The habit of outsourcing specific production jobs or processes to outside contractors is known as subcontracting in Odoo16 manufacturing. By utilizing specialized resources and skills, businesses can improve their manufacturing capabilities while still maintaining control over the entire production process.
Let's see how Odoo 16 Manufacturing treats subcontracting products and how the cost of subcontracting products is calculated.
Let's create a bill of material for subcontracting a product. Here, we choose the product FAN for subcontracting. For this, let's configure Subcontracting, move to the Manufacturing module and click on Configuration and Settings. There we can see the Subcontracting option. Enable the checkbox and Save the settings from there.
: Configuration > Settings > Subcontracting
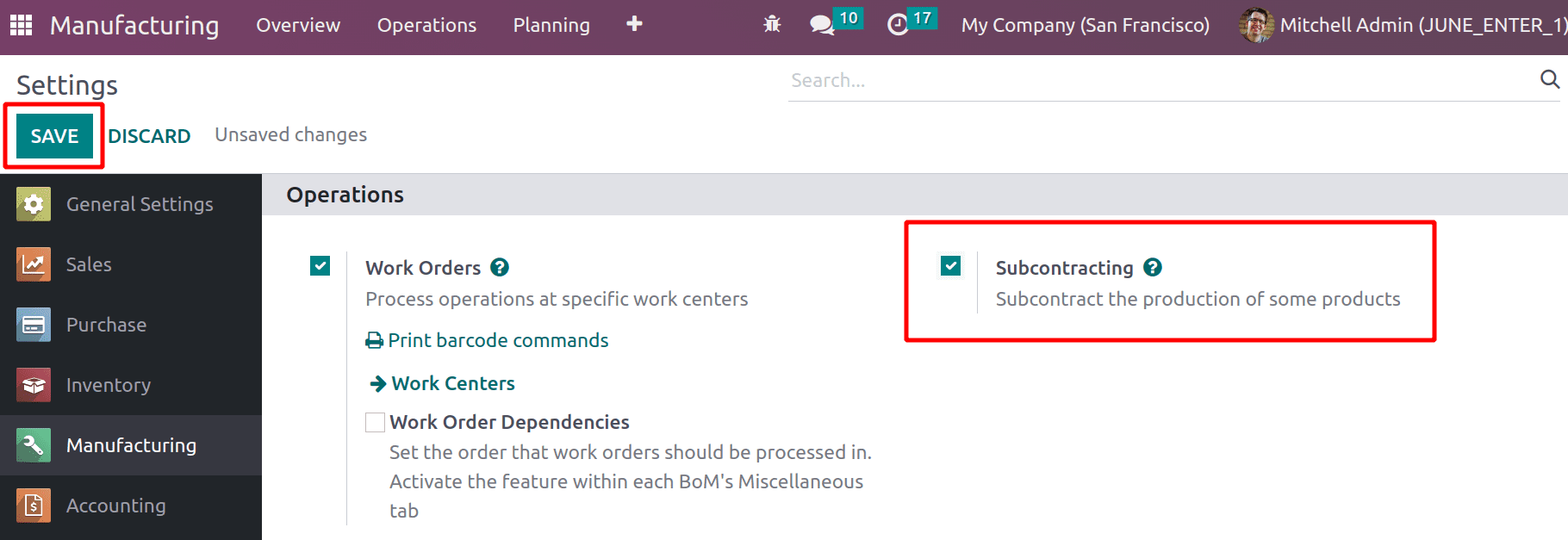
Creating a new BoM
Let's move to the Product menu and click on the Bill of Material option. To create a new one, click on the Create button.
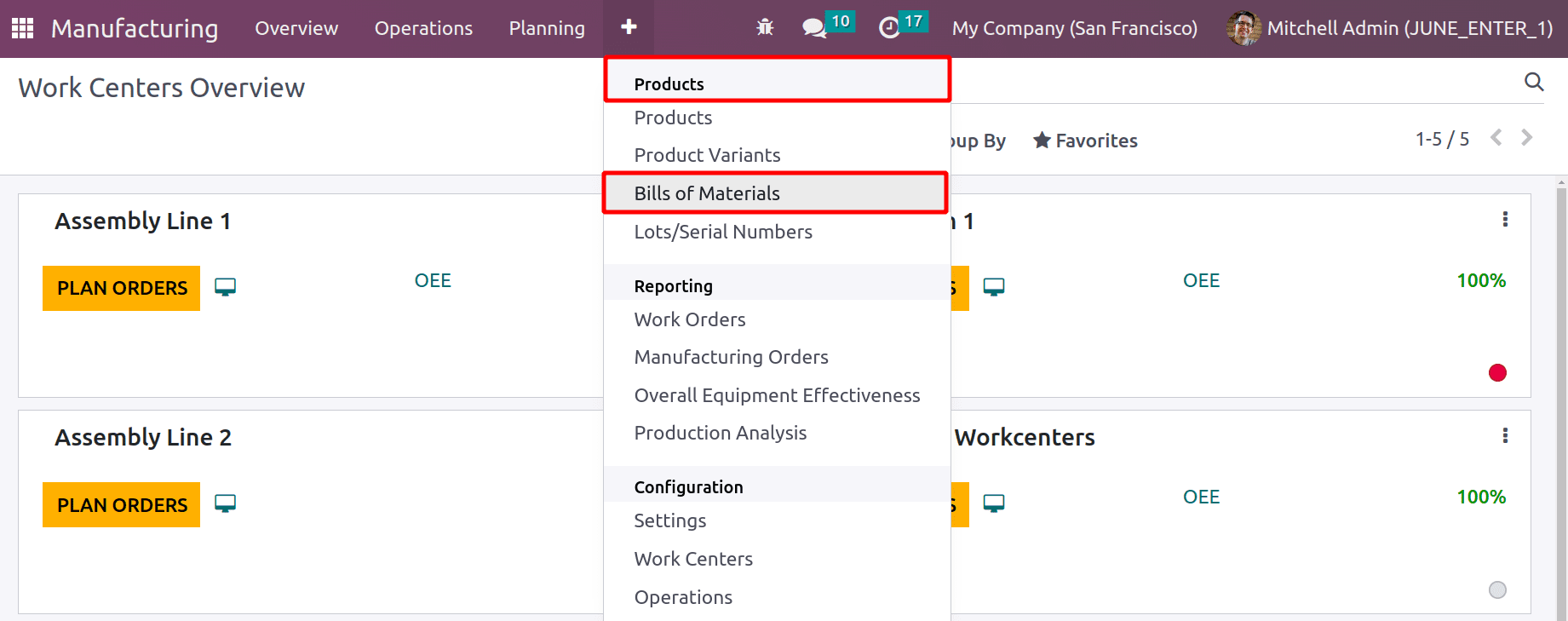
Choose the product FAN in the Product field. If there is any Variant it's possible to choose it there. Before that, let's check the settings of product FAN. We need to mention the Subcontractor, vendor price, and other details in the Purchase tab.
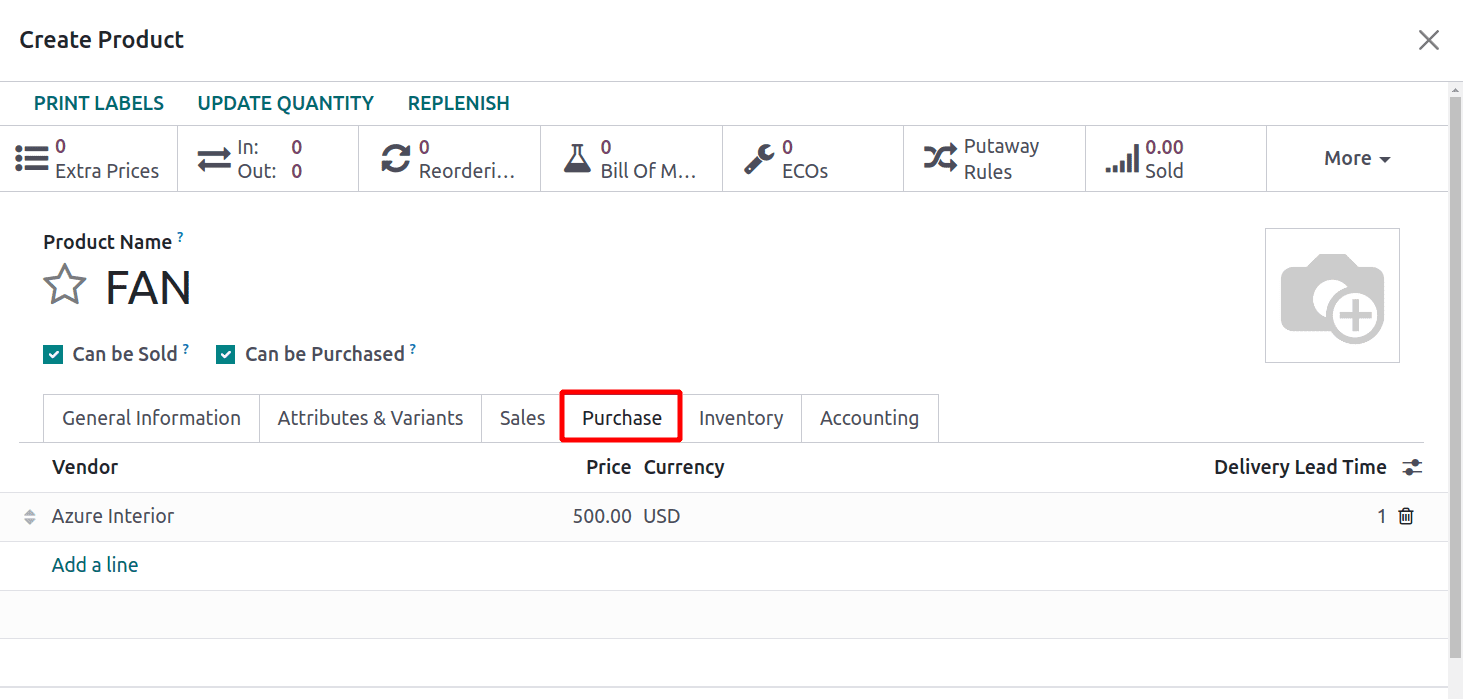
Inside the Inventory tab, mention the Routes of the product. Here the product is subcontracting to a vendor, so the Route must be Buy.
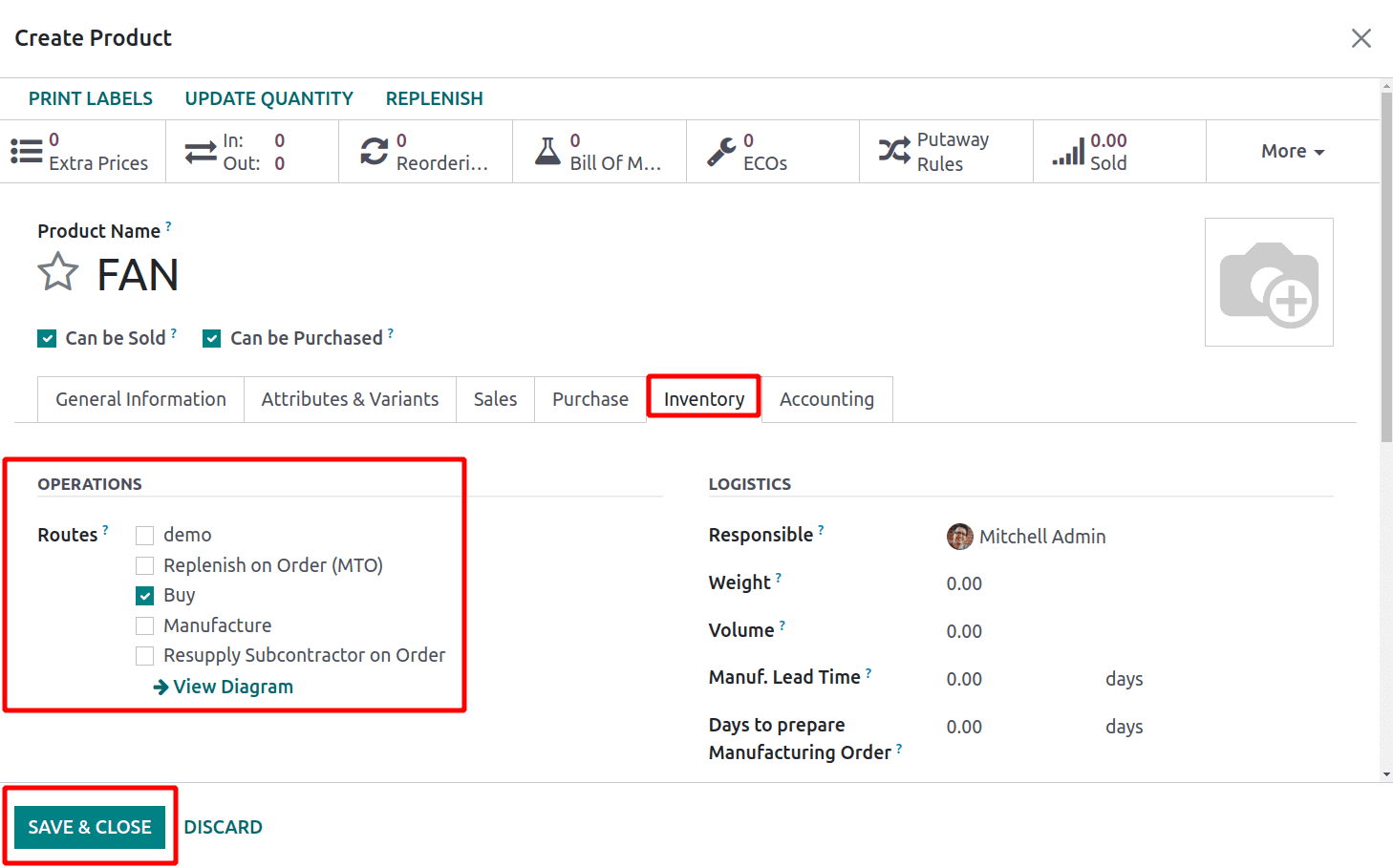
There we can see 3 Bom Types in Manufacturing, they are
*Manufacturing this product
*Kit
*Subcontracting
Here the process is subcontracting, so choose it and mention the name of the subcontractor in the specified field. In the components tab, add the components needed for the production of the finished product.
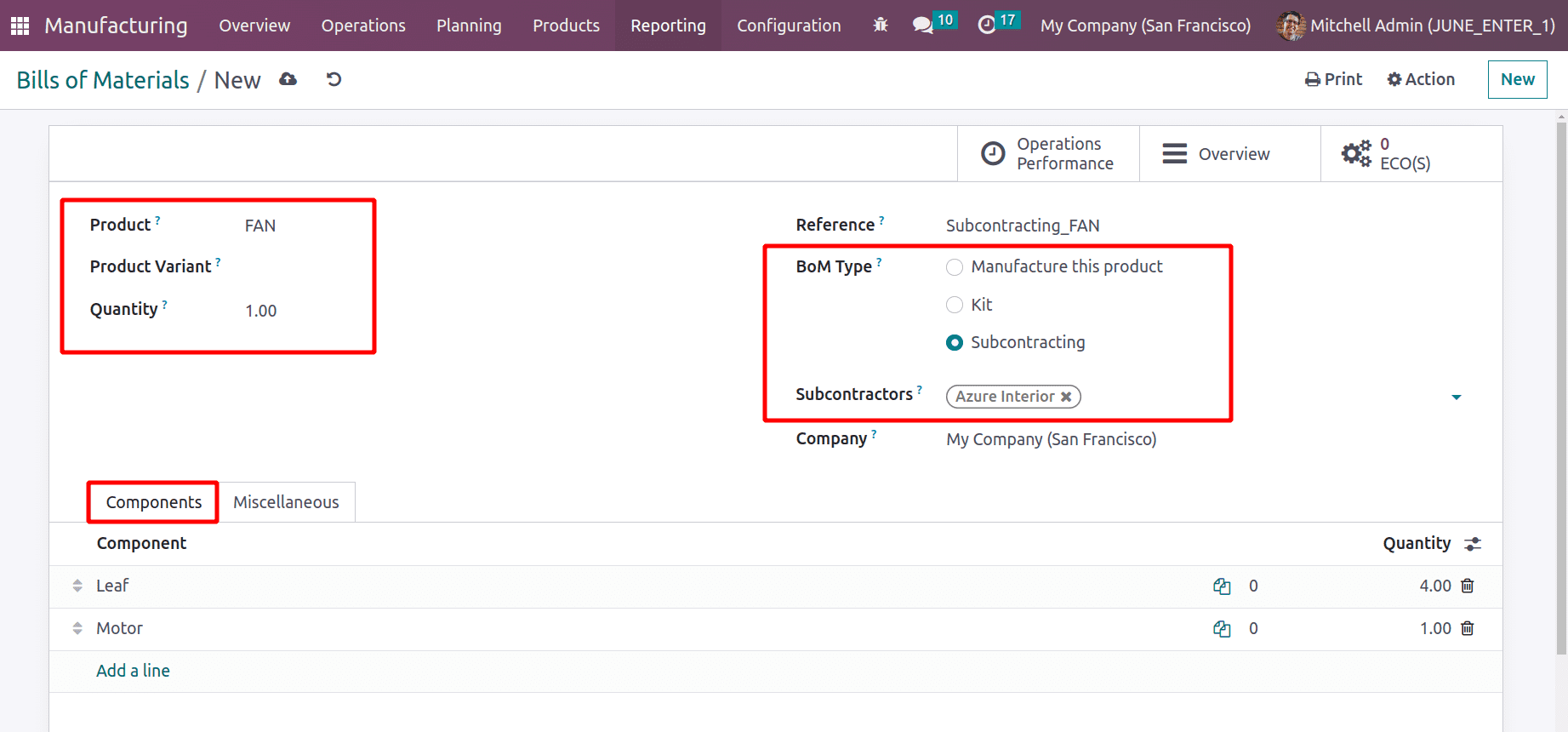
Then let's check the configuration of the components. Here the first component is Leaf, so we need to enable the route Resupply Subcontractor on Order. There is no product cost set now.
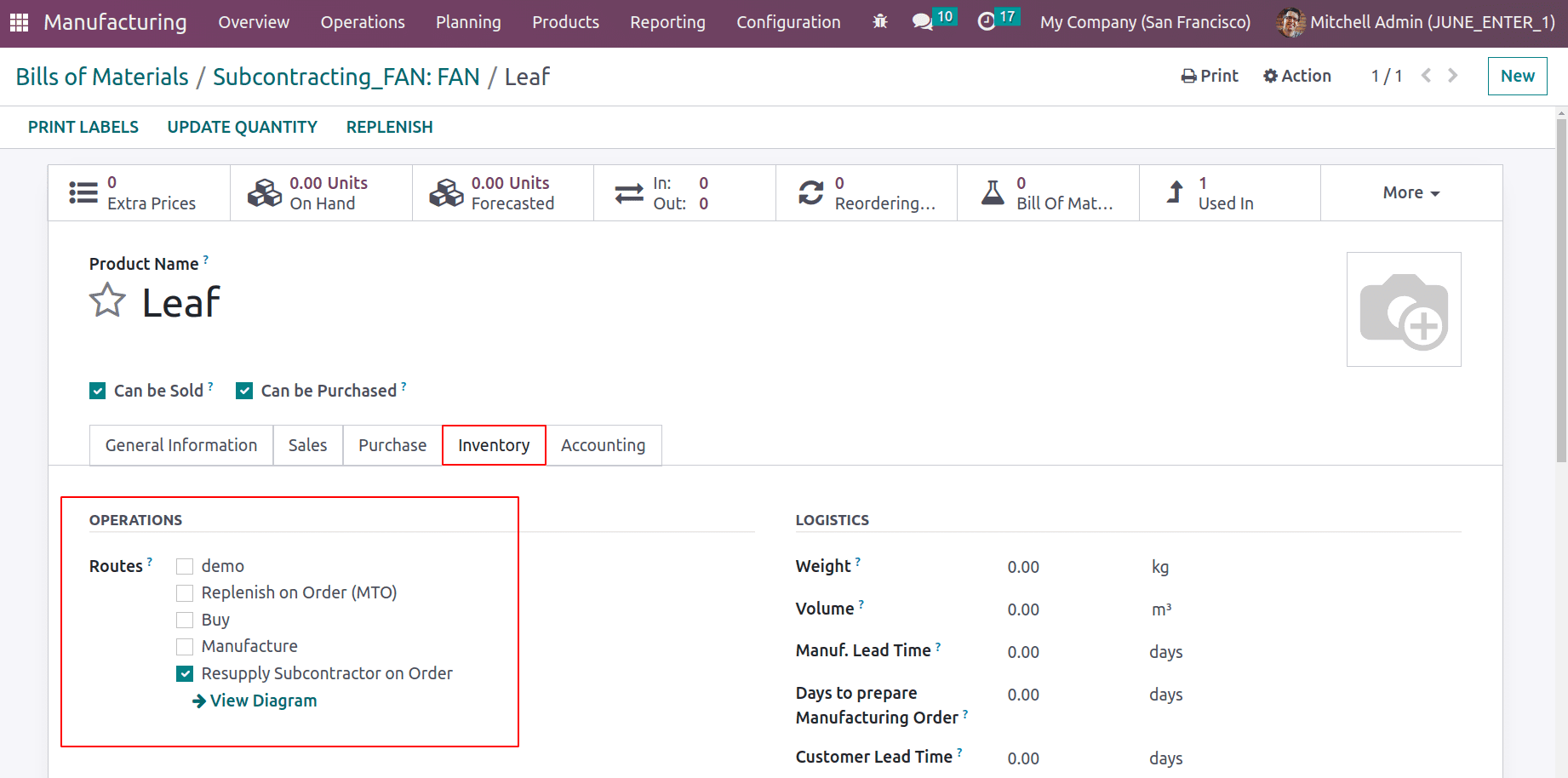
The same configuration must be done inside the second component, the Motor. The route must be a Resupply Subcontractor on Order. Here too, don't set any cost for the components.
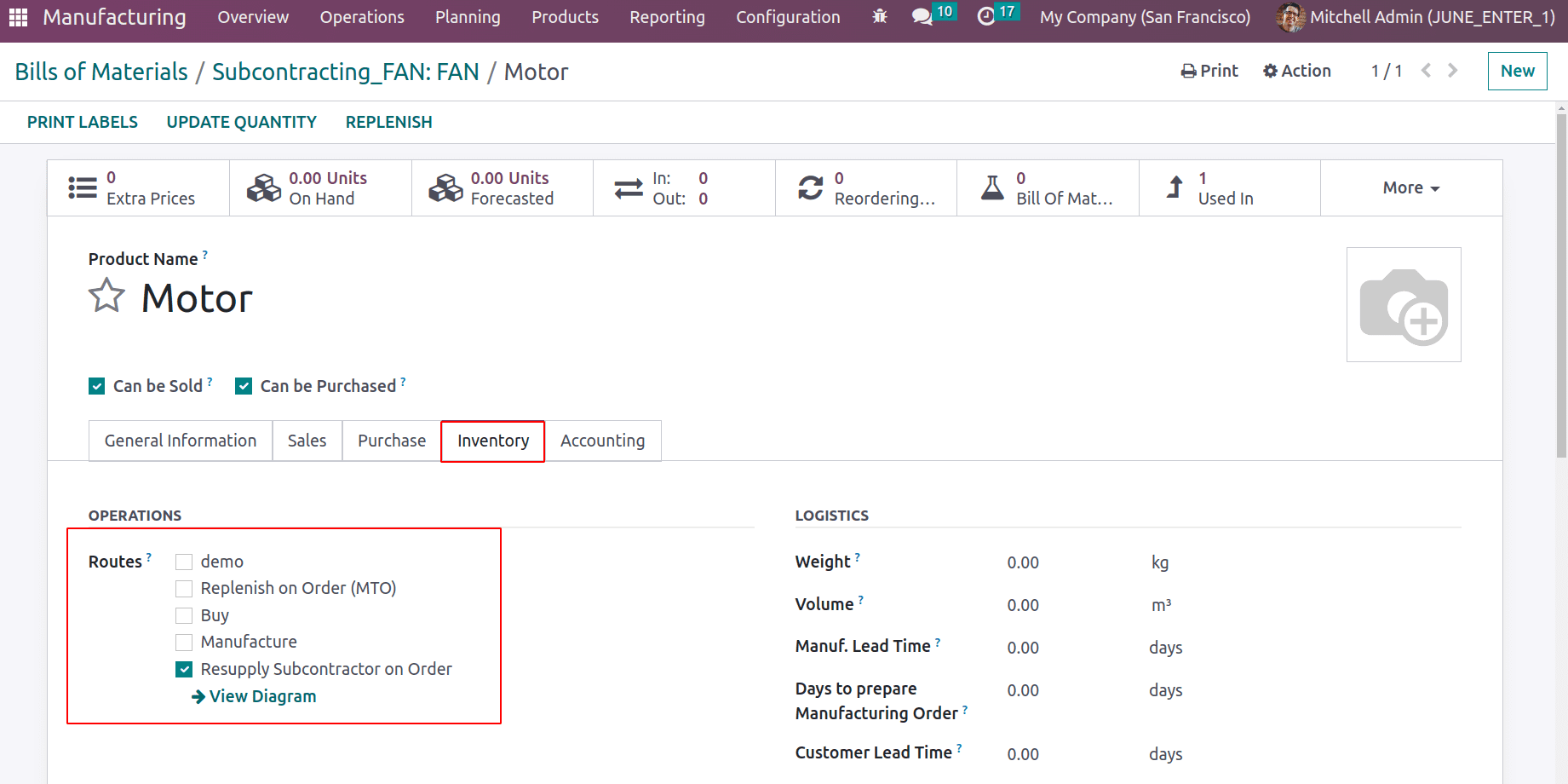
To get the stock account journals automatically, the Inventory Valuation should be Automated. For the products and components here we need to set the inventory valuation as Automated and costing method as either Average costing method or First in first out. Which can be configured inside the Product Category. When the inventory valuation is Automated, we need to specify the ACCOUNT STOCK PROPERTIES like the Stock Valuation Account, Stock Journal, Stock Input Account, and Stock Output Account, etc. The Stock Valuation Account records the number of products in stock. Stock Input Account and Stock Output are used to record the purchased or sold value. Here, the Costing method we chose is the Average Costing method.
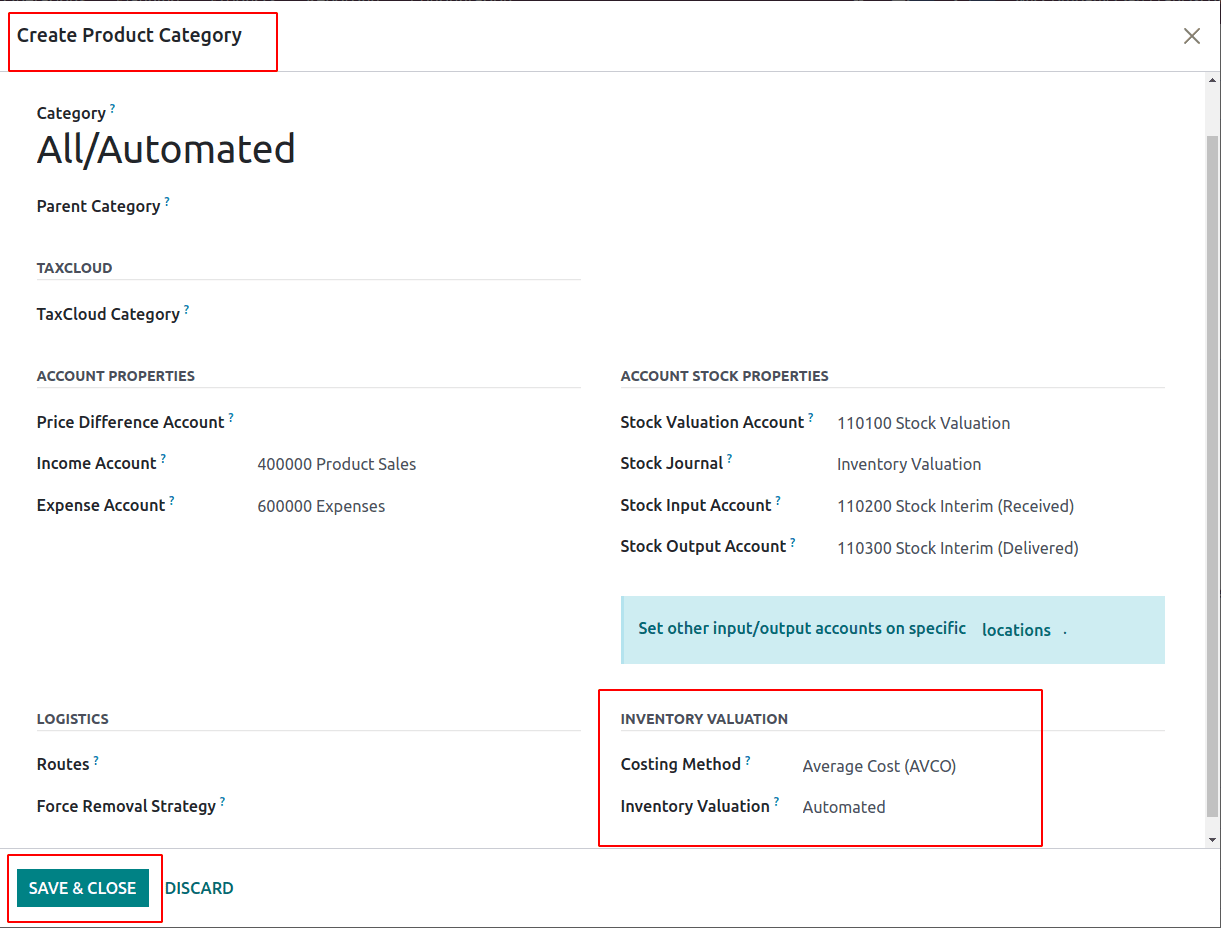
After saving the Bill of material for Subcontracting, let's move to the Purchase module, to purchase the product. Before subcontracting the product, here the onhand quantity of both components is currently zero, so first, we need to buy both components. From the purchase module, create a new Request for quotation.
Here we purchased one quantity of Motor with a cost of $75 and 2 quantities of Leaf with a cost of $100 per unit from a vendor called Deco Addict. Let's confirm and receive the product to stock.
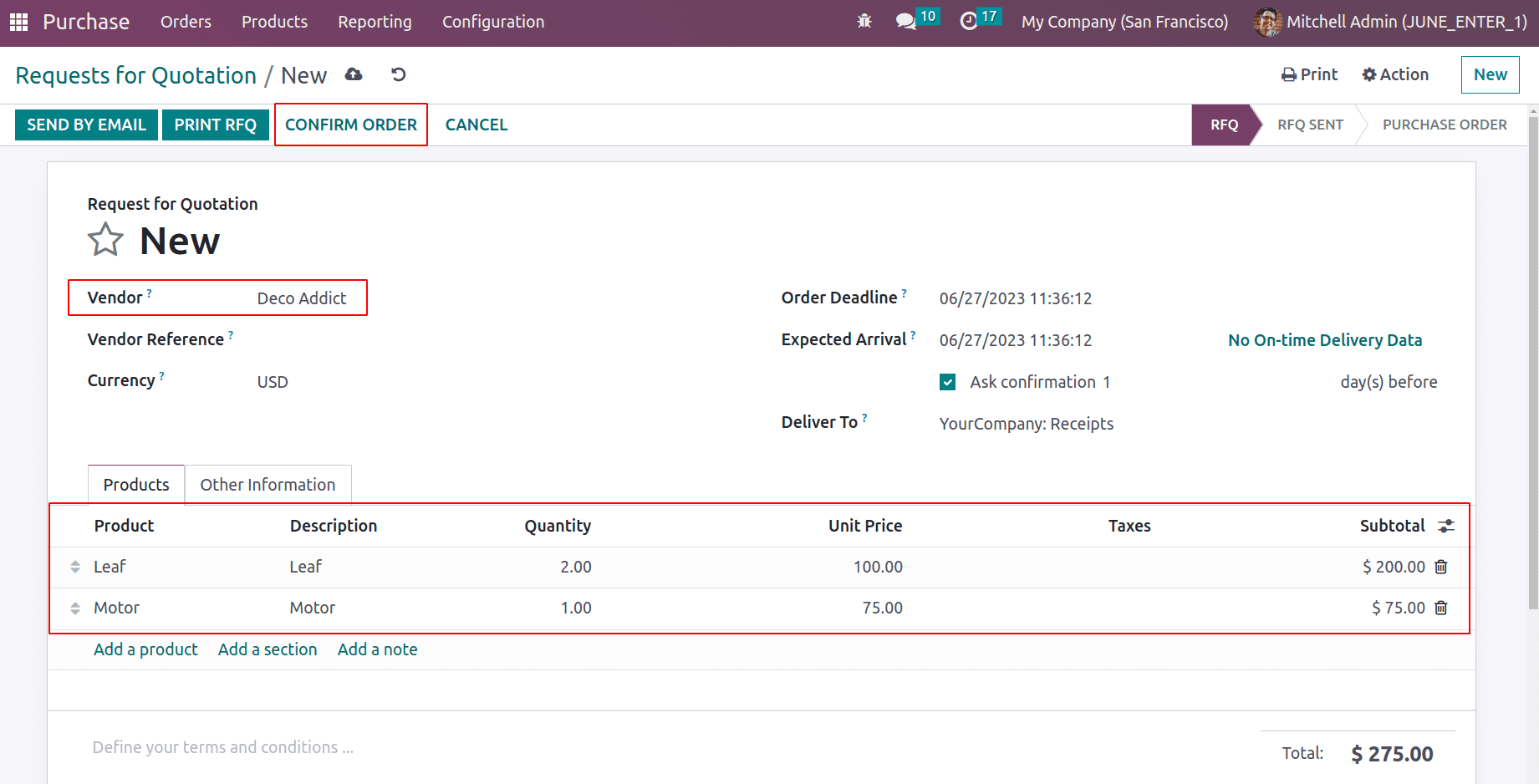
Then again purchased two quantities of Motor at a cost of $50 and 2 quantities of Leaf at $150 per unit from a vendor Gemini Furniture. Let's confirm and receive the product to stock.
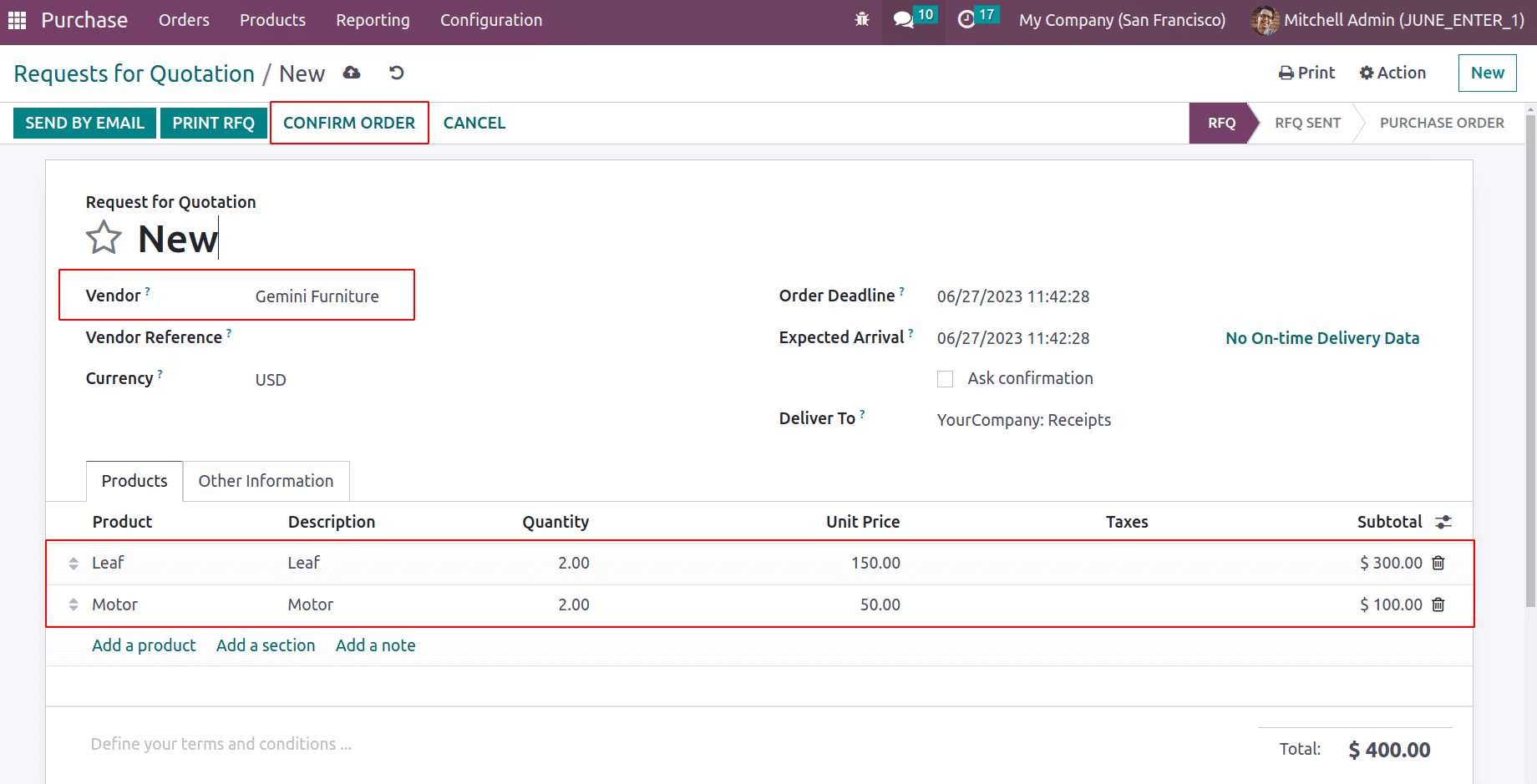
Let's check the components to see how the cost is updated. For that, let's move to the Product tab and open the first component, Leaf. Here, the cost is updated as $125. Since the product category is All/Automated, we set the costing method as Average Costing Method. The cost is updated as per the equation given below.
[(First purchase quantity * Price per unit) + (Second purchase quantity * Price per unit)] /Total purchased quantities.
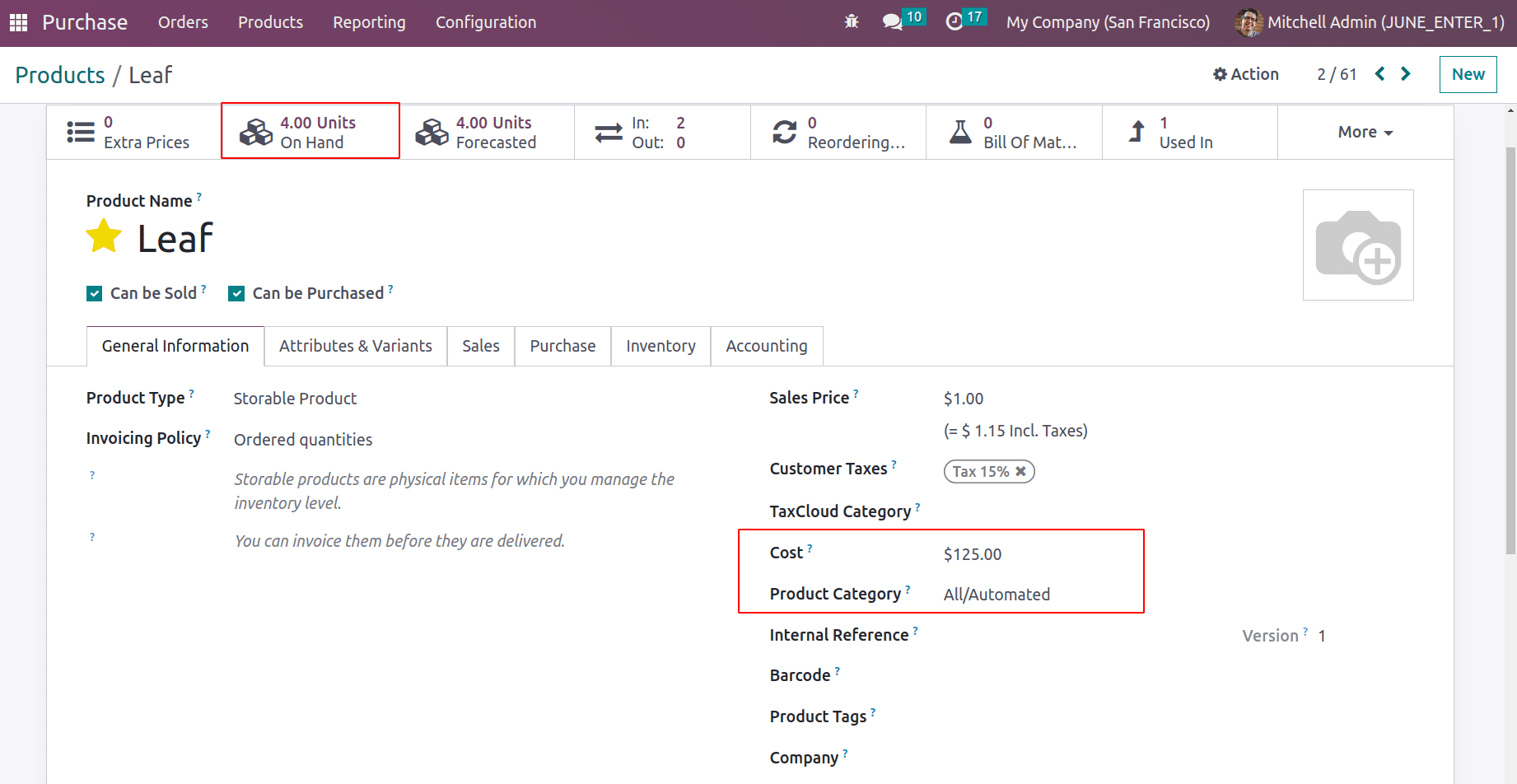
So here we have two purchased orders of 2 quantities with prices of $100 and $150. So
(2*100)+(2*150)/4= 125
The second component is the Motor. So the same product category is added for this product too. Let's check the cost of the Motor, which is updated as $58.33.
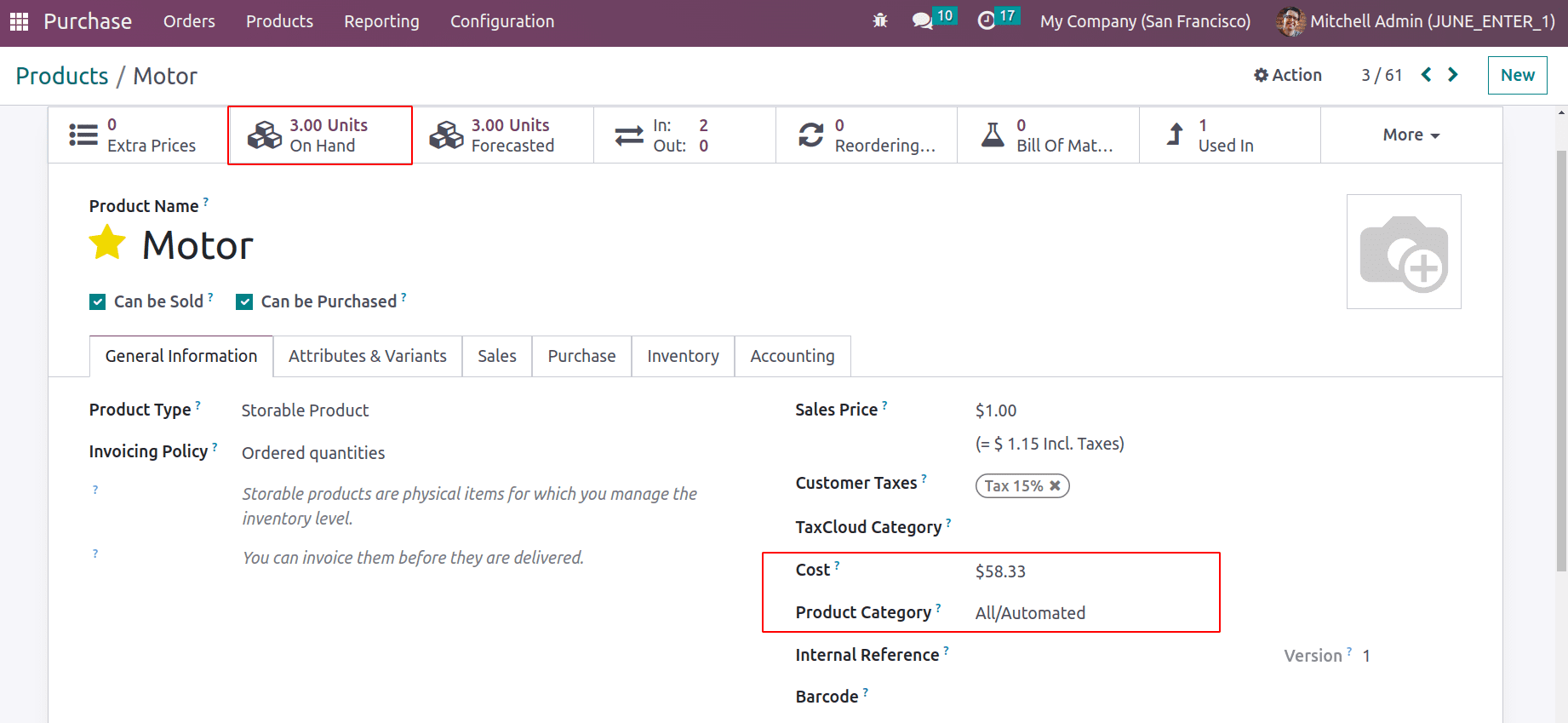
As Average Costing Method, the cost is updated as per the equation = (1*75)+(2*50)/(1+2)=58.33.
Now the components are available. Let's subcontract the product FAN. For that, first, we need to purchase the product from our subcontractor, Azure Interior.
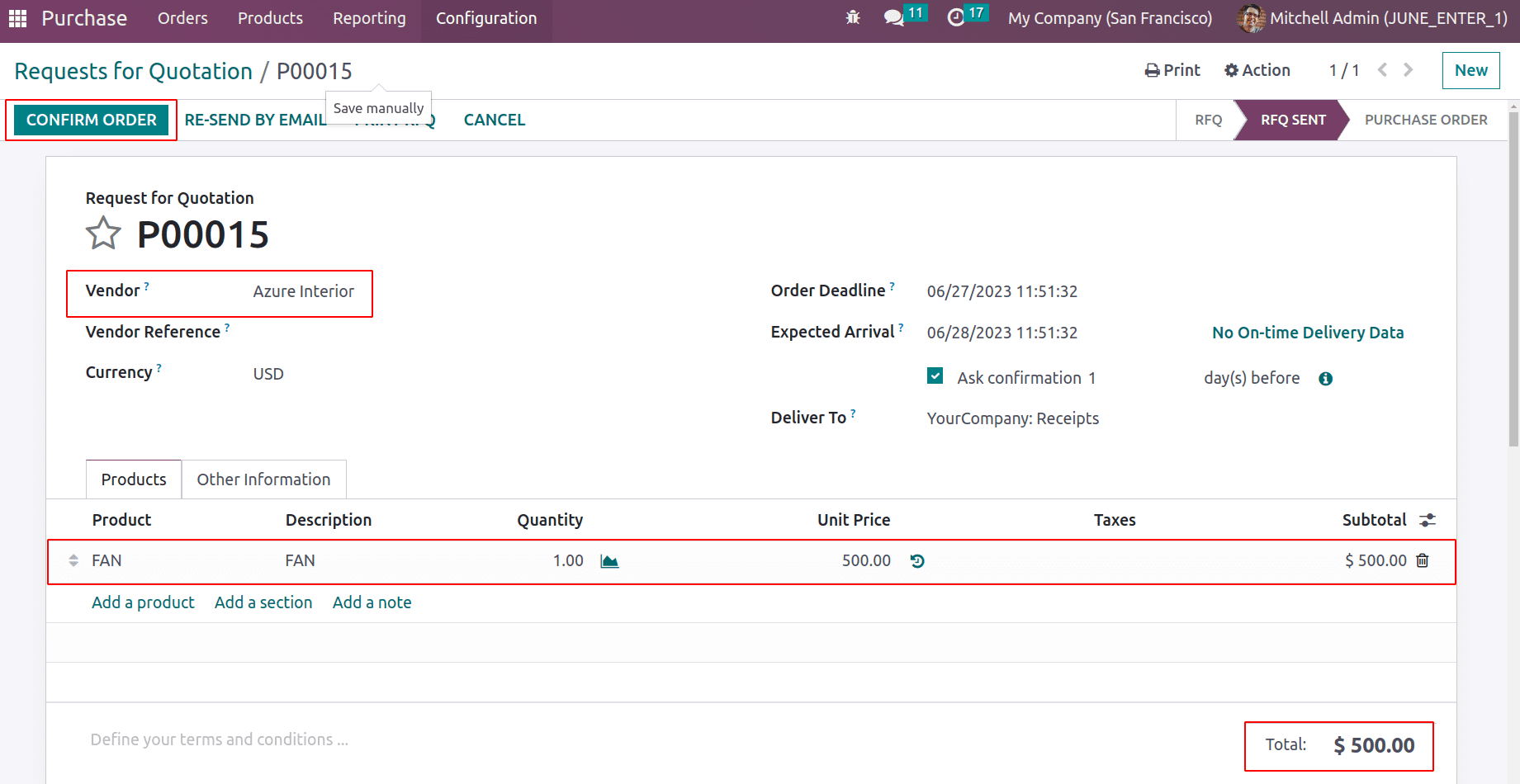
Here the vendor is the same subcontractor that we mentioned in the product FAN. After confirming the order, two smart tabs appear, one is Resupply and the other one is Receipt.
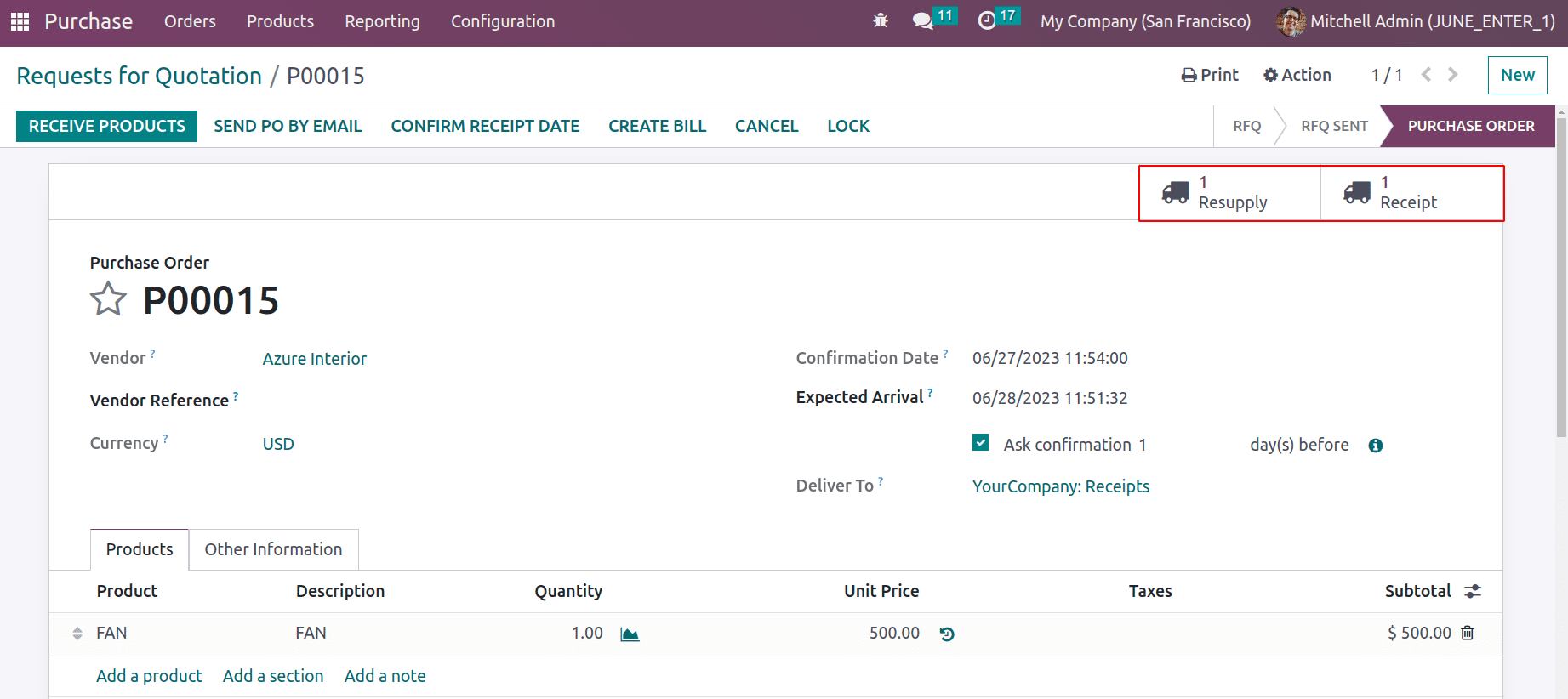
First, we need to choose the Resupply. Because before purchasing the product from the vendor, we need to supply the components to the vendor. When we open the Resupply option, we see the two components, the Motor and the Leaf, with the quantity mentioned inside the Bill of Material automatically added there.
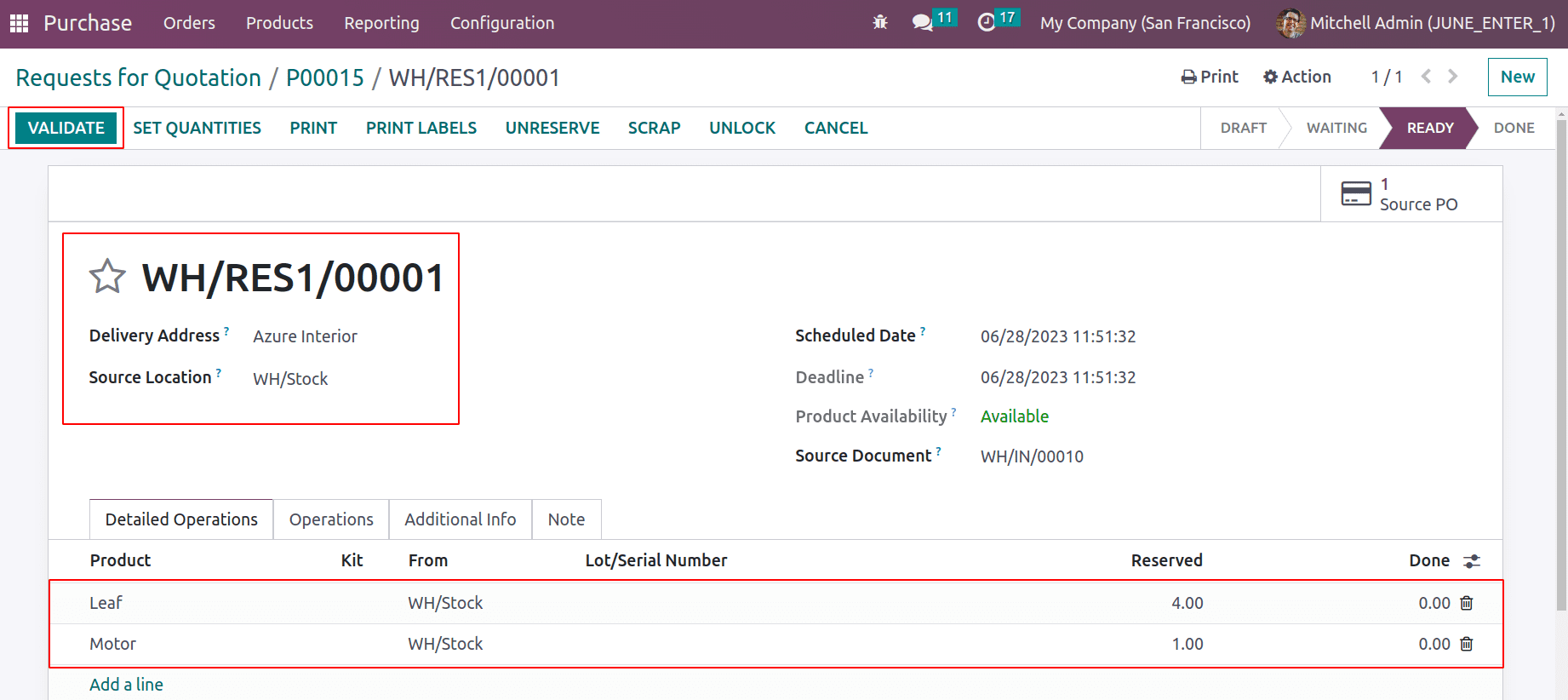
And the source location is WH/Stock, and the Delivery Address is ‘Azure Interior,’ which means the components are resupplied from our warehouse to the subcontractor.
Let's validate the resupply. Here the delivery address is Azure Interior, and the Source location is WH/Stock, which means the products are taken from stock and supplied to the Subcontractor just to validate it to complete the Resupply.
Once the components are supplied to a subcontractor, they can produce the finished product and send it back, which is referred to as the receipt.
Then open the Receipt and receive the product FAN. Here the product is received from subcontractors, and the destination is our inventory stock location.
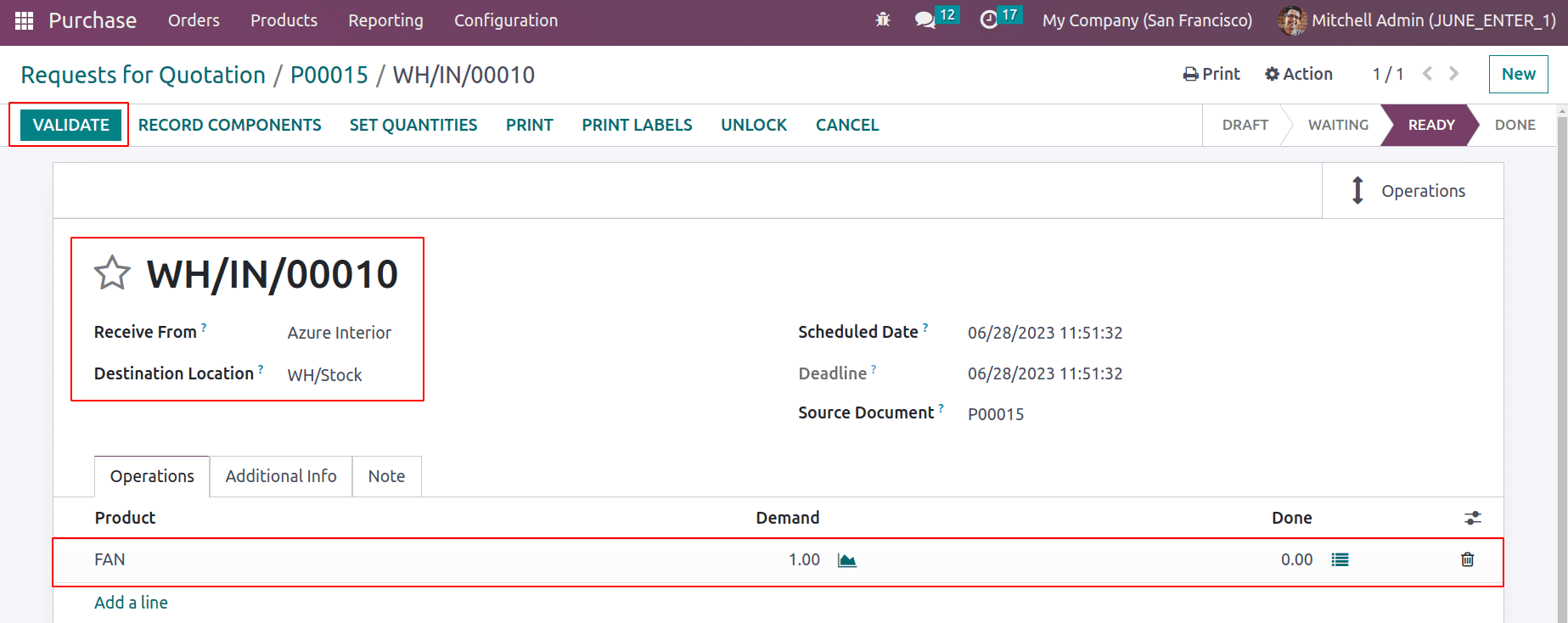
Validate the order to get the product to stock. Now the Subcontracting process is completed.
Let's check the cost of the product, FAN. For that, click on the Product menu and choose the option Products, and search for the product FAN from the list. Here, the product cost is updated as $1,058.33.

Here, before Subcontracting, the product cost was $500. To buy the product FAN from the subcontractor company resupply two products to the subcontractor. Four quantities of Leaf cost $125 each, and one quantity of Motor cost $58.33. So the total expense for resupply is (125*4)+(1*58.33)=558.33
So this expense is added to the current cost of subcontracting products, which means the product FAN has a current cost of $500. After completing the subcontracting process, the cost is updated as $1,058.33. Because the total subcontracting cost is added to the current cost.
$500 + $558.33 = $1,058.33
We can see the stock journals from the Accounting Module. For that, go to the Accounting tab and choose the Journal Entries option.
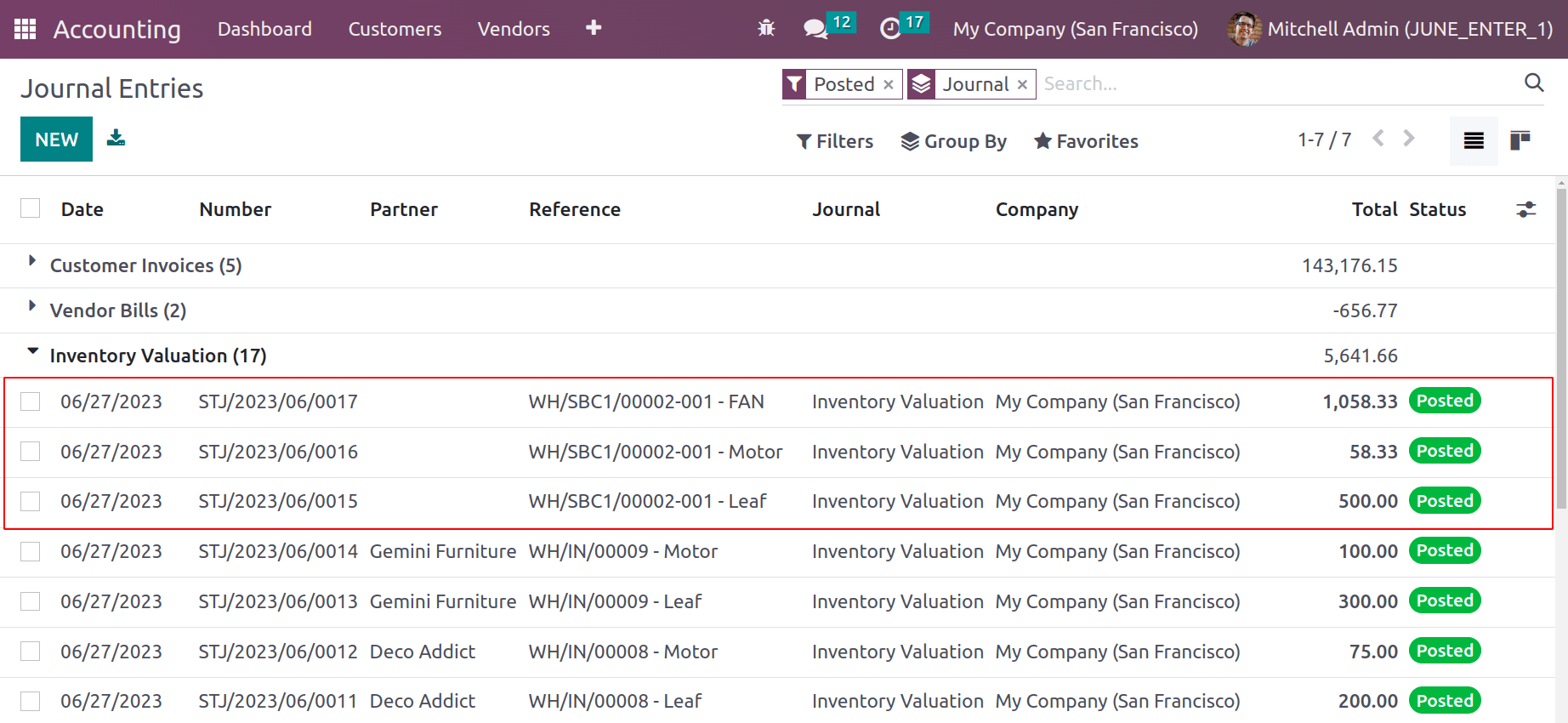
In conclusion, subcontracting in manufacturing with Odoo16 can be a useful tactic for companies looking to streamline their production processes and satisfy customer expectations. Companies may simplify operations, boost productivity, and ultimately attain better flexibility and competitiveness in the market by utilizing external resources and knowledge.