Cost computing of the finished goods is a challenging and difficult job to conduct. There are different types of costing methods like Standard, Average or Real Price, used for computing the costs of goods.
Under the manufacturing module, the cost of finished goods can be computed based on the components presented in the bill of materials, the hours spent at the work centers, the labor, the electricity or any direct or indirect cost experienced during the production stage.
Now let us see how to compute the cost of finished goods based on the cost of its components.
Prior to the action, one needs to open the Manufacturing module and select a product which you want to manufacture. Later create a bill of material for that product.
One has to set up a “final” product, to be manufactured, and set its cost as zero. Then set up a Bill of Material(BoM) for this product, and build this product via the manufacturing module.
As a next step, create a BoM for the final product. Here, in this case, Table is the final product and Table Top, Table Leg, Bolt and Screw are the different components of the final product.
To create BoM, go to the Manufacturing module.
Master Data -> Bill of Materials -> Create a new one for the product Table, just click on the “Create” button and add product name and components used to manufacture a Table. Also set or create routing for manufacturing this product and Save to mark the changes.
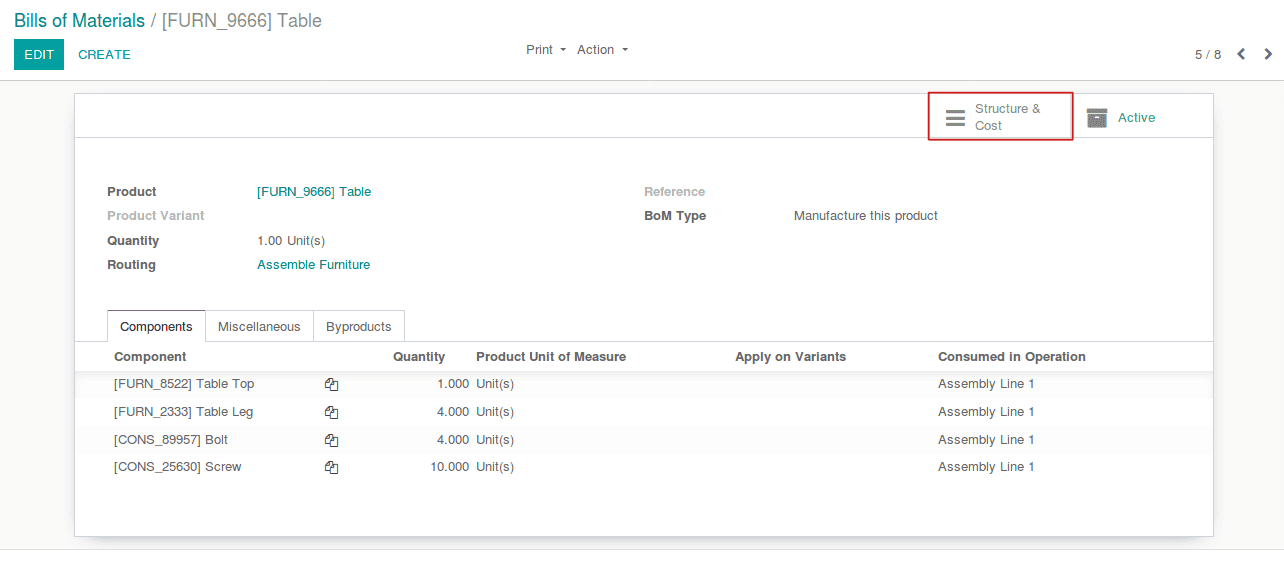
To analyze the cost of finished product from the BoM, click on the button Structure & Cost.
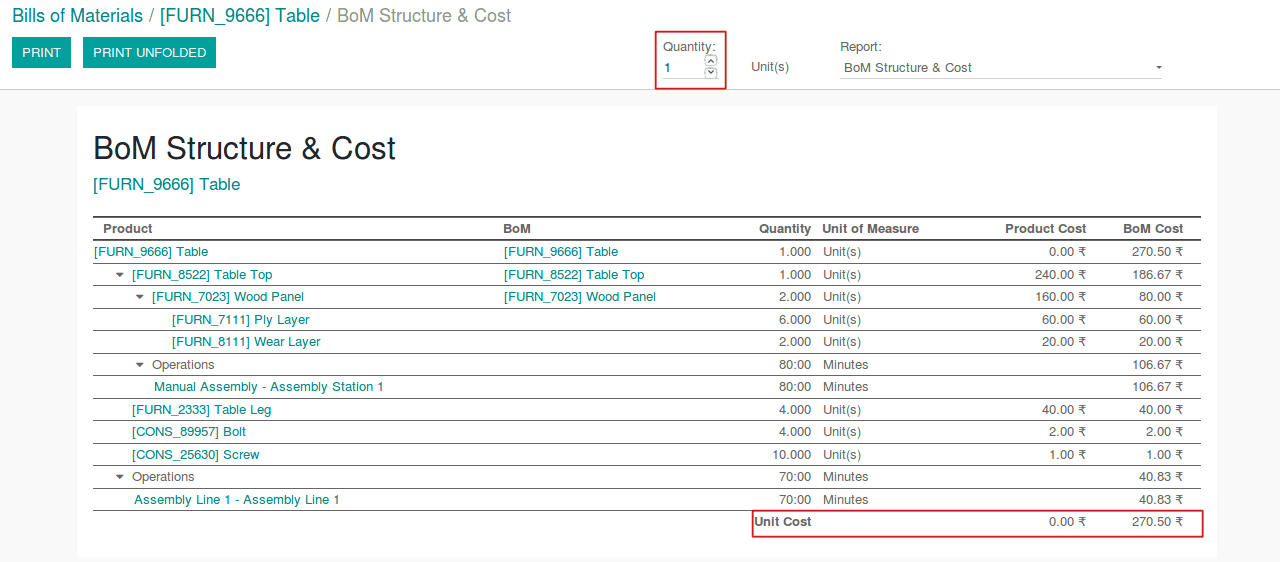
This is a BoM for producing a single quantity of the finished good. However, one can change the number of quantities for more production and also create BoM for that much quantity.
Under the creation form, one can find some columns containing some data.
Product: It shows the name of the finished product and the list of products and operations that are used for manufacturing the final product.
BoM: The column lists out the product name that is having their own bill of materials.
Quantity: The column displays the number of quantities/time used for each product/operations.
Unit of Measure: It is the magnitude of the quantity.
Product cost: Actual cost price of each product.
BoM Cost: Cost calculated through the bill of materials.
Upon the BoM creation, route of Table (finished product) gets set as Assemble Furniture.
Upon clicking on Assemble Furniture, a wizard gets opened like below:
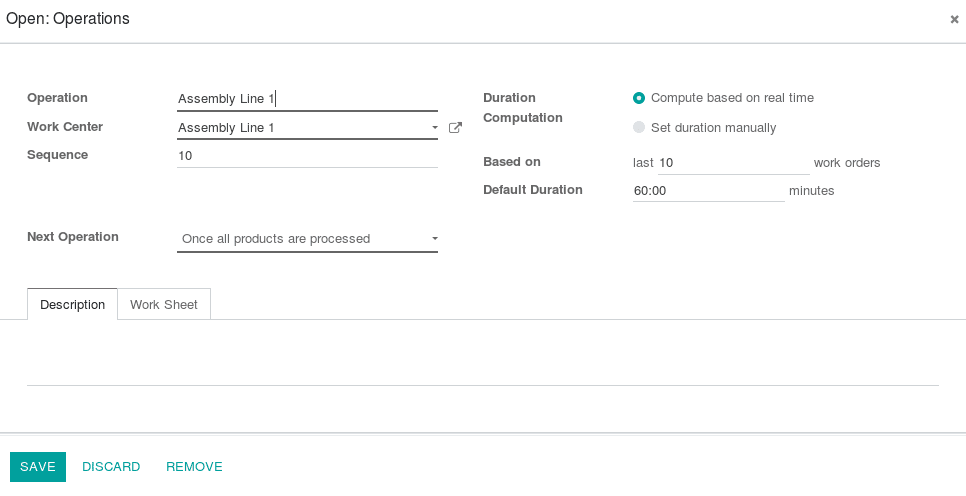
As you can see, there are two options for computing the production duration.
Compute-based in real time: Duration will be calculated based on the last work orders.
Set duration manually: Here, one can set the time duration manually.
If we choose the duration method as “Set duration manually” and save the changes, then the duration of the operation will be changed.
To check Assemble Furniture route, go to Master Data -> Routings -> Select Assemble Furniture routing, here the form will look like below image.
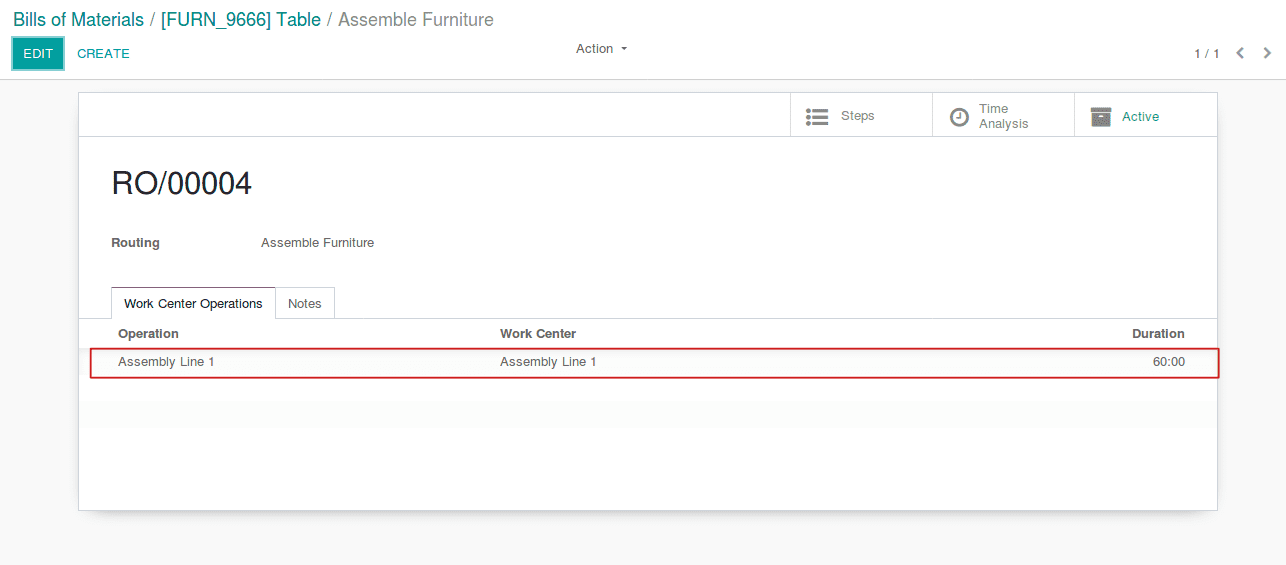
There is a work center named as Assembly Line1 and it will take 60 minutes (Set duration manually) to complete the process.
To check the details of the work center, open Assembly Line1 work center from Master Data -> Work Centers -> Select Assembly Line1 work center. The form will look like the below image.
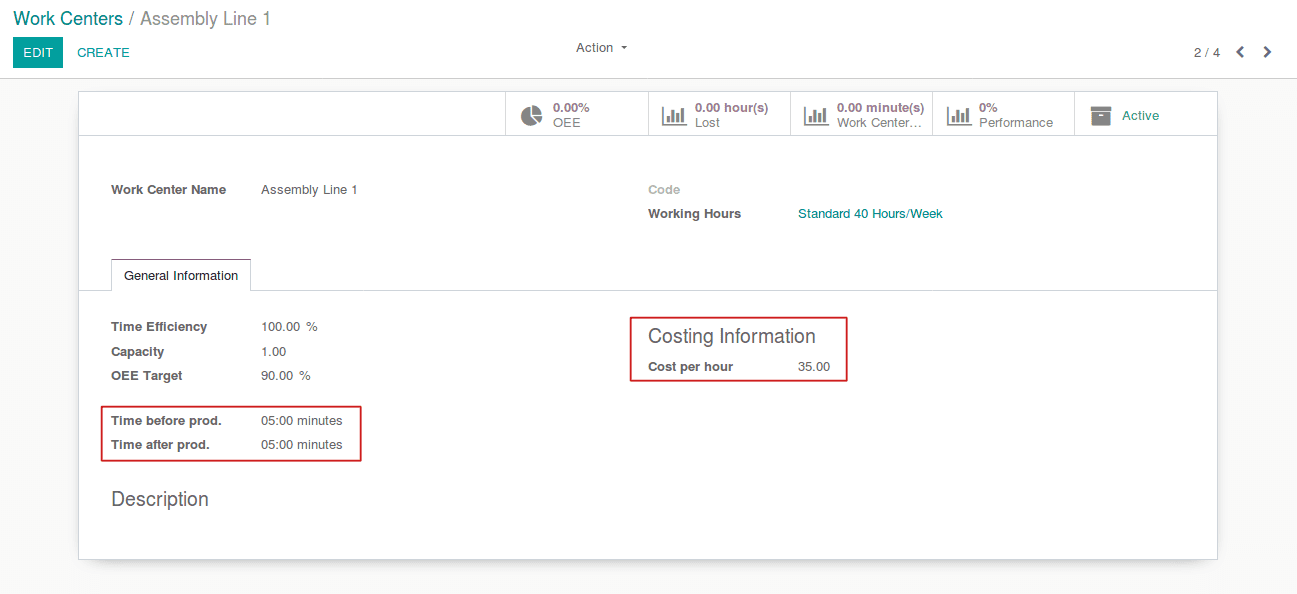
In this work center, we know the processing time is 60 minutes, but here one can take some extra time for setting up and cleaning i.e. the total time taken by Assembly Line1 work center is 70 minutes and the cost per hour is Rs 35. So the BoM cost for 70 minutes (1 hour and 10 minutes) will be Rs 40.83. In this case, the time efficiency of the work center has no role in the cost computation.
If we choose the duration method as Compute-based on real-time, the production time will be calculated based on the last work orders and will be dependent on the time efficiency of the work centers. Time efficiency is inversely proportional to the production time.
For example, if we create a manufacturing order for product Table.
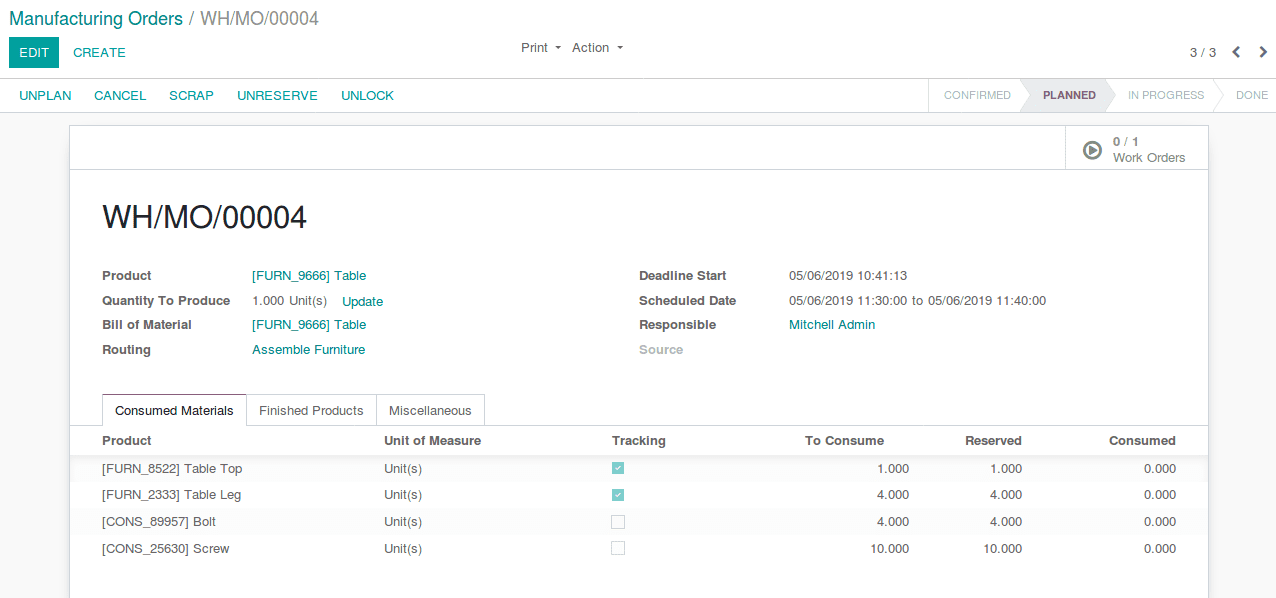
As you can see, there is a work order under it. One can click on the work orders smart button and check its time tracking tab.
Here, the expected duration denotes the sum of time before and after production. When the process takes place in this work center, at that point the real duration starts to run i.e. Real duration will be calculated based on the processing time of this work center. Eventually, the total production time will become the sum of real duration and time before and after production.
BoM cost of each work center will be calculated based on the production time, time taken before production and after production and the cost per hour.
ie, (Production time + Time before Production+Time after Production) * Cost per Hour.
BoM cost of a product will be calculated based on the number of quantity used and the product cost.
ie, Number of quantity * Product cost
The total BoM cost is the actual cost of a finished product.
ie, BoM cost of each work centers + BoM cost of each raw material.
This is how computing the cost of finished goods in Odoo.