Manufacturing is simply the production of new products using some raw materials, but in reality, this is a complex process. Many raw materials are used during the production process, and there may be numerous operations. However, there are occasionally opportunities to produce some byproducts alongside the primary product. In these circumstances, the by-product can also be expensive. With the help of the Odoo 15 Manufacturing module, such production and costs may be simply managed.
Suppose we were producing product B using component A, and as part of the production process, a new byproduct, C, was also created. Here, we produced product B, as we previously stated, byproduct C was also produced, although there were costs associated with the manufacturing of byproduct C. The cost of producing product B includes the production cost of the byproduct. With the help of the Odoo 15 Manufacturing module, such production and costs may be simply managed.
Let's design the goods to be produced as well as the components used in the production process. Go to the products tab and create new products there for that. The manufacturing item, in this case, is a STORAGE BOX, which costs $300. From the Inventory tab, the product's route is specified as manufacturing.
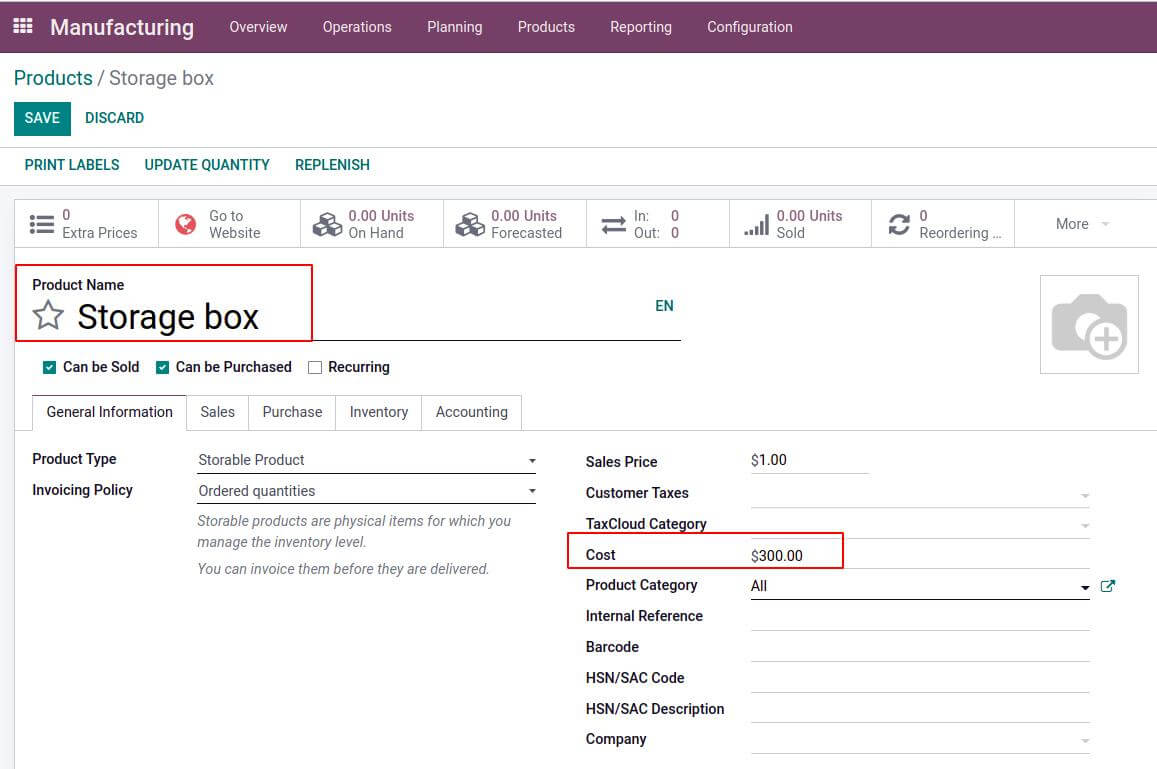
Let's start by making the first component, which we'll call the Ply Layer, which can be a storable product. And the product's price is listed as $100.00.
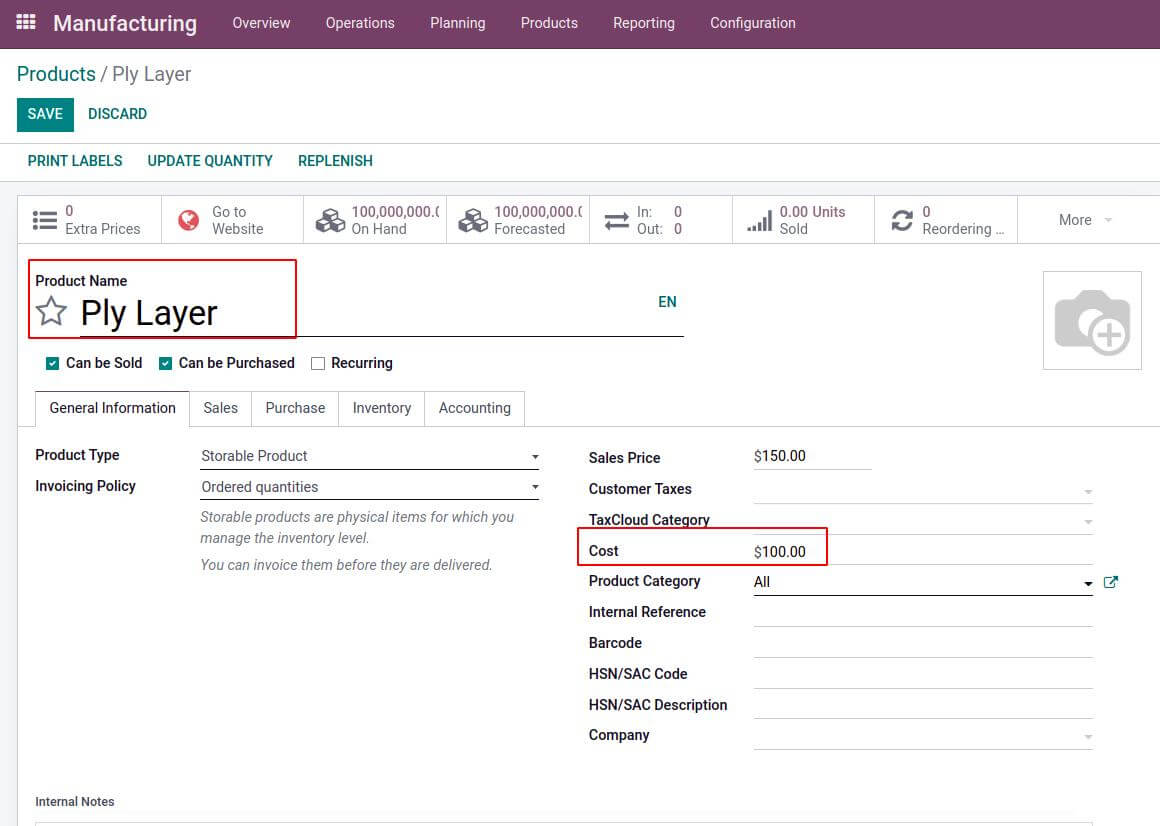
Then the second component is also a storable product. This costs $100 and is a Wear Layer.
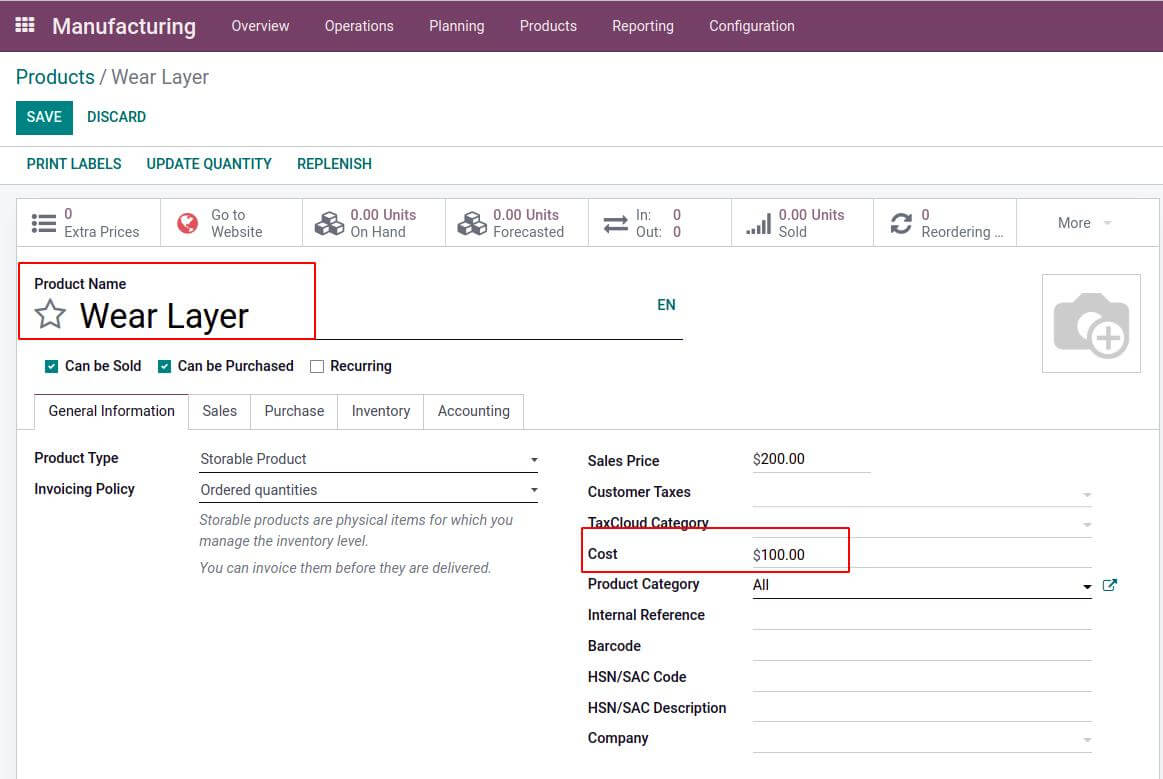
Before beginning the process, various options must first be configured. Therefore select the settings option from the configuration tab. There are numerous options on that page. The Work Orders and By-Products should be enabled. Work Orders assist in processing certain operations at certain work centers. Enabling the By-Products option will allow you to specify any byproducts that were produced alongside the final product throughout the production process. Once the option to save the changes has been enabled, click the SAVE button.
Configuration > Settings > Work Orders and By-Products > Save
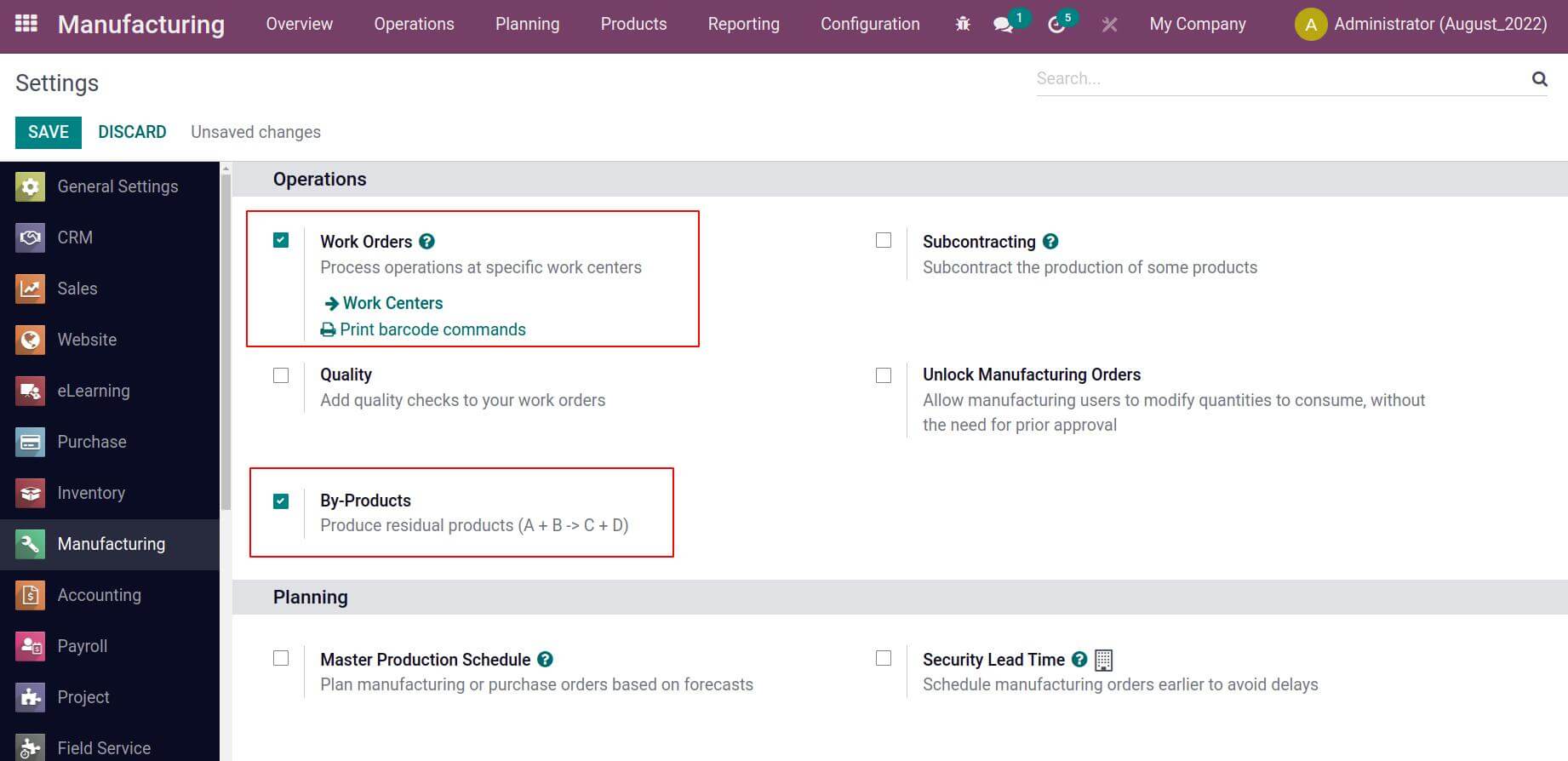
The first step in every production process is to establish a workplace. A work center is thought of as the location where all operations are carried out. Therefore, we must first set up a work center for our production process. Let's click the configuration tab's work center option.
Configuration > Work Orders
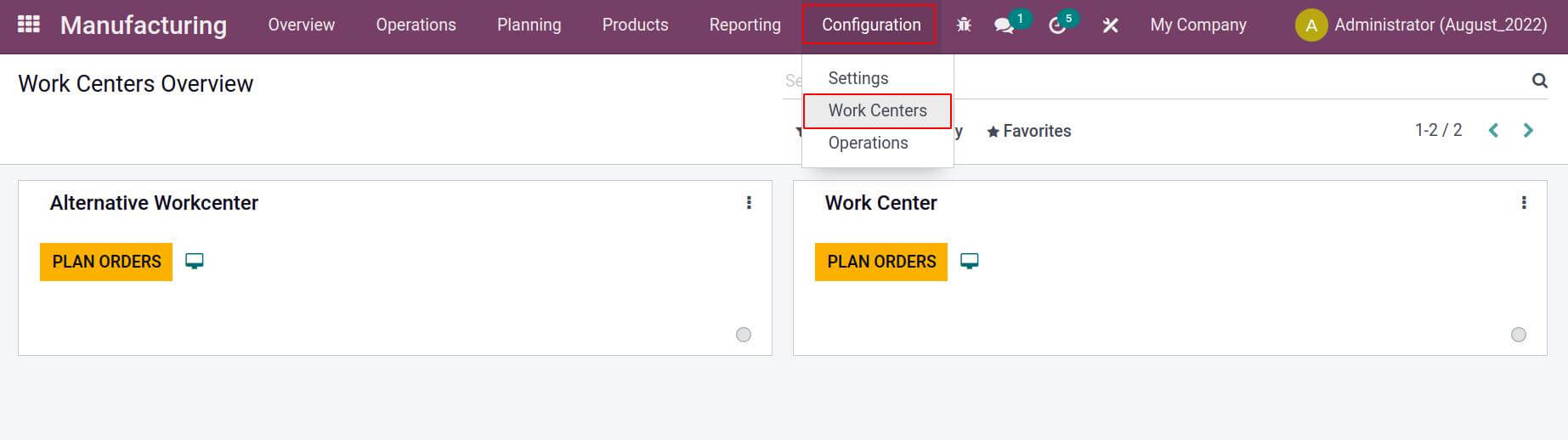
The newly developed work center was now open. The name, Tag, Code, Working Hours, and Alternative Workcenters for the Workcenter are displayed there. There, the costing data for the work center can also be specified. The cost of the work center is provided here. The rate increases to $1,000 when the work center works an hour. We can specify the Time Efficiency, Capacity, and OEE Target in the Production Information. Additionally, it is stated here how long it will take to set up the workspace and how long it will take to clean it.
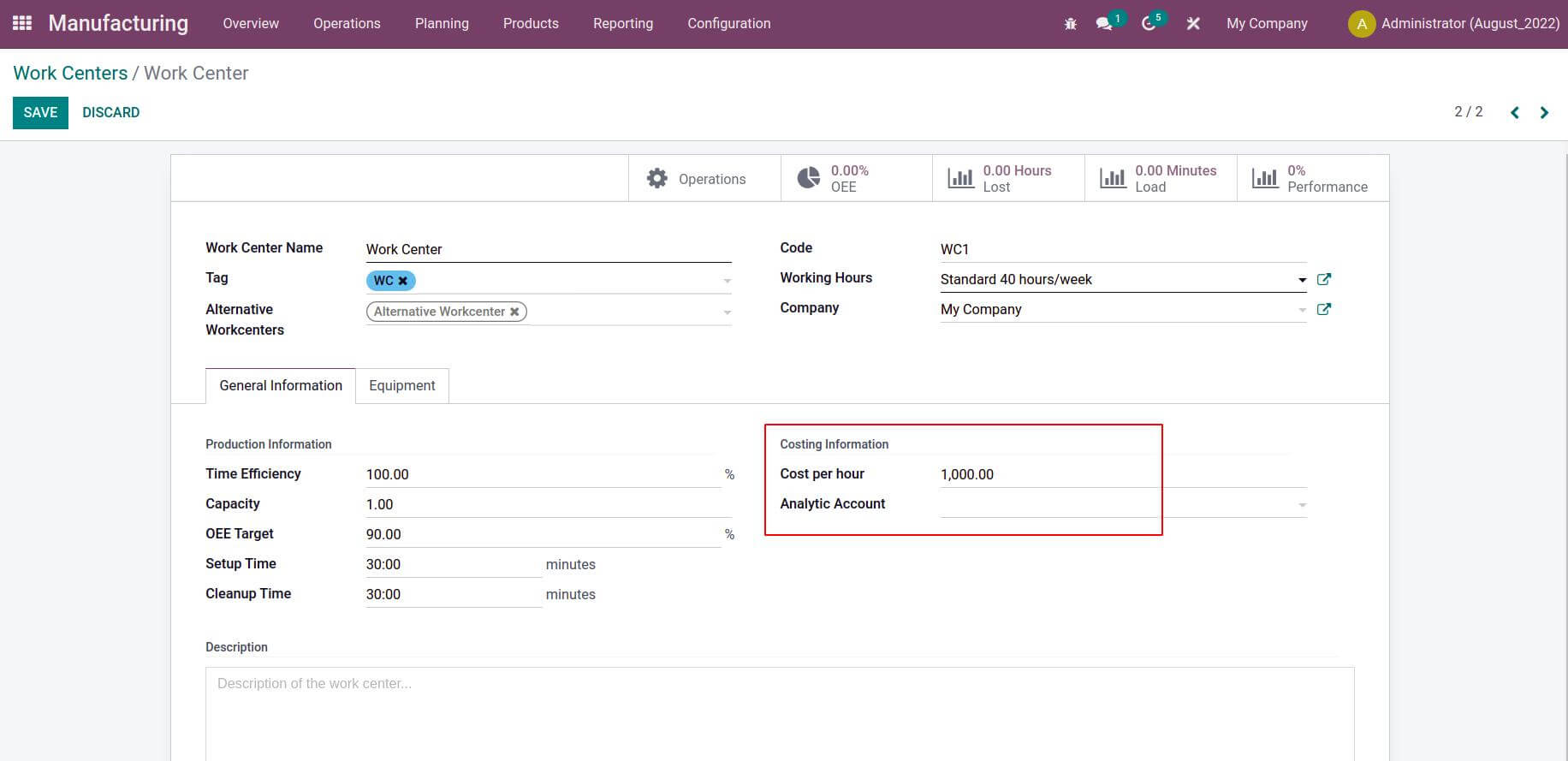
Before we begin production, let's construct a bill of materials. As an example, here is a bill of materials for the product "STORAGE BOX". Go to the product tab and select Bill of Material for this. By default, every created bill of materials is displayed; to create a new one, click the CREATE button.
Product > Bill of Material > CREATE
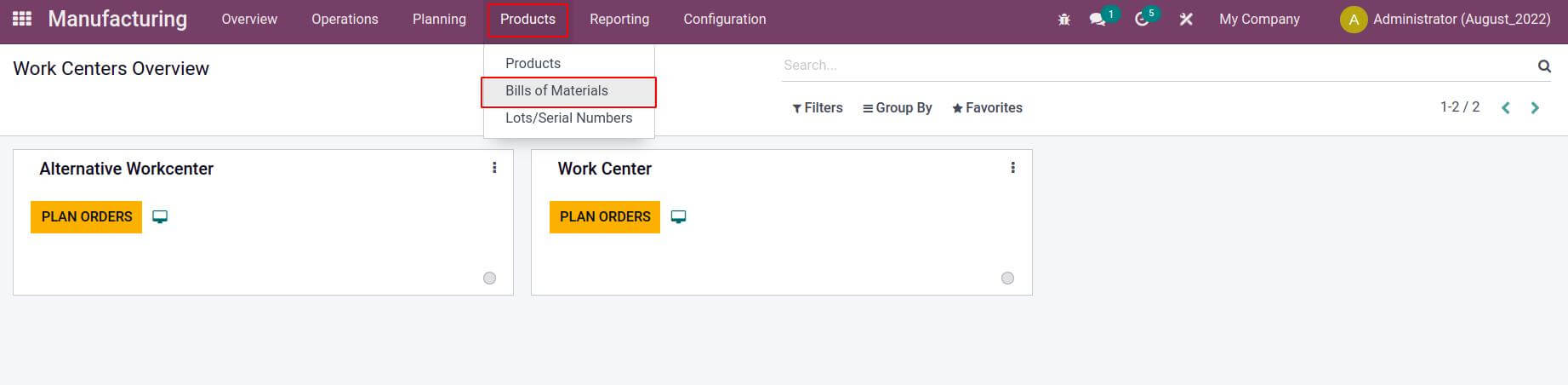
The name of the product, the components, and the production processes are all listed in the bill of materials. A STORAGE BOX with one quantity is the item we're going to make in this case. If required, include the Reference. Choose the BoM type as Manufacture this product, and add the list of raw materials and their quantities to the components tab.
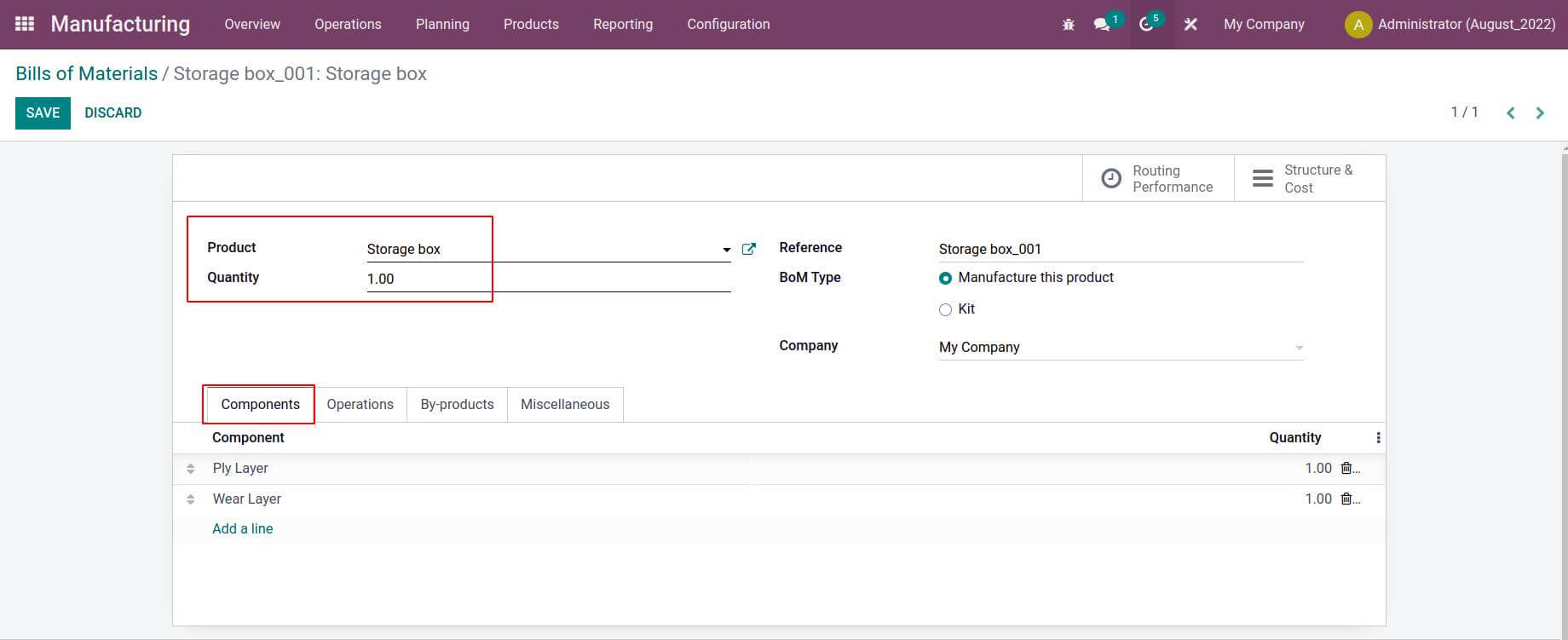
Go to the operations tab next. By selecting Add a line, new operations may be created, and by selecting Copy Existing Operations, existing operations can be copied. The operation name, sequence number, and other information must be specified when creating a new one. There is an option here called Work Center, where we can specify the workspace where the action was carried out. Mention how long it took to complete the operation. This can either be computed using tracked time or the duration can be explicitly set. Here, we manually set it to 60 minutes.
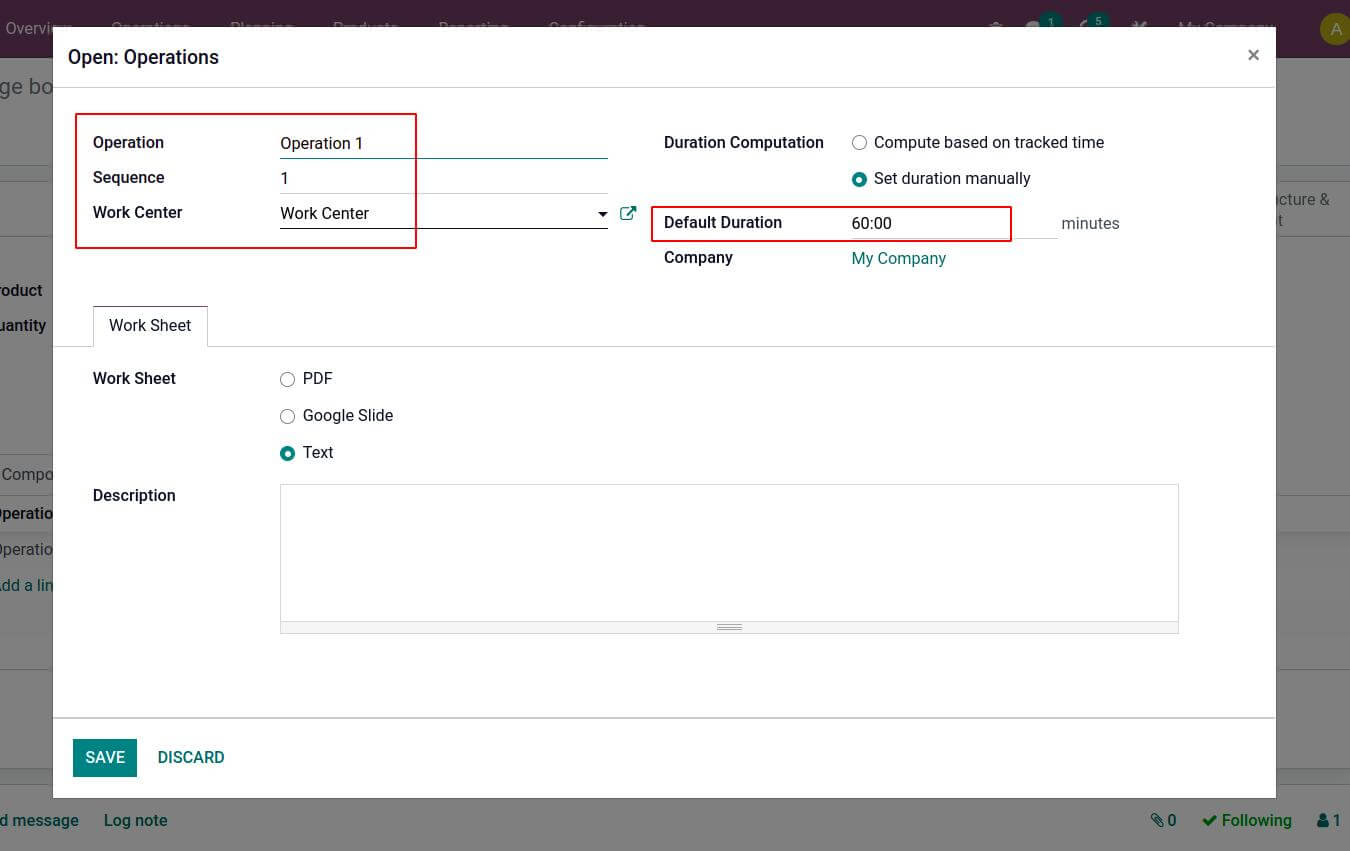
Now the operation is added in the Operations tab.
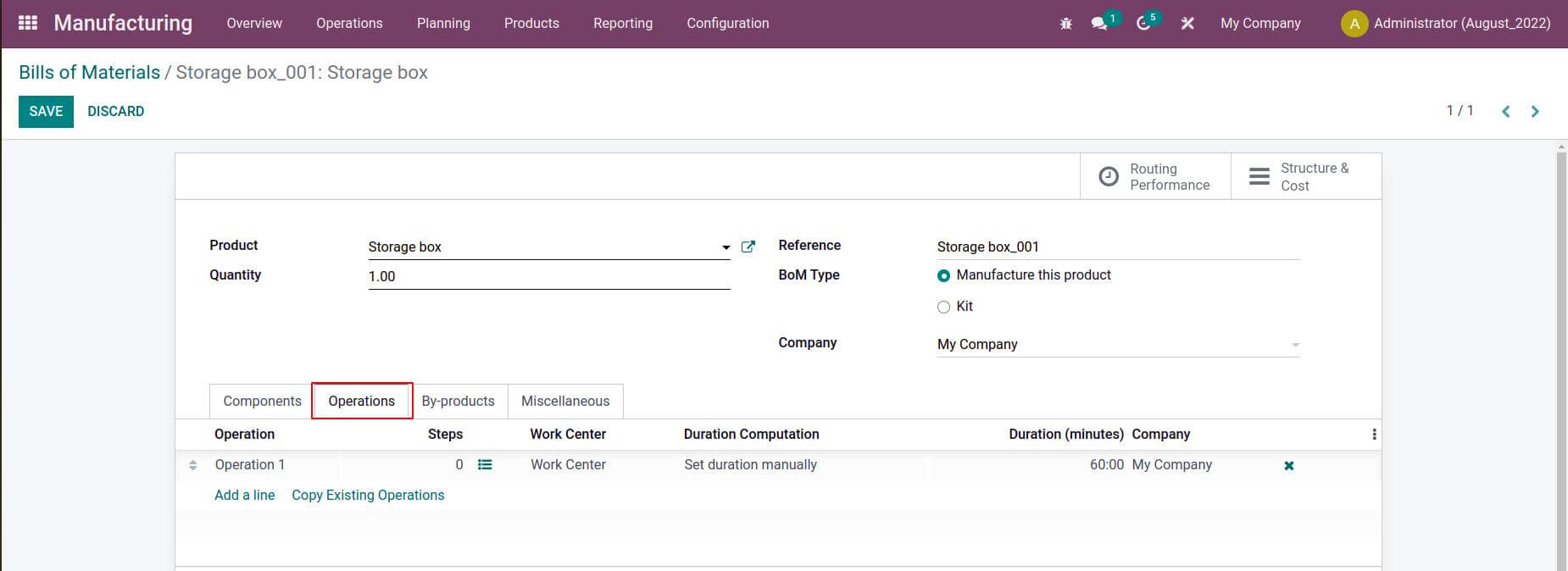
We can define which product is created as a byproduct during the manufacturing of STORAGE BOX in the By-products tab. A wooden Panel is listed as a byproduct here. Another choice is to give the Cost share in percentage. 10% is indicated, hence 10% of the overall cost is taken while producing the byproduct.
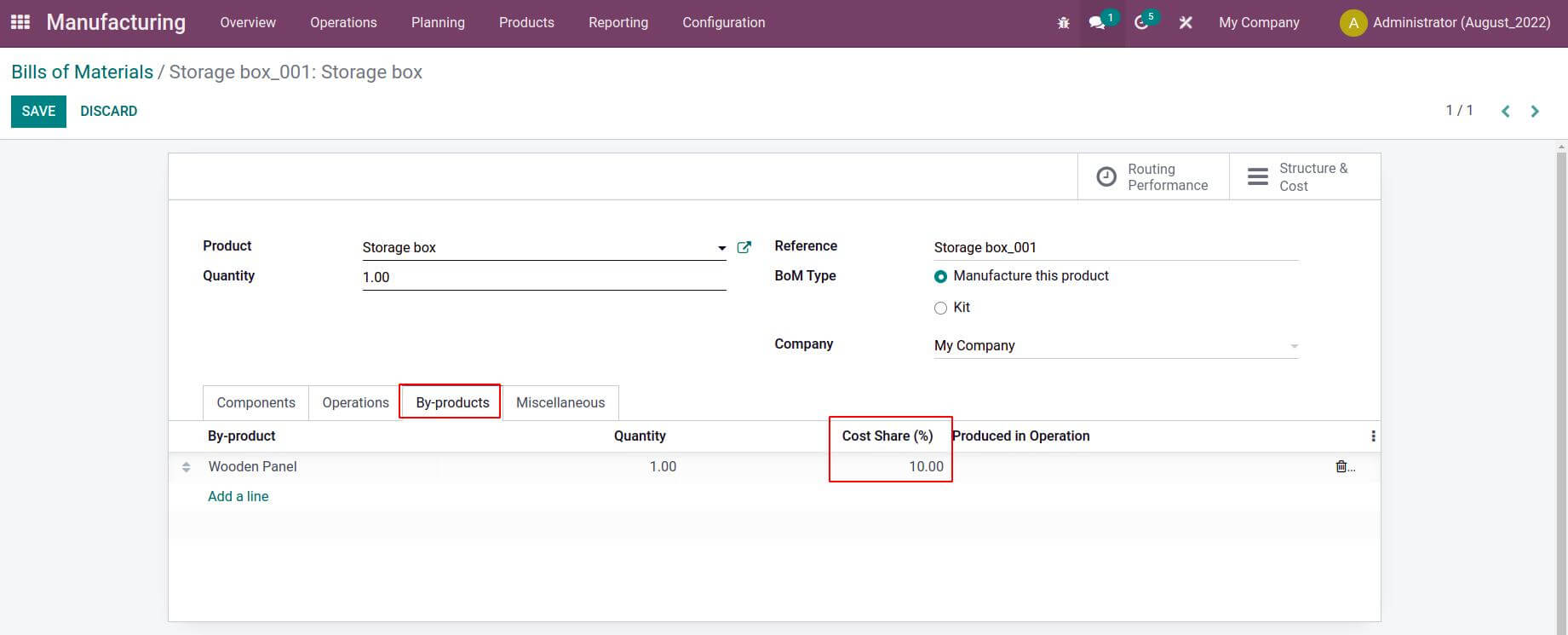
Just save the bill of materials after providing the necessary details. Two smart tabs are displayed; one is labeled "Routing Performance" and the other "Structure & Cost." To learn more about the estimated costs associated with producing the product, let's examine the smart tab Structure & Cost.
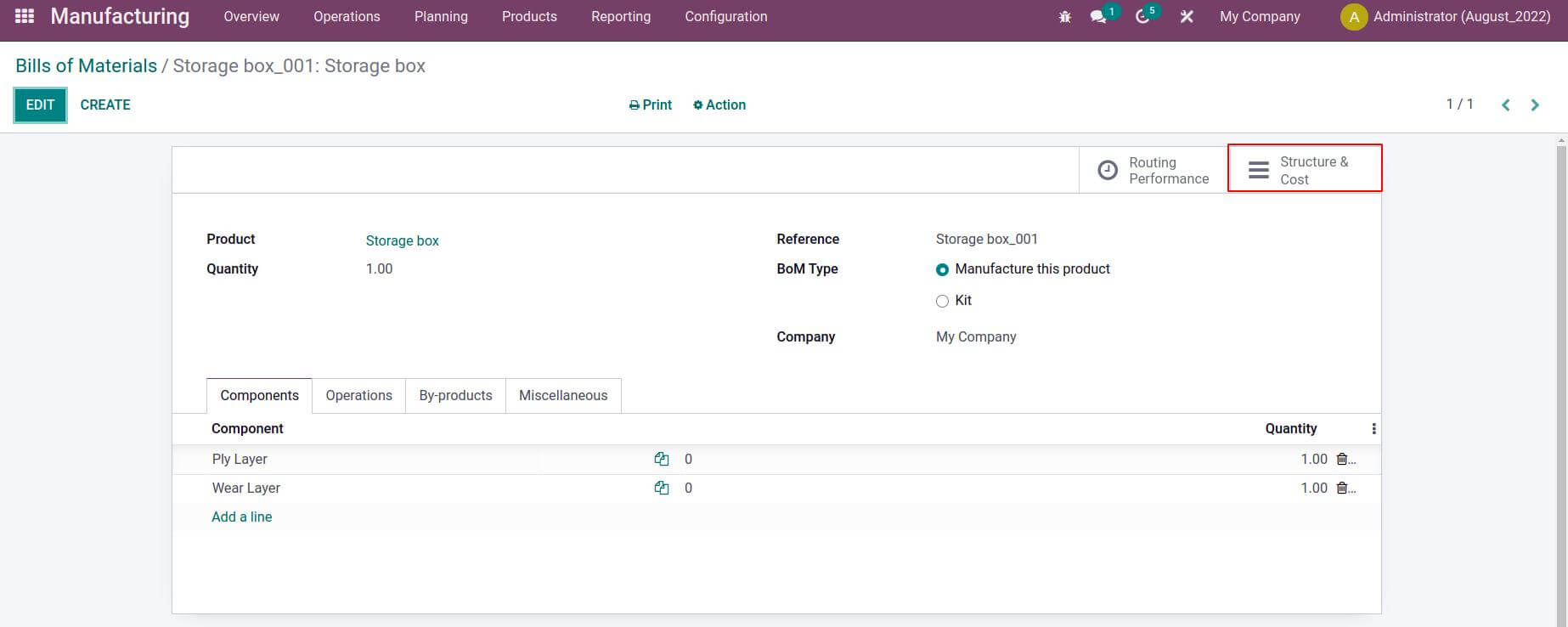
Here the cost of producing one product is given. Here, Ply Layer and Wear Layer are two of the components used. Ply Layer and Wear Layer each cost one hundred dollars. Consequently, the components cost $200 in total.
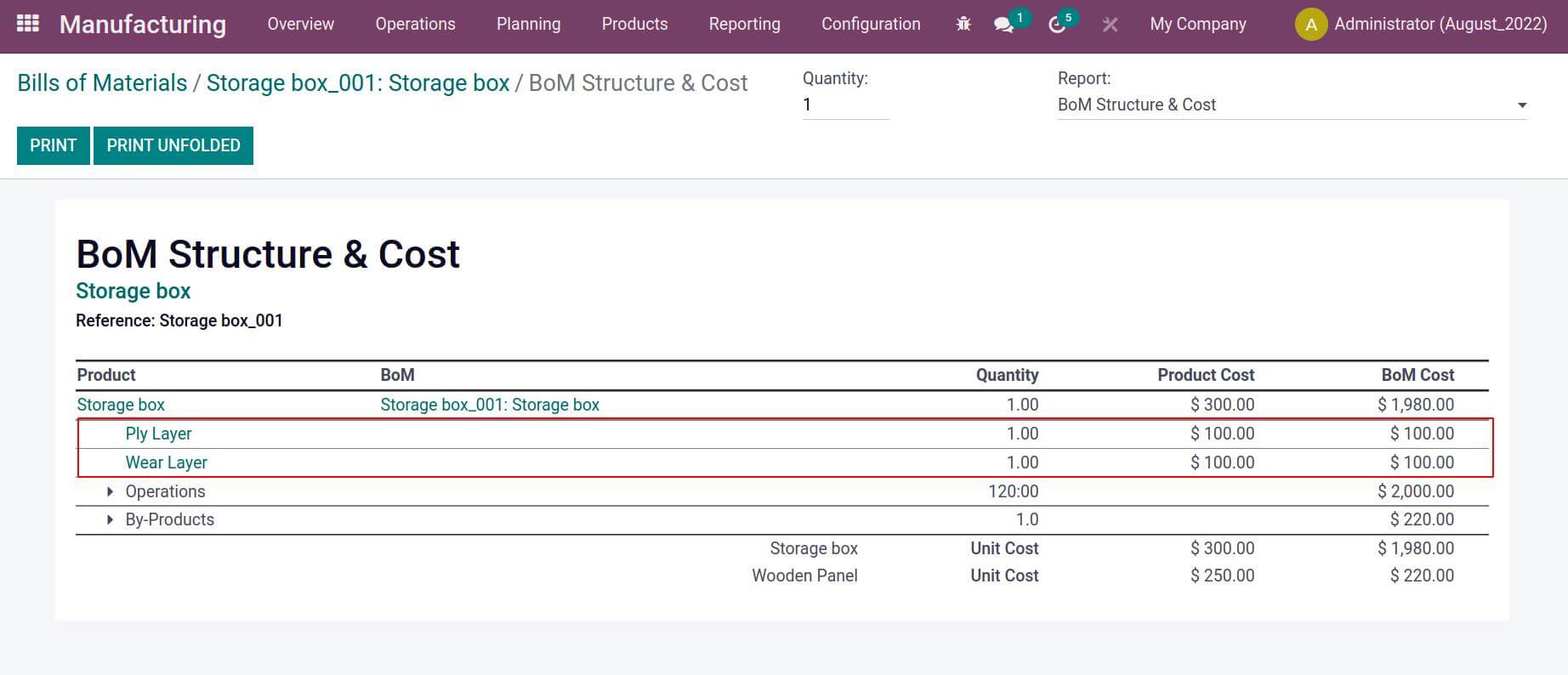
The cost of operations calculation comes next. In this case, only Operation 1 has been added. The operation is expected to take 60 minutes to complete. As we already indicated, the procedure is carried out in the Work Center, which requires 30 minutes for setup and 30 minutes for cleanup. The sum of the operation's duration, setup time, and cleanup time is 120 minutes. The cost per hour for the Work Center is specified as $1,000.00. Consequently, the operation's overall cost is $2,000. ( for 120 minutes which is equivalent to 2 Hours). The cost of each component and the cost of operations are added to calculate the total cost. Indicating that 200.00 + 2,000.00 = 2,200.00.
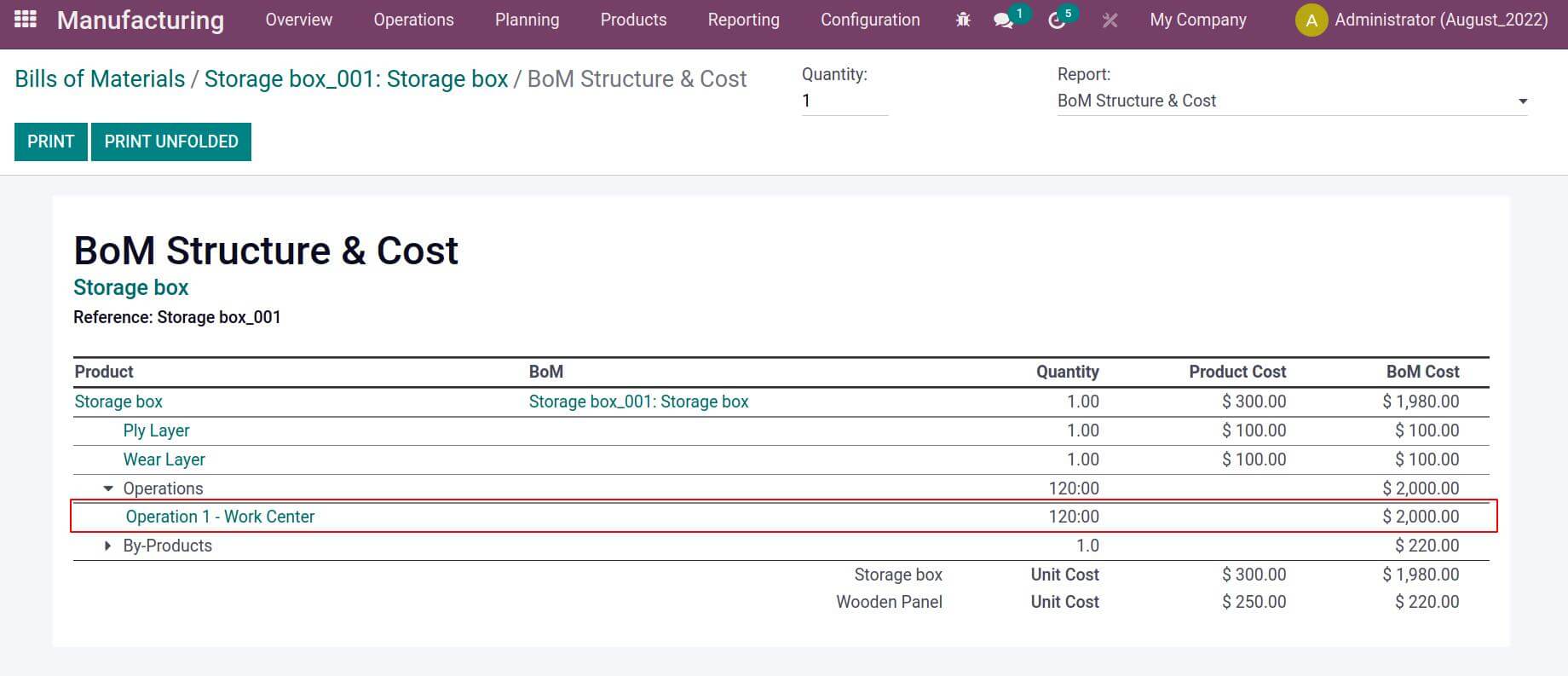
10% was the cost share that was mentioned in the bill of materials. Therefore, the cost of By Product is estimated as 10% of the overall cost. It indicates that 2,20.00 is 10% of 2,200.00.
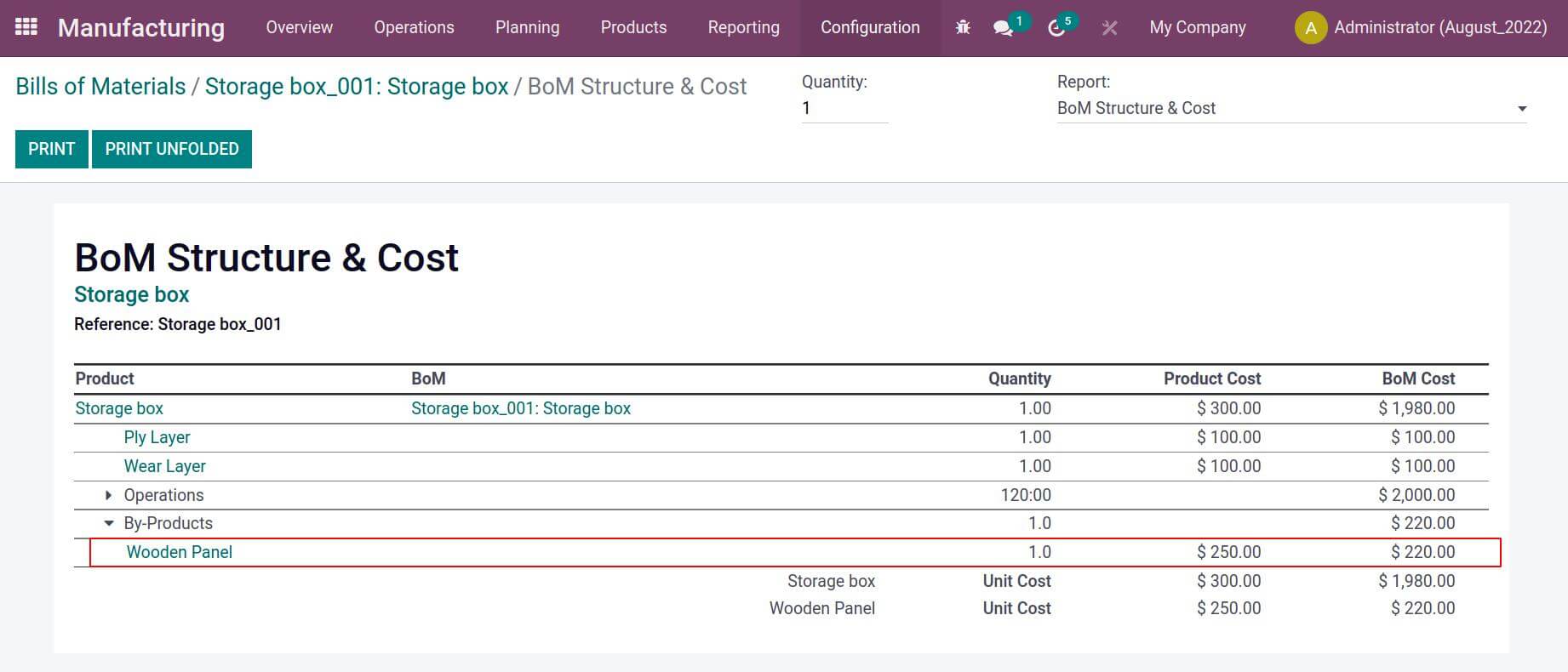
The cost of the product is calculated here as the difference between the overall cost and the cost of the individual product, therefore the cost of the storage box is 2,200.00-2,20.00=$1,980.00.
Here, the costs for the products Storage Box and Wooden Panel are 300 and 250, respectively. Finally, this section displays the Bom Structure & Cost for producing 1 quantity of the product.
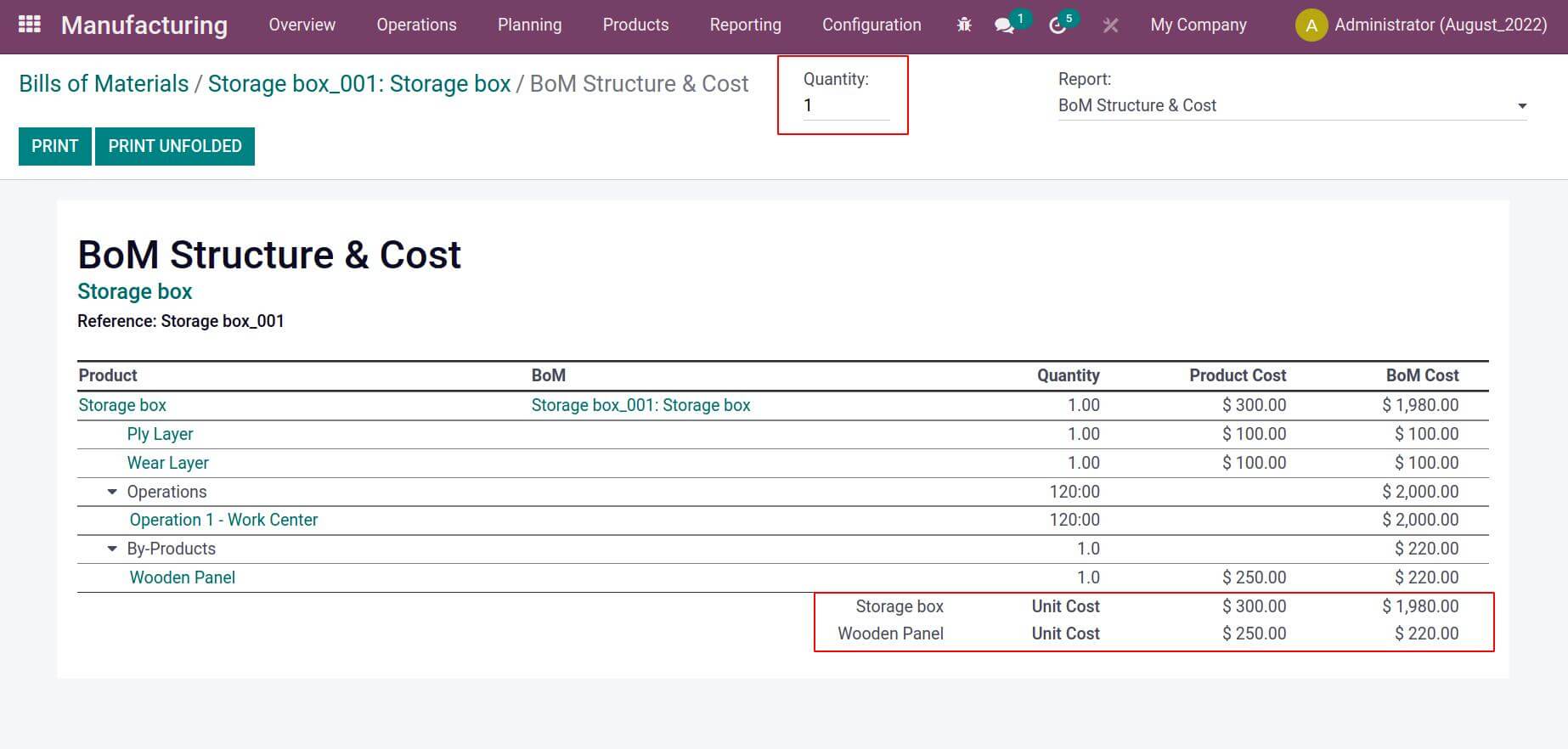
Here, we used the parts Ply Layer and Wear Layer to create the product STORAGE BOX. and a new wooden panel byproduct. The cost of the byproduct is 10% here. Here, the 10% cost is included in the cost of the product STORAGE BOX.
Let's make an order for the product's manufacturing. For that, select the Manufacturing orders under the Operation tab. Create a new manufacturing, then select the Product Storage Box option to have the Bill of Material selected for you. and then confirm.
Operation > Manufacturing Order

Now let’s check how production journal entries are affected. For checking the journal entry, move to the Accounting module. Choosing Journal entry from the Accounting tab after clicking on it. There, we can see the journal entry that was created following the manufacturing.
Accounting > Journal entry
The cost of both components is 100, according to the entry there. So, 200 is the total cost of the components. 10% of $200 is 20, which is chosen as the cost of the byproduct wooden panel because the cost share is 10%. And the balance of the cost (200-20=180) is used to calculate the cost of the product storage box.
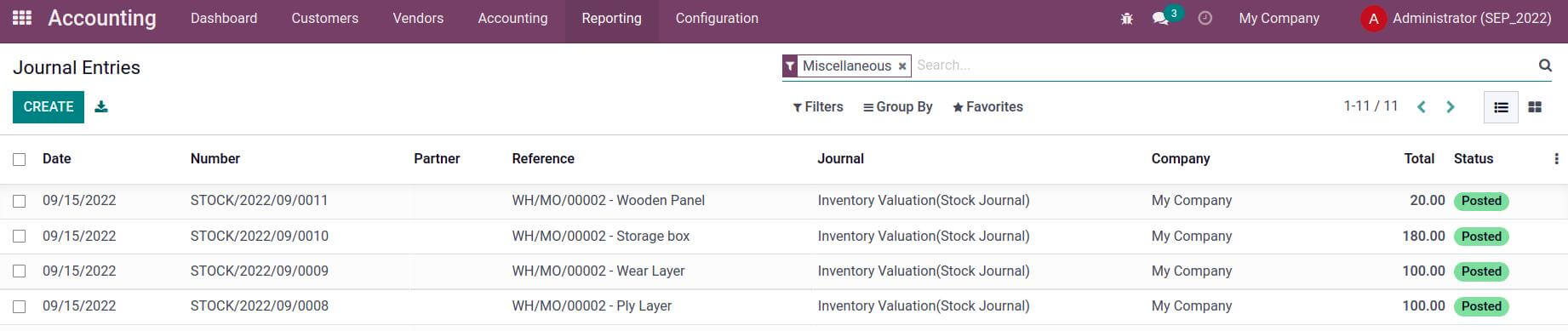
The cost share is then visible in the journal entry as well. Consequently, a percentage of the overall cost is allocated to the production of Byproduct as well.