It is important to make sure that there is always a minimum quantity on hand for some products at all times. It is possible to automate reordering such that a purchase order is generated automatically if the quantity on hand drops below a predetermined level by adding a reordering rule to a product.
Odoo offers a comprehensive solution for all business-related issues, and as such, it contains reordering procedures that will ensure that your catalogs never go out of stock.
In essence, Odoo reordering rules are the framework of a set of rules that aids the user in creating rules to fill out their warehouse with stocked goods.
Let us check how the reordering rule works in Odoo 16 Inventory, for which lets us create a product with the product type as Storable product, which will maintain the stock in the inventory and the one which can be purchased.

Once the product is marked to be purchased make sure that vendor is mentioned for the product under the Purchase page of the product form, as shown below.
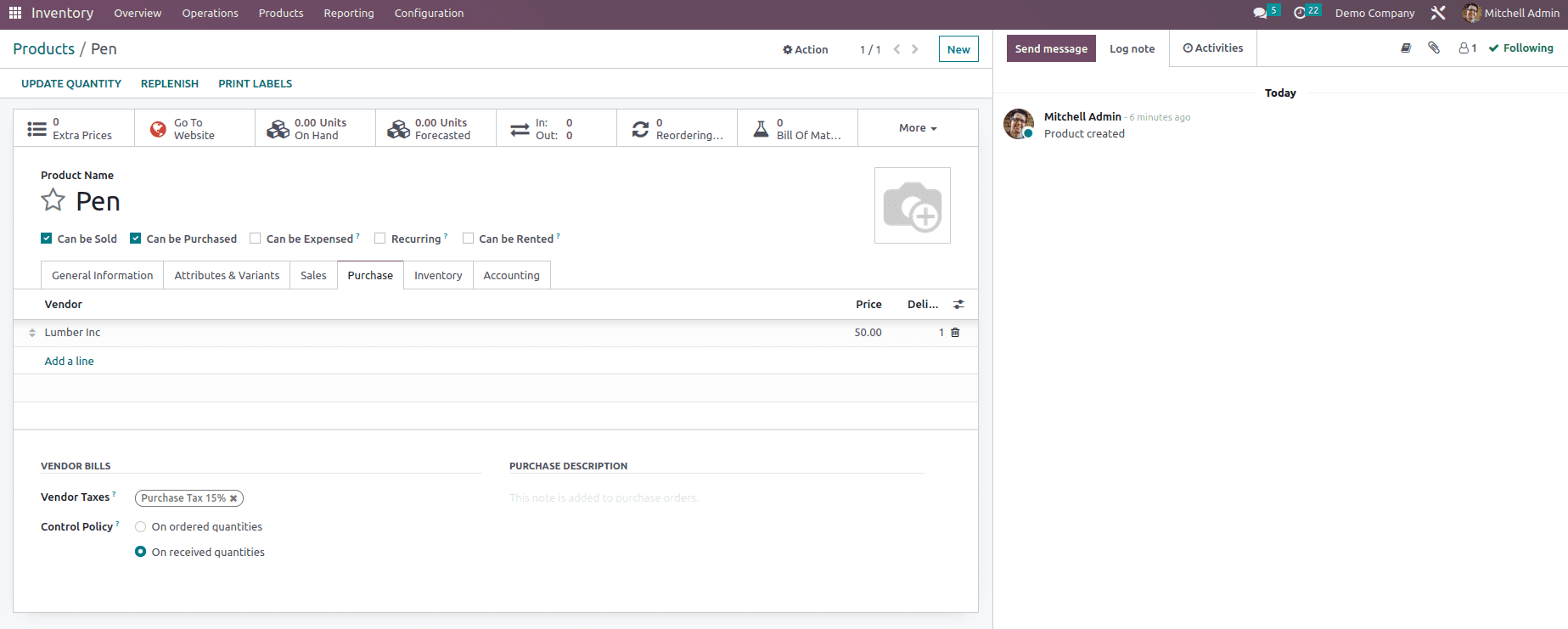
Vendors are included under the buy tab. Multiple vendors can be added, and when the minimum stock is reached, it will send out a request for quotes to each seller. If there are many vendors, the one who is mentioned first in the list is given preference.
Now in the product form, we can see that the On Hand of the product is zero, which means that there is not enough stock of the product in the inventory, so in order to manage the insufficient stock of product, let's use the Reordering feature.
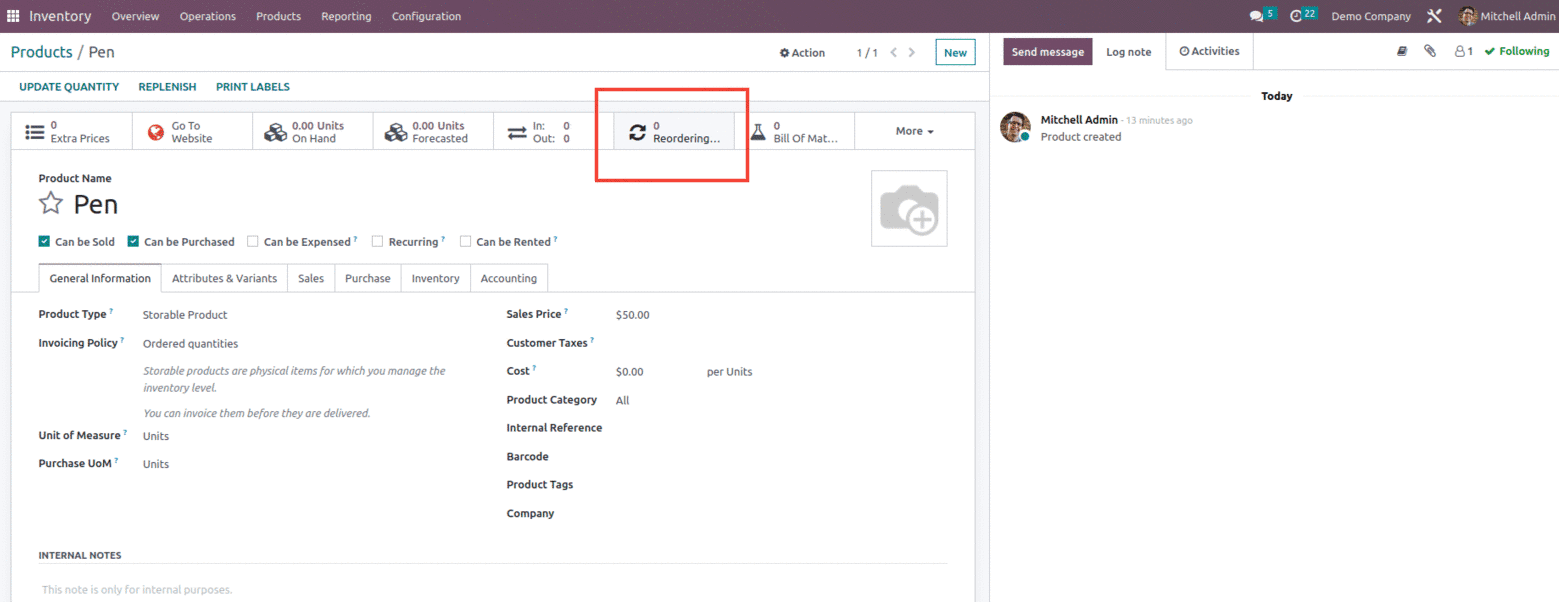
Let's see how to set up the Reordering rule for the product.
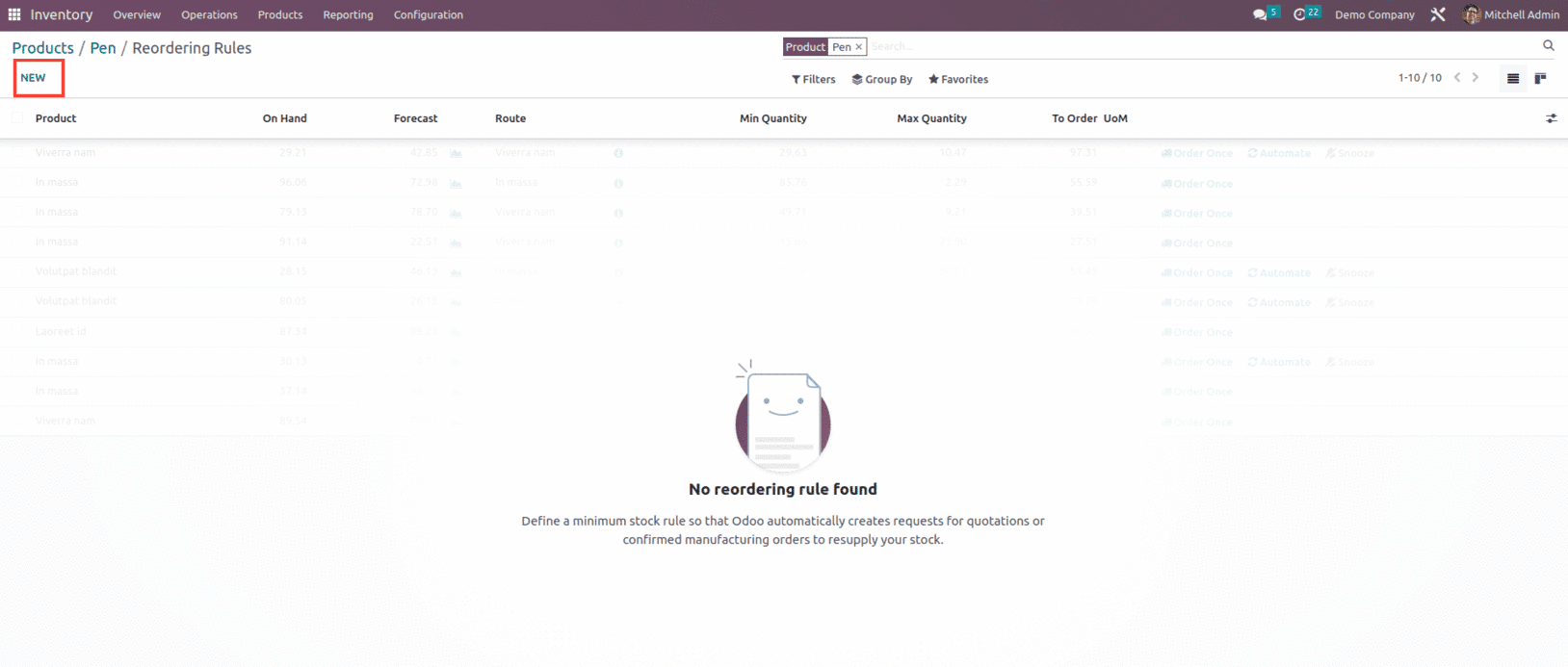
From here, we can set the reordering rule for the product which include fields such as Product name, On hand, Forecast, Option to set Route, Minimum quantity, Maximum quantity, Multiple quantity and few more options which can be enabled as per need, as shown below.
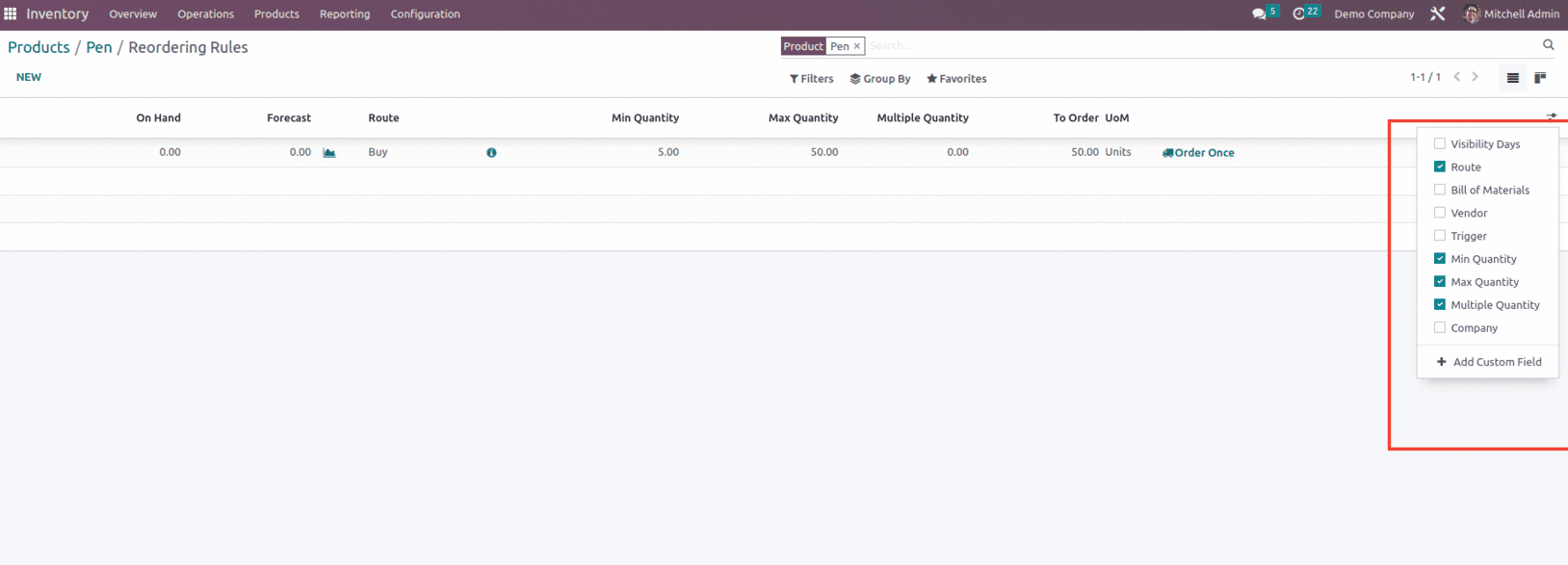
Max Quantity sets the upper threshold, while Min Quantity sets the lower threshold for the reordering rule. A new purchase order will be made to refill the available stock up to the maximum quantity if it falls below the minimum quantity.
It is possible to specify Multiple Quantities so that products are only ordered in lots of a particular quantity. Depending on the quantity entered, this could lead to the creation of a purchase order that would result in stock being on hand that is greater than what is shown in the Max Quantity box and the location outlines where the ordered amounts should be kept after being received and added to the stock.
Once the quantities are set and when we opt for an option called Order Once at that time a popup message comes which specifies that a purchase order is generated for the product with specified quantities, as shown below.
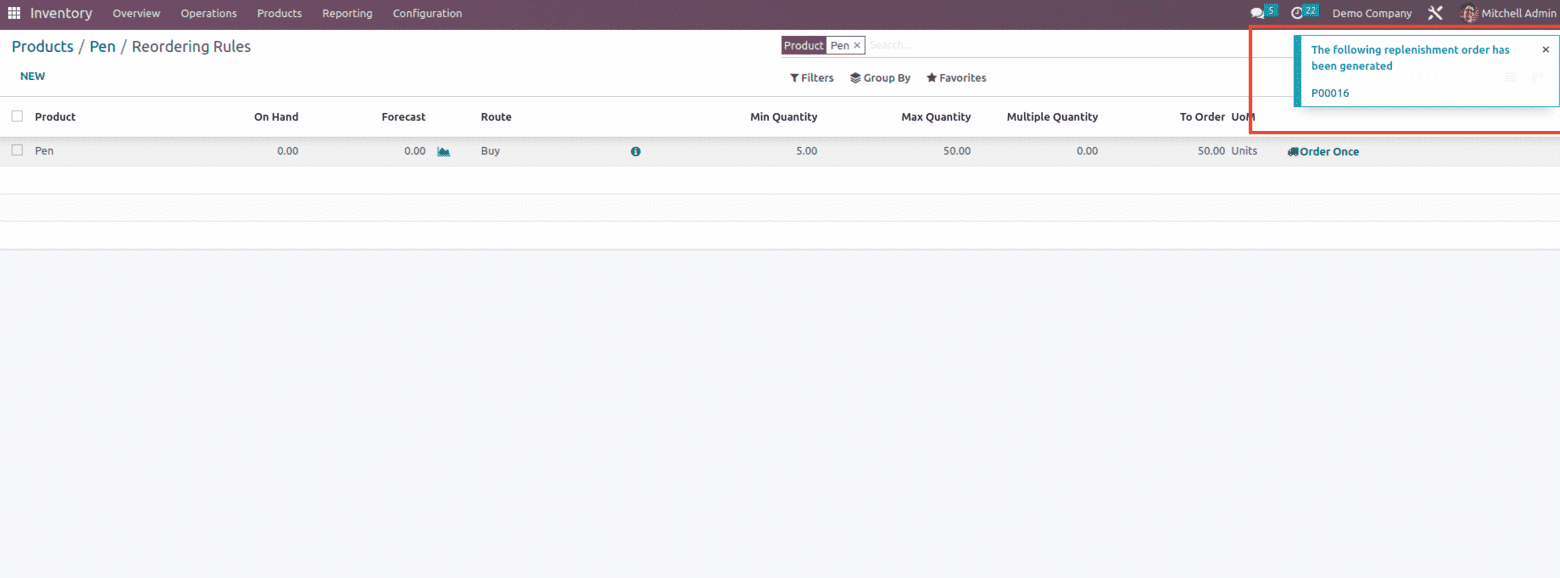
So as per the popup message received, a purchase order will be generated inside the Purchase module, as shown below.
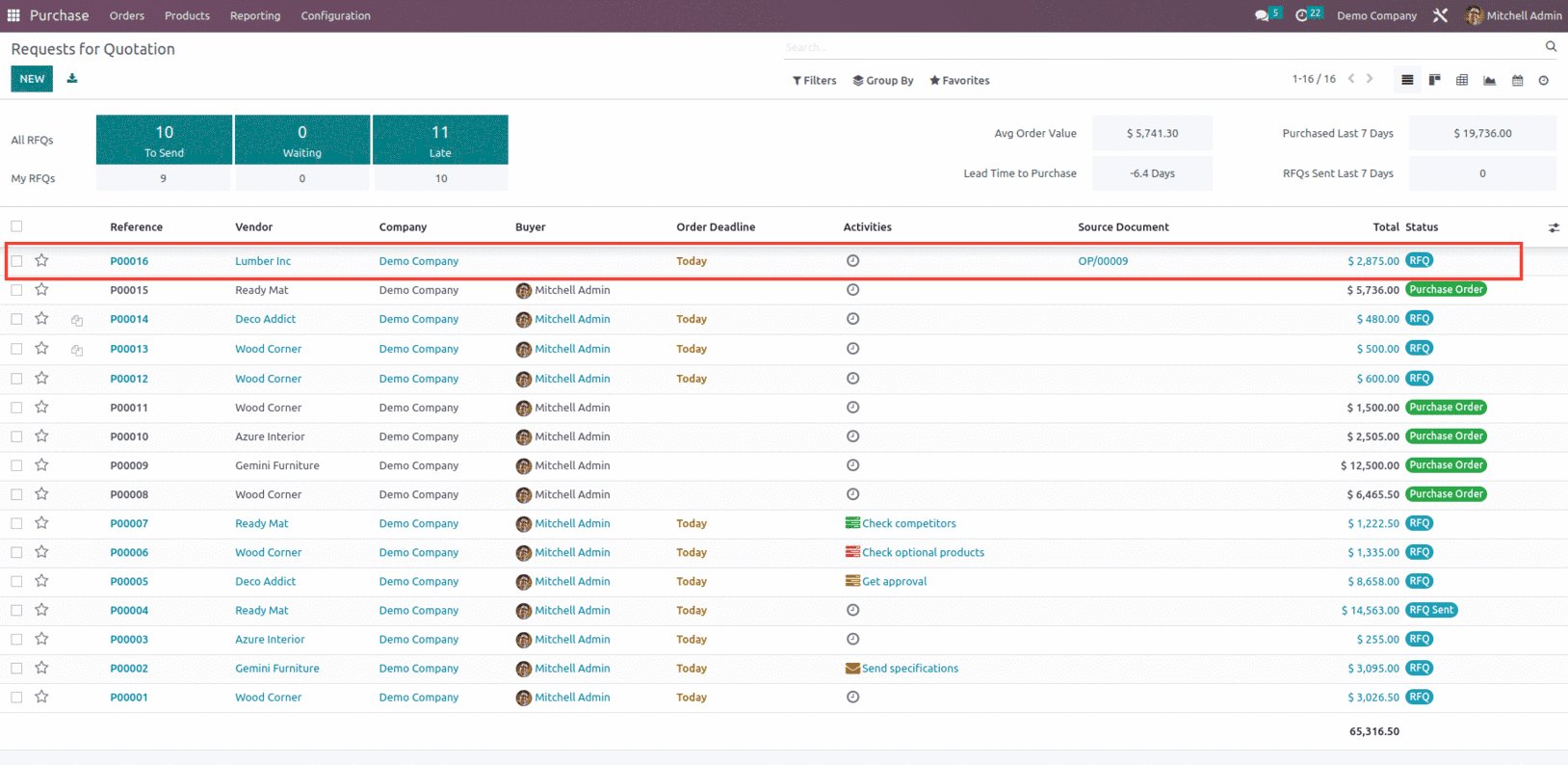
The purchase order will contain the required amount of product as mentioned in the rule which in turn will update the product On Hand as shown below.
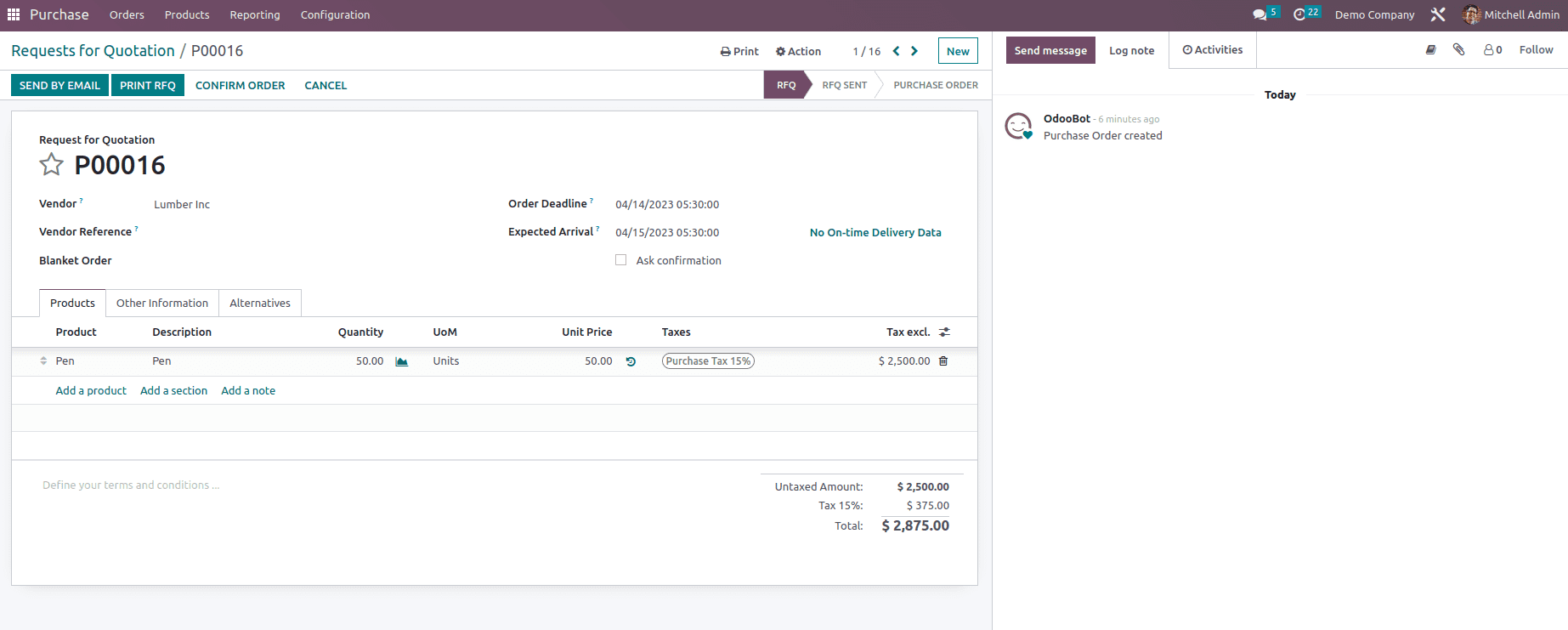
Once validating the purchase order, the quantity will be updated accordingly, as shown below.

This is how we can create and manage reordering rules in products, and the user can also manage recording rules manually as well as automatically.
To manually use the reordering rule, we can use the option named Run Scheduler in the Inventory module.
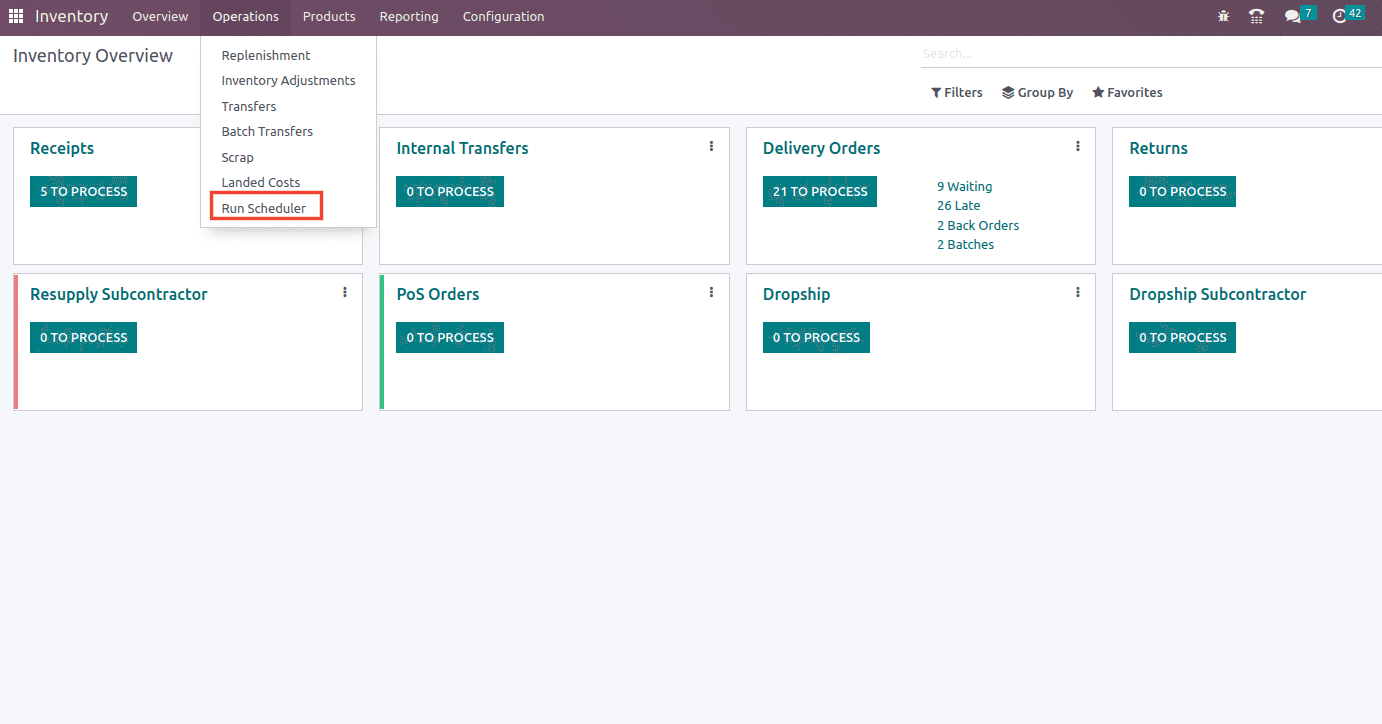
On manually running the Run Schedule, a pop message comes up that the stock will be reserved for operations waiting for availability, and the reordering rules will be triggered.
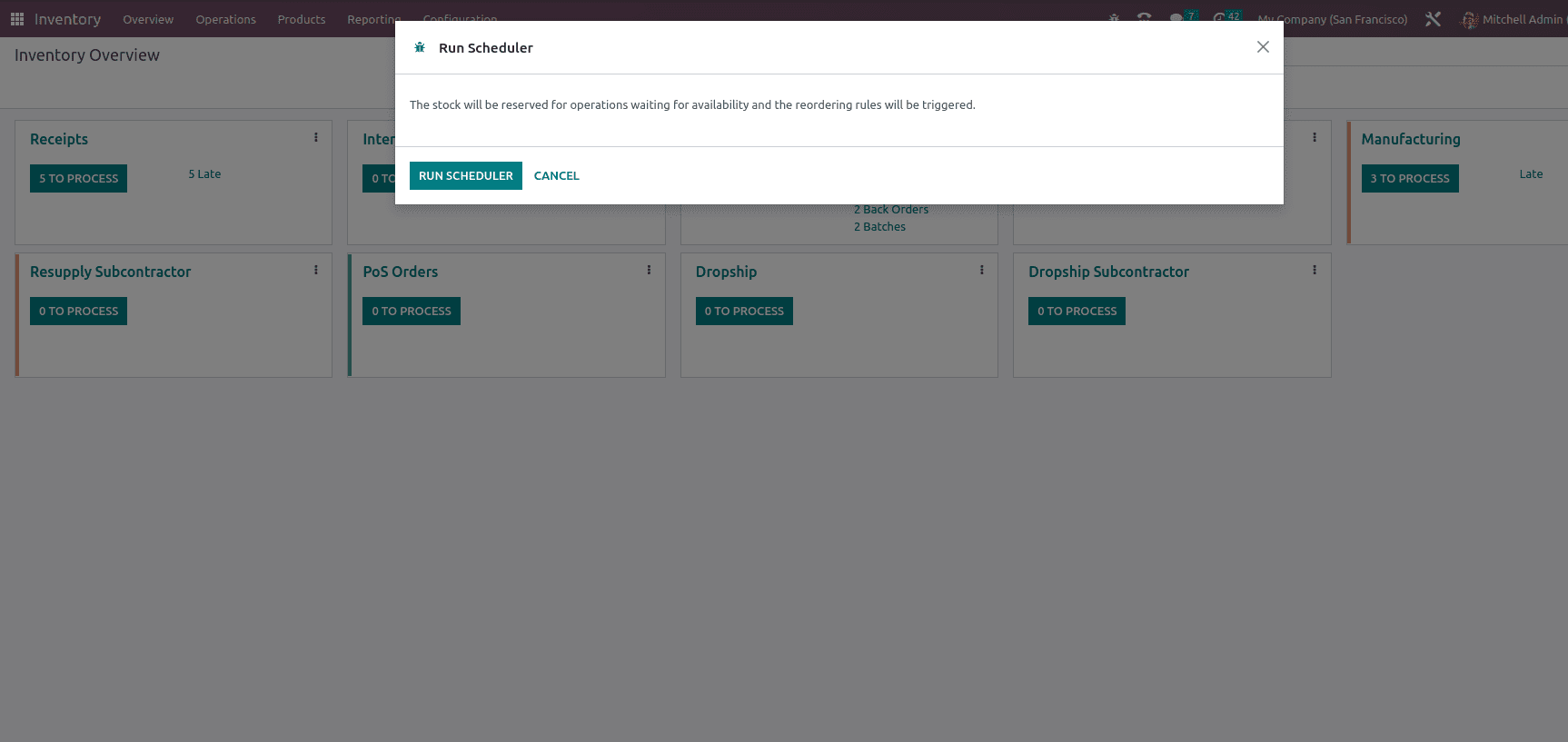
By default, Odoo offers automatically scheduled actions for "Reordering Rules" or other "Procurement Operations" that will proceed according to the schedule.
Prior to configuring scheduled actions, turn on developer mode and can enable it from the General settings under the Technical menu we have the option for Schedule action as shown below.
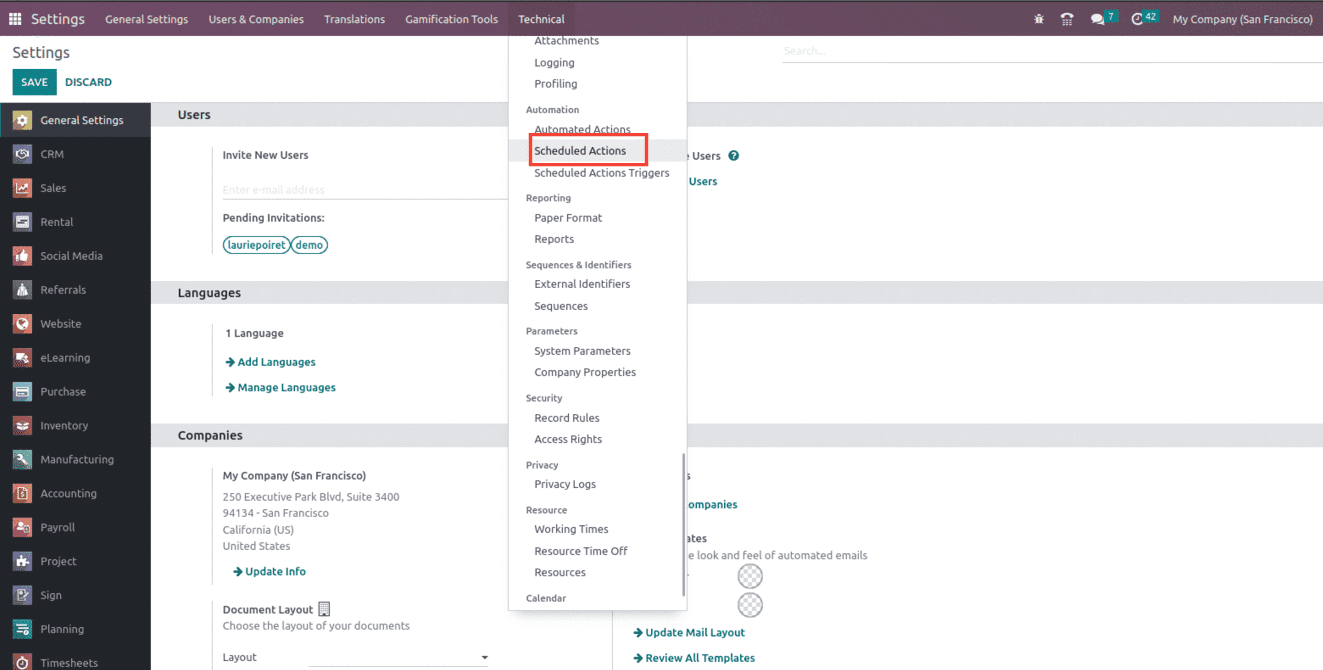
Then, choose the "Procurement: run scheduler" scheduler and modify it as needed.