The Manufacturing module of Odoo 15 allows you to efficiently manage and overview the entire activities on the manufacturing sections of your business. The module is equipped with highly advanced features and tools to make it more efficient.
This blog will give you a complete overview of how to manage product variants and semi-finished products with Bill of Materials in Odoo.
Bill of Materials is one of the features in the Manufacturing module that allows you to define and configure a new product that is to be manufactured. Product variant management and managing semi-finished or unfinished goods or products are two of the most advanced features in the Bill of Materials. These features can come in handy at any stage of the manufacturing procedures.
You can configure and use the feature from the Bill of Materials Menu in the Manufacturing module. It is easy to configure these features in the Bill of Materials in the Odoo Manufacturing module.
Bill of Materials
Listing out each product for manufacturing a new final product is necessary to increase the efficiency of the manufacturing sector in your business. It is extremely easy to configure the Bill of Materials feature in Odoo. Bill of Materials is available under the Product tab from the Dashboard of the Accounting module.
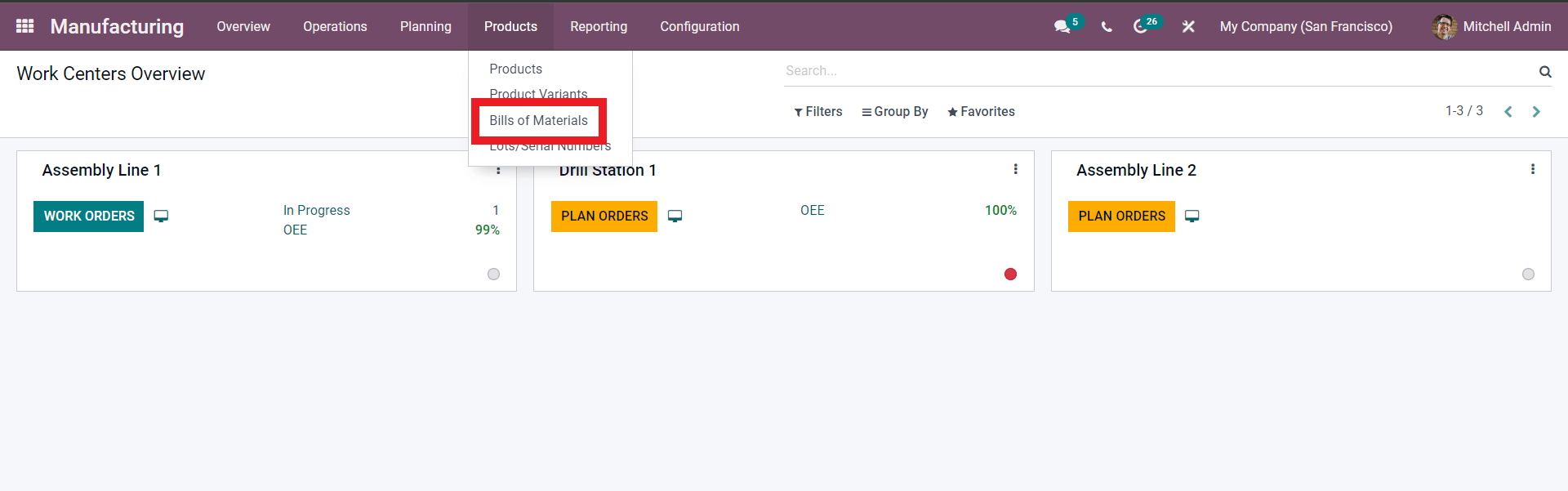
Click on the ‘Bill of Materials from the dropdown options as highlighted in the image given above to go to the Bill of Materials section as shown below.
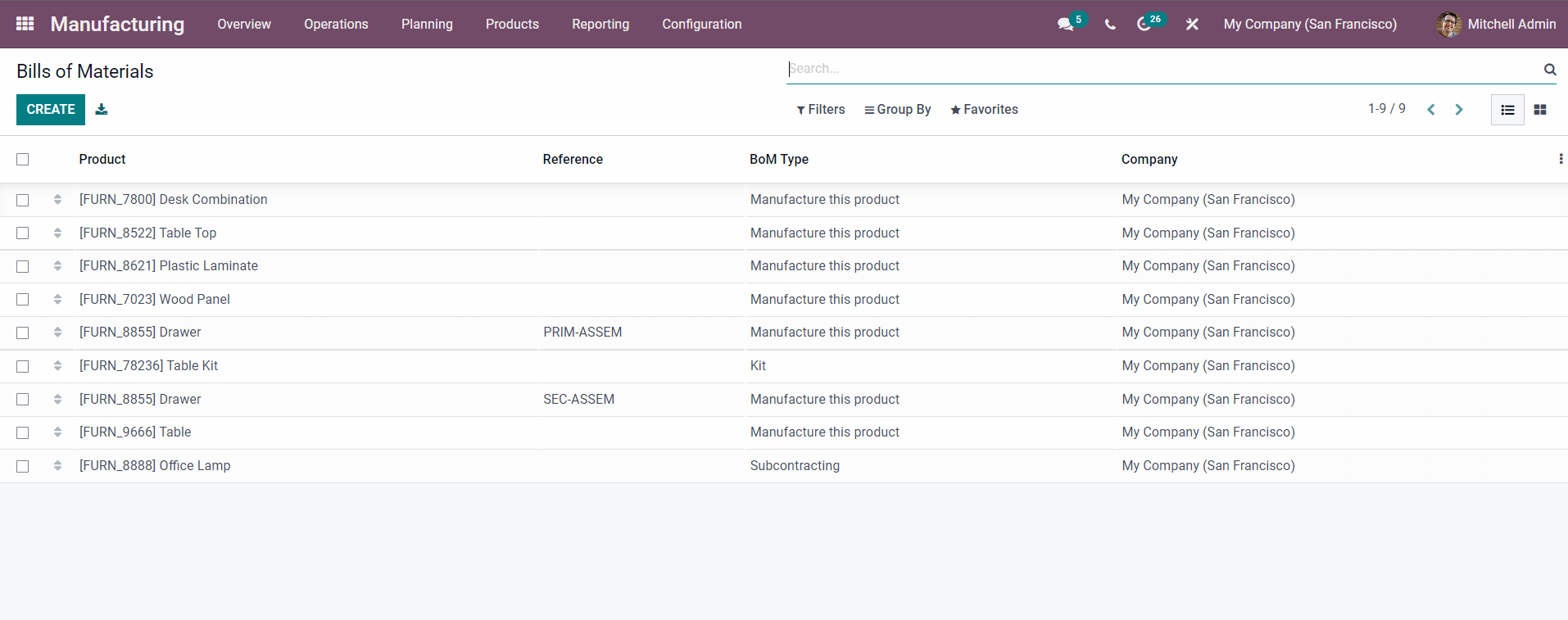
All of the Bill Materials that you have created will be listed here for you to overview, manage and configure. To create a new Bill of Materials click on the CREATE button as shown in the image given above. Click on it and the configuration will open up for you to configure a new Bill of Materials as shown below.
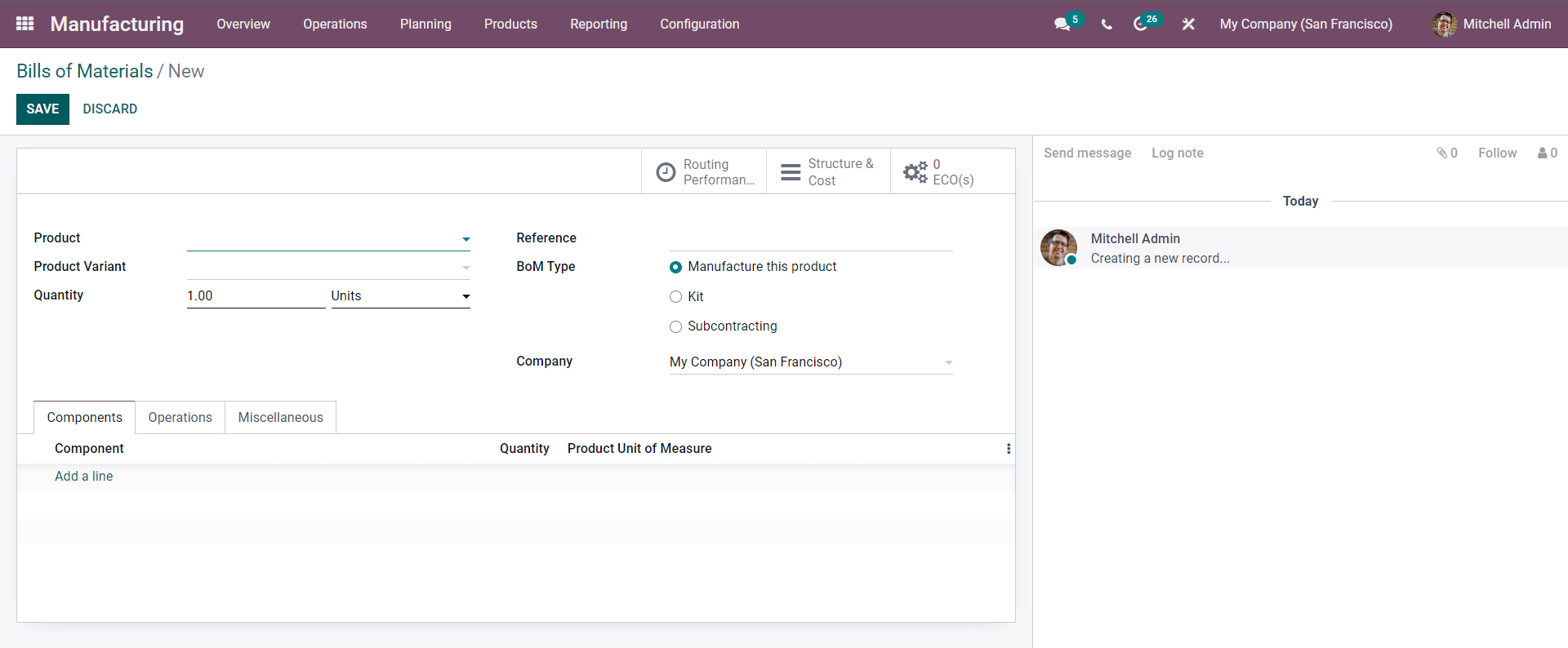
Note that if you have already created a Bill of Materials and want to configure then choose it and edit it if the new configurations are for the already created Bill of Materials.
You can either add the product from the drop-down list or create a new one by clicking on the ‘Create and Edit’ button as shown below.
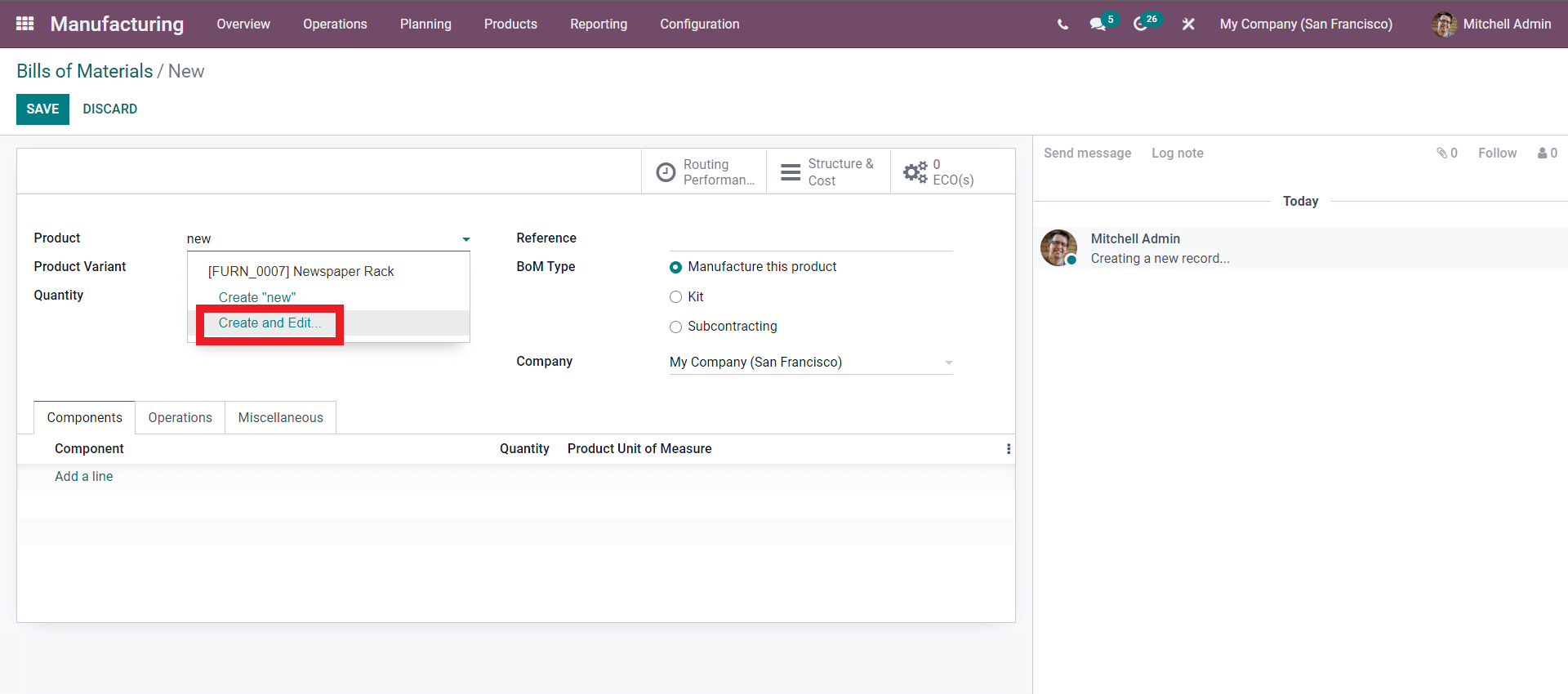
Click on it and a configuration section to configure the Product as shown below will open up.
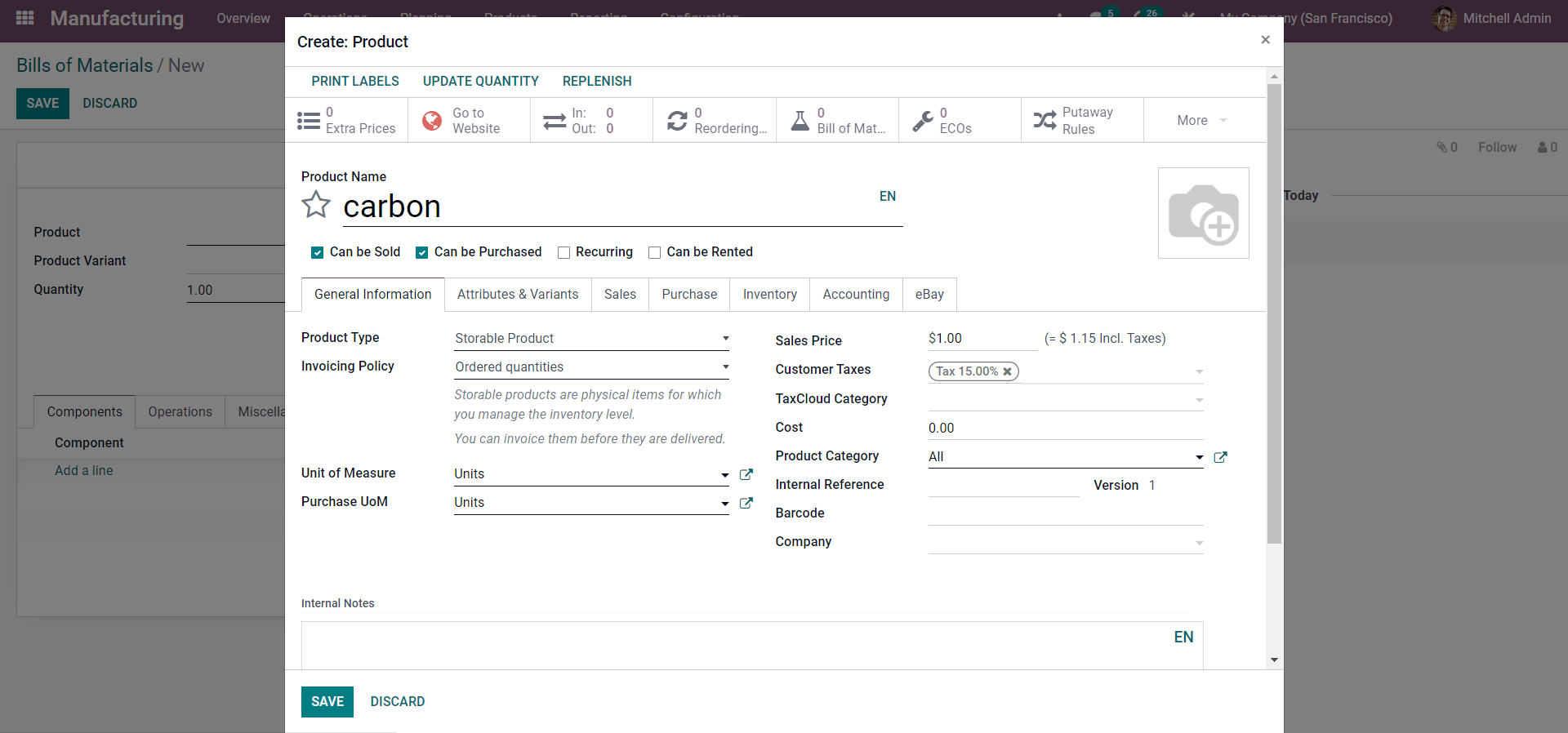
You can create and SAVE the product and it will automatically be added or will be available for you to include in the Bill of Materials. Enter the name of the Product and if it is a product that can be sold, can be purchased, Recurring, or Can be rented, you can choose from the options according to the nature of the product that you are creating.
From the product, the configuration section clicks on the Attribute s and Variants to give the newly created product a completed nature. From here you can add the product variants and Attribute s in these sections as shown below.
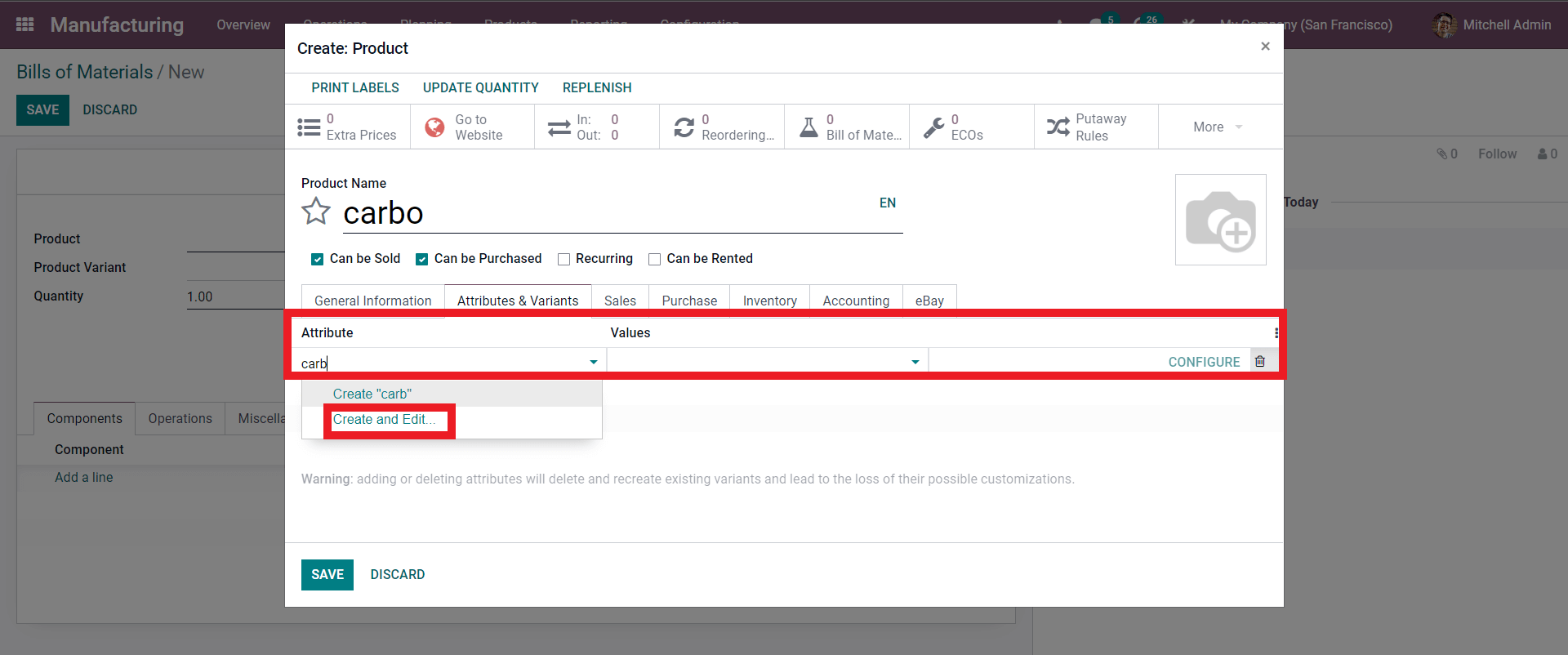
You can add the Attributes here. You can see a list of Attributes s from previously created products from here. If the Attribute is new then type the Attribute s name and click on the Create and Edit as shown above to create a new Attribute. A configuration page is shown below to configure the Attribute will open up.
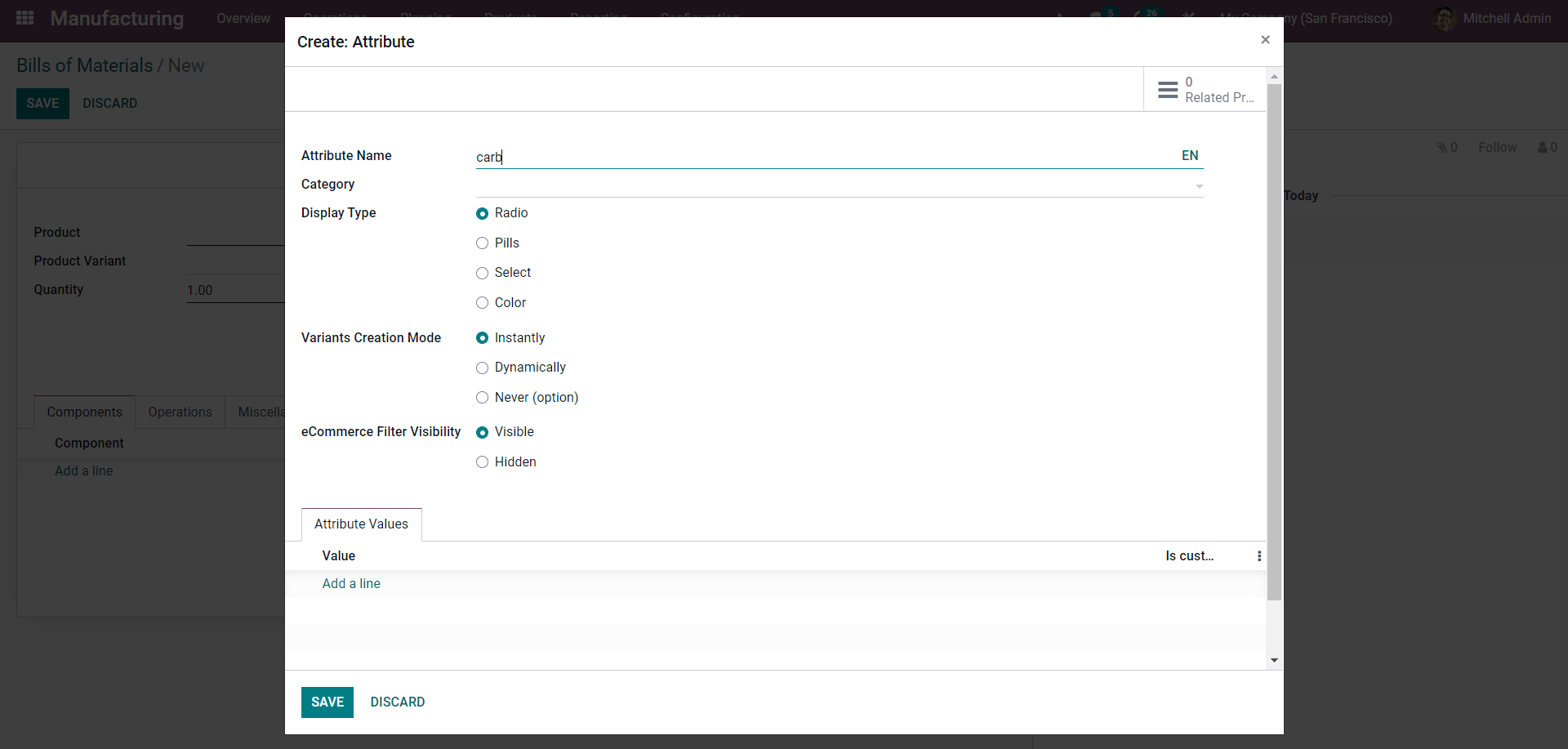
Note that giving Attributes to Products is essential for efficient product management. All of the products will be managed on the basis of the Attributes that you have given. This also allows Odoo to recognize and separate products from each other along with the product’s variants. This also allows you to manage and recognize products easily from a huge line of products.
Giving Attributes s to products can better help them define and at every stage of product management, in Odoo Attributes play a huge role, so it is important to define Attributes for the products. These Attributes s are used in the website module to define products displayed for sales, so when the customer searches for products based on Attributes Odoo can display the products efficiently increasing the chances of sales.
Configure the Product Attribute s and add the value by clicking on the ‘Add a line’ button under the Attribute values. All of these Attributes help Odoo to decide the Products Varients. After configuring the product variants click on the SAVE button and the entire procedure will be saved. The Product Configuration page will open up after this. Complete the configurations, click on the SAVE button and the Product will be saved.
Product variants
After configuring the product it will be available to add in the Bill of Materials section. Choose the product for the drop-down menu of options as shown below.
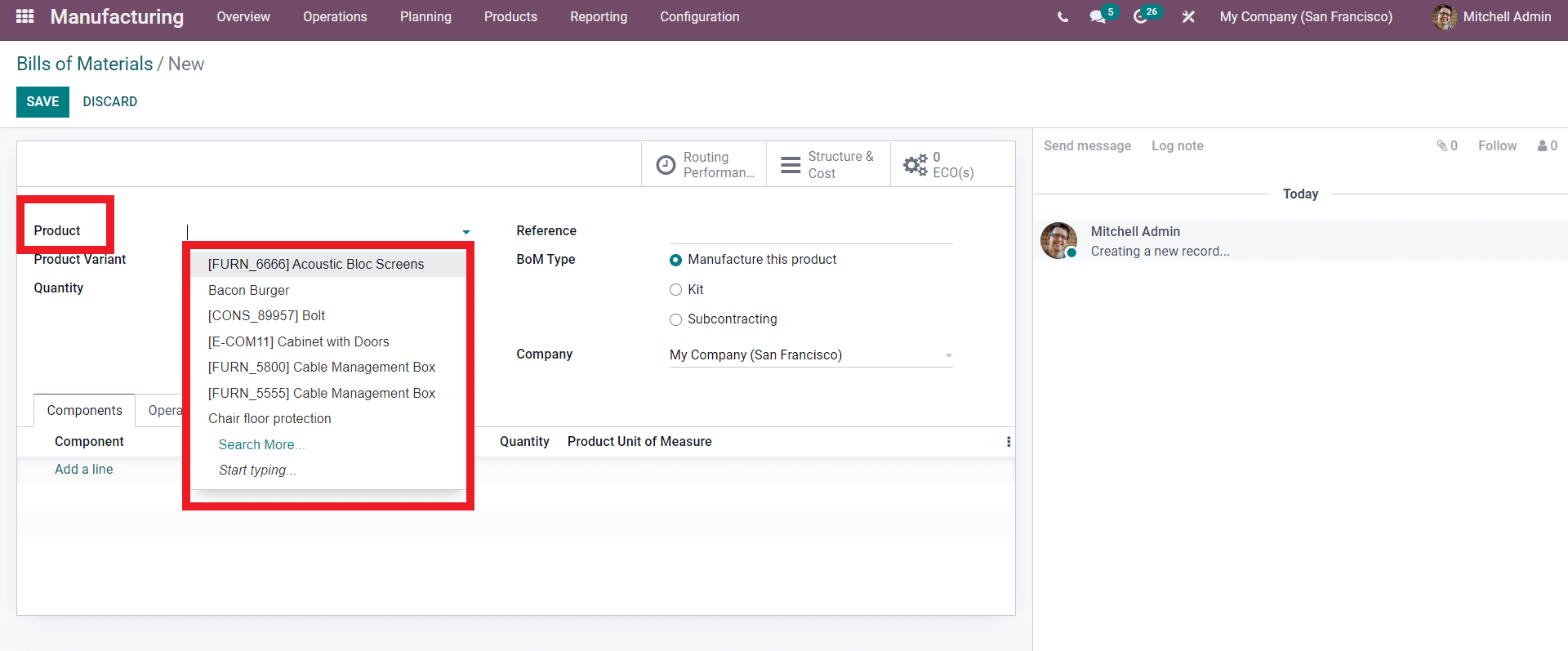
Select the product from the list of Products as shown above. After adding the Product you can add the Product variant using the Product variant option as shown below.
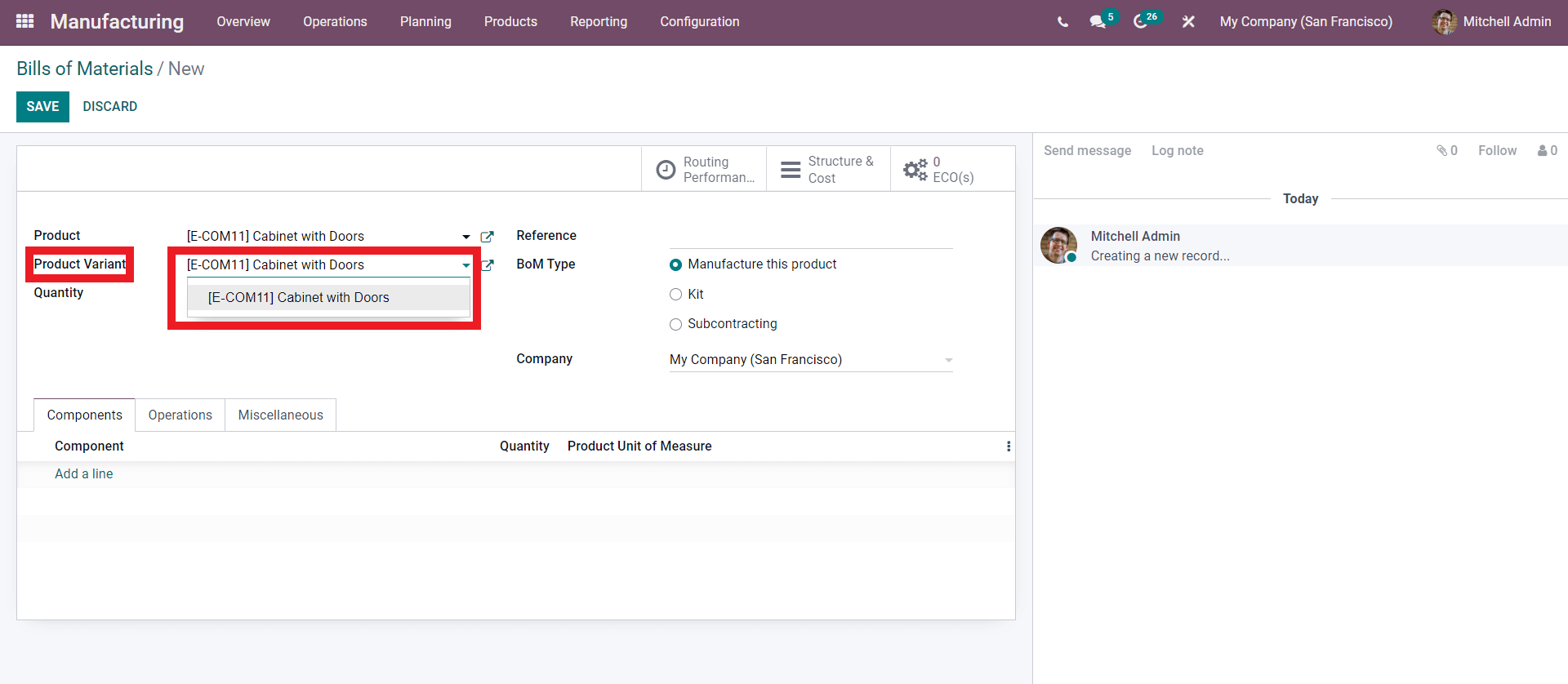
From the Product variant you can either choose a product variant or click on the Create and edit button to create a new Product variant as shown below.
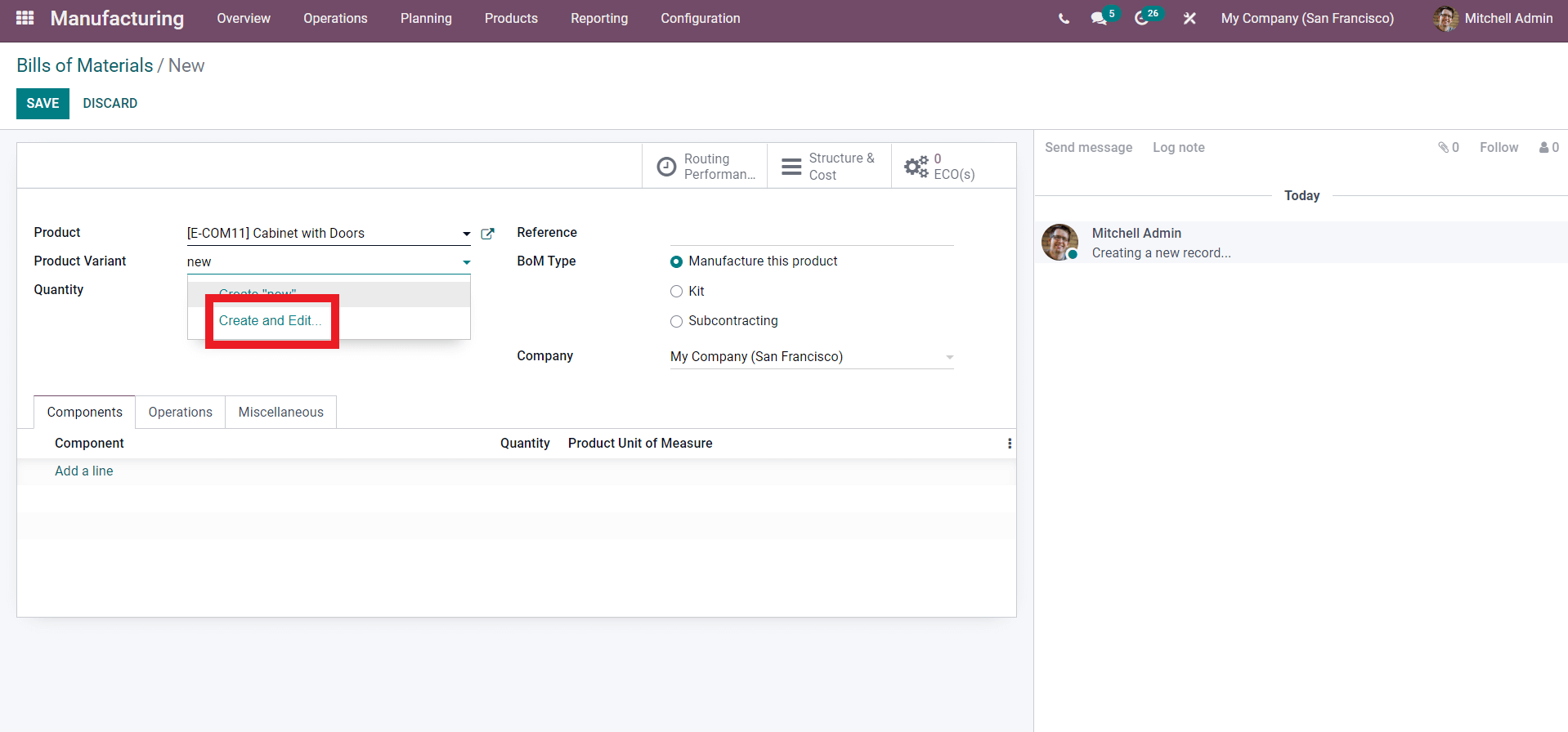
A configuration page will open up with advanced Product variant management options to configure the product variant as shown below.
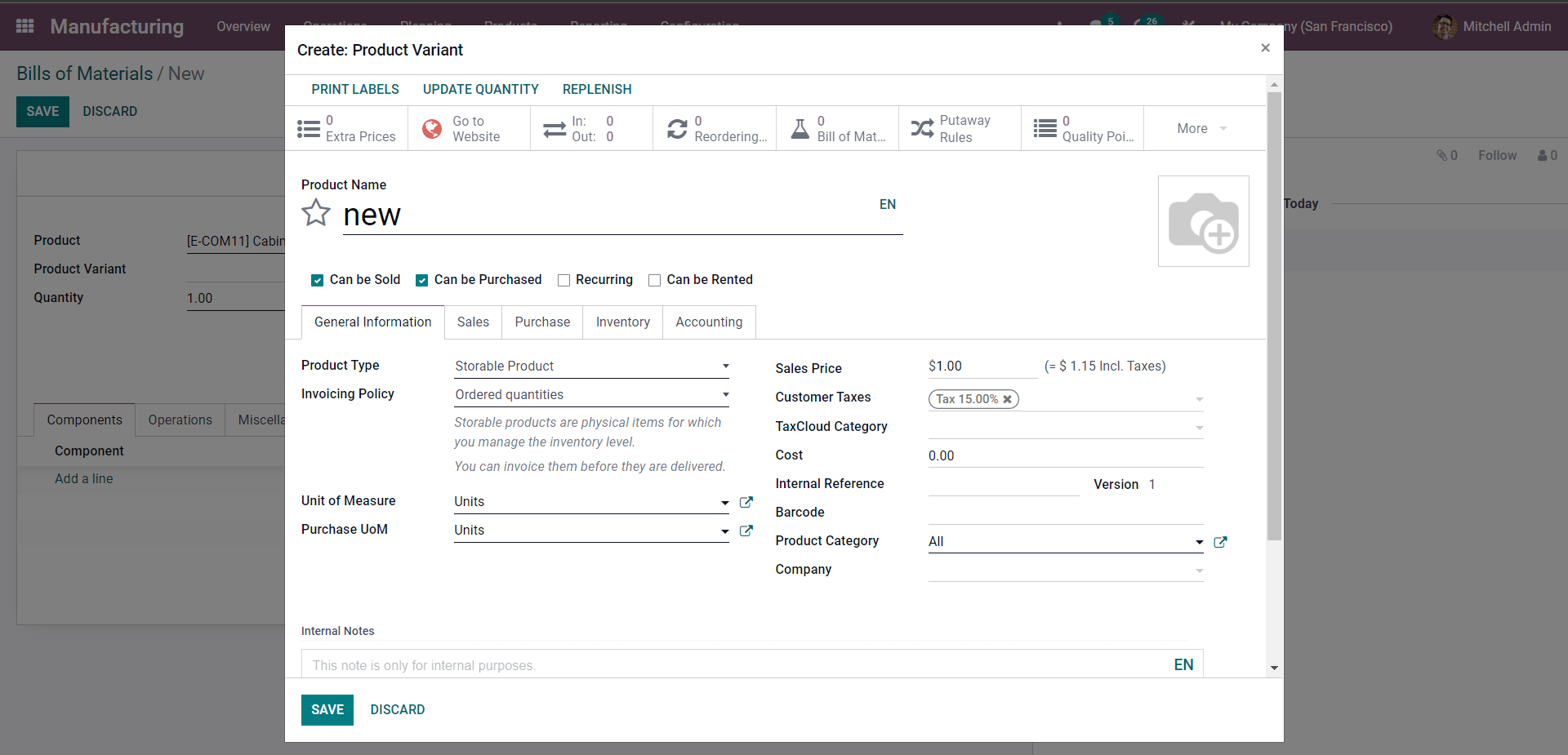
Similar to the product configuration you can configure the Product variant form here. Under the inventory, you can define the operations routes on the Product.
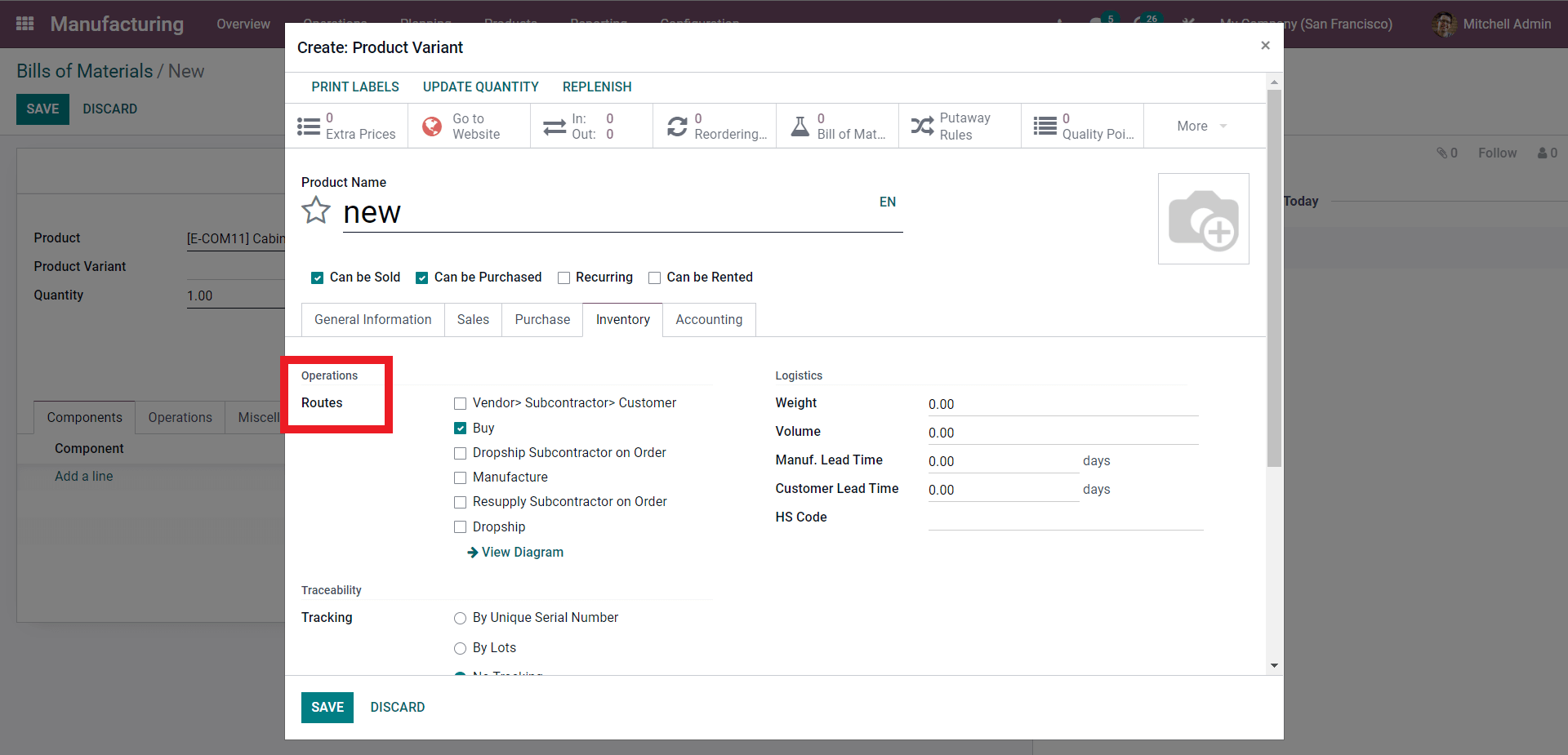
This allows you Odoo to manage products more efficiently. After the configurations, the product variant will be available to add from the section. Creating a new product variant is an option and most of the time if you have the necessary products left Odoo will give you the product variants automatically for you to choose from the Bill of Materials section.
If you are defining a product variant on the Line-item-basis then the Product variant field of the Bill of material should be left blank as the field is used for single product variants. So if you add a product to the Bill of material then the components can be added to the product to manufacture them and then if you have defined the variants along with their Attributes then the variants will be shown with the components for better product management.
Manage Semi-Finished products
Managing semi-finished goods can be a headache as it is not easy to manage and overview them in the traditional way. With the Odoo manufacturing module and the BoM feature, you can easily manage and overview the unfinished products easily without any product clutter.
In Odoo, you can create a sub-assembly product. A sub-assembly product is a product that is manufactured to use as a component to make another Product. To configure the feature go to the product and create Subassembly as a new product as shown below.
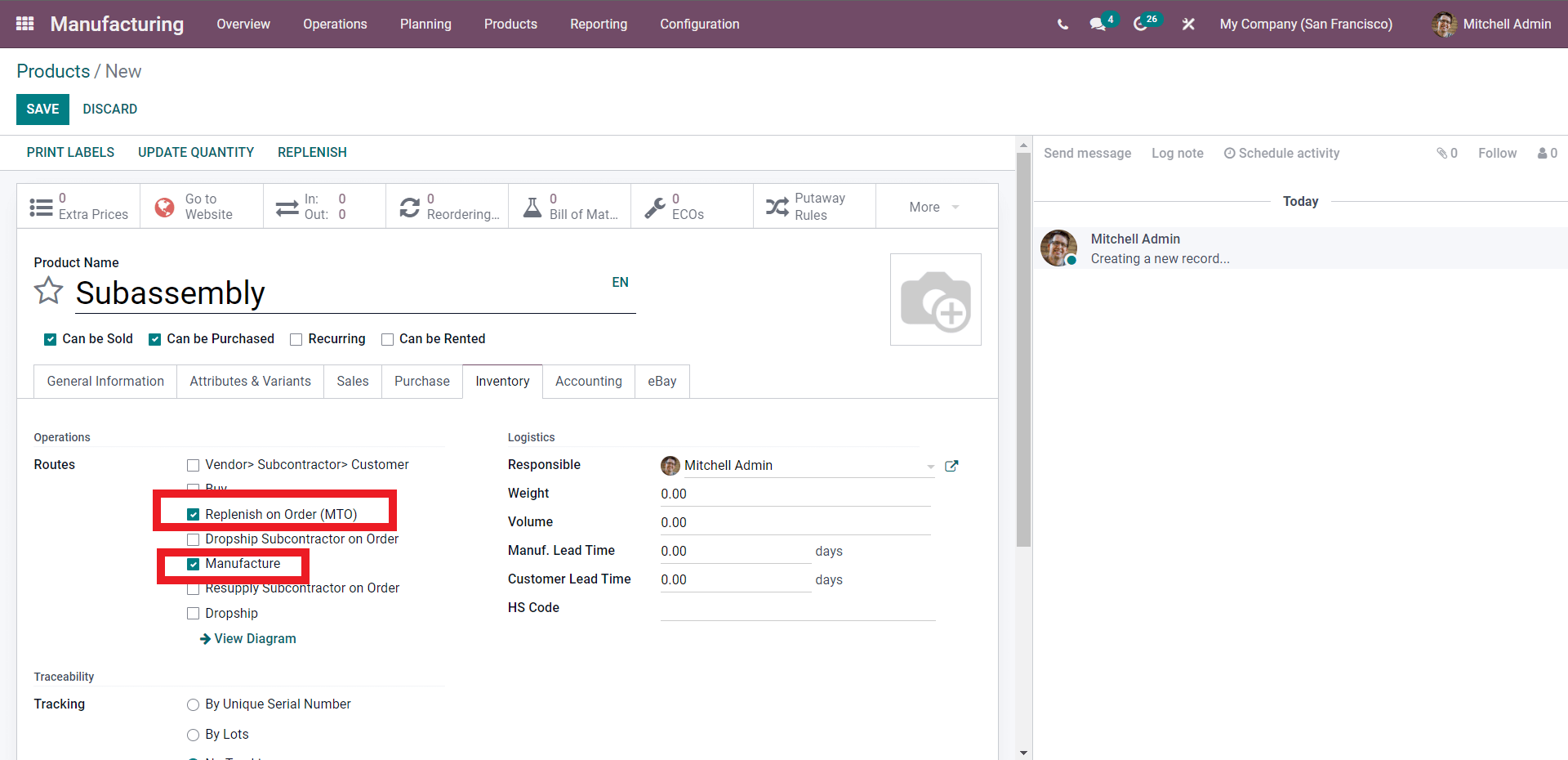
Under the Inventory, you have to set the Routes as Replenish on order and manufacture. After this, it will be ensured that every time when a manufacturing order is created for a top-level product another one will be created for subassembly products. You can find the product in the Bill of the material section after this. You can also create a new product from the Bill of material section as mentioned earlier. You can add the product from the product area under the Bill of Materials sections as shown below.
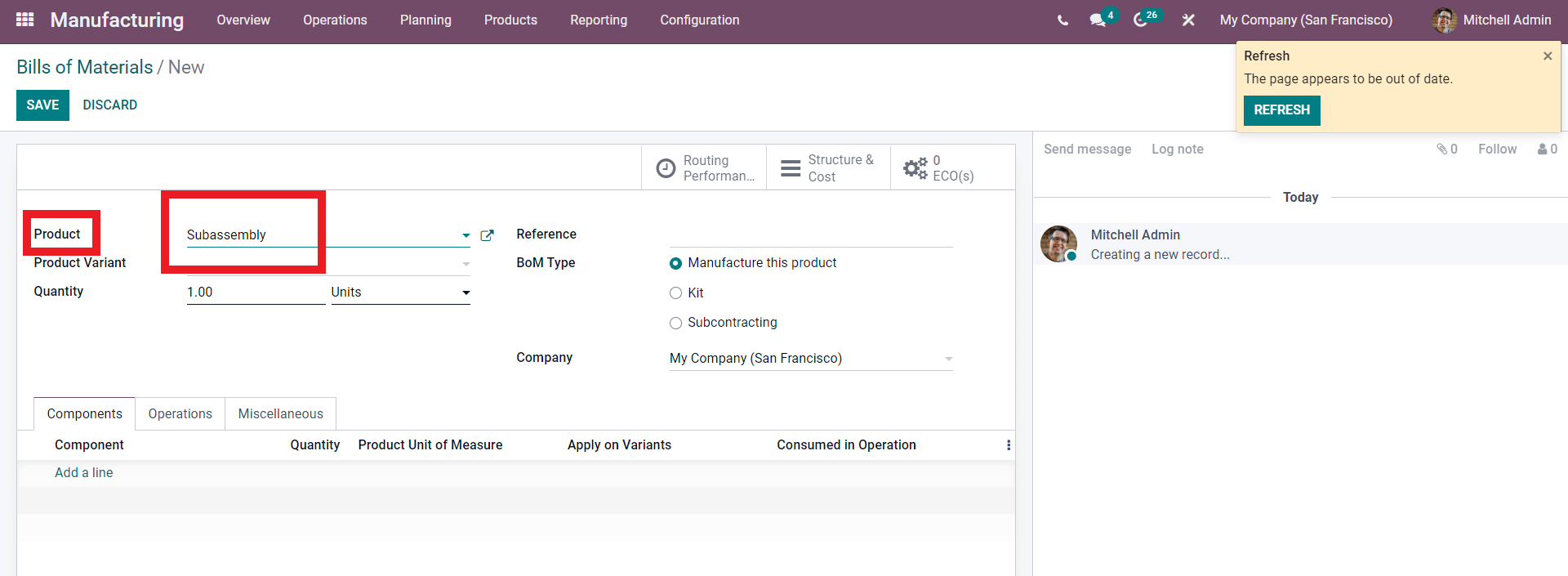
After this, you can add components to the Product as shown below.
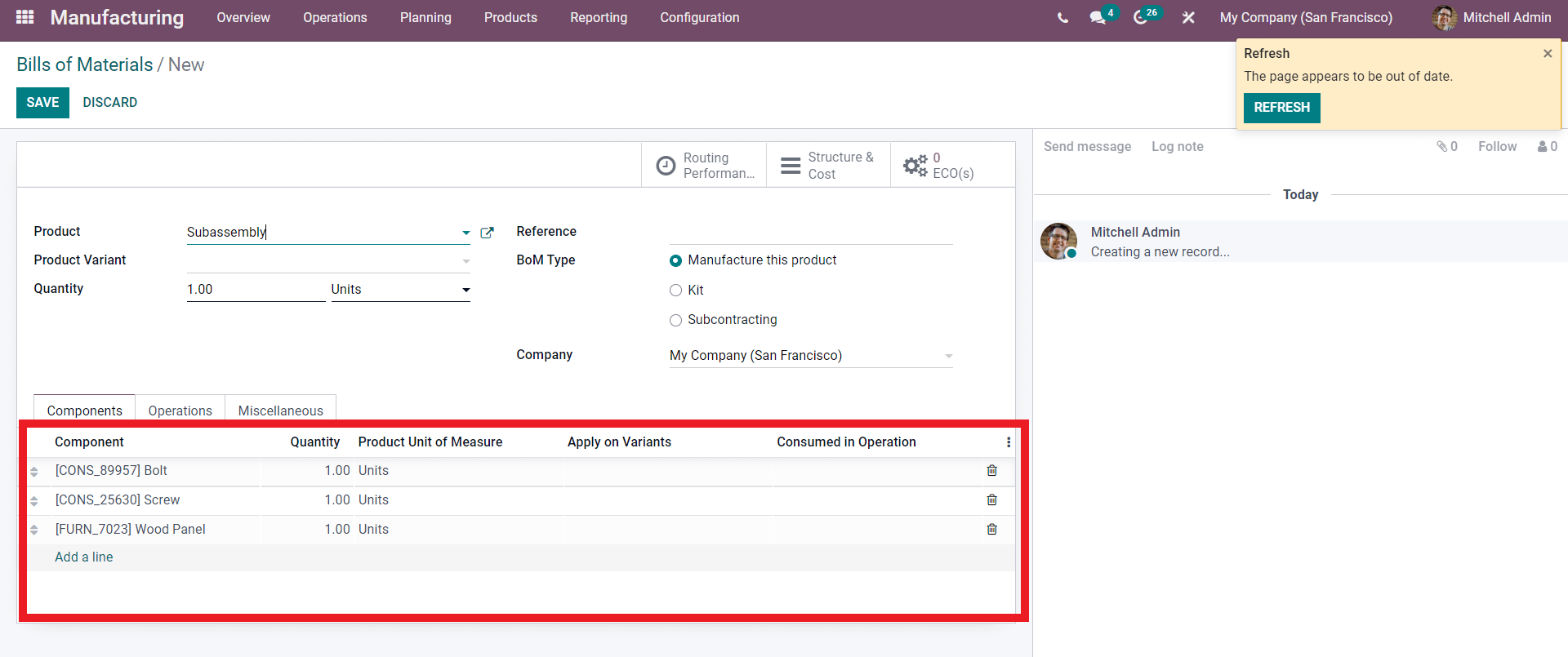
So the manufacturing will be carried out on the basis of the availability of the components. To ensure that the required component is available you can set a component to trigger a purchase order if it runs out. To configure this select the Component that you want the feature to apply to as shown below.
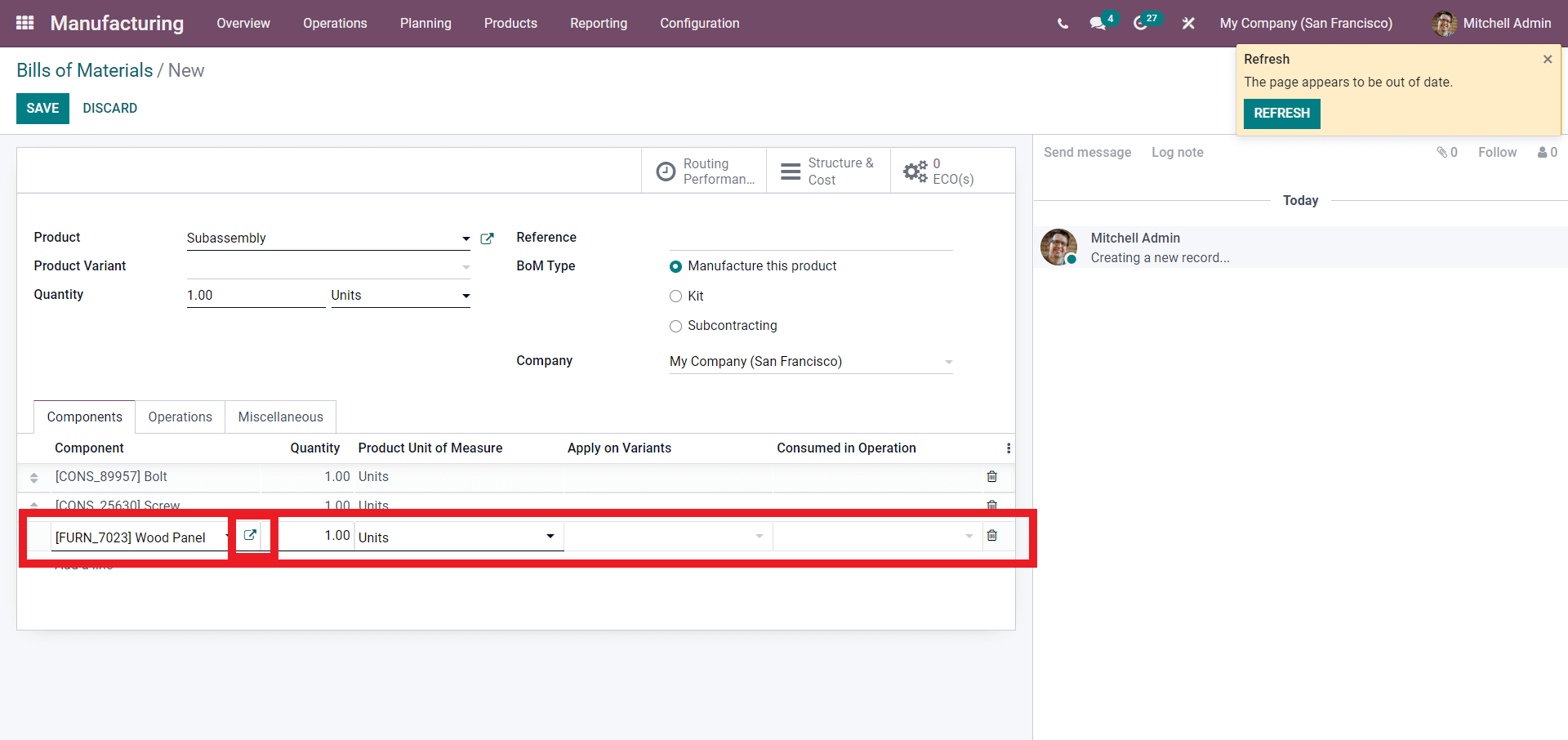
Click on the external link button form here as highlighted in the screenshot given above to configure the feature. A new configuration will open up on the selected component as shown below.
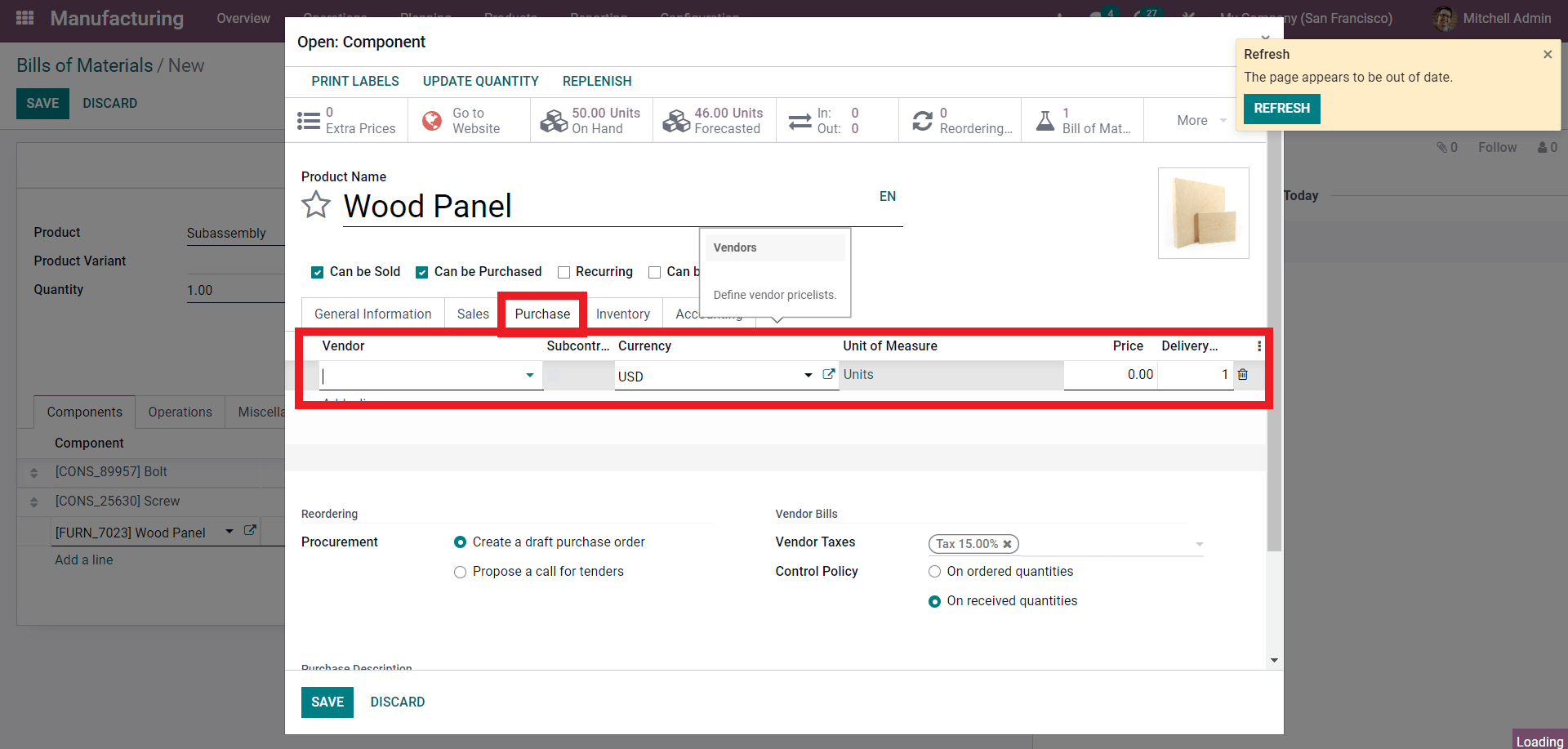
Click on the ‘Purchase’ tab and add the Vendor as shown above from the configuration section.
After entering the details on the ‘Vendor’ go to the inventory to change the Routes of the Operations on the component as shown below.
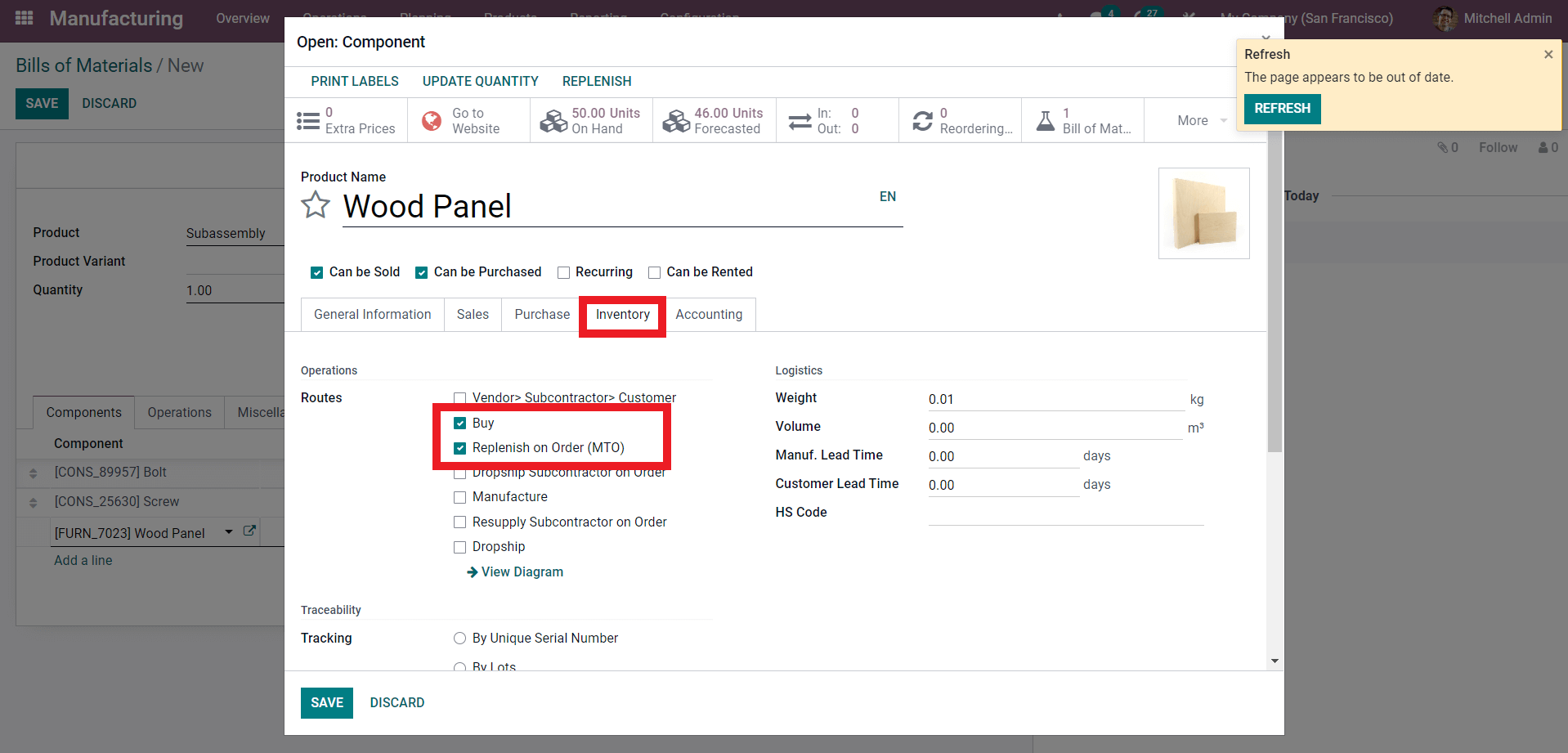
Select the routes as Buy and Replenish on order. After entering and configuring the necessary details click on the SAVE button and from the Bill of Materials do the same to save.
To create a Bill of Materials for the main product select the main product from the Bill of Materials section as shown below.
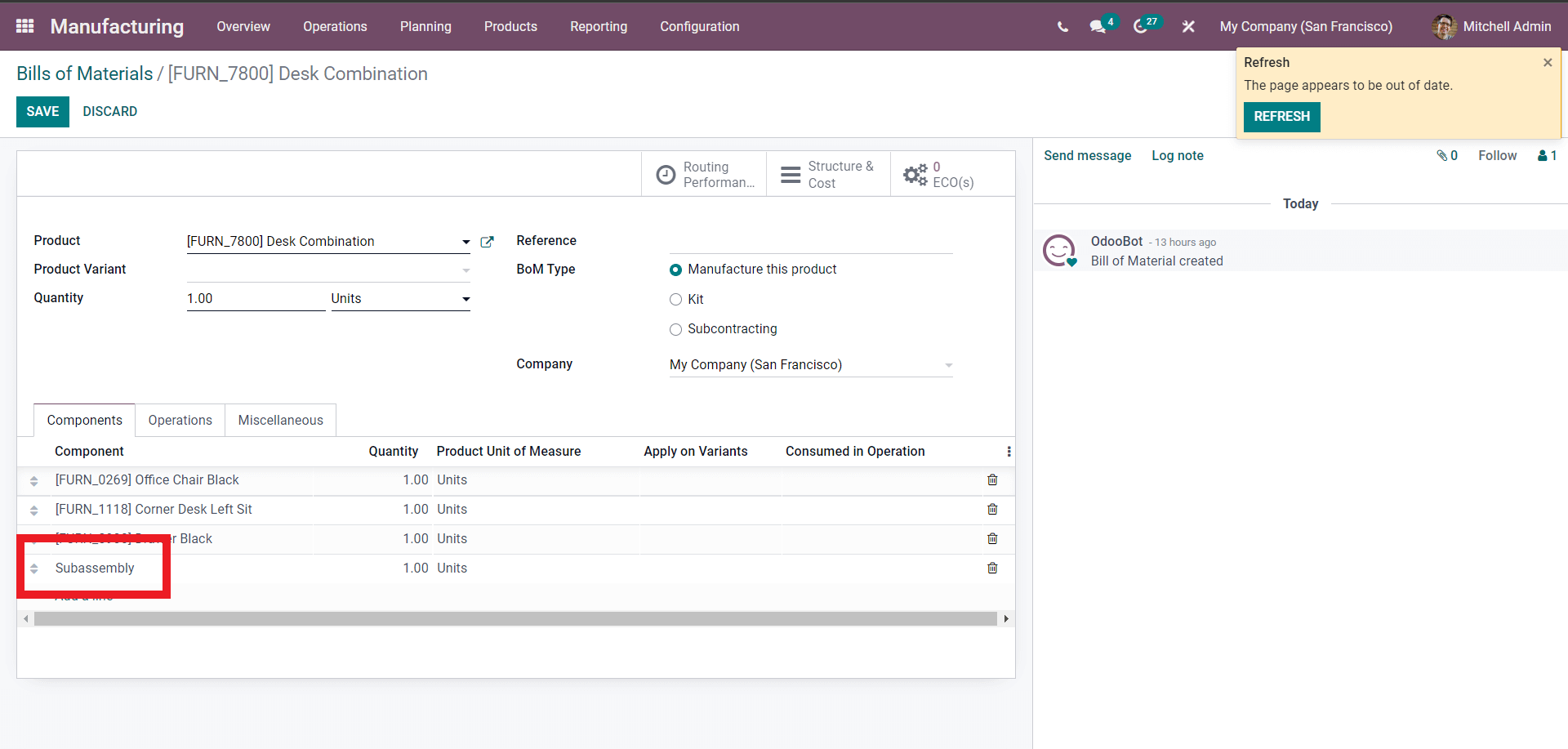
Select the main product and Subassembly as the component as highlighted in the screenshot given above. The new components are required to manufacture the selected main product. After this add the operations from the operations section to define the kind of operation that the selected product has to go through as shown below.
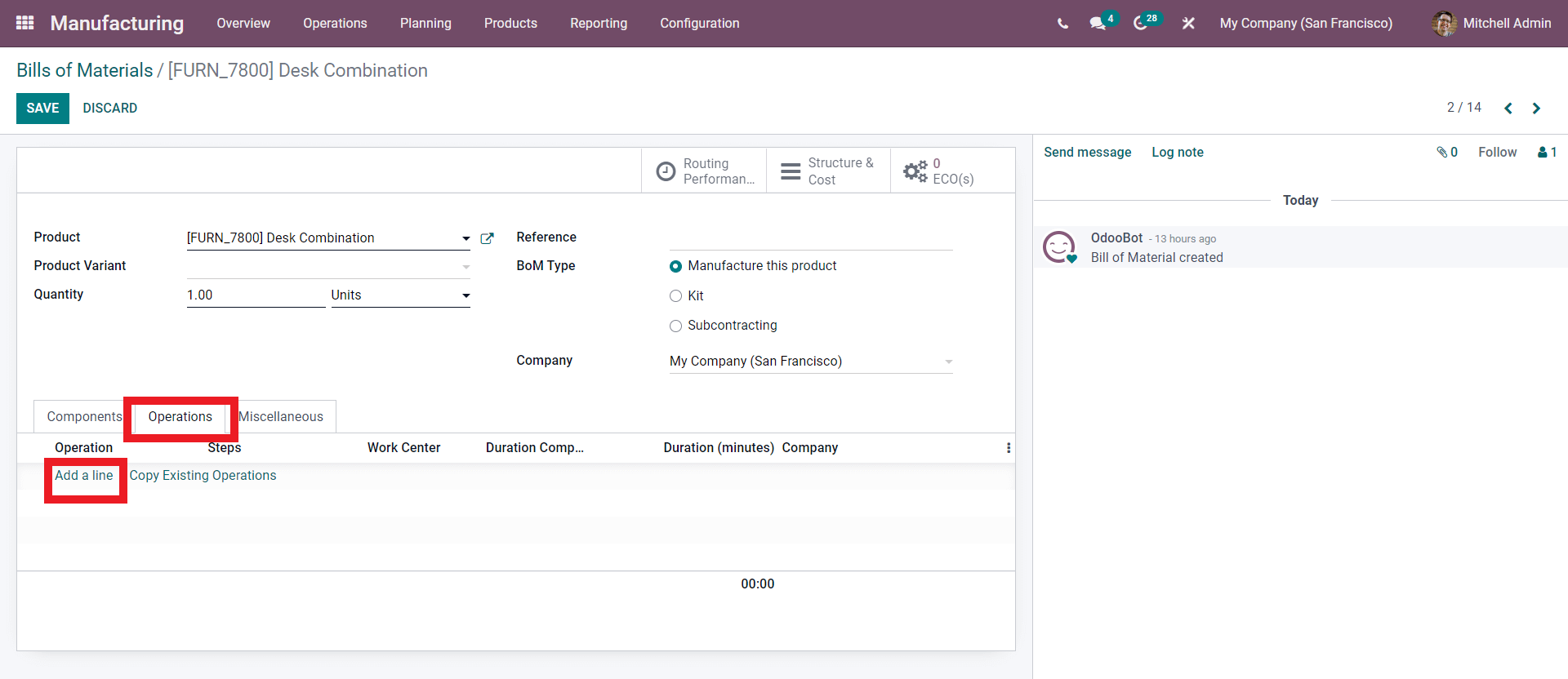
From here either click on the ‘Add a line’ option or you can copy the operation from an existing Bill of Materials. Click on ‘Add a line’ to add the new operation. From the Page opening up after this as shown below, you can configure the Operation.
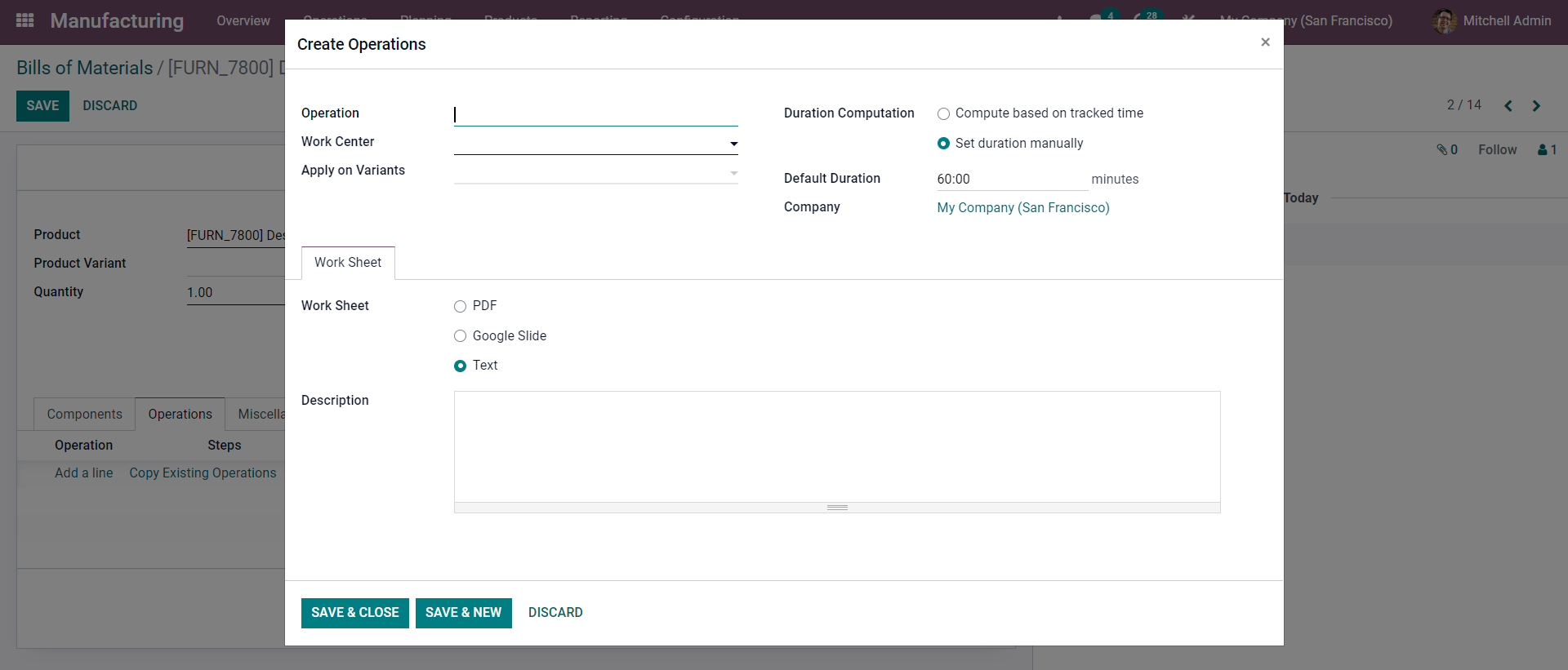
Name the operation and assign the Work center. If the Product has variations you can choose to apply to variants too. You can schedule the duration and if the worksheet is essential for the process then upload them via PDF, Google slide, or Text document and click on the SAVE & CLOSE button.
After this, you have to create the manufacturing order to manufacture the product. Go to the Operations tab from the dashboard of the Odoo 15 manufacturing module and click on Manufacturing orders and then the CREATE button to configure a new manufacturing order. A page will open up with the configurations details for placing the manufacturing order as shown below.
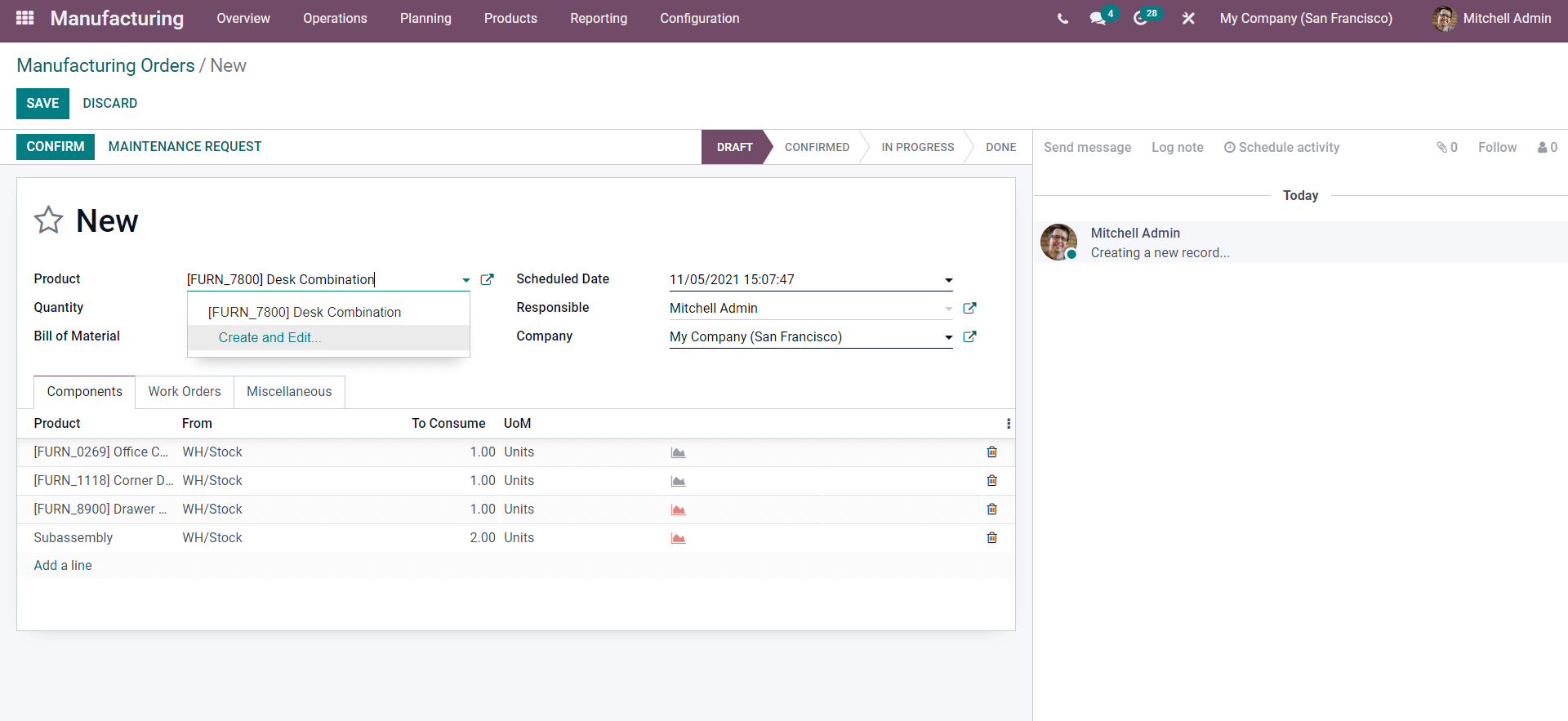
Add the Product under the product section and you can see that the components are added along with the product. Click on the CONFIRM button and the configurations for the next stage will open up as shown below.
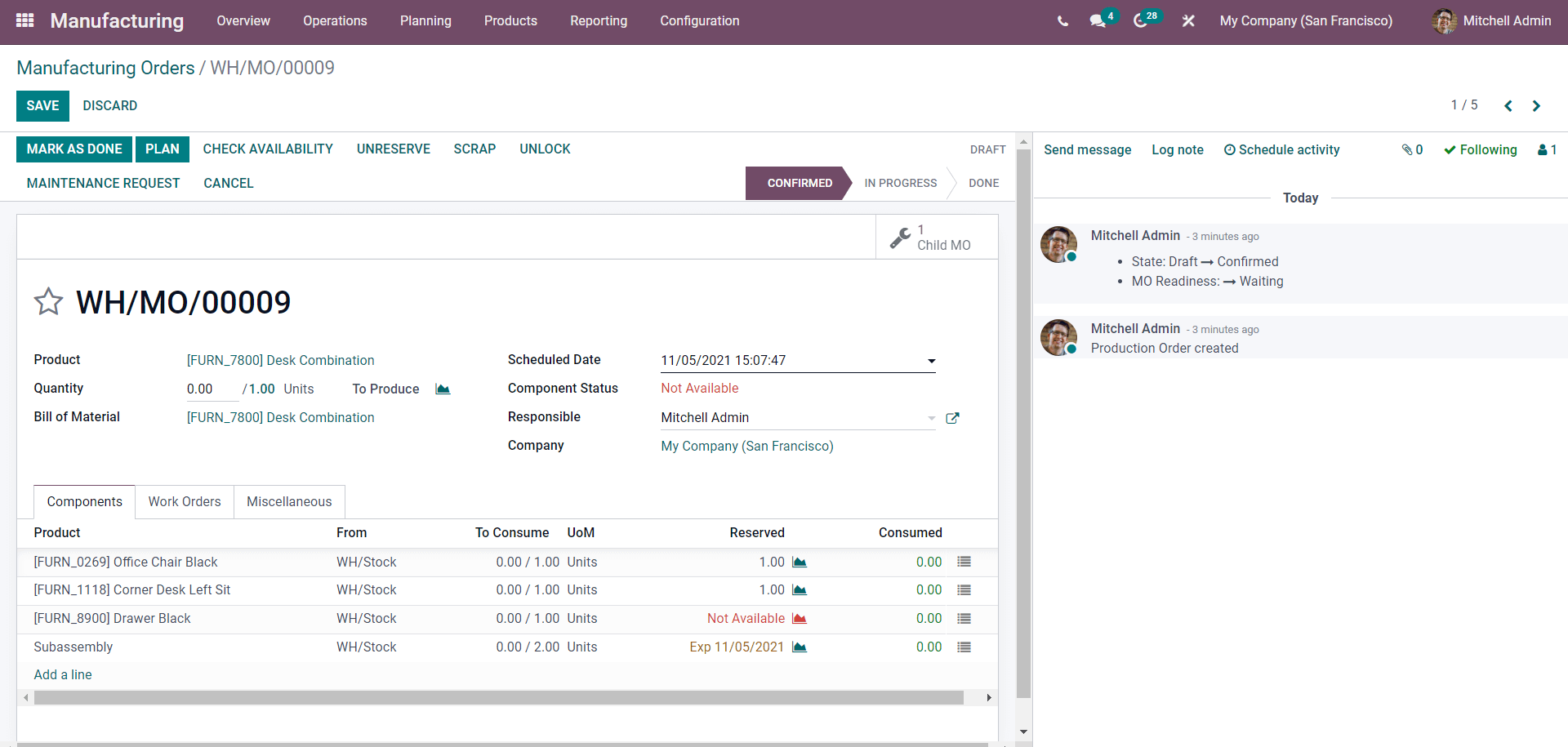
Note that if you fall short in components the page will show under the components section as Not Available in Red as shown above. After receiving the necessary components the process can be continued. Note that the subassembly has to be manufactured first for the main product to be manufactured. You can view the component status on the subassembly from the sections and it will show the expected date by which the process on the components is completed. After this click on the MARK AS DONE button to proceed to the final stage of the entire process as shown below.
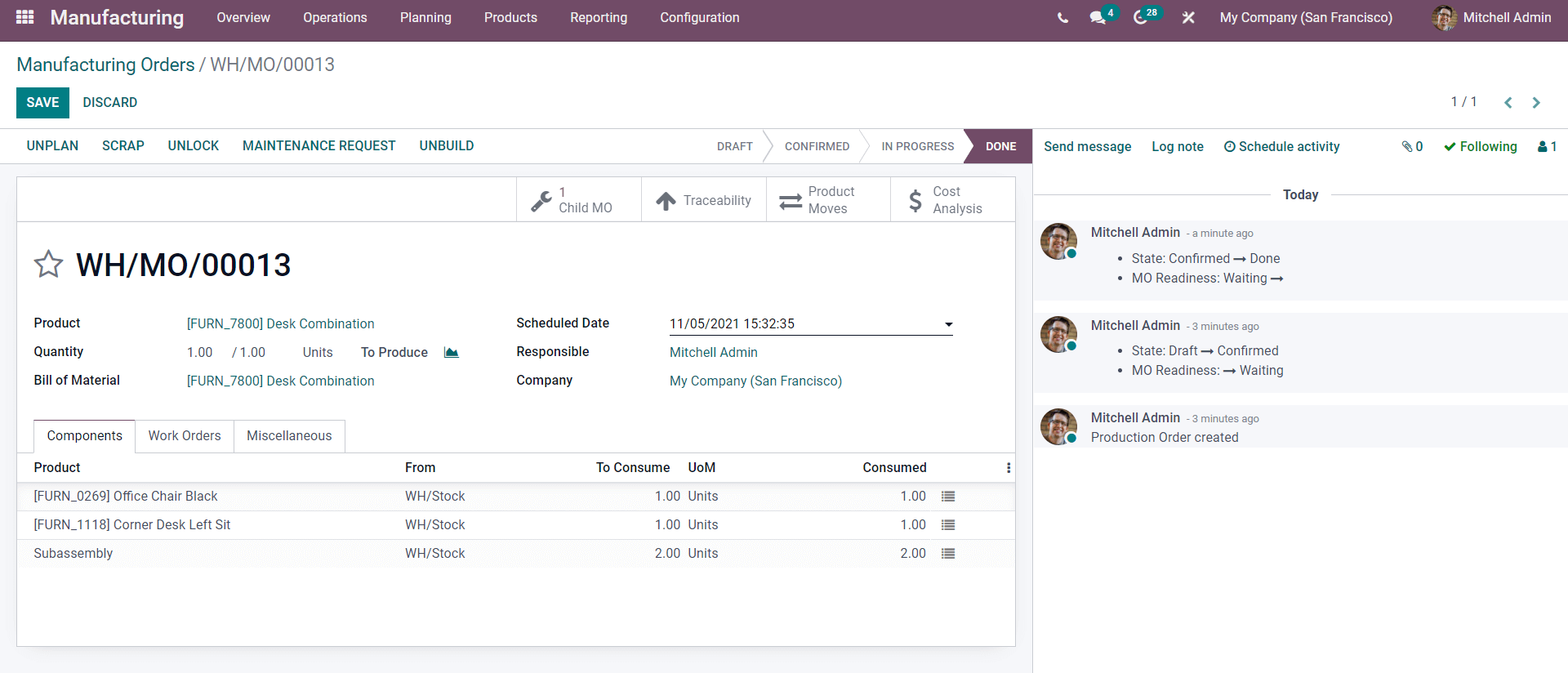
Click on the SAVE button and will let you access the order at any time and make the necessary changes to it. This is how you can manage Semi-finished products with the multi-level-Bill of material.
Importance of Bill of Materials
Bill of Materials can be defined as a document defining the quantity of the materials or the components required to manufacture a whole product.
Bill of Materials is a highly advanced feature in Odoo that has the ability to deal with complex product manufacturing and management functions easily. Using the feature to define and compile your product will allow you to effortlessly carry out any manufacturing-related procedures on a product easily.
The size and the number or the total amount of components required to make the product won’t create a huddle. You can easily go through the items from your product section and add them to the bill of material easily. One of the major advantages of using the feature is that it will allow you to have maximum space for configurations on the products at any stage of the manufacturing process. With the ease of usage and the reliability of the module mixed with the advanced integration of the inventory, you can easily manage and add products as components no matter how complex the production procedure is. This effortless nature of the module and the Bill of material feature will allow you to quickly go through the pre-manufacturing procedures easily without any huddles or blockages.
With the highly integrated nature of the Manufacturing module with other product manage t modules in odoo you can make sure that the necessary components won’t run out of stock when the time comes for manufacturing a product, especially when the product is to be manufactured on an emergency basis. This will allow you to keep your production up and running while at the same time ensuring more customer satisfaction they receive products at the scheduled time and date, which will, in turn, increase your sales to a huge extent.