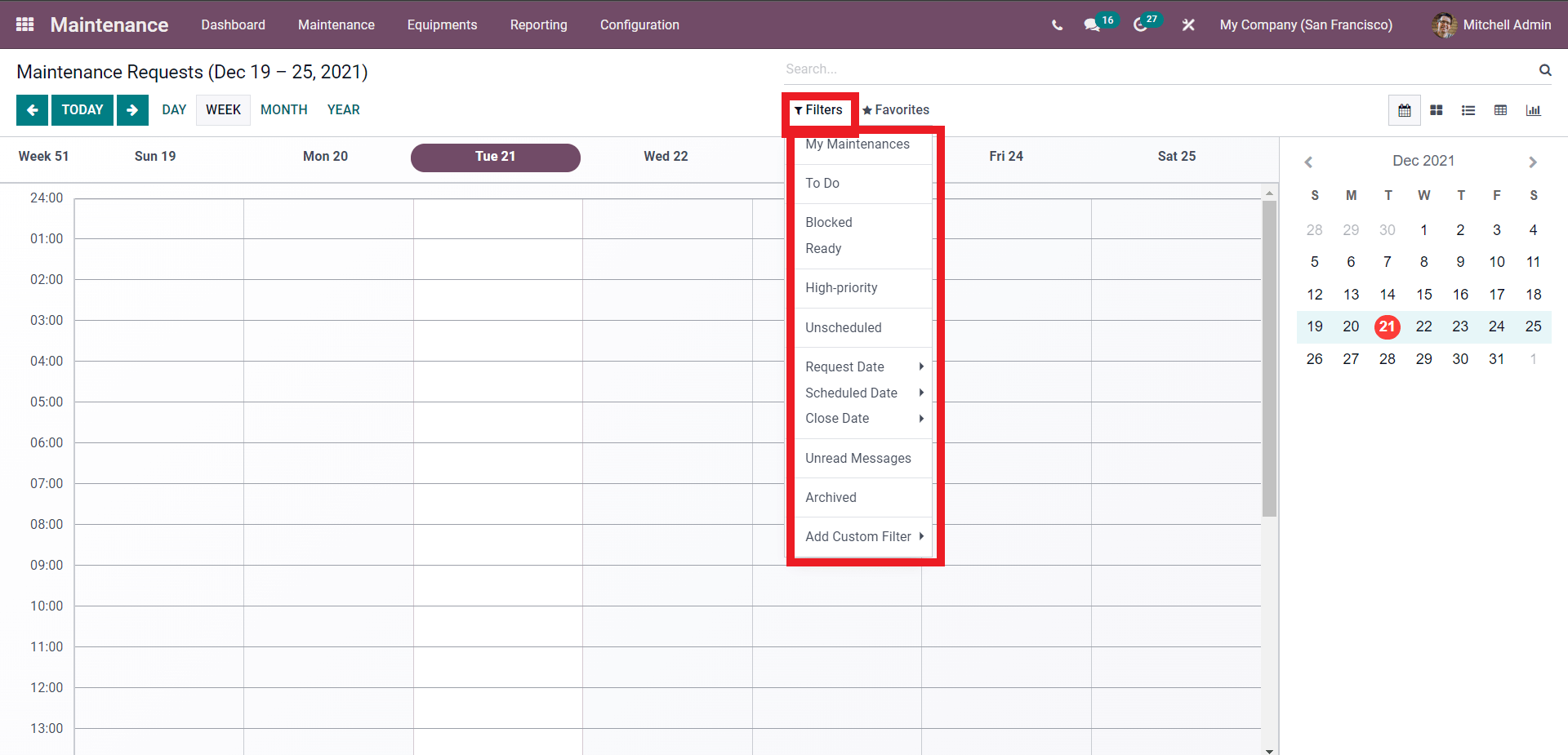
You can use the filter options to filter out the Maintenance requests for quick access. This will allow you to manage your maintenance requests efficiently.
It is integral for a business to keep its machines running as they are the major contributors to productivity. Odoo 15 maintenance module will let you manage and provide a complete birds-eye view of your machinery and equipment.