A vital procedure that involves numerous processes is product manufacturing. Therefore, using these manufactured products properly is another crucial activity. Allocating these manufactured goods to different consumers while taking priority considerations is essential to maintaining effective customer service. Ensure the best possible use of resources and the timely delivery of goods to the right customers, this entails thorough planning and effective decision-making, which raises customer satisfaction.
Each of a company's customers is crucial, as there are many of them. What would happen if numerous clients made orders for a product that wasn't in stock? In such circumstances, the business must either buy or produce these things.
When making a purchase, it's occasionally acceptable to buy several large quantities at once if the requested quantities are large. When manufacturing a product, it might be challenging to produce large amounts at once. Because there is some capacity at the workstation. Therefore, in such circumstances, it is not possible to supply the goods to every consumer who requests them at once. Here, the user's only option is to divide the quantities of the generated goods among the many deliveries. Allocating the manufactured goods to customers' deliveries correctly speeds up delivery times and reduces user work.
Odoo 16 introduced a feature Allocation of products, which helps the users to complete this task. So users can enable the Allocation Report for Manufacturing Orders option from the Configuration settings tab. Enable this option and save the new configuration.
: Configuration > Settings > Allocation Report > Save
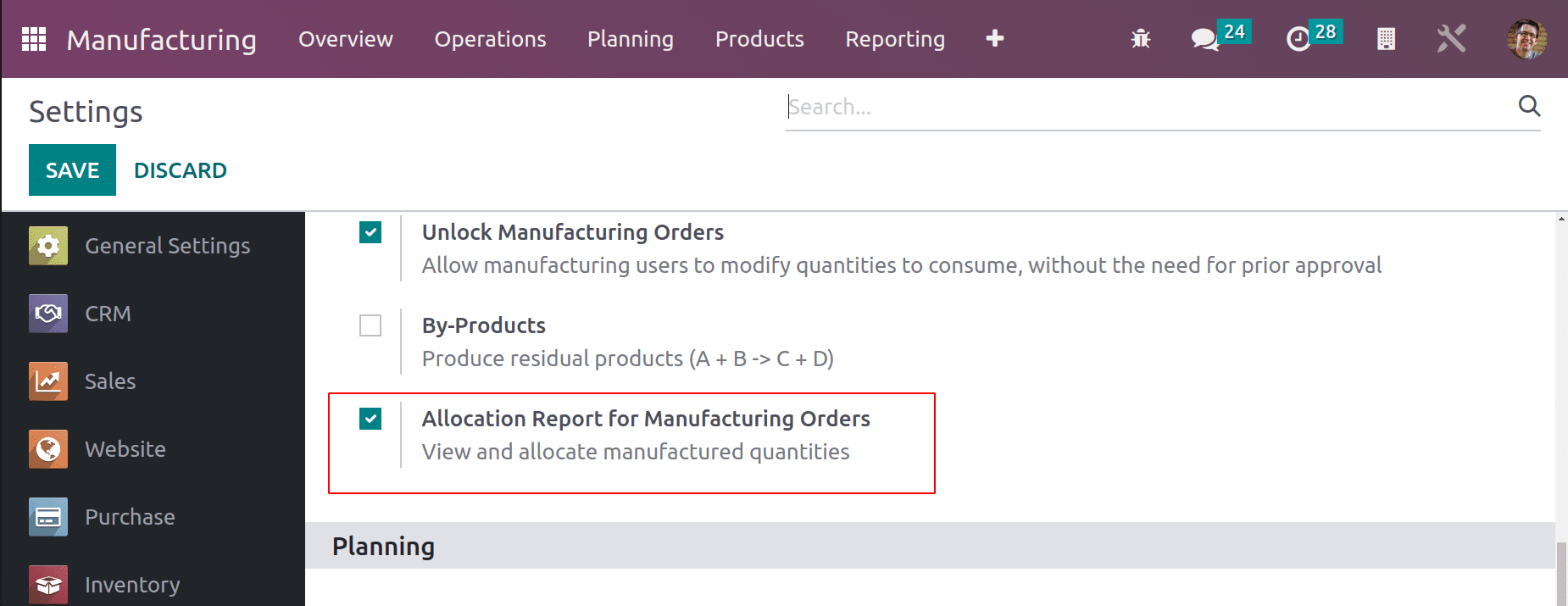
If the user selects this option, an Allocation Report is displayed once the manufacturing process is complete. An allocation report for the manufactured goods includes a list of delivery. Due to a lack of inventory in the organization, some deliveries are in the waiting stage. The user may then easily assign the product to each delivery from that point on.
A business has numerous product deliveries. It might be exceedingly challenging for a salesperson to search the delivery orders for a certain product when the product is refilled. To locate all shipments of manufactured goods and appropriately fulfill orders, the user can use this allocation report.
Let's begin by explaining how this allocation works. Here is a product table that is in stock in zero quantities. Three clients in this scenario ask for the products. The user wishes to manufacture the product to replenish it. Let's see how simple it is for the user to locate the deliveries and assign the product to delivery to finalize the order.
Consider a product Table that can be stored. However, the inventory does not have the item. The Inventory tab's route manufacturing option is turned on.
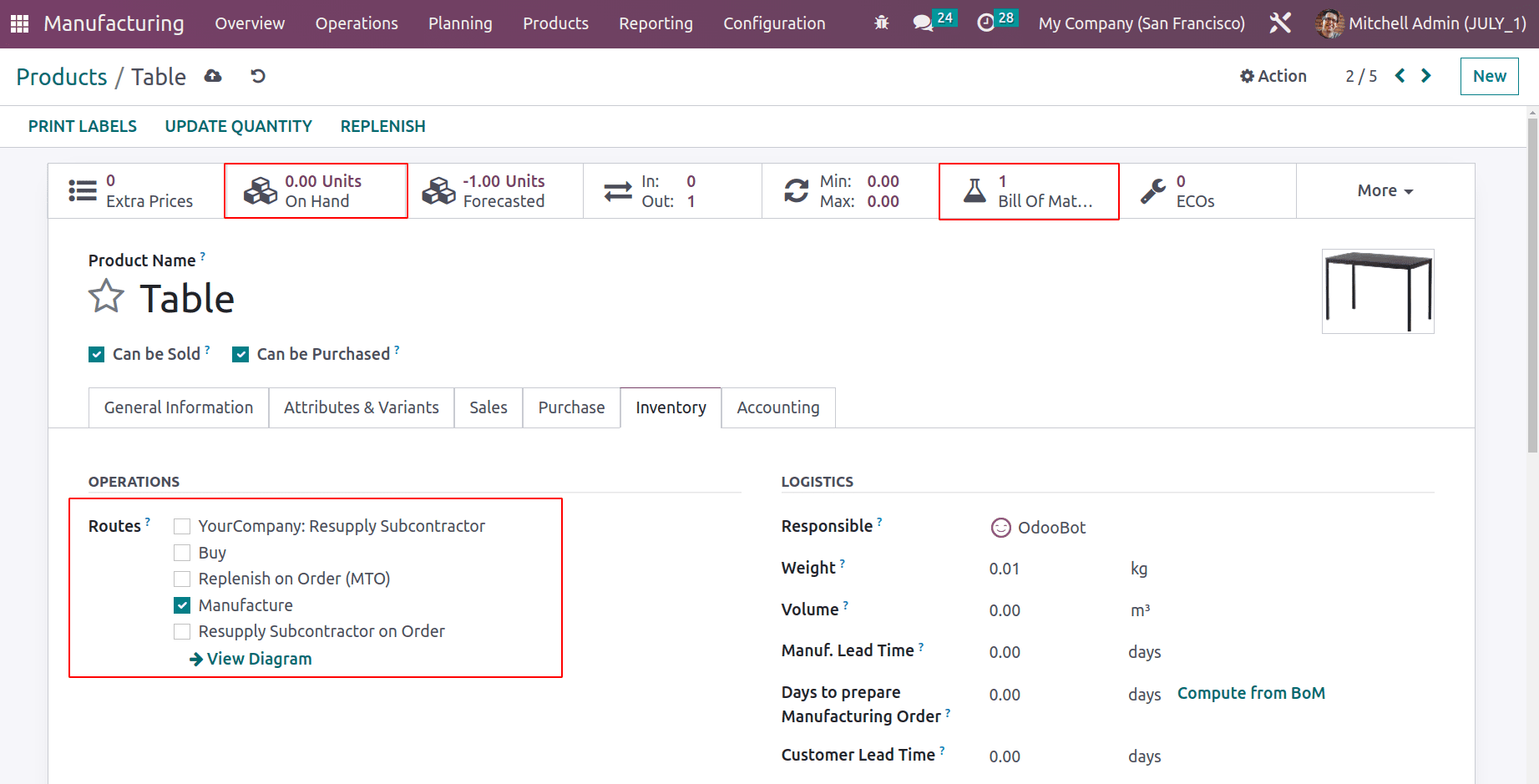
There is a smart tab called Bill of Material that displays every created bill of material. Open the Bill of material.
This page displays the generated bill of materials. Produce this product using the right bill of materials. This bill of materials is utilized during production. The operations listed in this bill of materials are carried out during manufacturing to create the finished product, and the components listed here are used as raw materials for manufacture. Currently, there are enough components for creating several tables.
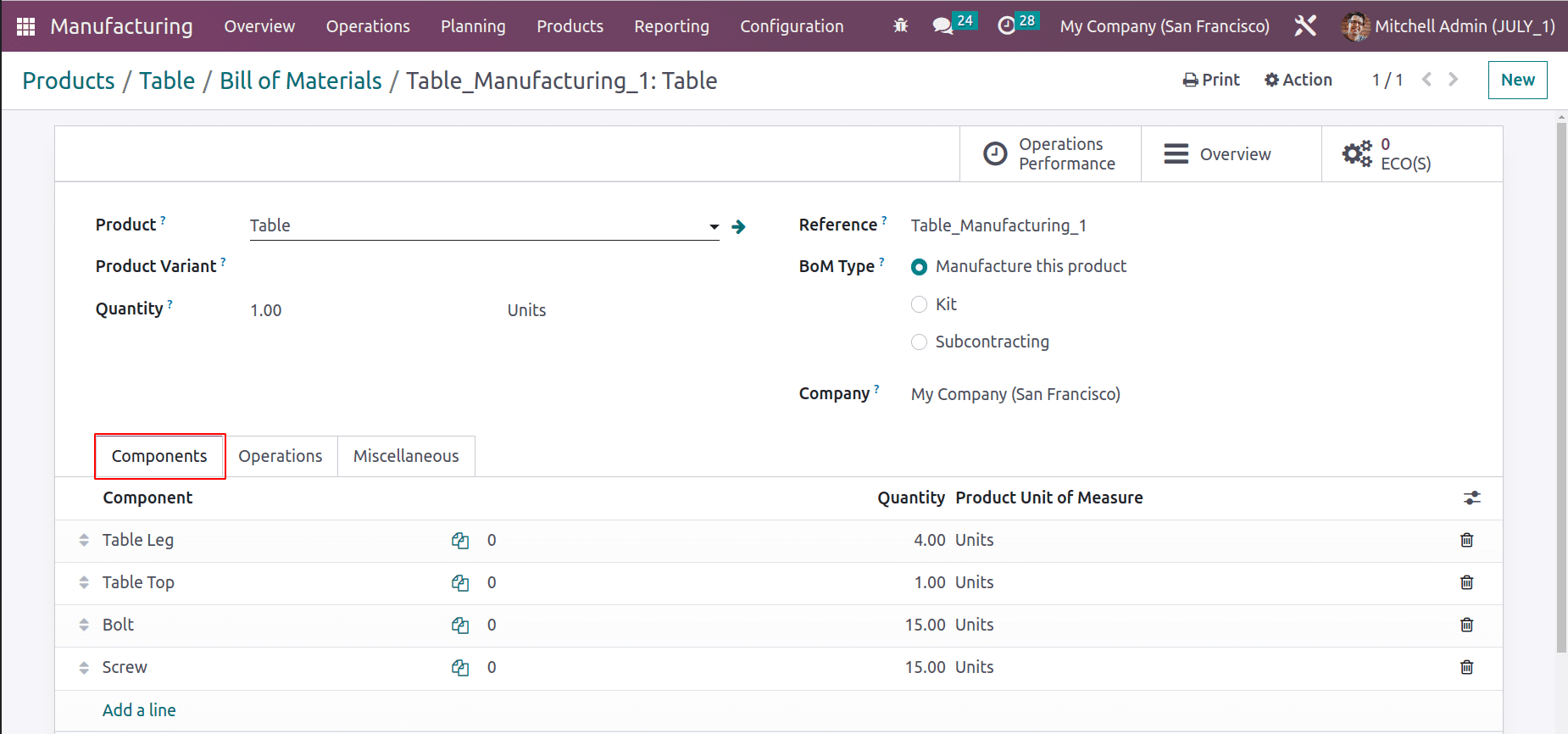
The Operation performed during the manufacturing is Assembling, which is carried out in the workplace known as Assembly Line 1.
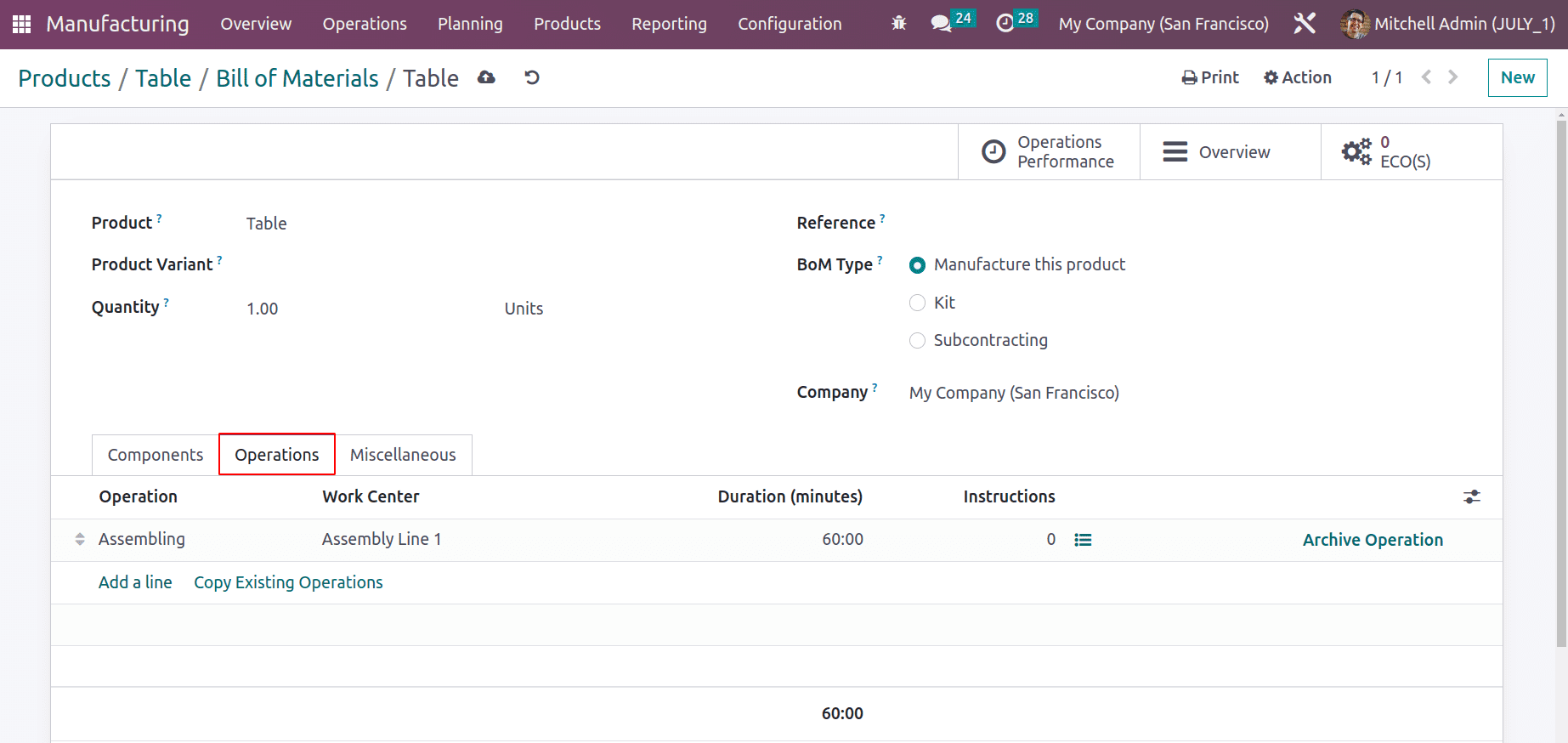
The item in question is currently out of stock. If customers enquired about this item. Let's examine what transpired in these circumstances. Let's thus come up with some quotes for the product. Users of the sales module can generate quotations. Create a new quotation in the sales module.
Here is the sales quotation created for the client of Deco Addict. He requested ten table pieces. Check the order, where the quantity is 10 but there is no stock. That’s why the forecast report is shown in red.
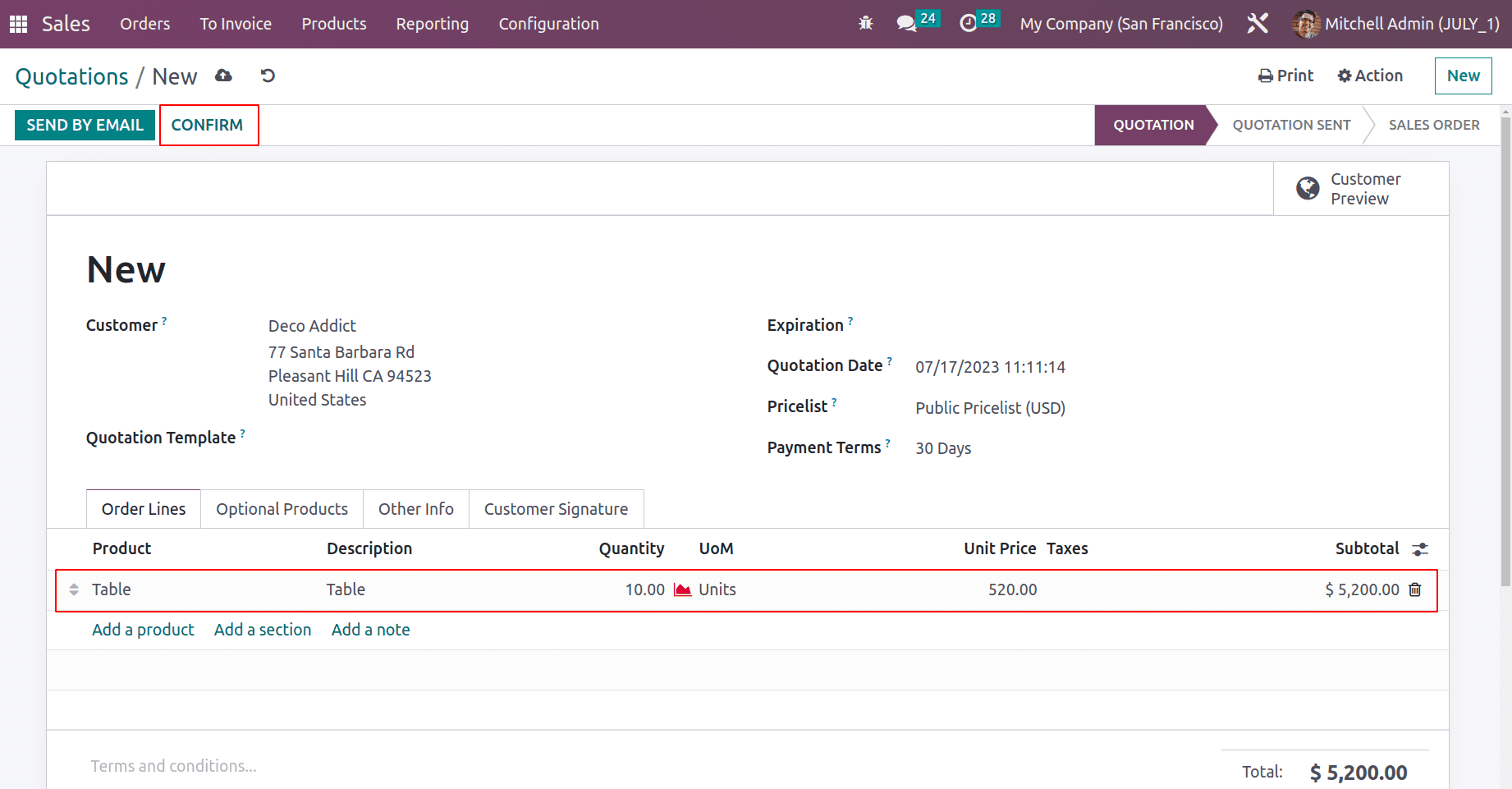
Open the delivery tab to check the status of the delivery order. While checking the delivery the product is not available.
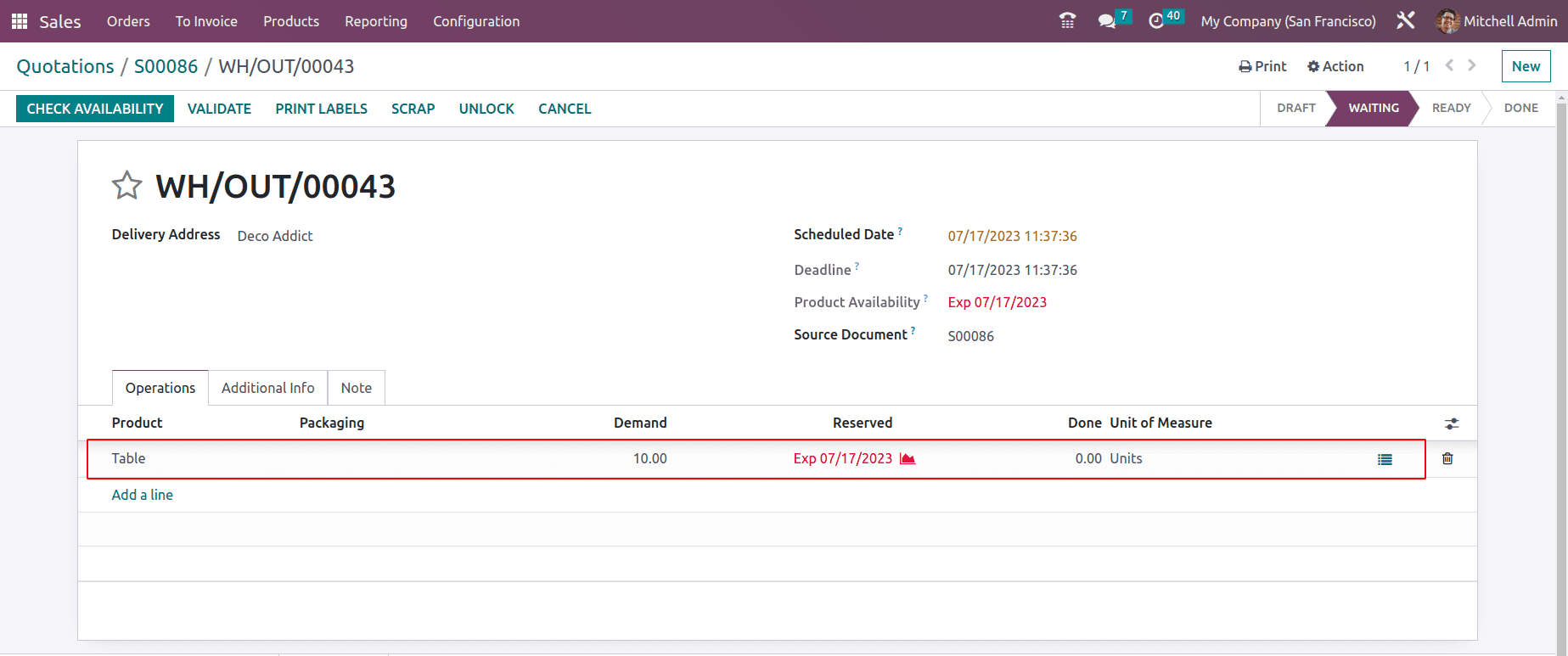
The second quotation is created for the customer Azure Interior. Here the customer requested 5 quantities of product Table. Confirm the order. While checking the delivery, which is also in the Waiting stage, because the product needs to restock.
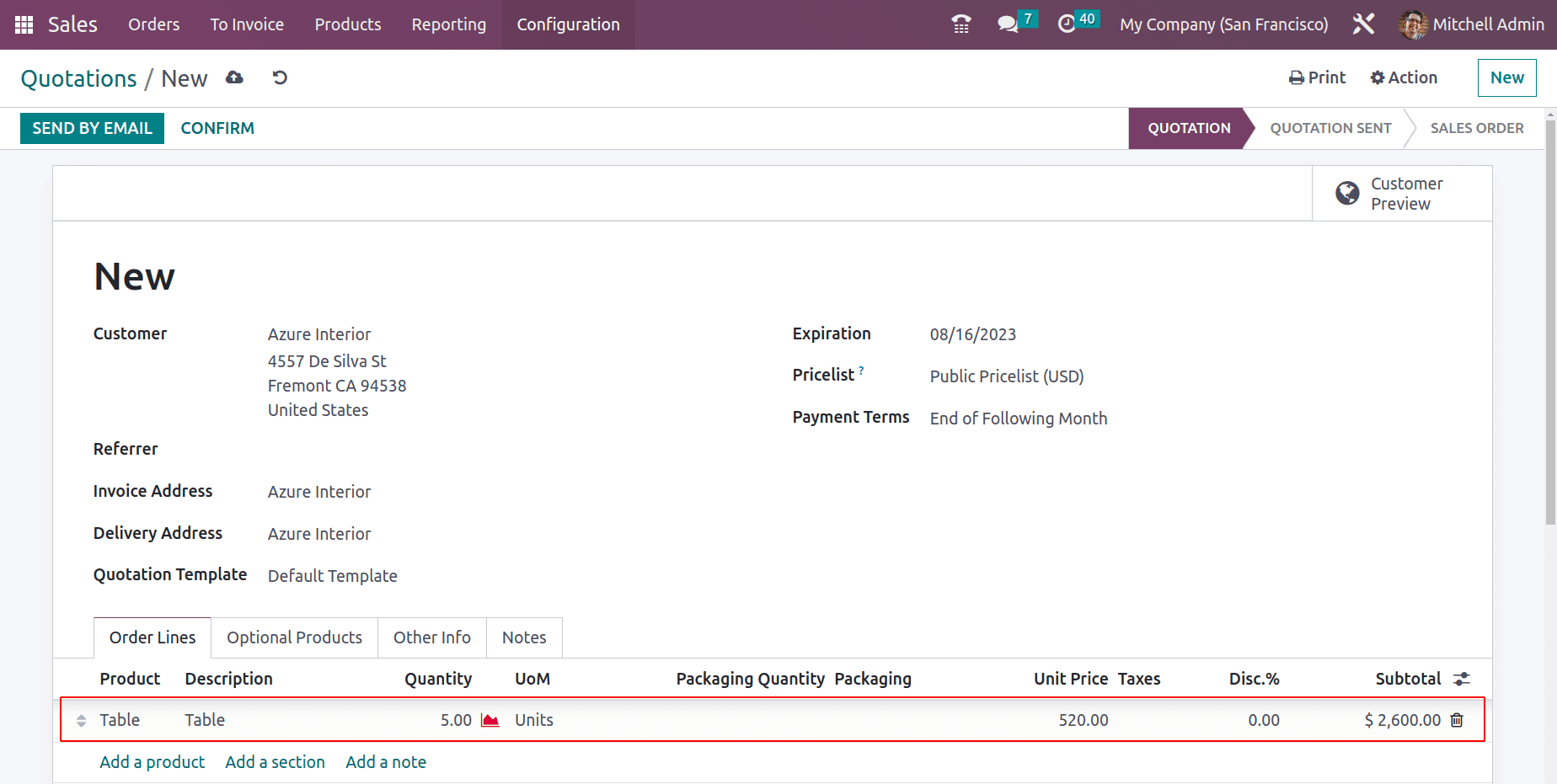
The third customer is Gemini Furniture. He asked for 2 quantities of product. Confirm the order. The third delivery order is created and moved to the Waiting stage also.
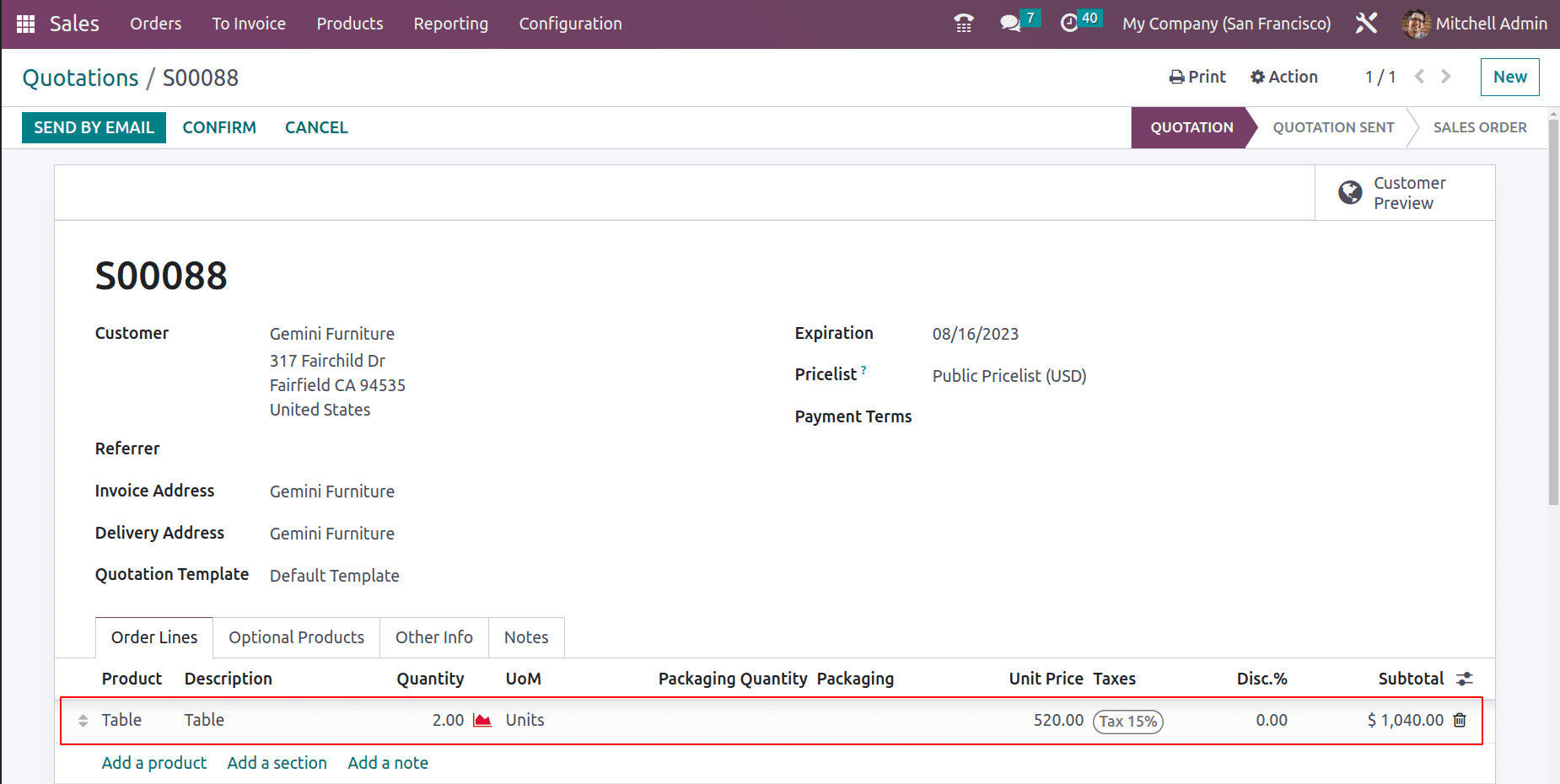
Here, three buyers each wanted a different quantity of the same product. However, the item is sold out. Consequently, the business chose to produce the goods.
Let's make a production order now. Choose the Manufacturing module to start the production process. From the Operations tab, users can select the manufacturing order.
Then a new manufacturing order for the Product Table with 20 quantities was created. Here the same bill of material which is shown inside the product’s smart tab is chosen. So all the components and operations are copied to the manufacturing order to complete the production. Confirm the order. Here the product table needs to create 20 quantities because 3 orders for a total of 17 quantities are waiting.
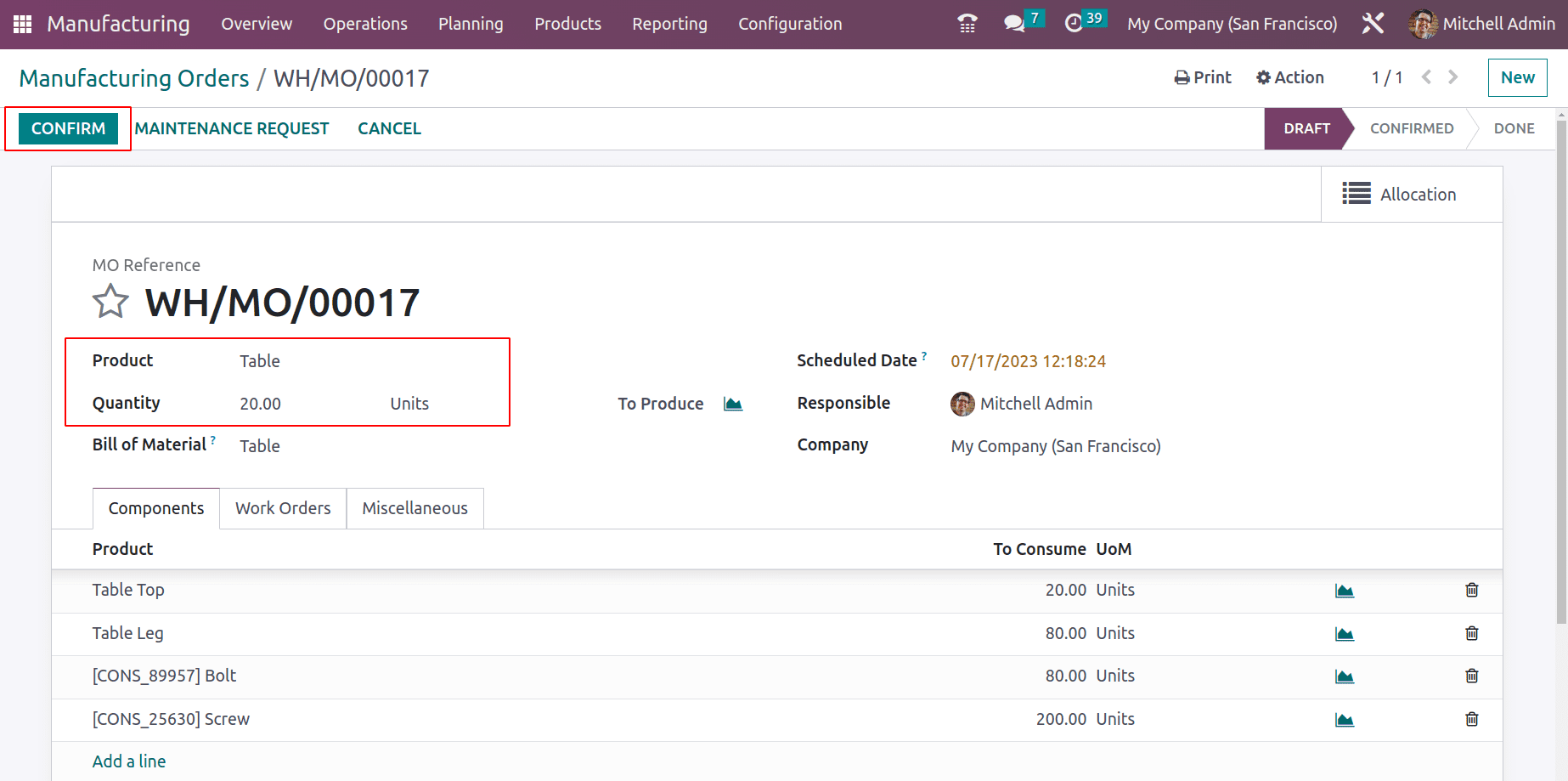
The operation is in the Ready stage after confirming the order. Start the operation by clicking the start button. Then complete it properly.
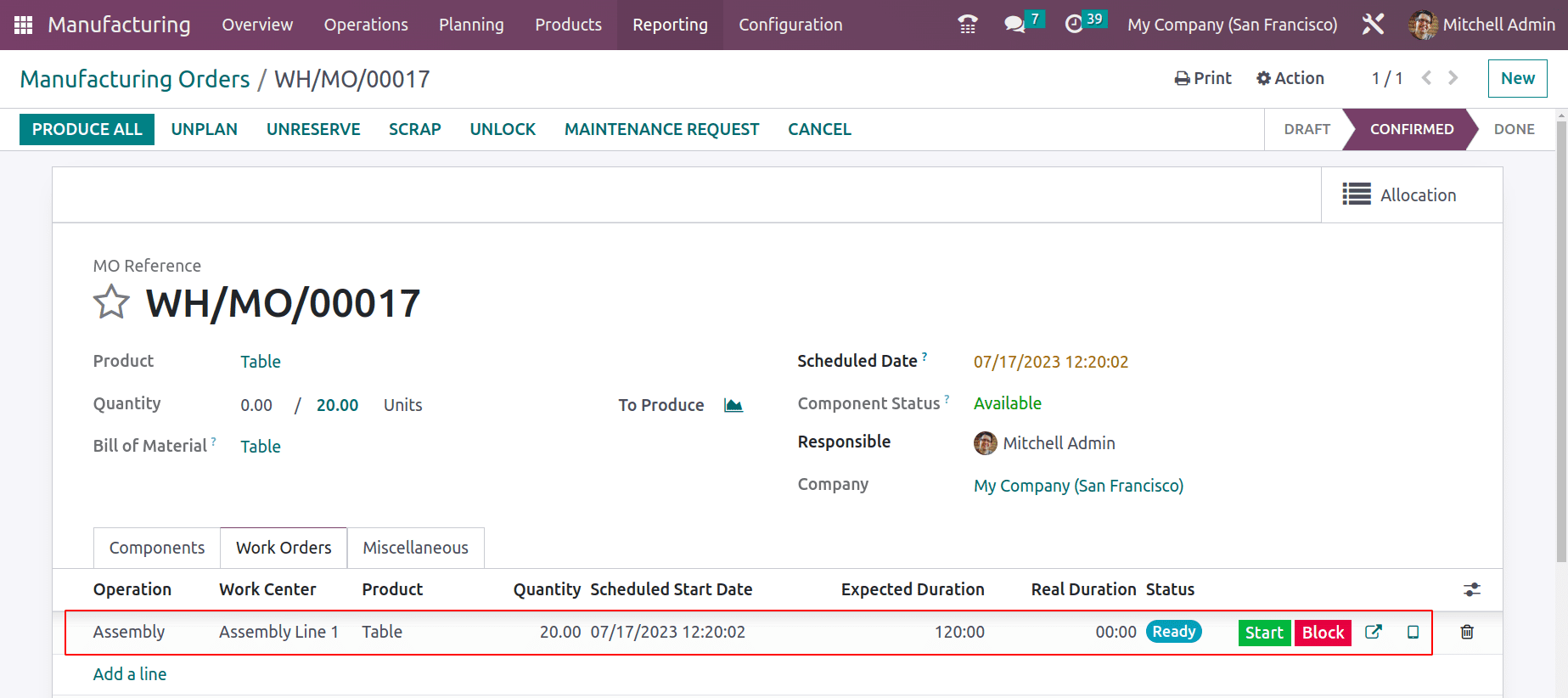
After completing the operation click the Produce All button. Then the manufacturing order will complete and the 20 quantities of product will go to Stock.
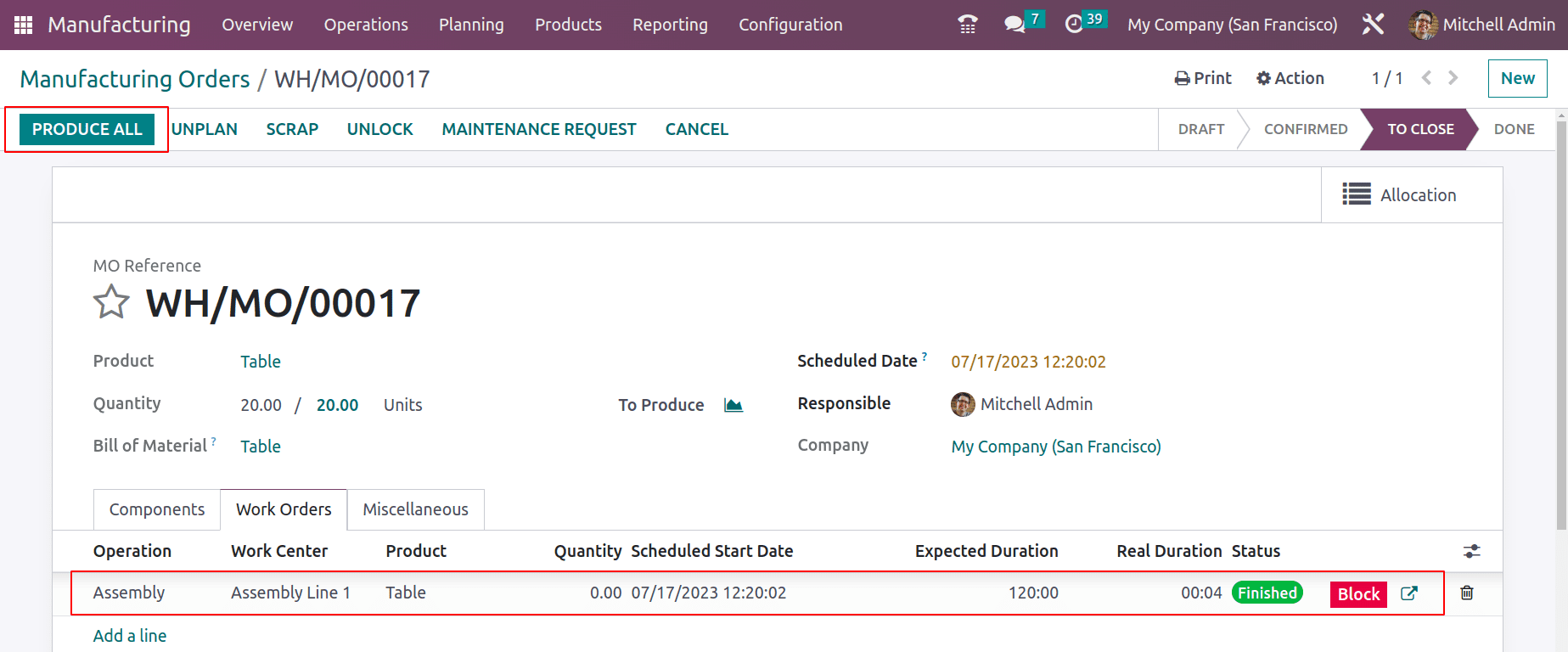
Now the manufacturing process is completed. Some of the smart tabs are shown inside the completed manufacturing order. There also an allocation tab will be shown. Open it to see the Allocation report.
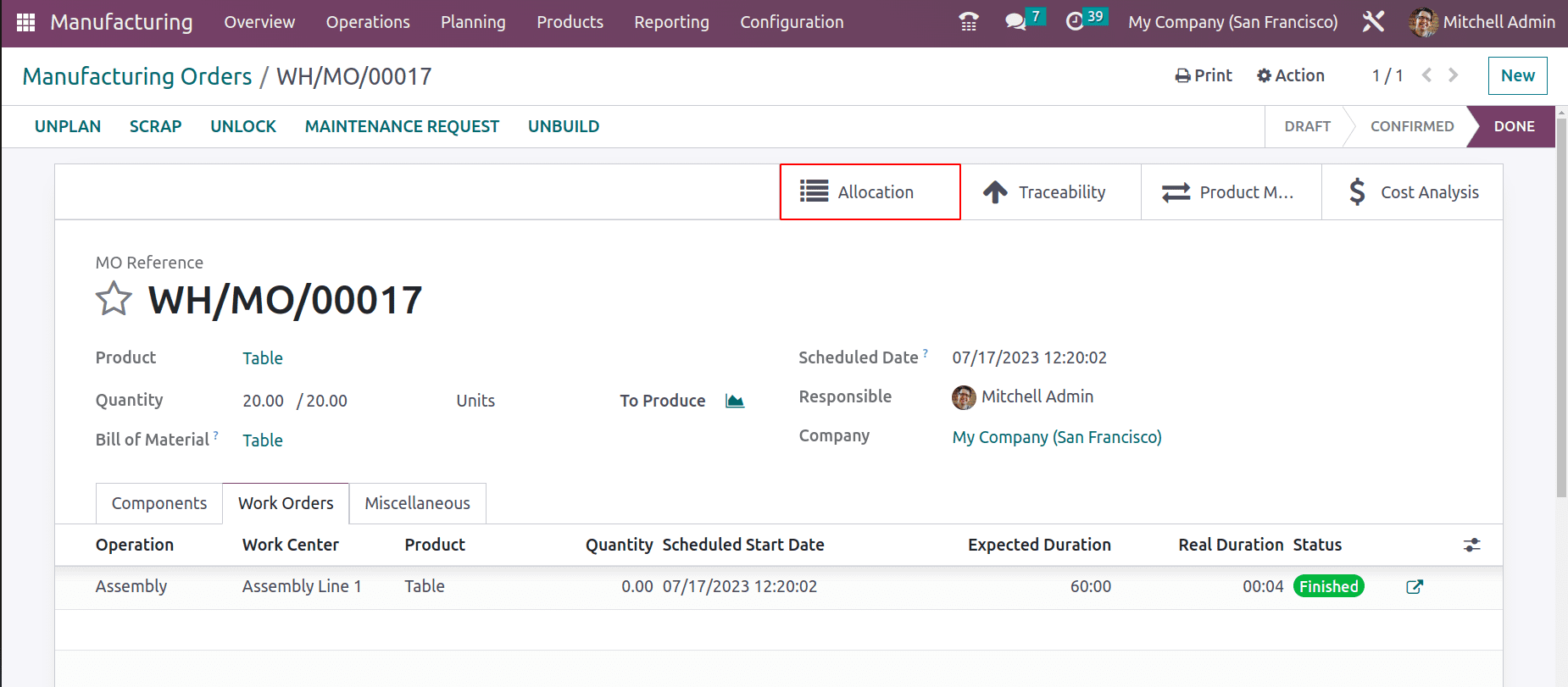
The Allocation reports contain all the previously created deliveries. The details like the sequence number of delivery order, name of the requested customer, and the requested quantity are shown inside the Allocation request. All of them are waiting for the product Table.
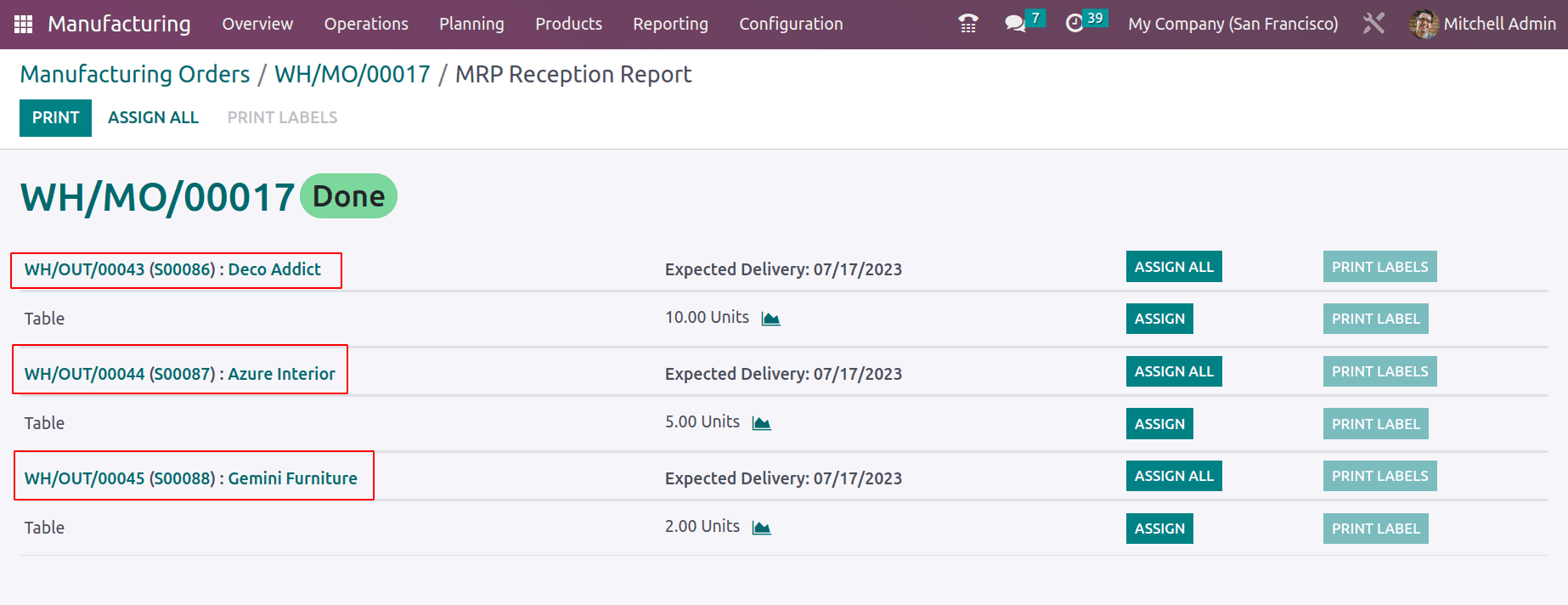
The Assign button can be used to allocate products to delivery orders. The ASSIGN ALL button is used to assign all products.
After assigning the product to the delivery then open the delivery. To open the delivery order from here click on the delivery sequence number. Here the assigned product is reserved for delivery. The user can click the Validate button to complete the delivery then the product will move to the customer location from the stock.
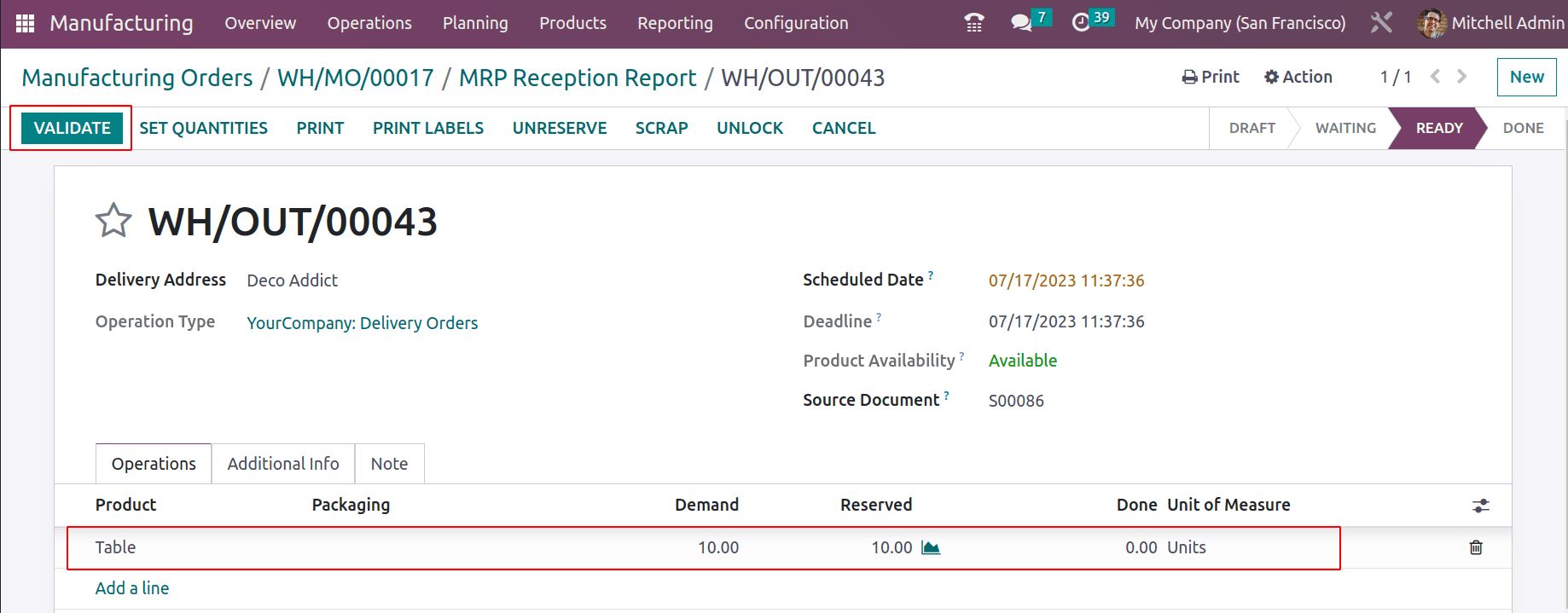
The user can attach products to every delivery in the same way. The user can allocate products on time due to the report's key benefit. If there isn't enough inventory to accomplish every delivery, the user can choose which product gets assigned to which delivery order. As a result, the most urgent delivery can be finished quickly.
When manufactured goods are properly allocated to delivery orders, time delays can be cut down, and customer satisfaction rises as a result. Odoo 16 reduces the complex procedure to a one-touch approach. To know more about the important features of the Odoo 16 Manufacturing Module, refer to our industry page Odoo Manufacturing.