Manufacturing a product may involve a lot of processes. So the cost of the finished goods or manufactured product will depend on the cost included for Bill of Materials, workcenter cost, labor charges, and other indirect costs.
Even though Odoo has costing methods like standard price, average cost, etc., it is entirely different from the manufacturing cost. At each stage of production, the cost of production may vary. And the total cost can be analyzed from the structure.
As the first step, we have to manufacture a product. To analyze the cost of production initially set the cost of the product as '0' and set the bill of materials for the production.
Consider the scenario of manufacturing a table. The table components or bill of materials may include tabletop, table legs, and some screws and bolts. Let us create the bill of materials for the table.
Go to the Manufacturing module> Products> Bill of Materials and then CREATE. A form will open to enter the details. Add the product to be manufactured in the product field.
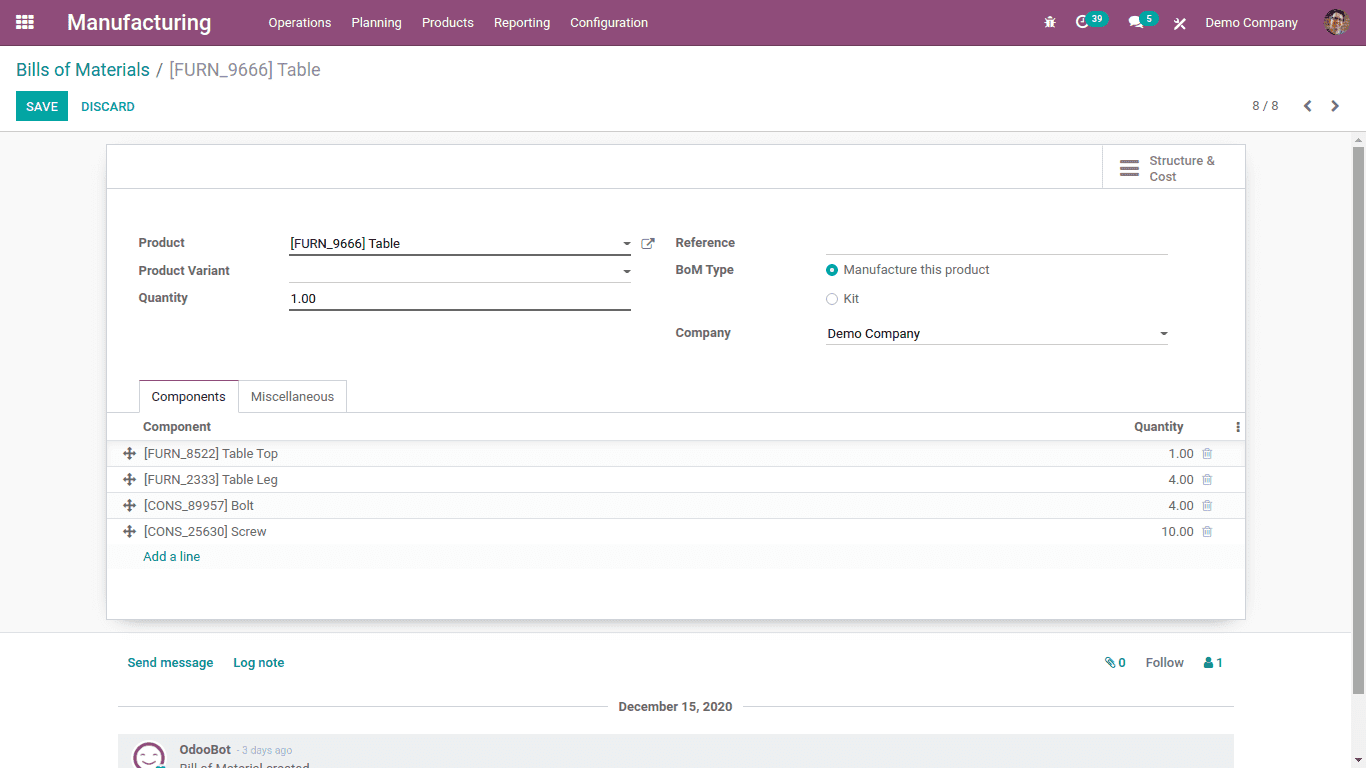
Quantity refers to how many tables have to be manufactured. To manufacture product BoM type should be 'Manufacture this product'.
Under components, one can mention the raw materials required to build the product. So you can add the components required to manufacture 1 product. So when a manufacturing order is created to produce 10 products, odoo will automatically calculate how much quantity of raw materials required to complete the order.
The smart button 'Structure & Cost', will give you the cost details and hierarchy.
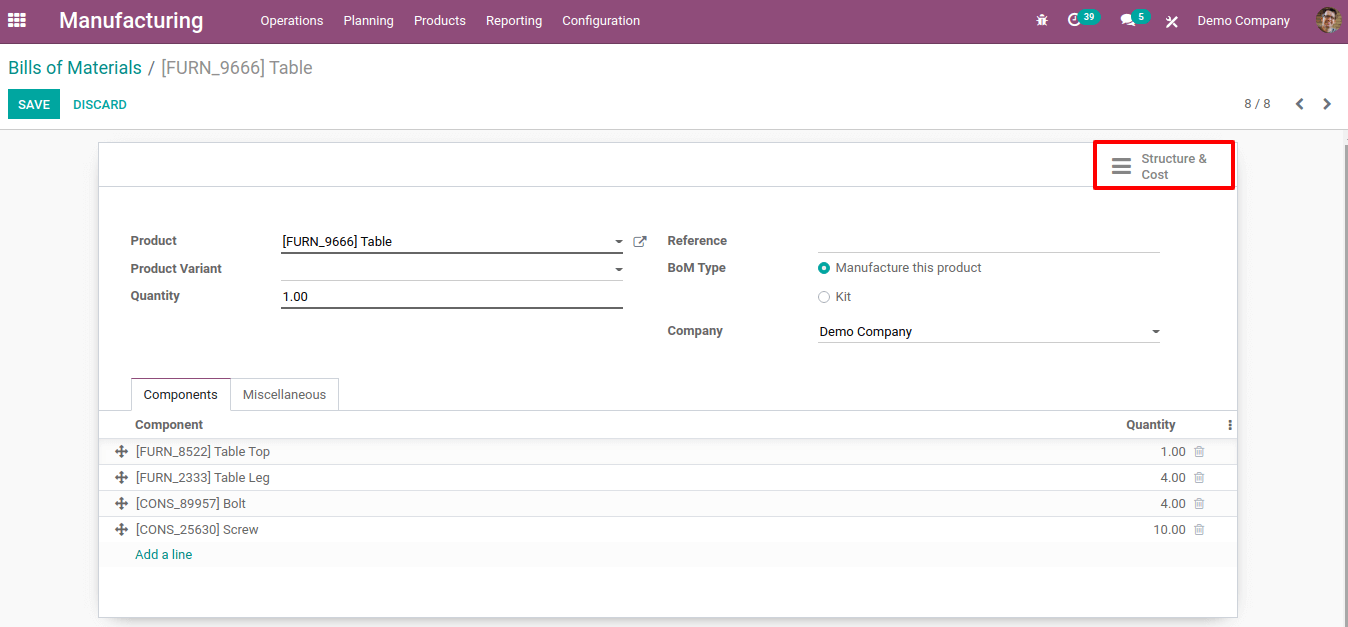
The 'BoM structure' and 'BoM structure & cost' can be separately analysed from here.
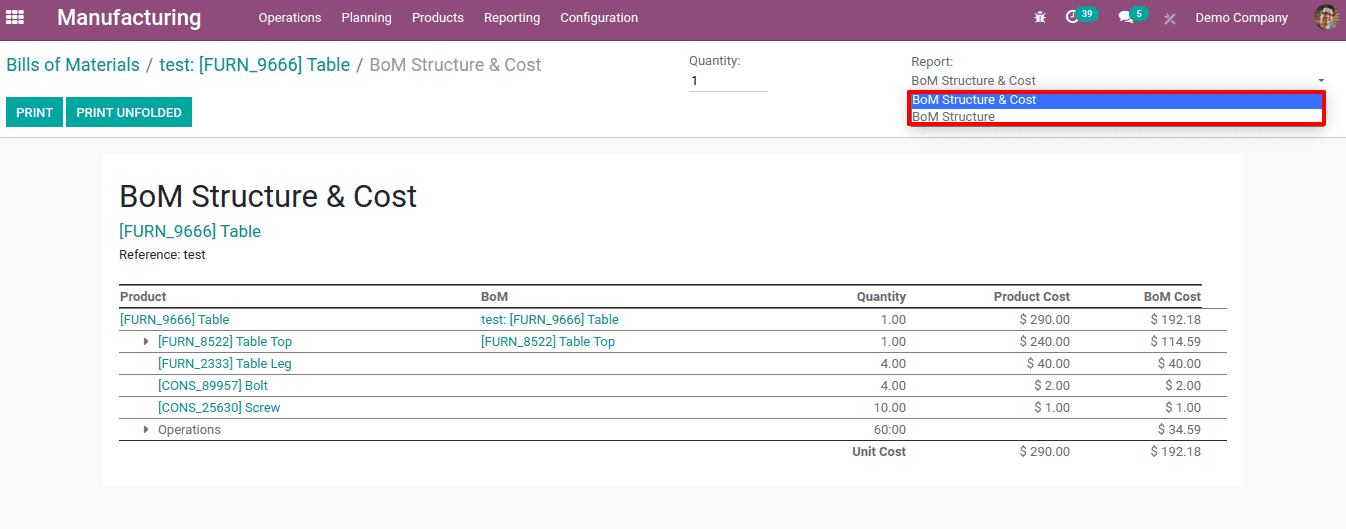
From here the product cost and BoM cost can be compared.
On clicking the arrow at the product and operations, will unfold the details. For table manufacturing, it required a table top. But at the same time, the tabletop may be manufactured using some other components like some wooden panels.
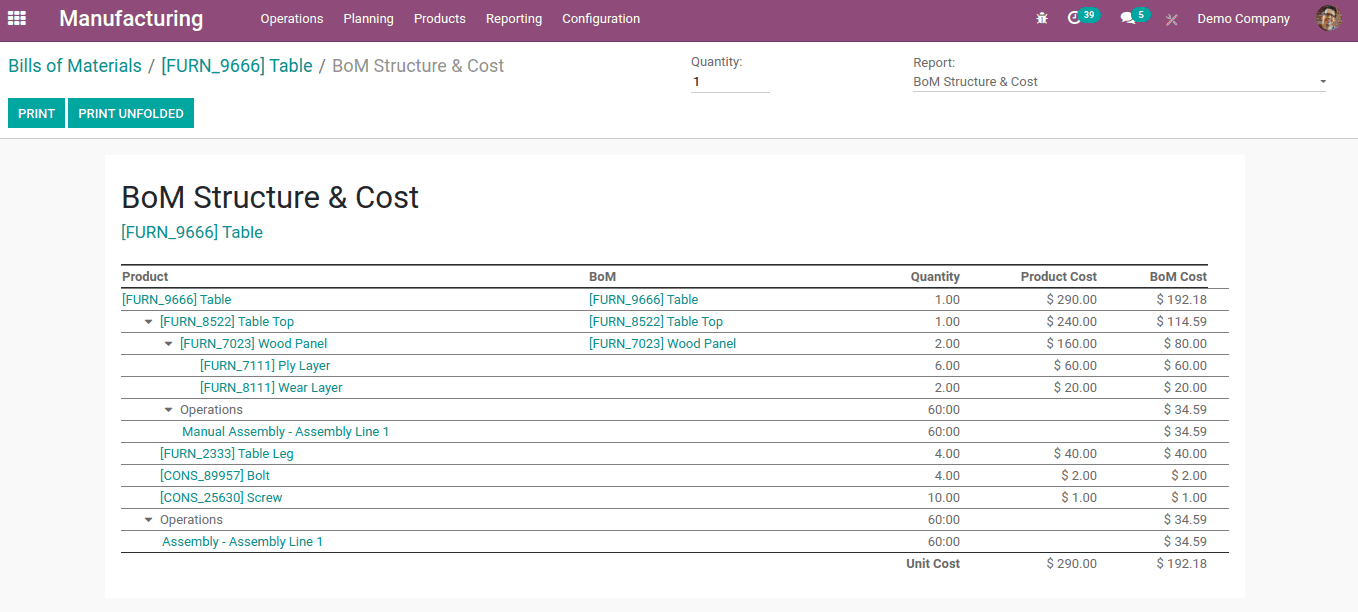
So once you click on the arrow at the BoM 'table top', it will show the details of the BoM of Tabletop. Thus the multi BoMs can also be folded and unfold in the structure. While unfolding we can analyze that the 'table top' is manufactured using the 'Wood panel' and the wood panel is made up of 'Ply Layer' and 'Wear Layer'.Also, the cost associated with each component can be visible.
By changing the 'Quantity', the cost for manufacturing bulk quantities can be analyzed.
Now regarding the 'Operations', while manufacturing a product different operations will have to be performed. The operations like cutting, chiseling, assembling, etc. will be included here. So from the configuration settings enable 'work orders' and save.
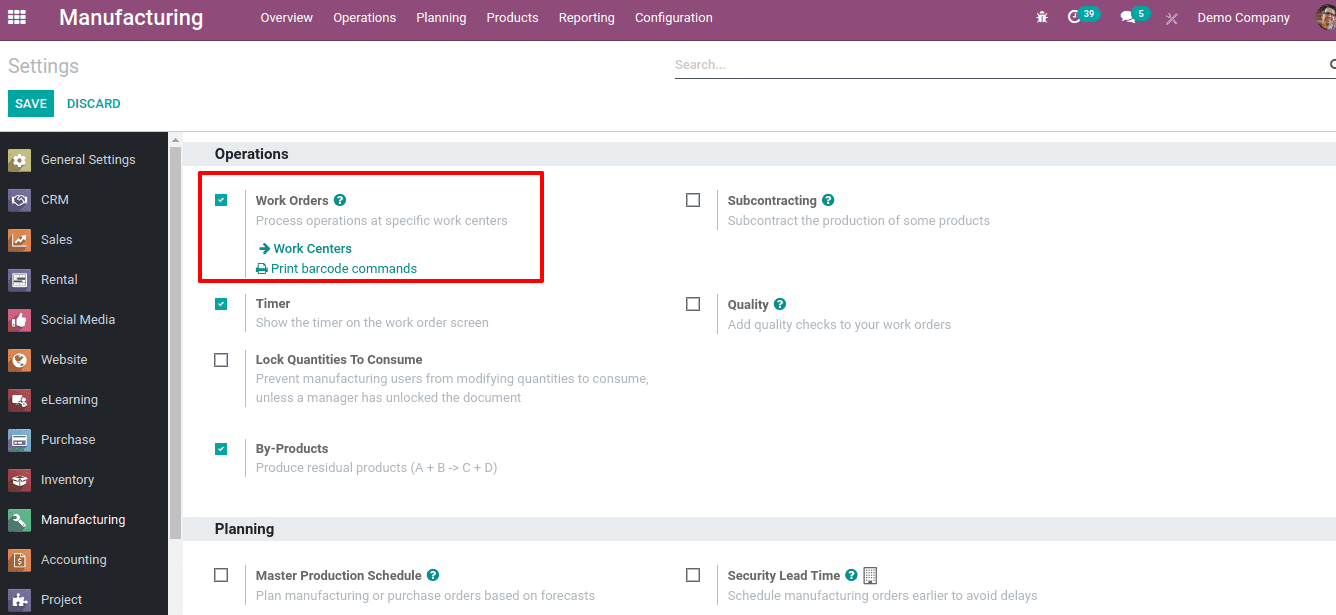
This helps to process different operations in work centers. Once the work center is enabled in the BoM form itself we can see the operations tab, where we can add the operation to be performed.
One can create operations from Configuration> Operations and create operations.
So when an operation involves the manufacturing process the cost of the work center will be taken into account on the basis of how much time it takes to perform the operation also
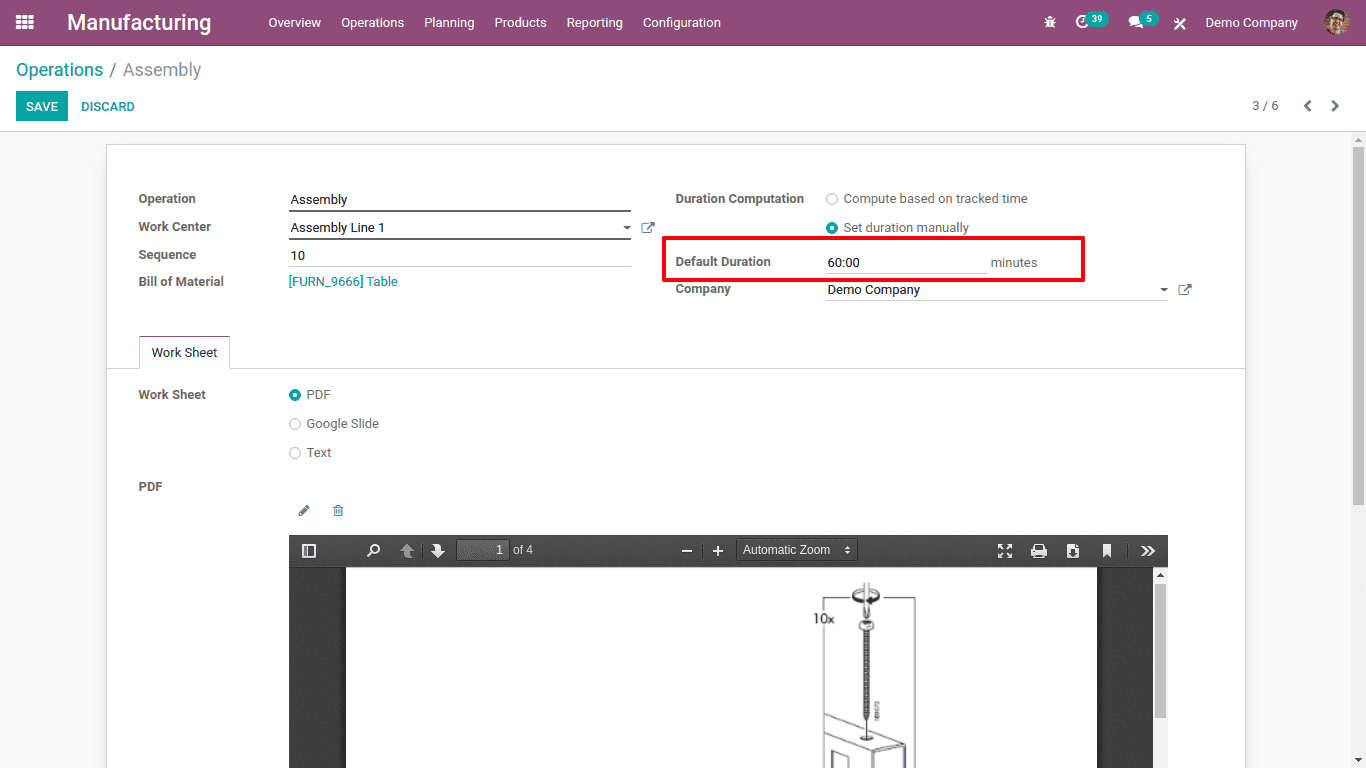
Here we have entered the duration in minutes. Here, 60 minutes is added as the default duration, which means the work center will be active to manufacture the product for 60 minutes.
Here, duration computation is manual. So the efficiency won't depend on the operation time. For computation based on the traced time, the efficiency will depend on the time taken to manufacture the product.
Now move to the work center, Assembly Line 1. Under costing information, the work center cost per can be mentioned.
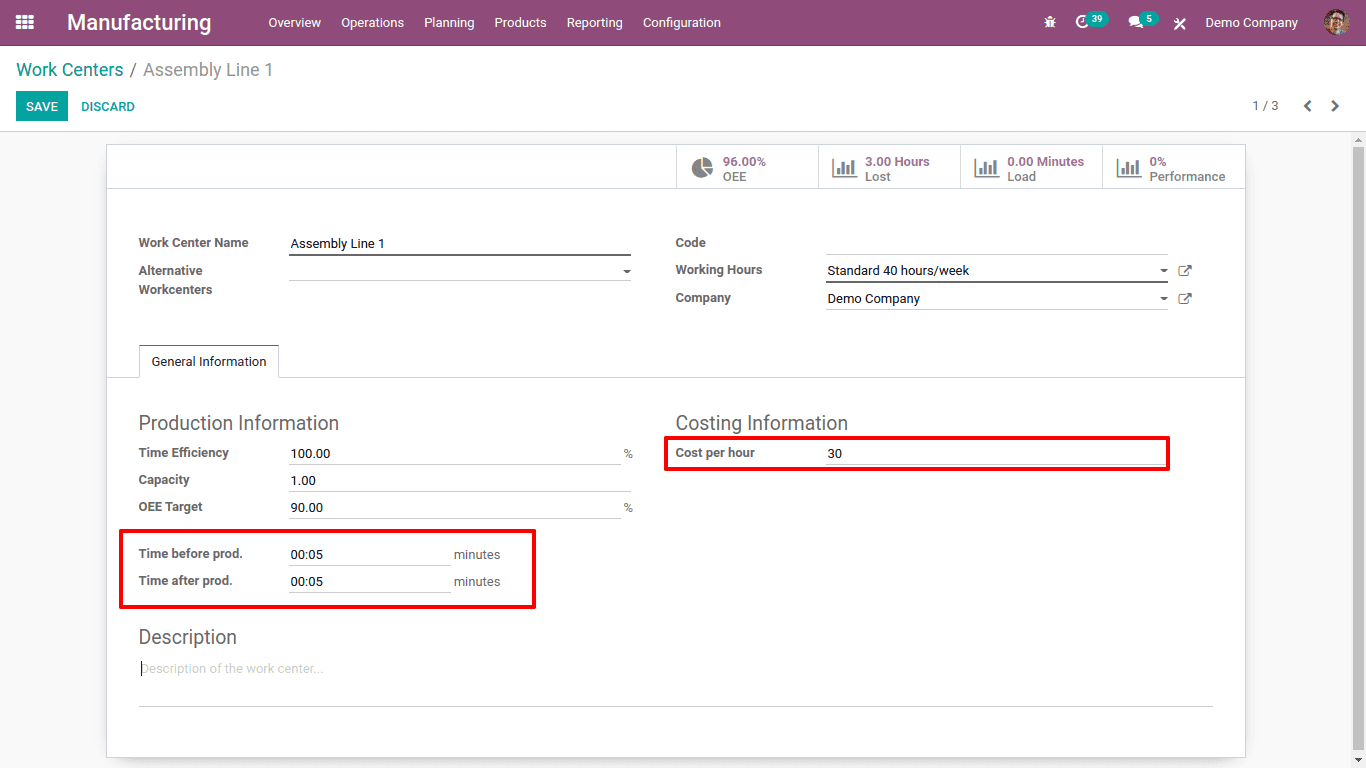
The time before and after production can also be set in the work center. Here the cost per hour is 30. 60 minutes is required to manufacture the table and the time before production and after production is 5 minutes each. So the total time will be 70 minutes.
So the cost will be (70/60) * 30 = 35.
So once the operation and workcenter for the operation are assigned, we can include the operation in BoM.
Under the operations tab, click on 'Add a line' and one can add the operations and workcenter in which the operation has to be performed.
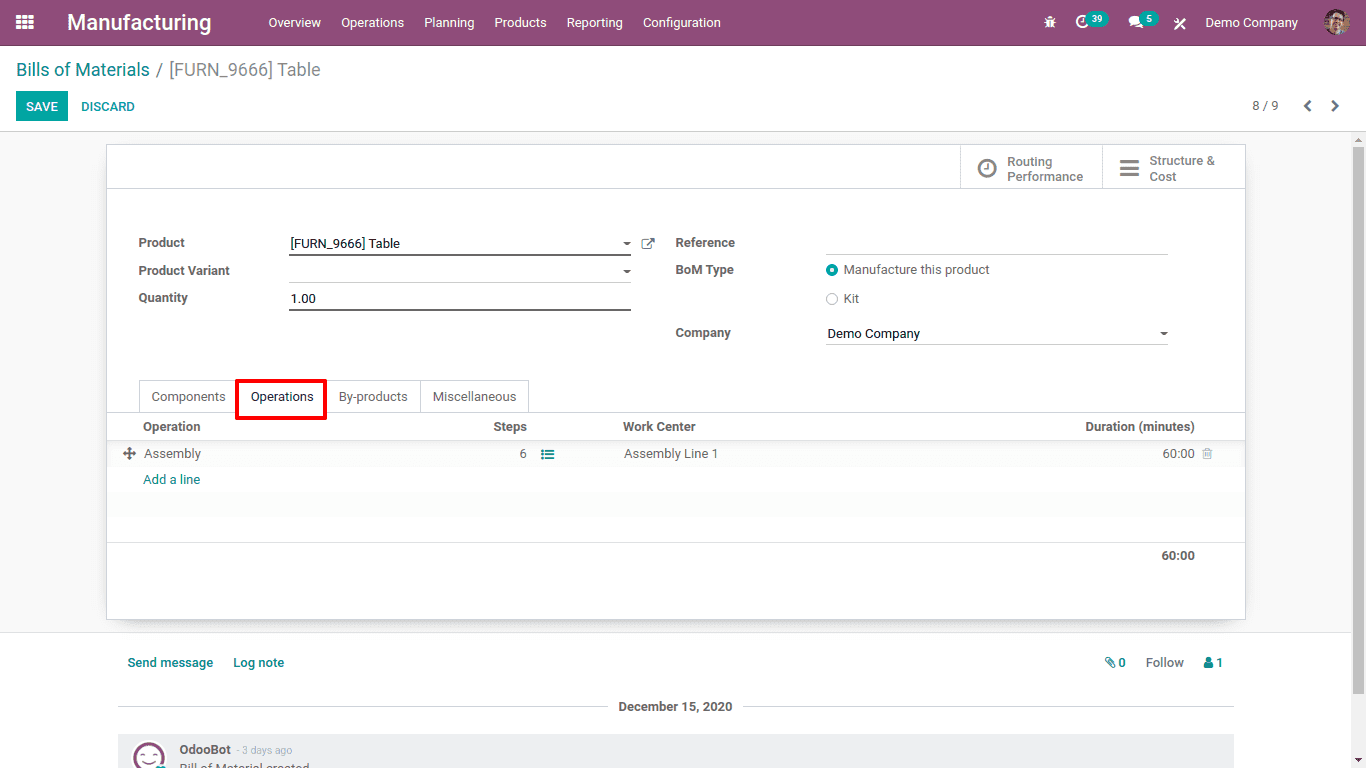
Let us create a manufacturing order for the product table.
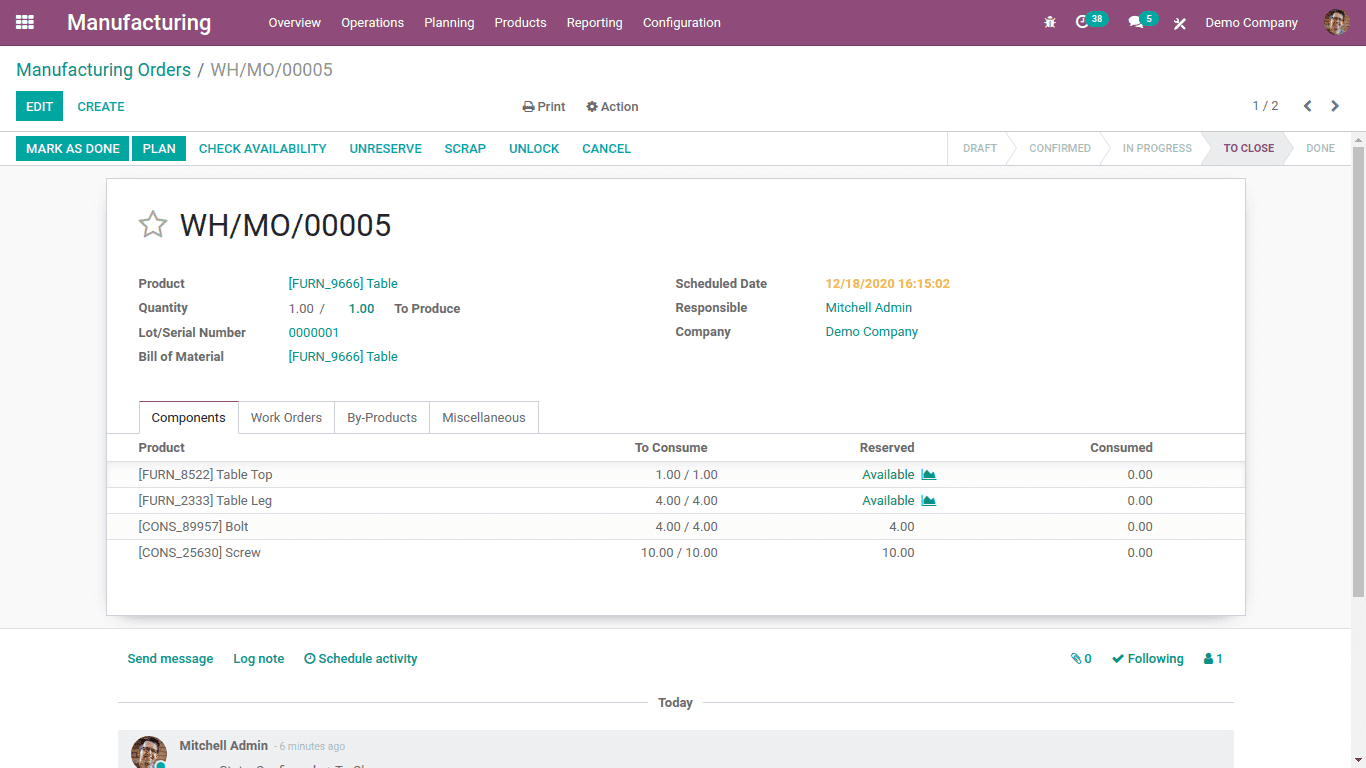
Quantity to produce is 1 and hence the 'To consume' will show the required quantity.
Under the 'Work Orders' tab, the expected time and real-time gets recorded.
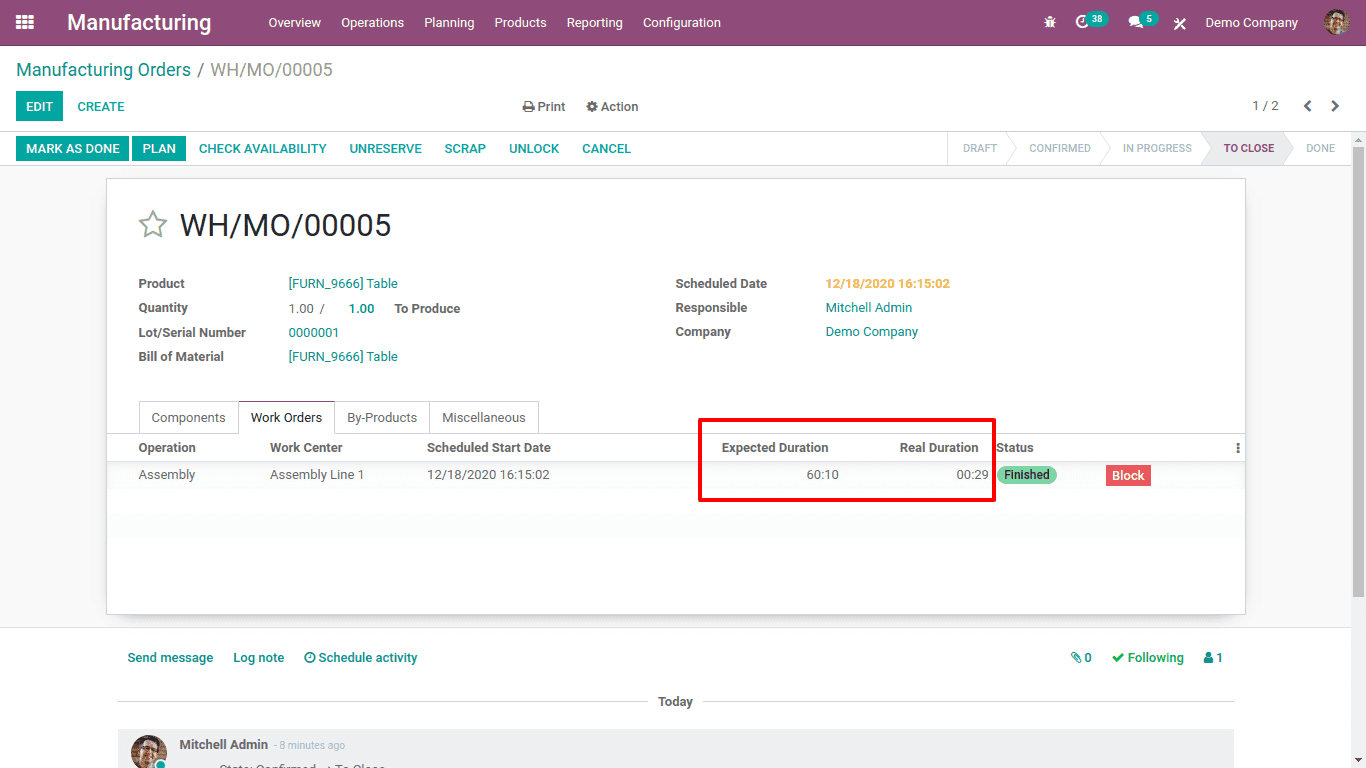
The expected duration defines how long it may take to produce the table while real duration is the actual time taken to produce the table.
# The work center's BoM cost will be calculated as the product of total time taken and cost per hour, ie
(Real-time + time before production + time after production) * cost per hour
# Product's BoM cost is the product of total quantity consumed and cost of raw materials, ie
Quantity consumed * cost per unit product
# The total BoM cost of the finished product will be the sum of BoM cost of work center and product,
Total BoM cost of work center + Total BoM cost of Product
You can read more about How to Track Products in Odoo 14 Manufacturing by referring to our previously published blogs