Inventory management allows us to manage all inventory activities including logistics, stock management, finance, and so on in one place. It improves the supply chain transparency and makes inventory management time and cost-efficient.
For small and medium-sized business owners, inventory management can be a real headache. Getting the right inventory management system and adopting the best practices can untangle the inventory management process for your business. This would mean getting rid of the production bottlenecks and reaching your customers on time.
Inventory includes all the finished goods, materials, and merchandise that the company sells in the market to avail profit. While some industries may consider only the finished goods as part of their inventory, other industries may include materials from the start. The inventory management would require us to keep track of all the assets that can be processed to sell or directly sold in the market to generate revenue.
The inventory is the major asset of the company and undeniably the most important of business. From raw materials to finished goods that have a value of the sale is to be controlled and managed under the inventory management. The biggest current asset of the company is not to be toyed with. The management of such critical assets cannot be subjected to risks of entry errors, duplication errors, and calculation errors. An optimized system that can not only organize but also automate processes as required will be a great advantage to companies of any scale.
Without accurate data about the inventory, we may run the risk of stocking too much or too little. While having too much runs the risks of obsolescence, too little may lead to a shortage of supplies resulting in potential customer loss. Accurate stats of the inventory as well as timely reporting would help managers manage the stocking and restocking of items more efficiently. This would help companies save money in the unnecessary stocking of items.
The inventory management would include overseeing the supply chain from suppliers to customers. While we can start off with manual tools, this would soon become too complicated to handle and stand chances of error. To avoid this, we can always shift our inventory management to systems or softwares designed with functionalities that would help regulate the inventory movement to faultless efficiency.
Most of these systems are designed not merely to manage stock monitoring and reordering. They work as integrated systems that can collaborate with other departments of the company like manufacturing and accounting to develop a real-time database. The clear visibility provided by an inventory management system allows you to reduce expenses, provide better customer service and prevent loss from stock mismanagement. It can also provide us with insights into the financial standings of our company.
Inventory management involves managing the various aspects like
- Warehouse
- Products and
- Shipping
The modern user interface of the Odoo inventory management system allows you to keep a flexible management system for single inventory or complex multi warehouse environments. The inventory module comes with multiple features like double entry bookkeeping, barcode scanning, customer portal, cross-docking, drop-shipping, and smart scheduler.
Odoo inventory management supports basic operations like managing shipments, inventory counts, scrap management, and so on. Additionally, it supports advanced routing options like drop-shipping, cross-docking, and multi-step delivery. Functionalities like drop-shipping and cross-docking benefit small and medium businesses with small warehouses.
Warehouse Management
Warehouses
Odoo inventory supports more than one warehouse. For companies that operate with more than one warehouse, we can have a single control panel for all the warehouse activities. From the Inventory configuration, we can select warehouses and add to the list of warehouses in the window.
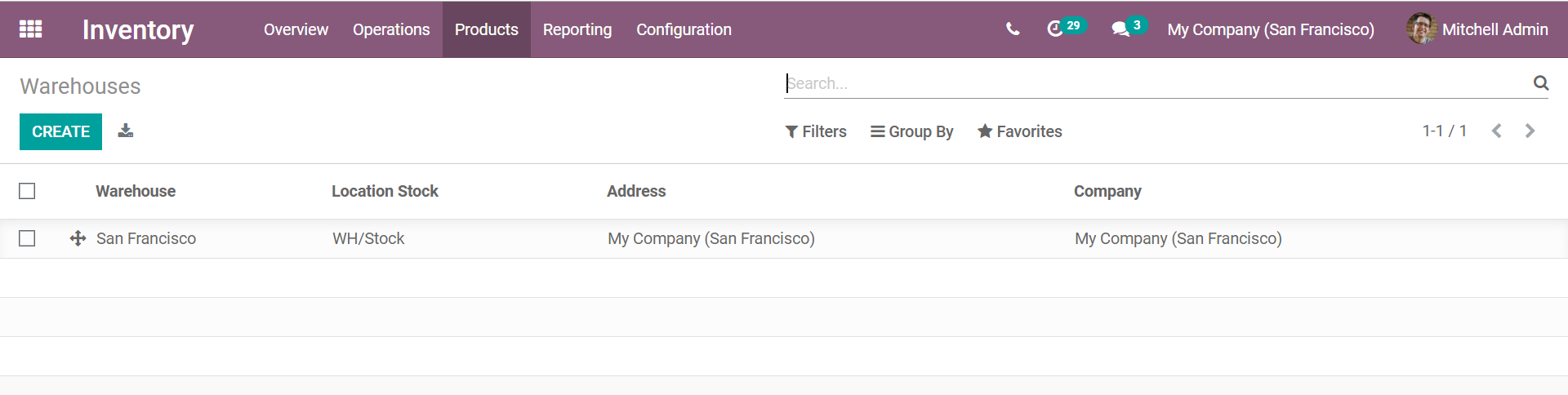
Putaway rules
Putaway rules determined in Odoo allow us to move an incoming shipment in any location of the warehouse to be moved to the most appropriate location. Depending upon the nature of the products, some products need to be stored in certain places to avoid perishing. For example, dairy products might require refrigeration. So we can devise a putaway rule for the particular product that will directly stock the goods to the location.

Locations
We can add multiple locations within the warehouse for better traceability and product flow. This would also be beneficial for creating put-away rules and managing operation types. There can be as many locations as we want under the same warehouse. We can create hierarchical locations in Odoo and create a tree of parent-child locations.
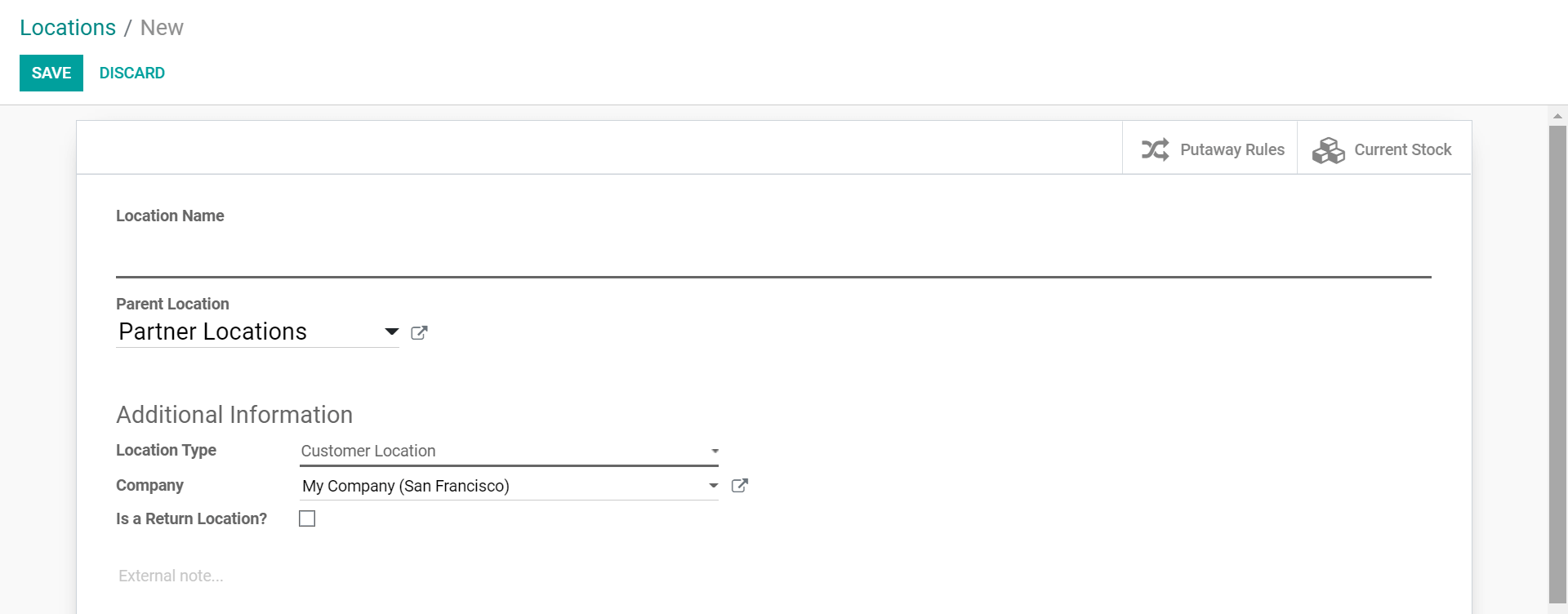
Operations Type
We can create operation types to create inventory entries of various operations to perform. This would allow us to group the inventory operations. Operation types can be delivery, manufacturing, and so on.
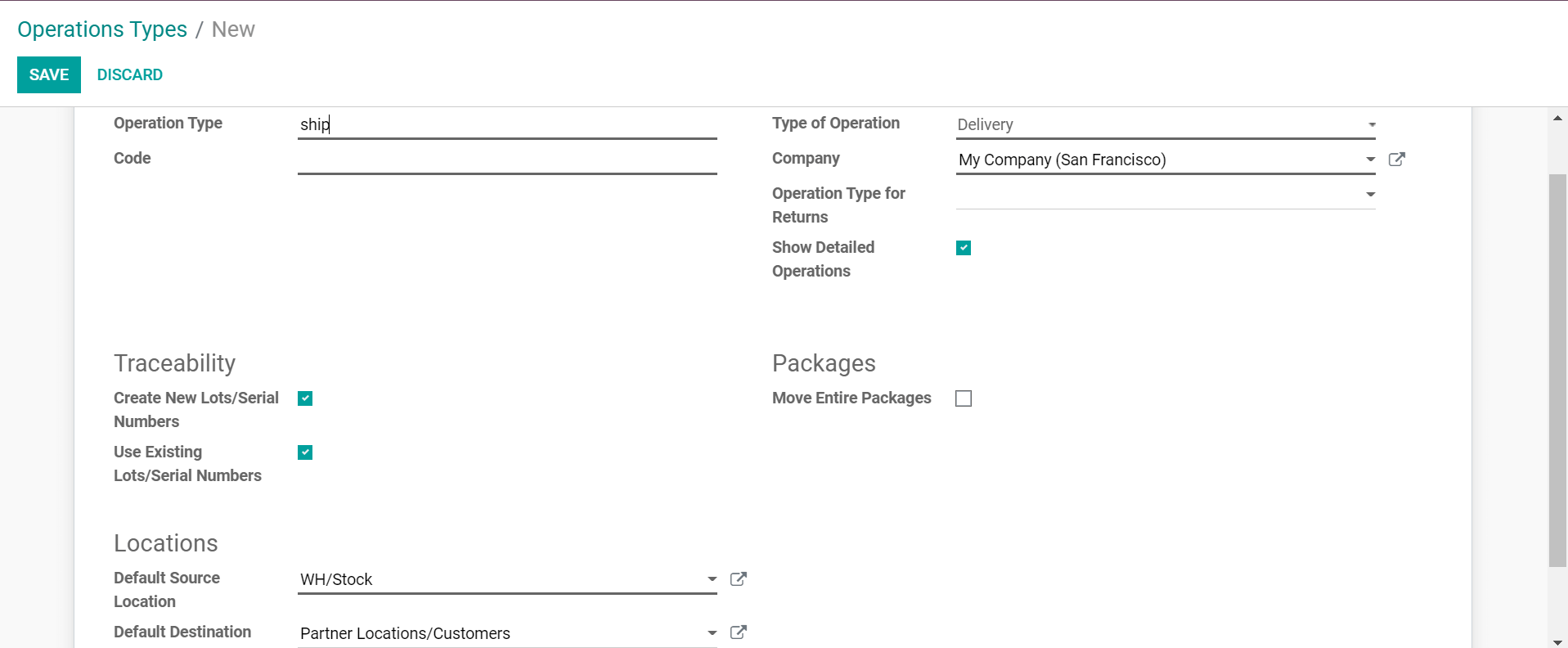
Products
Product Categories
We can create categories for the products in our inventory. This allows us to group and sort the products for easier inventory actions. Categorization allows better management
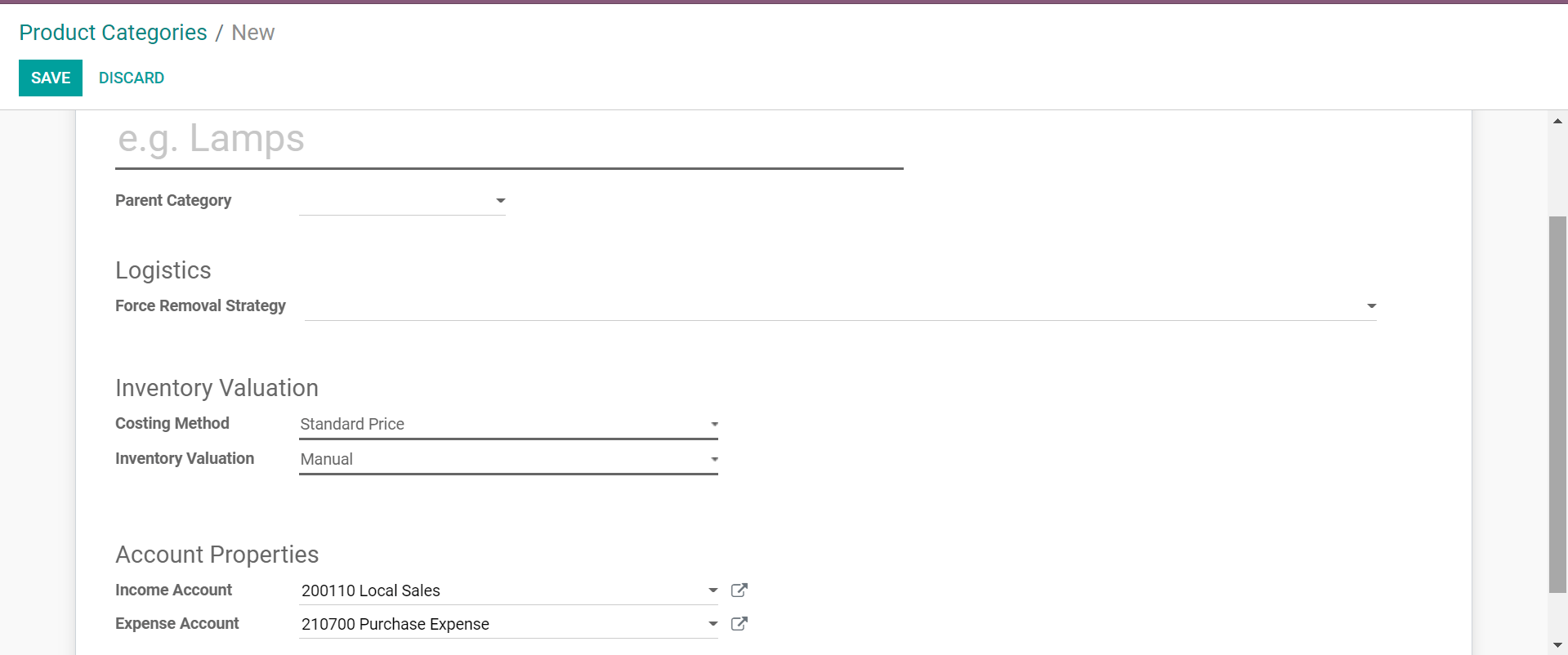
We can also determine a parent category if needed. Categories can be set to have a common removal strategy. This can be first in first out or last in first out. The removal strategy determines which product has to be removed first based on the stocking date.
Once we have the category configuration completed, we can add attributes.
Attributes
This helps to create product variants based on attributes. For example, we can create the attribute as 'color' and then add values ??like 'red', 'green', 'blue', etc. This would allow us to create product variants based on the color variation.
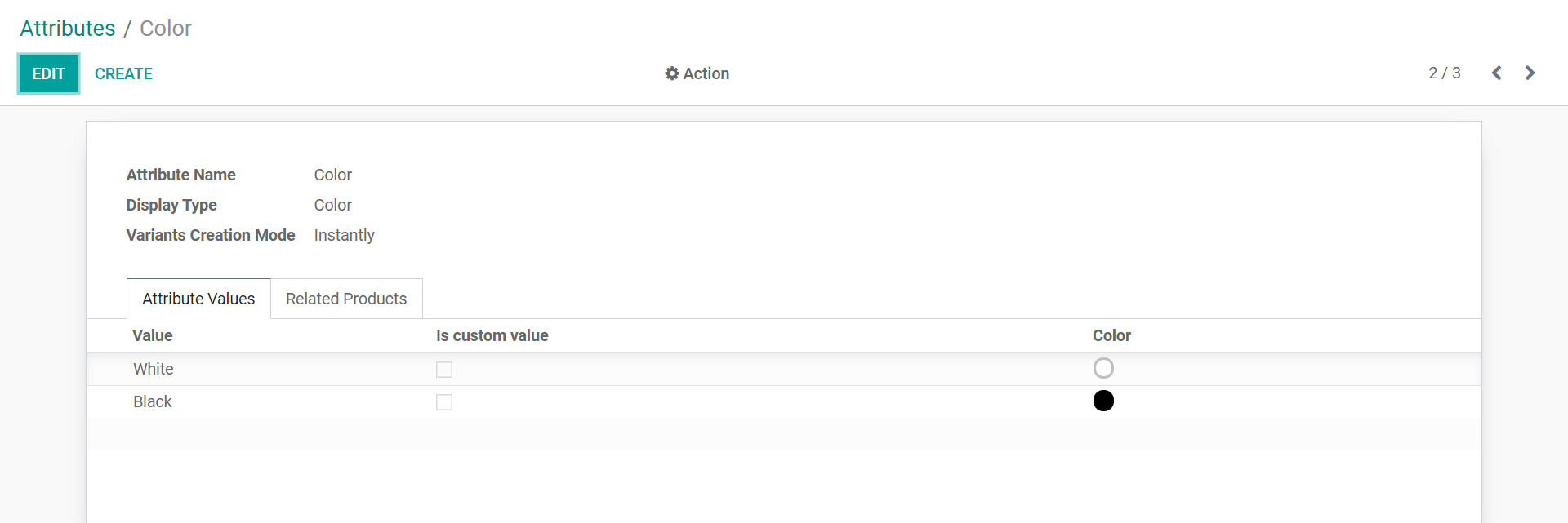
We can choose the attribute and similar value while creating a new product.
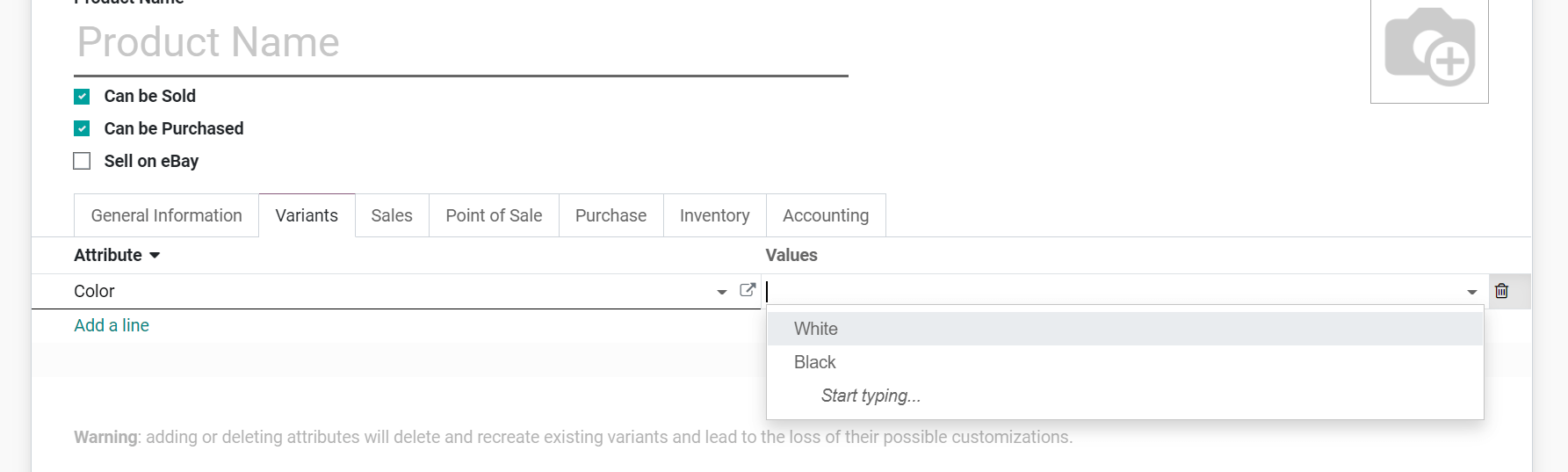
Reordering Rules
The reordering rules allow automatic replenishing of stock items when necessary. We can set a minimum and maximum quantity for each product. While the stock falls below the minimum, the stock replenishing is triggered to meet the maximum quantity of the given stock. This ensures that the products with automatic triggers are never out of stock or overstocked.
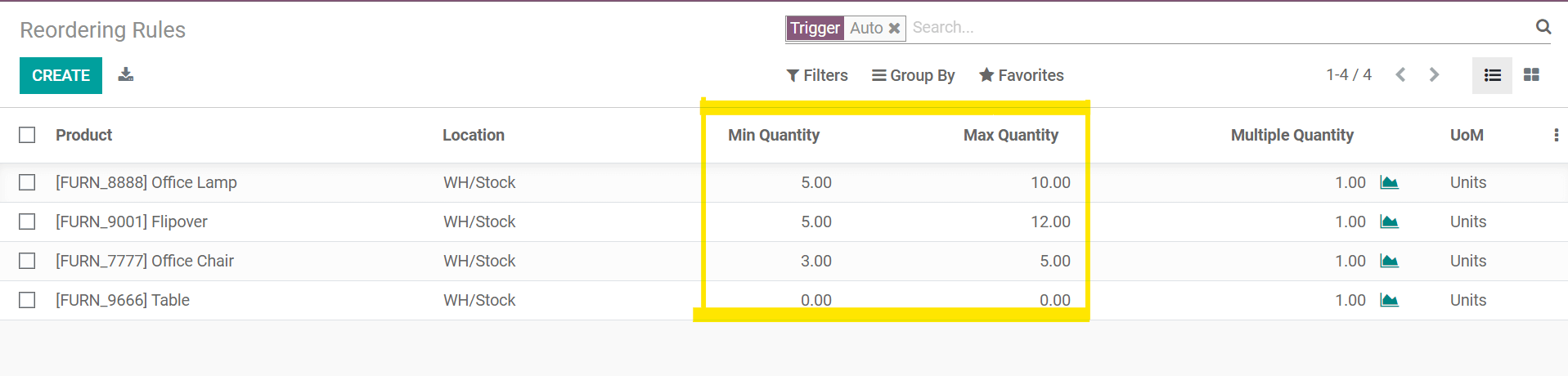
Reordering is triggered only for storable products.
We can add trigger nature as auto or manual. We can also add preferred routes and companies for each reordering rule.
Units of measure
We can create categories of units of measure like weight, working time, and length. The categories allow the conversion of units within the same categories. Once we add categories we can create the various units used. We can use days, hours, and so on for the category working time. Once we create a unit, we can assign the rounding precision and determine it as the reference unit for the category or in comparison to the reference unit as smaller than or larger than the reference unit.
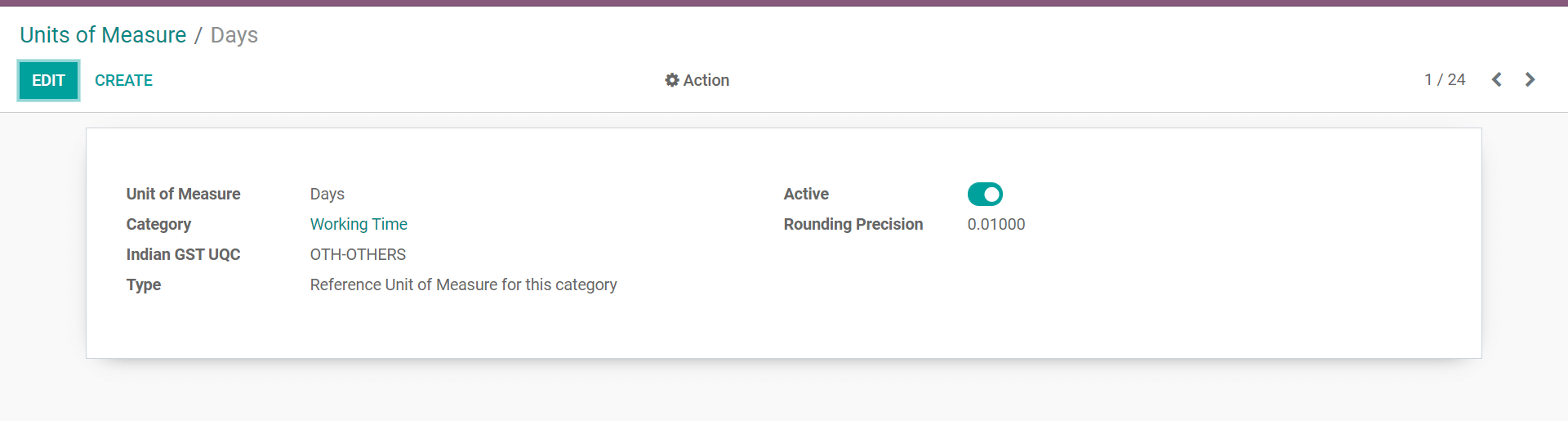
We can also determine a conversion ratio for units other than reference.
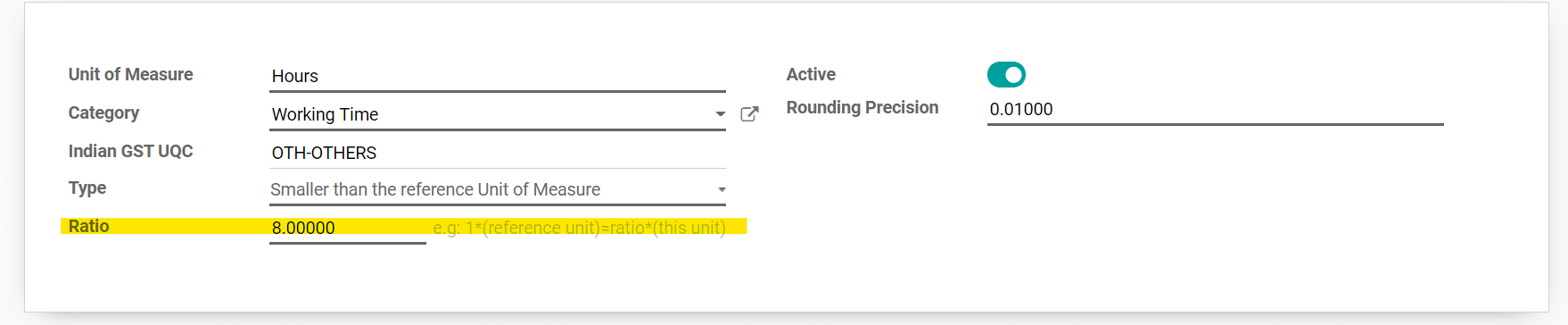
Delivery
Under the inventory, we have to manage the delivery of the products too. We can modify the delivery-related settings under configuration.
Shipping methods
Various shipping methods spending on the shipping partner or charges can be created. The shipping charges for these methods can be determined as fixed or computed based on rules. For third-party shippers, these charges are computed by the shippers.
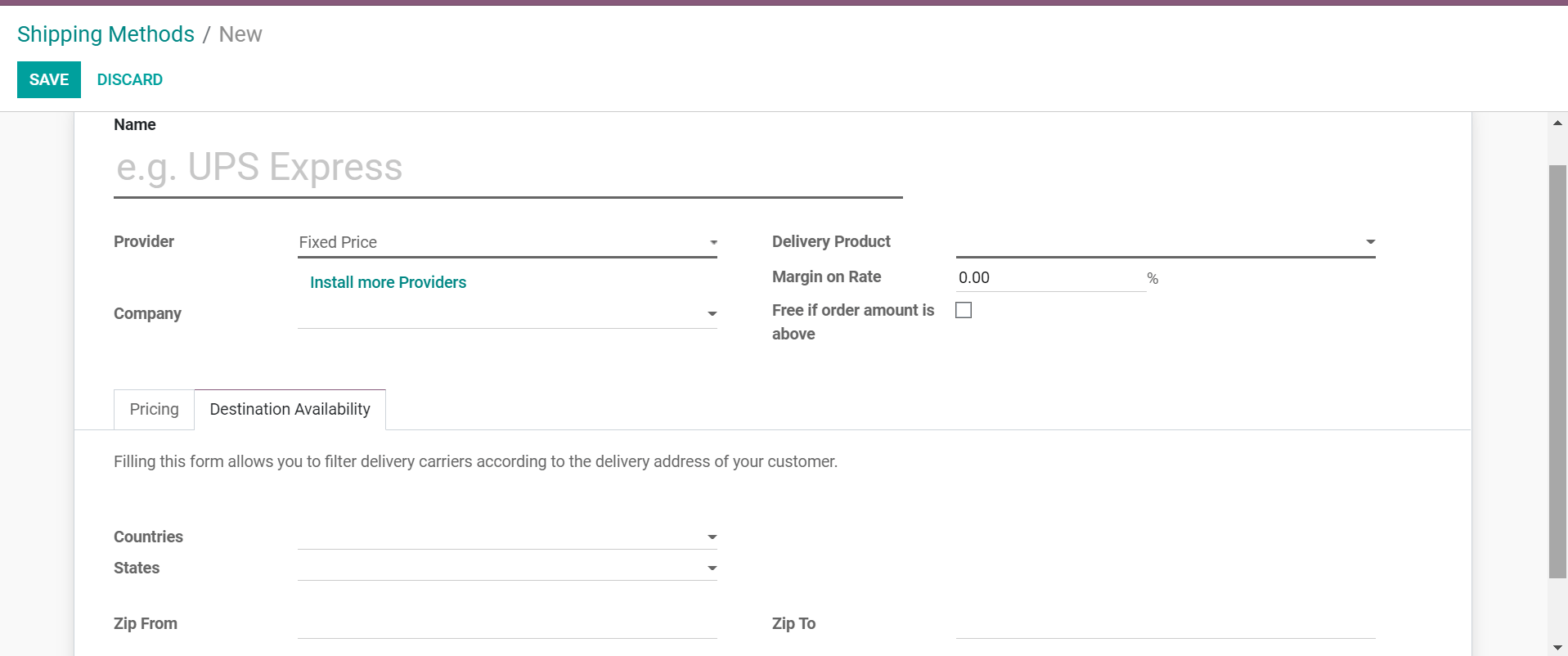
We can integrate shippers in the configuration> settings. This would allow adding them as providers while creating a shipping method. We can install connector modules from apps
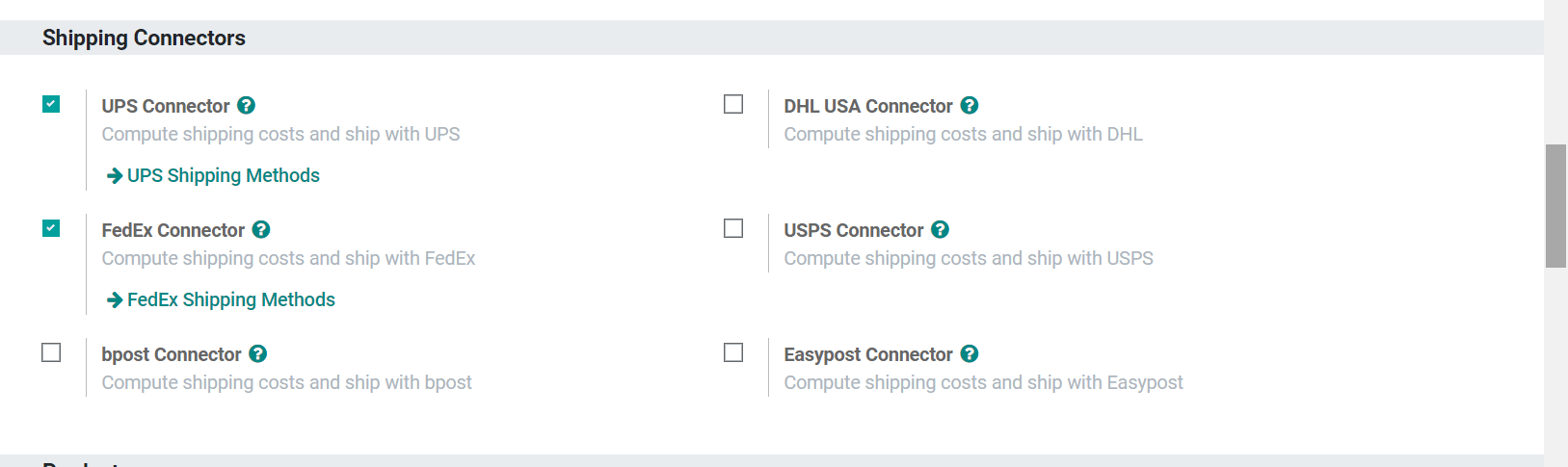
Delivery Packages
We can configure the different packaging that is used while delivering the products under configuration. We can integrate with a carrier or not and assign the various measurement values ??to determine packaging size and maximum weight.
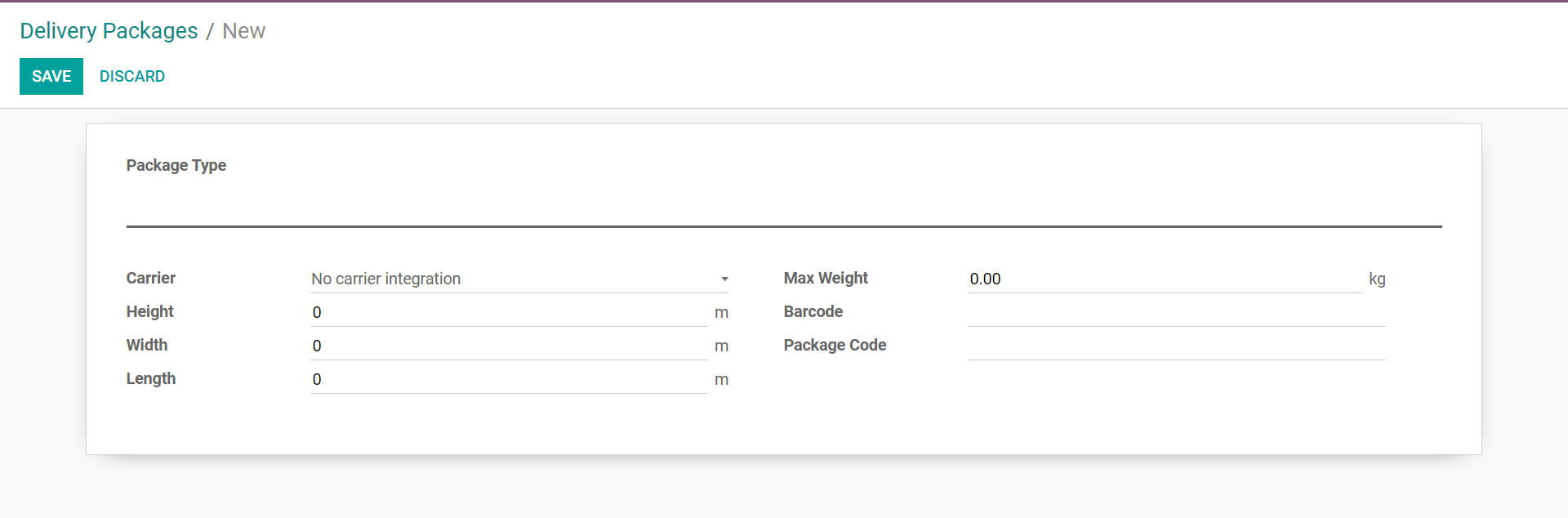
This an overview of the configurations available in the Odoo Inventory. We can modify these different sections and their settings to manage and organize the inventory with better efficiency.