A finished product can be sold only after it is manufactured using the required components. An enterprise that deals with manufacturing and trading, firstly purchase the raw materials, later process them and produce the required product out of the raw materials and finally sale the finished products afterward in the market. We know that the product sale is mainly dependent on its market demand.
The main challenge that any manufacturing enterprise encounters are the ample number of finished products in hand, but unable to sell them due to their less demand in the market. One solution to curb the above situation is to manufacture the product according to the demand. But there arises another issue with raw materials or component products. The raw materials when stored for a long time often lose their quality and get damaged. In either of the above situations, the ultimate result is the damage of the products and their huge loss.
The effective functioning of a manufacturing and trading enterprise can be accomplished by manufacturing the products only after the creation of a sale order. This enables to purchase the required amount of raw materials which results in less wastage, improved quality and increased profit. Now, a hurdle being encountered that is “How to achieve this?”. As an ERP software, Odoo comes up with an automated feature that creates a purchase order and manufacturing order simultaneously upon the creation of a sale order.
How to configure this setup?
From the Odoo Apps, install the Sales, Purchase and Manufacturing apps respectively.
1. Create a product that has to be manufactured and the component products required to manufacture the given product.
Go to Sales > Products > Create.
[Please ensure that the product type of the component products should be Stackable. Also, they can be purchased and sold as a single product if needed. So, enable the fields Can be Sold and Can be Purchased.]
2. Select the product category as Consumable in the General Information tab since the final product is not accounted in the stock.
3. Disable the Can be Purchased field since the given product is manufactured from its component products.
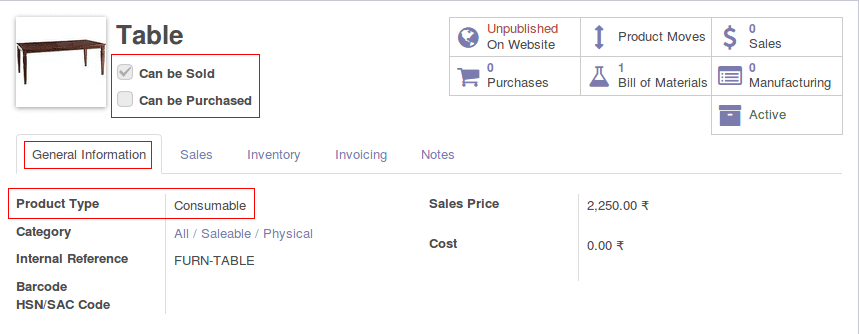
4. Enable the routes Manufacture, Make to Order in the inventory tab.
5. Create Bill of Materials (BoM) comprising of the component products along with their quantity for the parent product created. When creating a BoM, make sure that the product name is the same as the parent product created and the BoM Type selected is Manufacture this Product. Bill of Materials can be created in two ways.
i. Clicking on the Bill of Materials button in the product page.
ii. Go to Manufacturing > Master Data > Bill of Materials.
6. Create a sale order with the product which is to be manufactured.
7. Go to Manufacturing > Operations > Manufacturing orders.
You can see that a manufacturing order is created for the selected product in the sale order.
8. Go to Purchases > Purchase > Requests for quotation.
You can see that a purchase quotation is also created for the component products of the selected product under the sale order.
9. The selected product can be manufactured only if the component products are available. They become available only when they are purchased and added to the stock. Confirm the purchase order and receive the products.
10. Validate the products in stock.
11. Once the components are available in the stock, the Check Availability button disappears which indicates that the manufacturing process can be started.
12. You can click the Produce button when the manufacturing process is started the status changes to In Progress.
13. Once the manufacturing process is completed, you can mark it as done/completed by clicking the Mark it as Done button and the status changes to Done. Once it is done, you can process the sale order afterward.