Odooo 16 Manufacturing along with other sub modules say maintenance, PLM and Quality facilitates users to manage the production process more efficiently. These applications can be used in any kind of production industry, it can be automobile industry, food production, clothing industry and many more. Since it handles the production and managing production equipment and offers necessary quality checks as well.
In this blog we will be discussing the improvements introduced in Odoo 16 Manufacturing.
Merge and Split Manufacturing Orders
Odoo 16 ERP allows to merge and split manufacturing orders depending on the situations. Sometimes the demand from multiple customers for the same product generates multiple manufacturing orders. So instead of managing these manufacturing orders what can be done is that one can merge the manufacturing order for the same items if the raw materials are available to generate the entire demand quantity.
Merging MO
Consider the following MOs generated from various customer orders which is defined by the column ‘Source’ and the components are seems to be available and the total demand is 7 quantity.
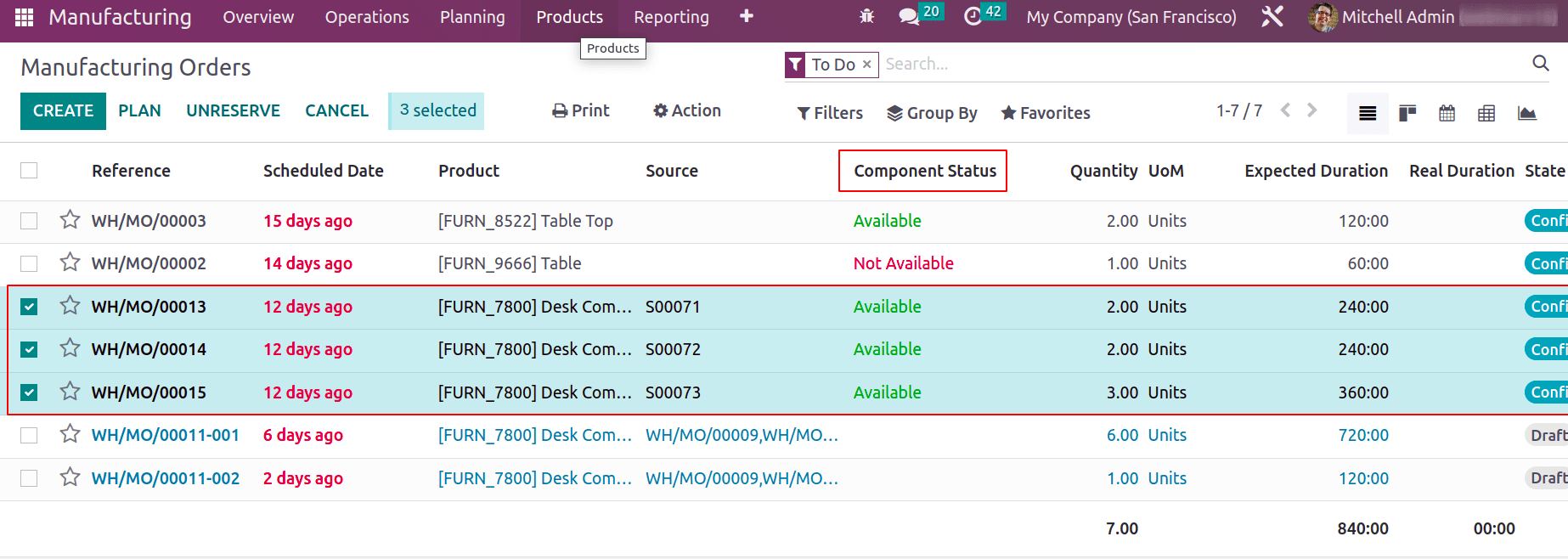
The ‘Action’ button facilitates to merge all these three MOs to a single MO. Once it is merged, it will be depicted as a single MO in the list view and the source will be updated as the merged MOs separated by comma.
The Component status seems available, thus production can be managed with single MO.
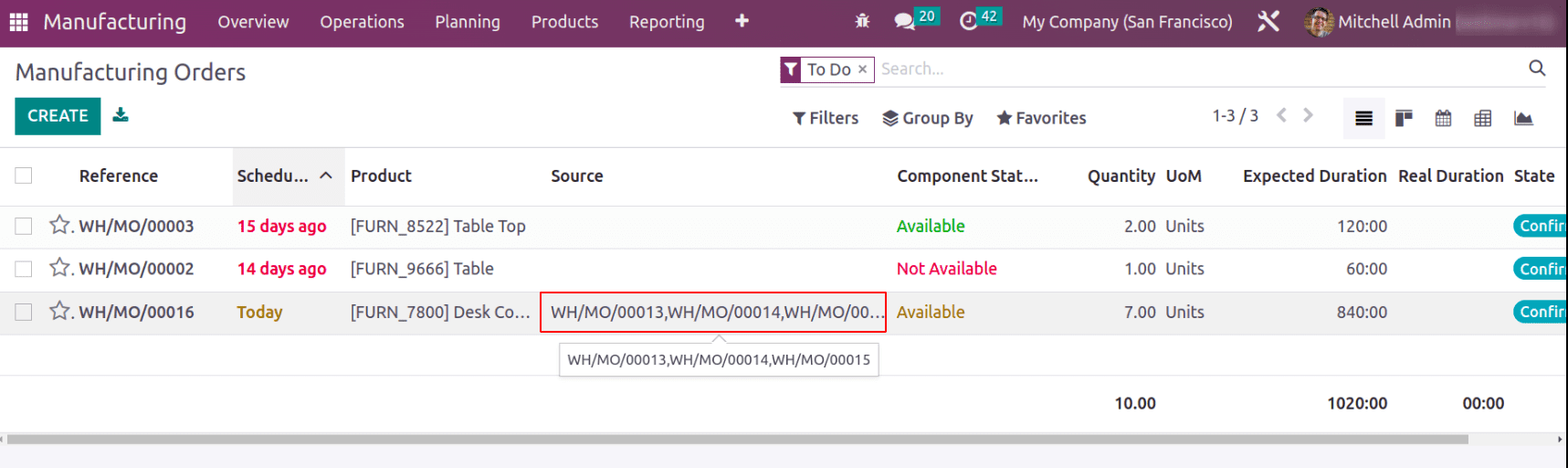
Splitting MO
Consider another scenario where a customer orders 10 items which leads to the creation of a manufacturing order of 10 quantities. But stock is insufficient to produce 10 quantities.
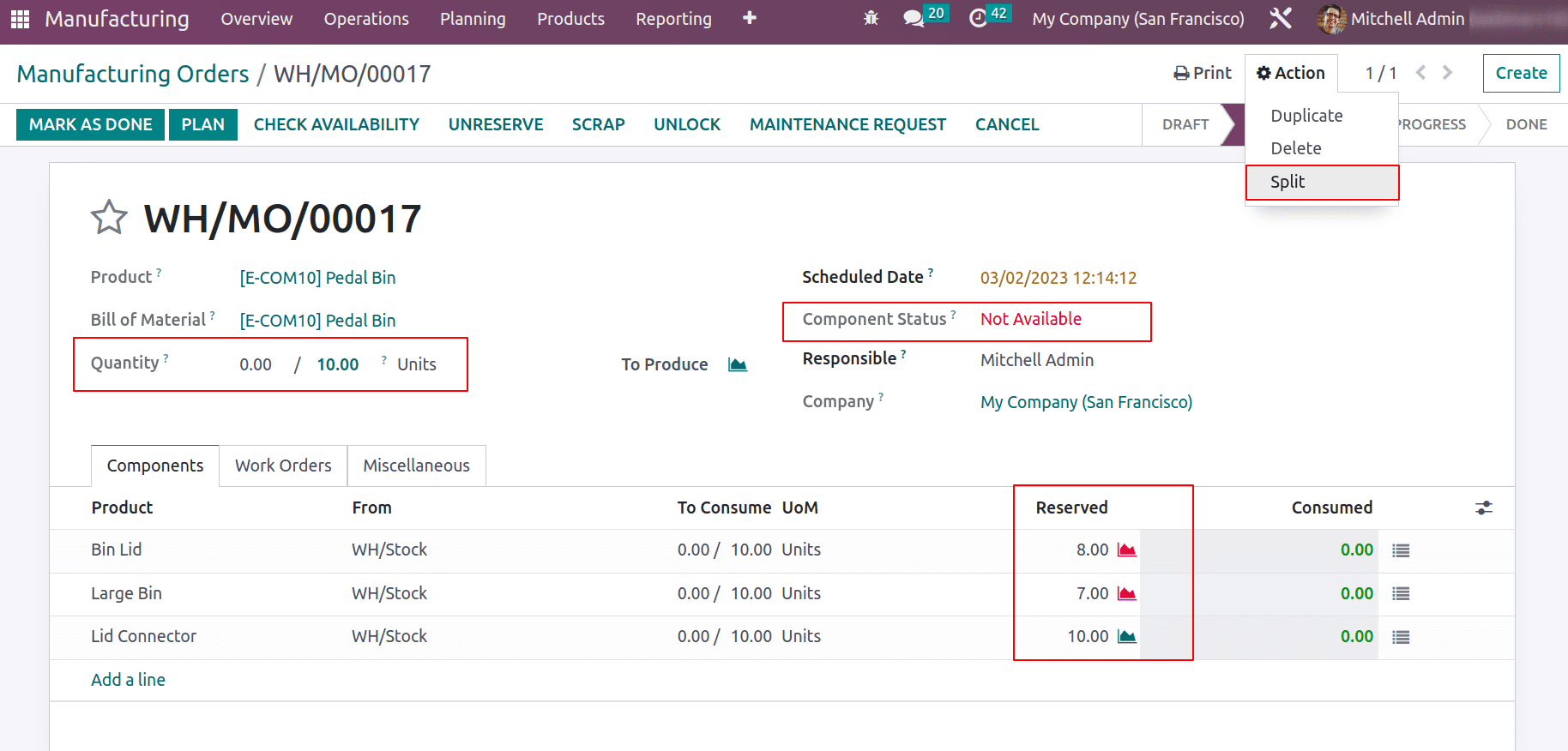
In the above screenshot total quantity to produce is 10 but raw material stock is available to manufacture only 7 quantities. So in this case one can split MO to two MOs one with 7 quantities and the other with 3 quantities. Also the production can be scheduled based on the availability of raw materials.
The split button pop ups another wizard which depicts the details of manufacturing order, along with product, Quantity tot produce and production capacity. Now can add the number of splits and add the schedule date of MO, responsible person and quantity to produce and SPLIT.
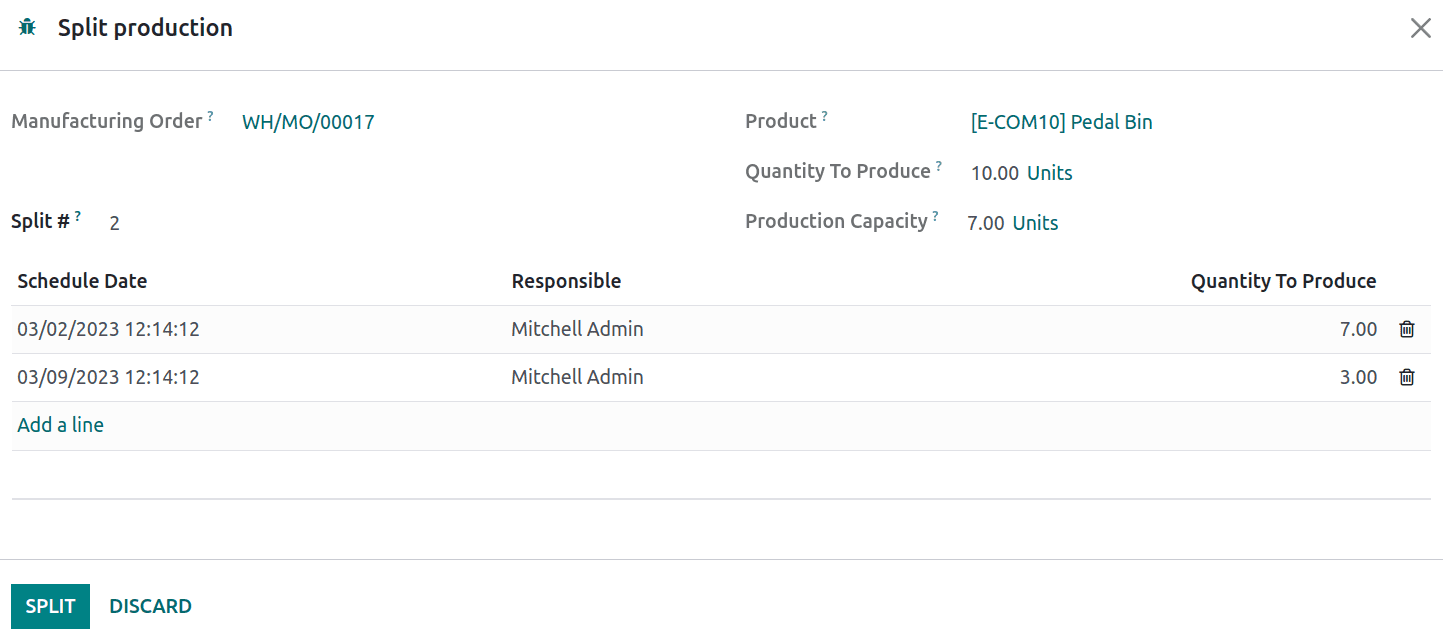
This will split the MO to two sub MOs, one with 7 and another with 3 quantities with different schedule dates.
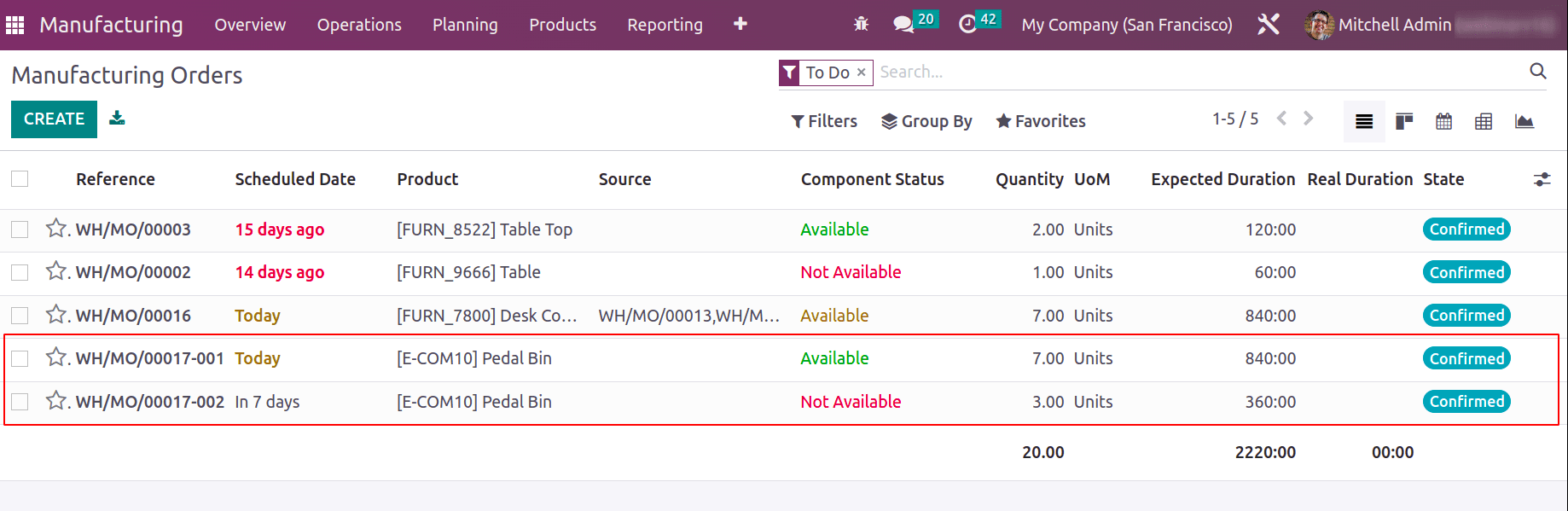
Allocation Report for Manufacturing Orders
Allocation reports can be considered as a tool which will depict the orders for which the products are manufactured. Normally even the products purchased or manufactured are to satisfy the customer need, it can be based on orders. Thus manufacturing of items can be used to satisfy multiple customer orders. Once the feature is enabled and saved an allocation report will be generated when the manufacturing is completed.
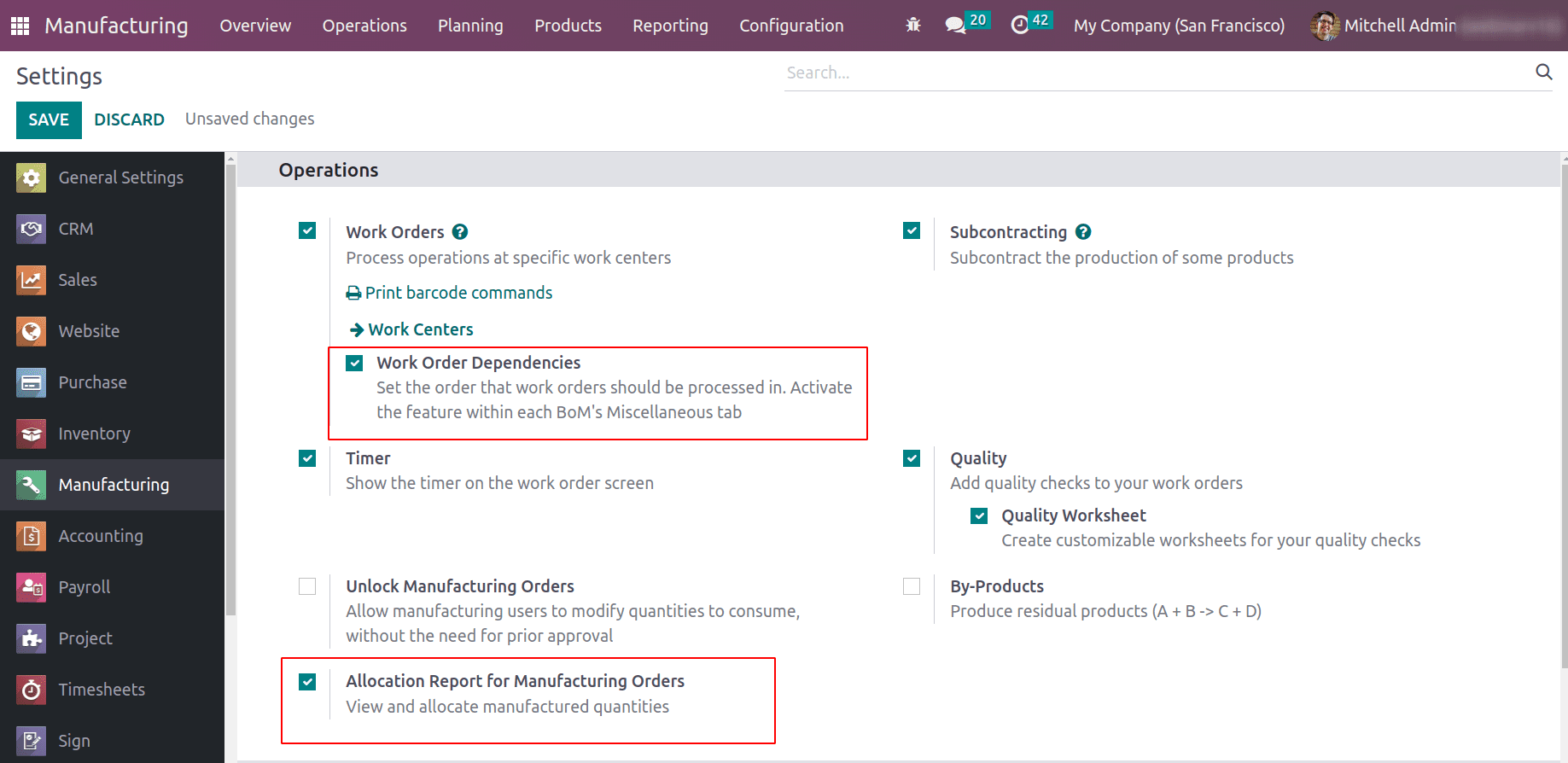
Now let’s see how this allocation report generates. Consider the previous example of ‘Desk Combination’. As we combined it to a single MO of 7 quantities, after production product should be reserved to those orders as well.
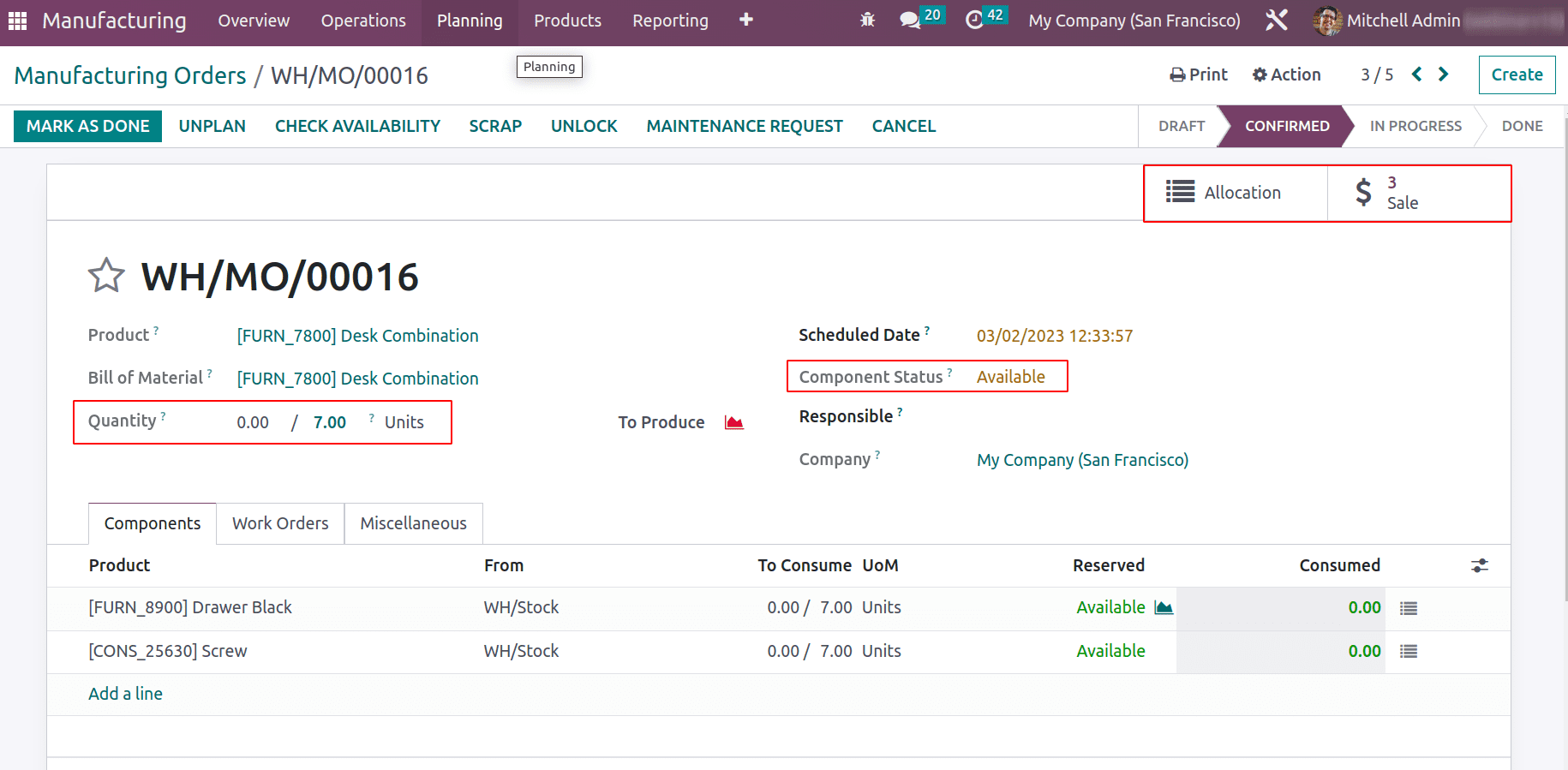
The two smart tabs ‘Allocation’ and ‘Sale’ show the allocation report and source sale orders respectively.
The allocation report depicts the allocation of product quantities to each sales order. The assign and unassign button helps users to assign and unassign the quantities to sell orders. If another demand of a customer need to be delivered immediately, the assigned quantity can be un-assign and satisfy the more prior demands.
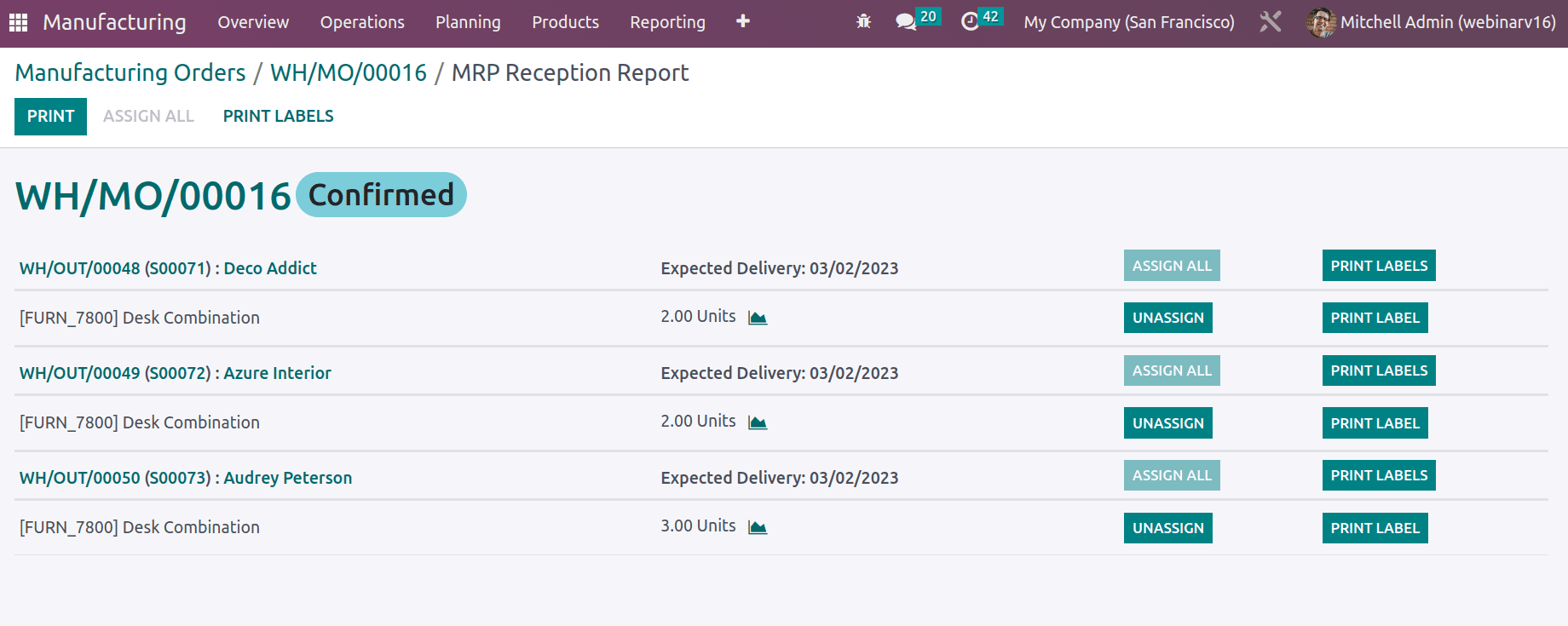
Work Order Dependencies
The Production process might involve multiple operations which work in the same or multiple workcenters. If a work center is assigned with multiple work orders, there should be an order of production, like which work order should start first and all.
The work order dependency can be enabled from the configuration settings of Manufacturing order, which will give a feature to activate ‘Operation Dependencies’ in the Bill of Materials.
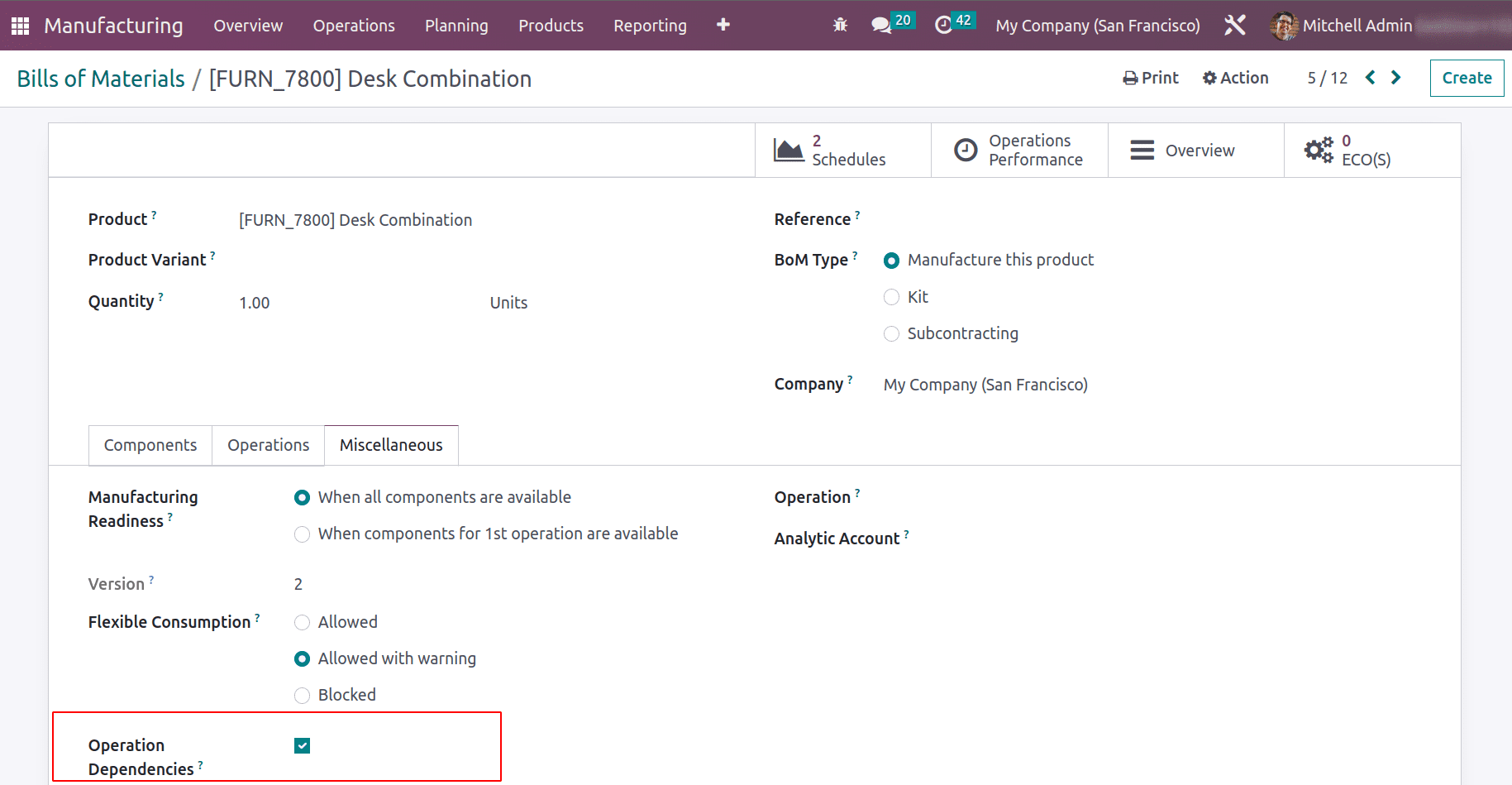
Thus operations can be blocked by other operations and the operations which have to operate can be decided. In the operations tab as operations are added, one will be able to add the operation which is blocked by another operation.
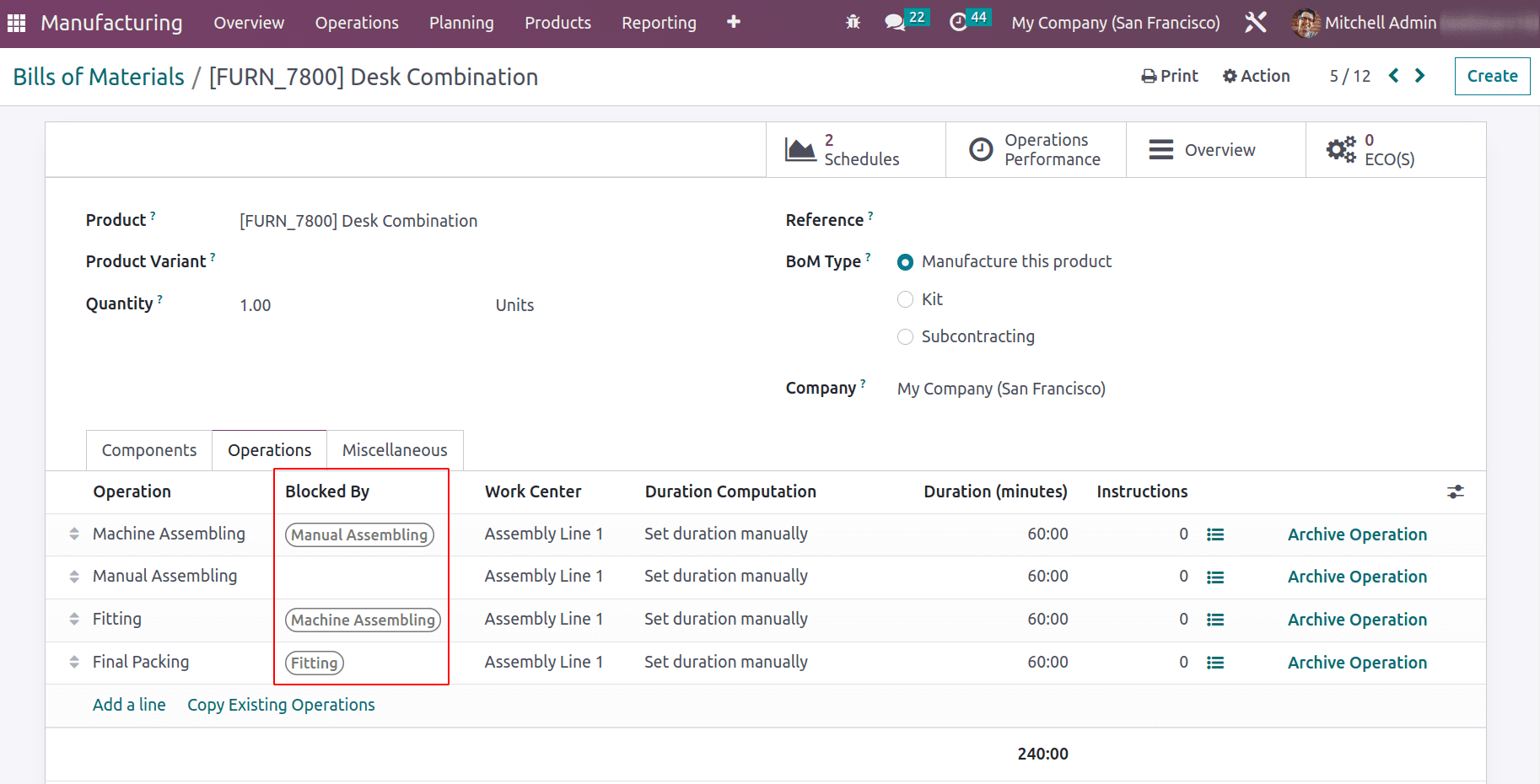
Here four operations are there: Machine Assembling, Manual Assembling, Fitting and Final Packing, where operation Final Packing is blocked by Fitting and Fitting operation is blocked by Machine Assembling and Machine Assembling is blocked by Manual Assembling. Thus the operation order is decided. Thus when an MO is planned for this product, the operation order will be Manual Assembling > Machine Assembling > Fitting > Final Packing.
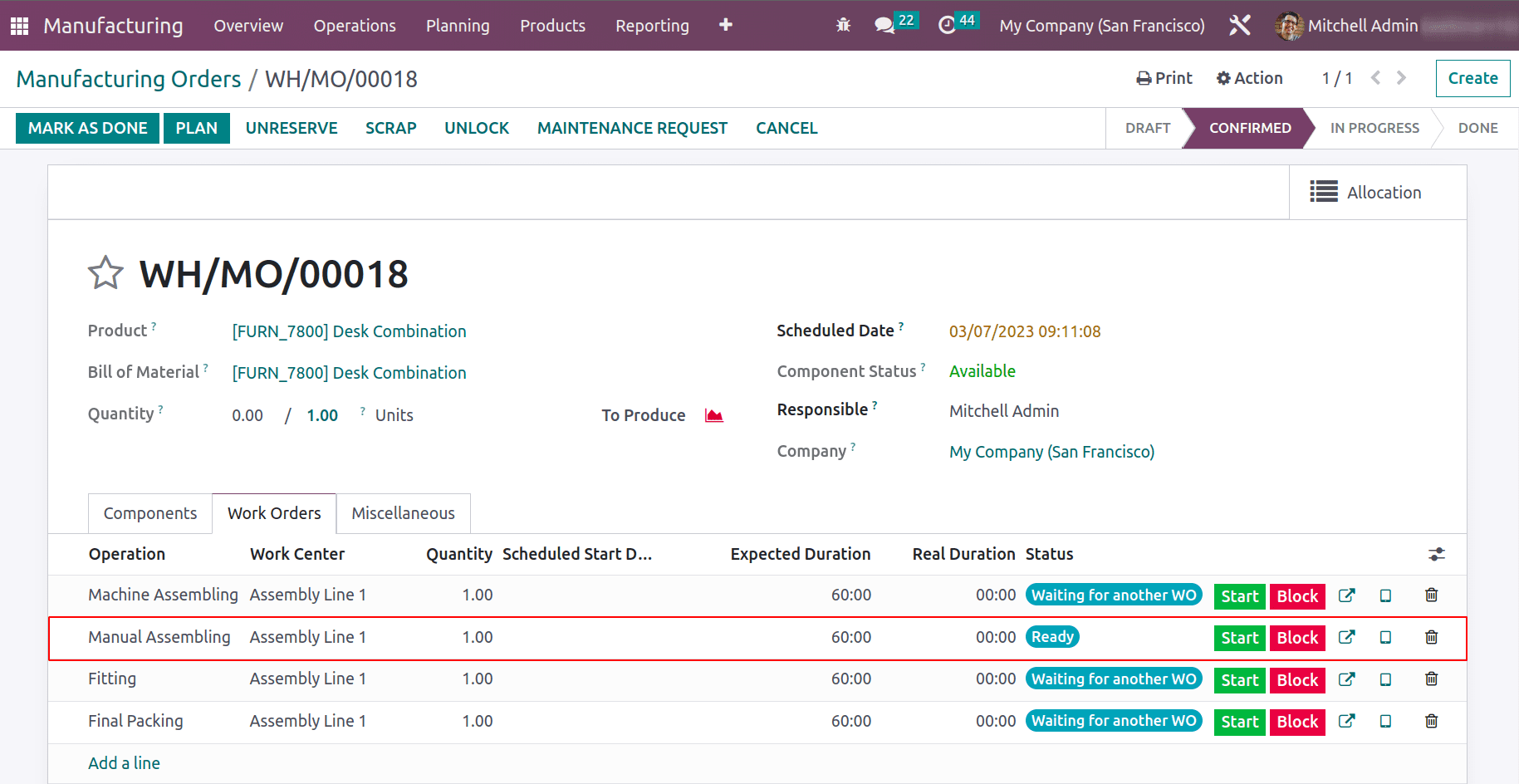
Once Manual Assembling starts and completed , next operation machine assembling will start then Fitting and the Final packing.
In the gantt view of Work Order Planning the work order dependency will be shown as below.
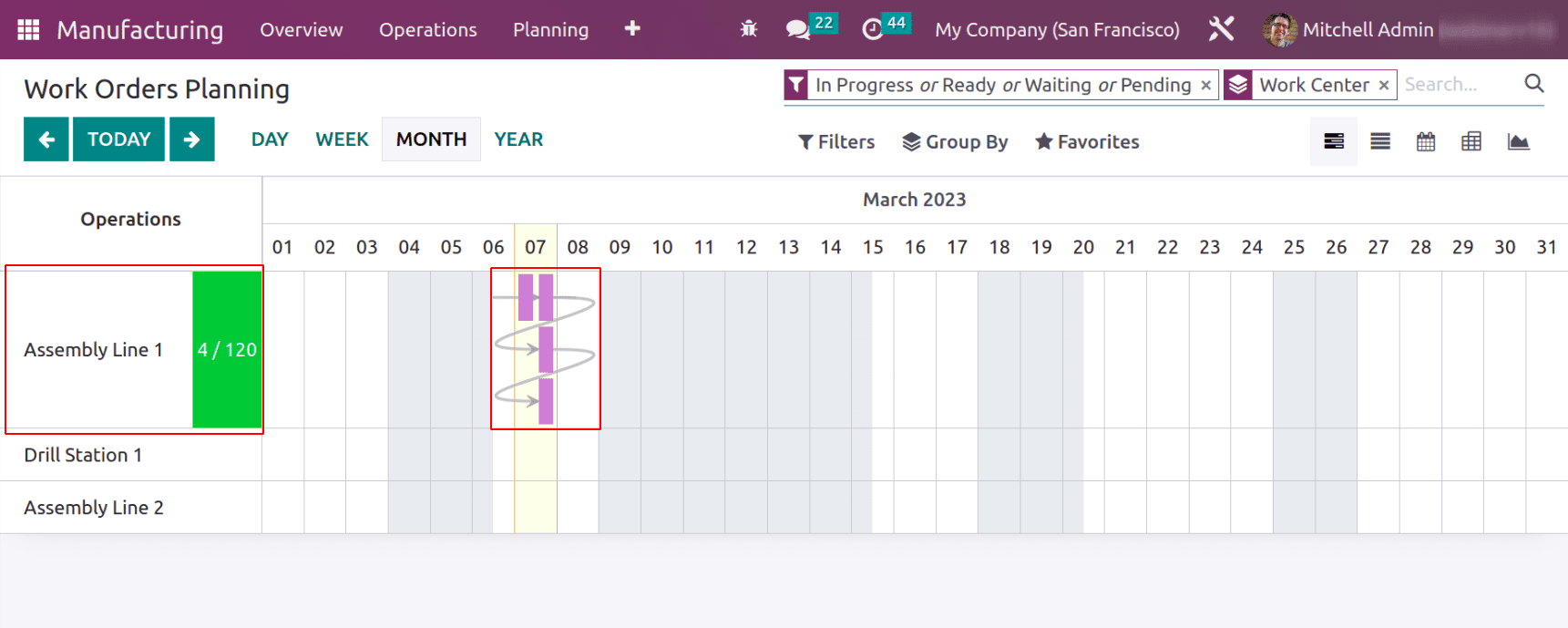
The order of work orders are represented by the arrow in the gantt and progression of the work order will be depicted in green color.
Work Order: Product Search
Now work orders can be able to search with the final product to produce. Till Odoo 15 the search will be only possible by work center and manufacturing order.
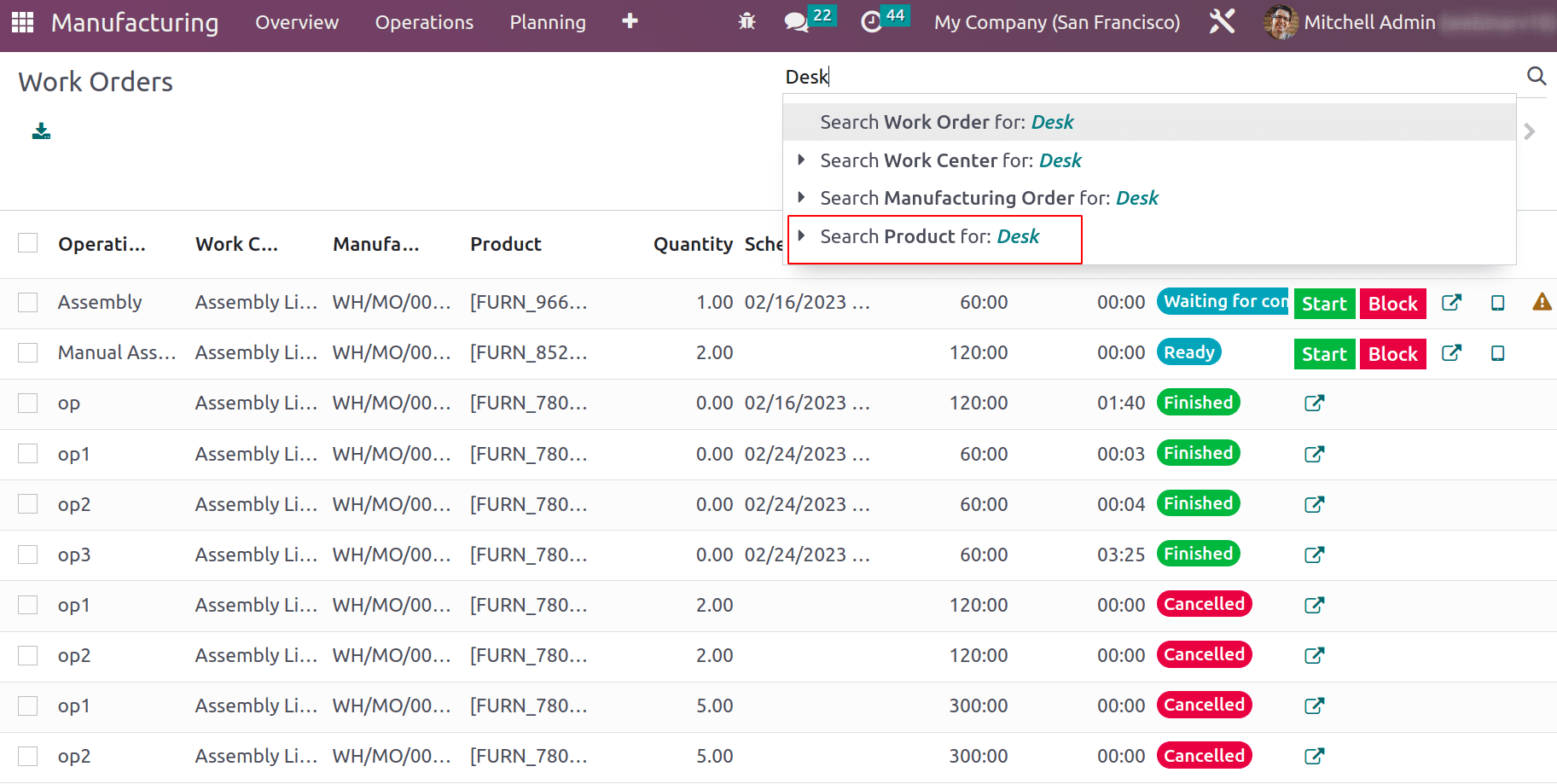
Work Center Capacity
A work center capacity defines the number of products that the workcenter can produce parallel in that workcenter. But apart from this general case, if certain products are produced in that workcenter more or less quantity can be produced than mentioned in the general case. These exceptions can be added as specific capacities.
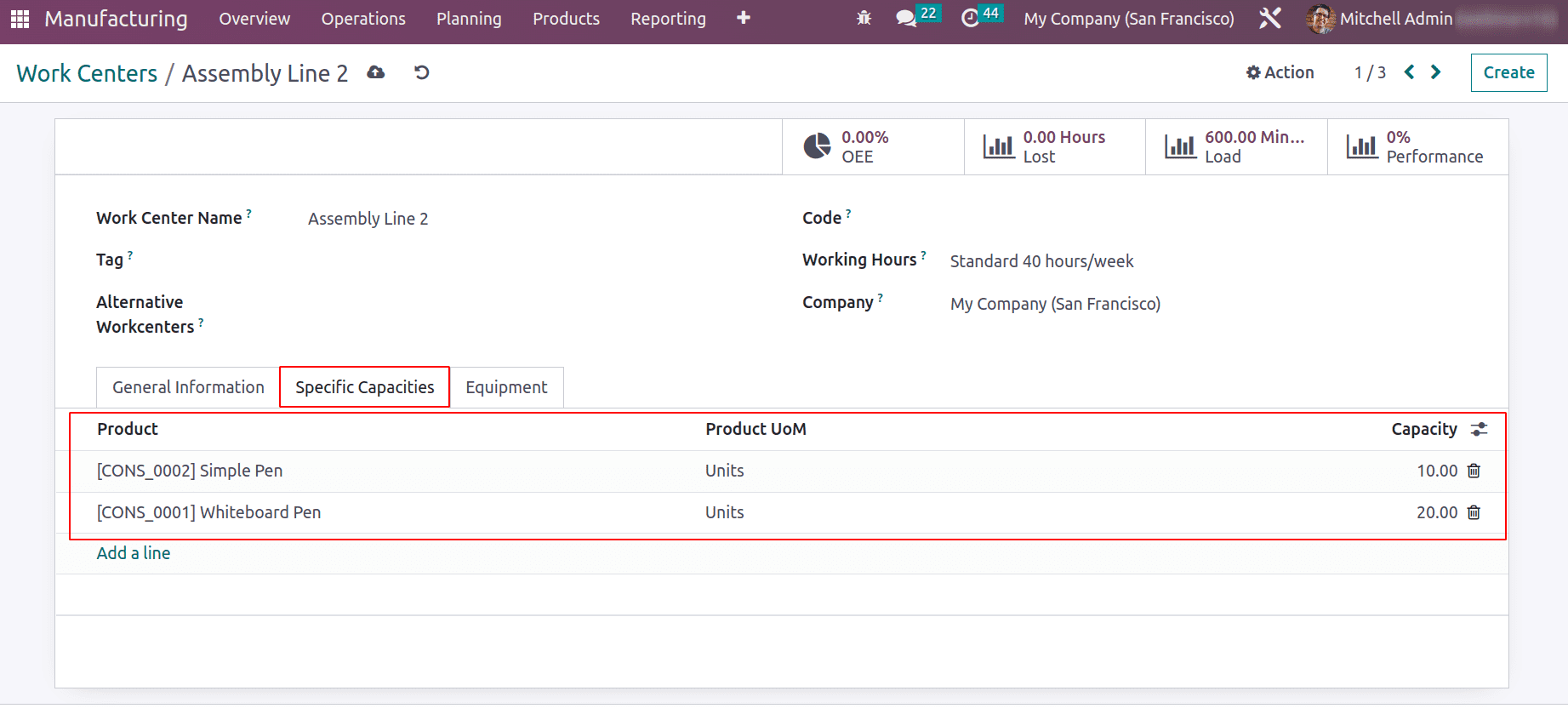
Allowed Employees for Operations
Another new feature introduced will be allowing employees to do the work orders of a workcenter. Each workcenters assigned some employee and they will be only able to process the work orders assigned in that workcenter.
In the General Information tab of the workcenter, allowed employees to that workcenter can be assigned.
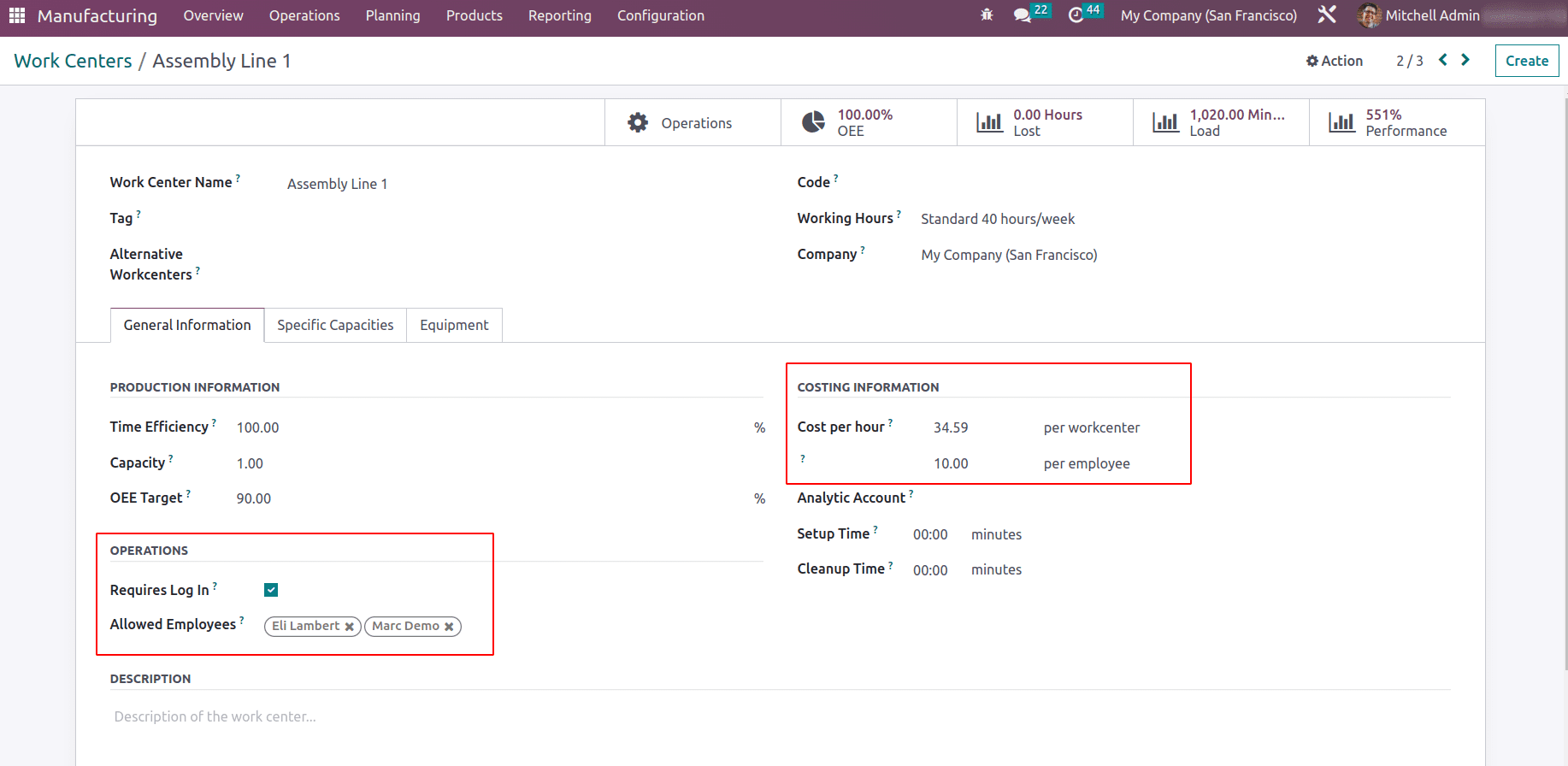
Allowed employees only able to login and complete the work order. Employee PIN to login will be added in the HR setting tab of employee form.
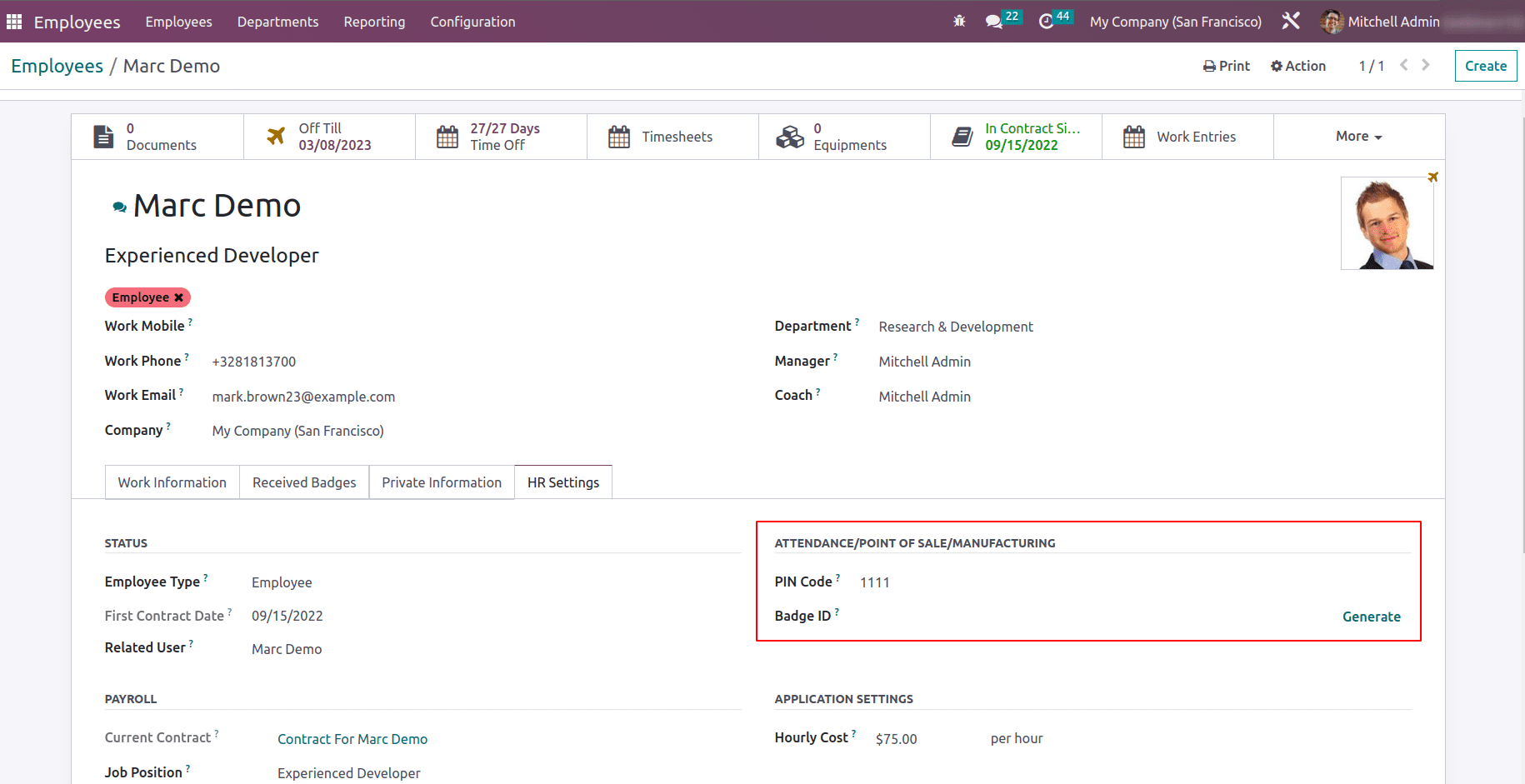
So as work order is planned there will be a LOGIN option to the workcenter.
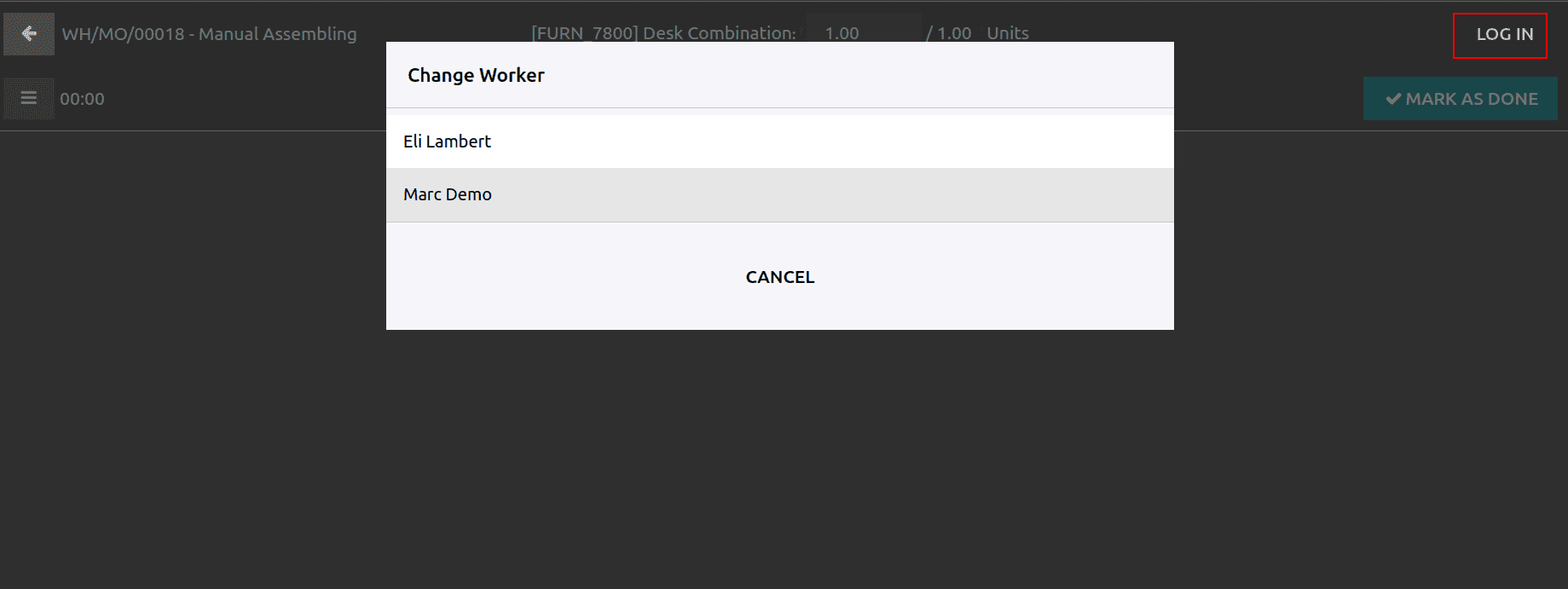
Costing Information: cost per employee
Since employees are assigned to work in the workcenters there will be a cost for employees, which can be set in the workcenter under the ‘Costing Information’. As employee works for 1 hour what will the cost, which can be updated in the respective field ‘cost per employee’
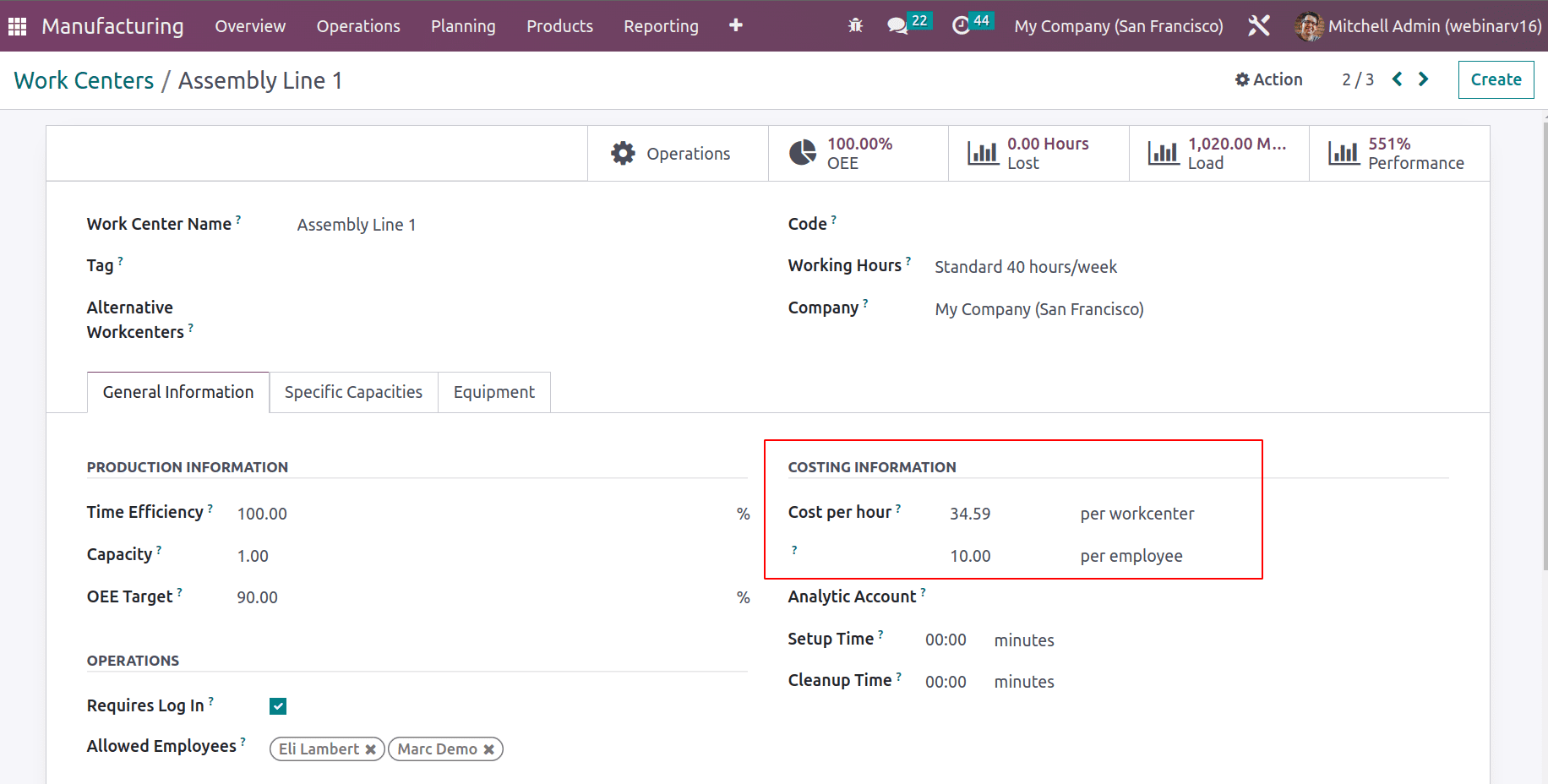
BOM Overview
An updated BOM overview will be available in the Bill Of Material, which is similar to ‘Structure & Cost’ in the earlier version.
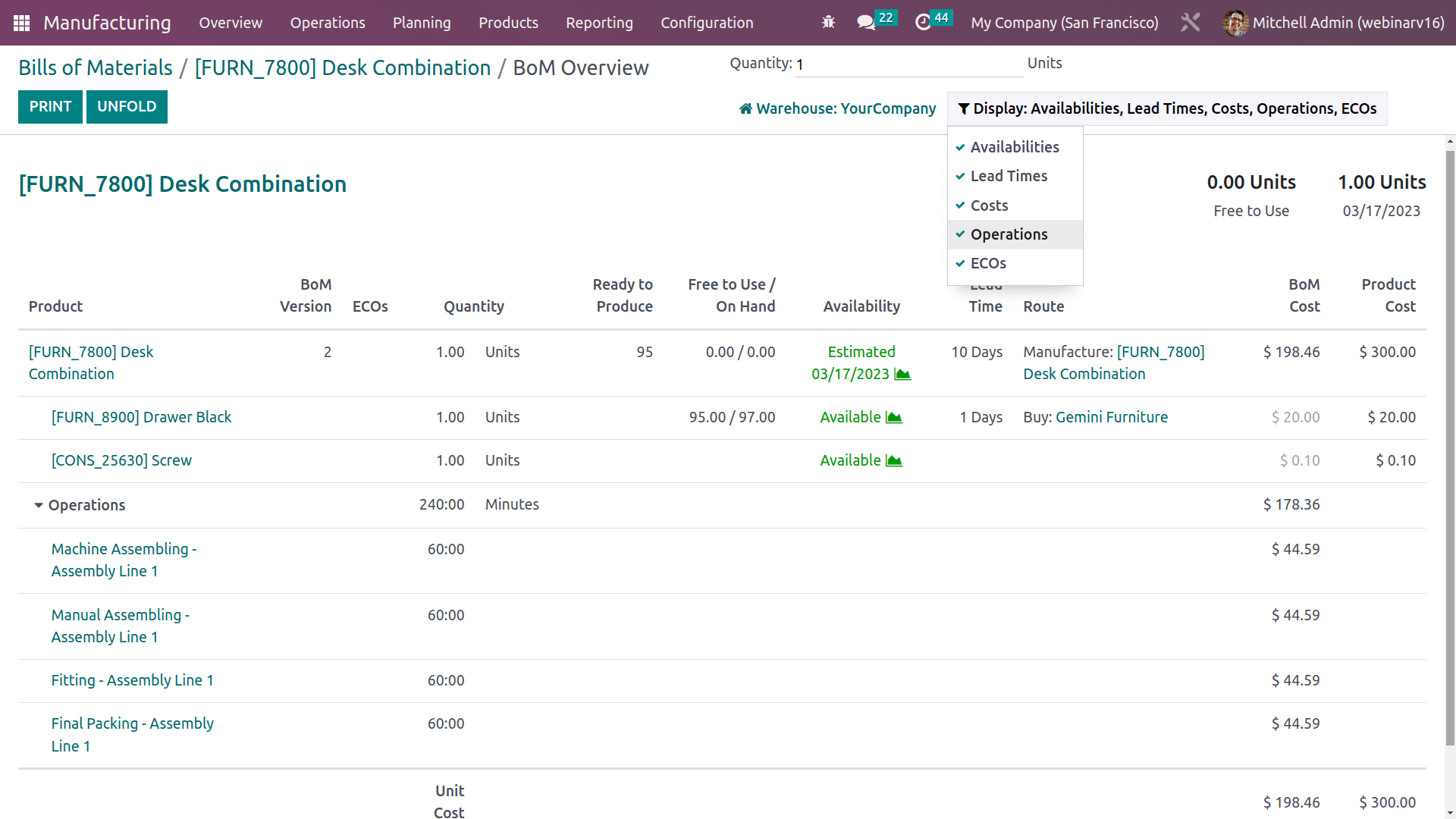
This will give clear details of BOM, Operations , Availabilities of products, lead times, costs, operations and ECOs.
Kit Valuation
The cost share feature is now introduced in the kit where the total cost share percentage should be 100%.
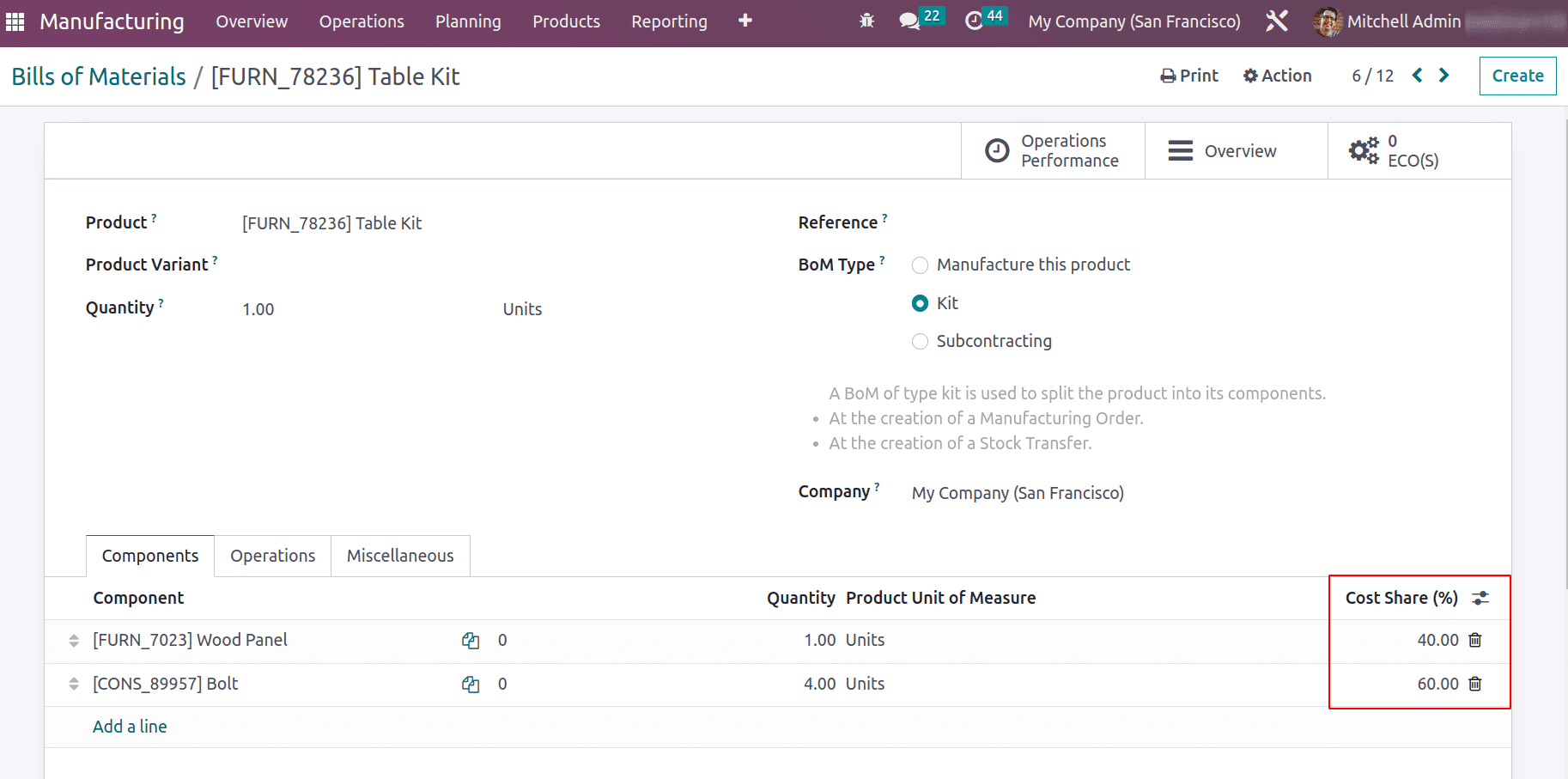
To read more about the importance of Odoo Manufacturing, refer to our industry page Odoo Manufacturing